Charlotte, N.C.-based Nucor Corp.—a steel recycling company—faced a range of inefficiencies when it purchased the Marion Steel Co. in Marion, Ohio. The previous operators relied on estimates to determine the amount of steel to be placed in the furnace. Inaccurate estimates were leading to unsatisfactory end products that had to be recycled again. Meanwhile, the plant was struggling to comply with state energy regulations.To correct the problem, Nucor introduced a scale and weighing system using control products from National Instruments Corp. (NI), of Austin, Texas. “The system gives us better control of the scrap metal, which means we’re not under-utilizing or over-utilizing the capacity of the furnace,” says Dave Brandt, electrical engineer at Nucor. “Using the National Instruments controller, we can efficiently measure the weight of what we’re putting in the furnace.”The weight control allows operators to run a more efficient process. “When we have the right weight, we can eliminate reheating and other unacceptable processes,” says Brandt. “The controller helps save energy by optimizing the performance.”Another energy problem that plagued the plant was the electric flickering that occurred when a large amount of energy was used to heat the furnace for recycling. The flickering was inconvenient for Marion residents and prompted monetary penalties for Nucor. To end the flickering, Nucor installed an online reactor in series with the furnace that measures the amount of energy drawn from the power grid. If the furnace approaches the prescribed limit, the system can quickly change methods to reduce the amount of power being drawn.Nucor is part of an emerging trend of bringing control tools and technology to the management of energy. In the case of Nucor, the goal was to create a more efficient manufacturing process. But many plants are using automation systems to reduce energy for costs savings and to reduce their carbon footprint.Plant operators are more concerned about energy consumption these days. Just a few years ago, energy consumption was not a large concern at plants. Energy was cheap and few cared how much you burned. But two trends have changed the consciousness of plant managers. The cost of energy has soared, and the need to reduce carbon emissions has become a powerful social motivator.Track & reduceSo plants have turned their attention to reducing energy consumption, both to save money during difficult economic times and to drive down carbon emissions. Since you can't change what you can’t measure, plant managers are looking to their automation systems to keep track of energy consumption and to reduce overall use. In some cases, it’s a matter of making the plant more efficient—and thus less of an energy hog—and in other cases, plants are integrating automation with heating, ventilation and air conditioning (HVAC) systems to measure and reduce energy consumption.Plants are under pressure to reduce their energy consumption, and not just for cost savings. Whether it’s government regulations or simply being a good citizen, reducing carbon emissions has become important in just the past three or four years. “In renewable energy and efficiency, there’s a lot going on,” says Brian MacCleery, green technology engineer at NI.“The motivating factor is cost, but there’s a growing realization that being environmentally friendly and saving money go hand in hand. A kilowatt of power is a pound of coal. Saving kilowatts saves on emissions.”Concerns about the environment may be as important as cost savings at this point. “If you read the press and listen to officials in the European Commission or Washington, it’s clear that politicians want less carbon emissions,” says Laurent DeMortier, president of the Energy Management Business at Alstom, a transport and energy infrastructure provider based in Washington D.C. “Spending less is not the only motive. Energy consumption savings is as much about the environment.”One of the quickest ways to reduce energy consumption is to conduct an energy audit and make the plant’s facility more efficient. “Usually with a building, you have a building monitoring system. We interface to that system so we can optimize how the energy is used,” says DeMortier. “By merging control with the IT (information technology) in the building system, we can send signals to manage the building’s needs. If you have solar energy, you can program the system to switch to grid when the sun’s not out and switch to solar when the sun is out.”Surging gremlinsSometimes, an energy savings solution is built from a thousand tiny improvements. Last year, Forest City Gear Inc., a Roscoe, Ill., gear manufacturer, turned to Total Energy Concepts Inc., in Detroit Lakes, Minn., to help trim its energy costs. Total Energy brought in its affiliate, V-Blox Corp., of Jacksonville, Fla. to conduct an audit of Forest City’s plant. Part of the energy was in the plant’s manufacturing process. “We were experiencing downtime and we didn’t know why,” says Rustin Mikel, vice president of operations at Forest Gear. “We were getting error readings. The service tech would arrive and everything would be fine. The machine was in a bad mood and we didn’t know why.”Turns out it was “noise,” sometimes called “gremlins,” in the system. “All of the resistive-type equipment in the plant was causing small surges—not massive surges that would destroy the board,” says Dave Mulvaney, president of V-Blox. These surges were producing false error readings that forced costly shutdowns and service technician visits even though there was nothing wrong with the system. “We did a complete energy audit and worked on grounding issues to solve the gremlins issue,” says Mulvaney. “After the grounding, we also eliminated hot spots such as arcing.”Mulvaney notes that plants typically get about a 15 percent energy savings from a complete energy audit, which often leads to automating plant lighting and eliminating heat and cooling leaks. Forest City’s list of tiny improvements includes nearly fifty individual items. But the biggest energy saving often comes through improvements in the efficiency of the plant equipment itself.While tightening the building’s energy consumption is important, many plant operators see greater value in optimizing their core processes for efficiency. These changes come with valuable byproducts such as increased throughput, greater safety and lower maintenance expenses. “Plants are using process automation for increased energy efficiency,” says Larry O’Brian, research director at ARC Advisory Group Inc., in Dedham, Mass. “Most end-users don’t think of their automation as a platform for optimizing energy, but we’ve seen integration between energy systems and control that’s very successful.”Power & processAs well as controlling plant processes, control systems are being used to optimize the building’s IT. “We’re integrating the process side with the power side,” says Jeff Vasel, global electrical integration manager at automation supplier ABB Group, in Houston. “Energy efficiency is one of our goals. With the control architecture, you can see the health of the entire plant from one view.”Using control technology in improve energy efficiency has made a huge different at the University of Texas, in Austin. The campus generates its own energy to heat, cool and run power for 75,000 students and staff in more than 17 million square feet of buildings and facilities. The three UT power plants have recently been overhauled to reduce energy use. “We’ve had a lot of success using control systems to save money on energy,” says Kevin Kuretich, associate director of utilities at the school. “A control algorithm can run a plant better than an operator.”By using control technology to manage energy consumption, the campus was able to reduce use to 1970s levels. “We use less gas now that we did in 1977, and since that time, we’ve gone from 12 million square feet to 17 million square feet,” says Kuretich. “And all the new buildings have been high-energy-use facilities. Energy use has grown between 20 percent and 30 percent.”Until 2005, energy wasn’t much of a concern for the university. Gas was cheap, which meant electrical generation was cheap. But when gas costs soared, Kuretich turned to Emerson Process Management to control the generation process and cut energy consumption. “We added a flue gas recirculation duct and fan and its control-based algorithm,” says Kuretich. “You can drop the logic into any PLC. It’s completely control based.” The return on investment came in six months.Making equipment more efficient is also a big factor in reducing power consumption. “A view into the equipment is important,” says Marcia Walker, development manager for sustainable production and power generation and energy management at vendor Rockwell Automation Inc., in Milwaukee. “By studying the equipment, you might find line A is 25 percent more efficient than line B. So we’re not just looking at traditional OEE (overall equipment effectiveness), we’re also looking at energy.”Plants are using control technology to dig down into their machines to make energy-efficiency changes. “At the end of the day, it’s your understanding at the sensor level and the historian level that lets you tweak for efficiency,” says Simon Jacobson, research director at AMR Research Inc., in Boston. “Control vendors are using modeling and visualization to get the most out of their equipment.”With increased pressure to reduce energy consumption—both to save money and reduce carbon emissions—plants are turning to automation and control technology. Sometimes the solution is as simple as integrating control and building systems to shut off the lights when nobody is in the building. But the more significant savings come through improved process control that optimizes the plant’s core processes.Related Sidebar - Envac—Optimizing an Already Efficient ProcessTo read the article accompanying this story, go towww.automationworld.com/feature-6670.
Subscribe to Automation World's RSS Feeds for Feature Articles
Companies in this Article
Companies in this Article
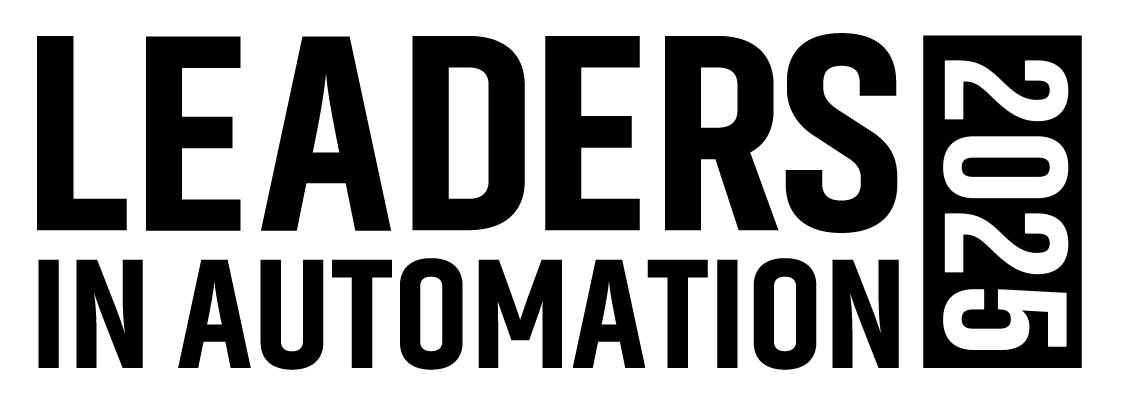
Leaders relevant to this article: