Two years ago, The Wall Street Journal reported about “a wave of technologies and ideas that are creating a computer-driven manufacturing environment that bears little resemblance to the gritty and grimy shop floors of the past. The revolution threatens to shatter longstanding business models [and] upend global trade patterns.”
Since then, some early adopter manufacturers have jumped on board, piloting or deploying smart technologies, lines and plants. But most still struggle to best use the Internet of Things (IoT) and fully and effectively embrace smart manufacturing. IoT is a catalyst that will require industrial operations to change more radically over the next five years than they have in the past 20.
Leaders around the world from private industry, academia and government are working to develop and expand initiatives to help manufacturers and standards bodies to research and apply smart IoT technologies and infrastructures. More than flashy catch phrases, these initiatives are helping channel the current industrial revolution. Newly forming standards will drive compliance and help producers realize the true value of smart manufacturing.
In Germany, for example, the federal government has set aside funding to underwrite Industry 4.0, a trade initiative focused on R&D investments related to IoT and smart-manufacturing concepts. It encompasses the government’s high-tech strategy to promote computerized industrialization, connected machines, autonomous sensor-actuator components and systems to create intelligent networks and cyber-physical systems (CPS); and lays out design principles that will lead the shift from centralized to decentralized production, providing a non-hierarchal integration of horizontal supply chain and vertical processes. This will require the merging of industrial and IT systems and communication based on the open standard Ethernet IP.
Meanwhile, in the U.S., a group of industrial practitioners, suppliers, universities, government agencies and laboratories formed the Smart Manufacturing Leadership Coalition (SMLC). Their joint vision is to enable collaborative R&D and develop and disseminate approaches, standards, platforms and shared infrastructure to facilitate the broad adoption of intelligent manufacturing.
The Made in China 2025 plan is prioritizing innovation, technology integration, quality management, green manufacturing, and promotion of service-oriented manufacturing and manufacturing-related service industries. The Chinese government initiative has gained support from several multinational corporations, and aims to develop and share production standards and techniques for modernization of specific industrial sectors.
The Korean government announced its Strategy for Manufacturing Industry Innovation 3.0 in June 2014, and is formulating action plans through nationwide collaboration with the private sector to help small and medium-sized enterprises efficiently participate in the global value chains. The initiative encourages private sector-led efforts and offers various incentives for participating companies with outstanding performance.
The Factory of the Future out of France, recognizing the transformative impact of emerging technologies, aims to go beyond supporting the modernization of production tools, and assist companies as they reshape business models, organizations, methods of design and marketing, as digital tools are breaking down the partition between industry and services.
All these visions rely on the convergence of plant-floor operations technology (OT) and business-level information technology (IT) to enable the data from a myriad of sensors, actuators, controllers and switches to connect people and processes across the enterprise and throughout the supply chain.
Yet a study of manufacturers conducted by IndustryWeek found surprisingly low levels of OT and IT integration. Only 14 percent of executives indicated that plant-floor data is completely integrated with enterprise systems. Also, about a fourth of executives indicated that a little more than half of their plant-floor machinery (not including computers) is Internet-enabled; 30 percent reported that none of their equipment is Ethernet-enabled.
Additionally, an anticipated 220,000 IT and OT engineers are needed every year for smart manufacturing to truly scale. Our manufacturers need help. Global initiatives discussed above are also leaning in to help develop and offer training resources for engineers to gain the skills to install, maintain and troubleshoot industrial network systems.
What these global initiatives can provide includes guidance on companywide security best practice standards, designs, policies and procedures. As manufacturers walk through their journey and begin unleashing the new gains in productivity and efficiency, uncertainty will be replaced by the understanding that standards-based solutions, IP technology and training are the means to realizing the vision of smart manufacturing.
>> Keith McPherson is a board member at large for MESA International. He has more than 25 years of experience in the automation and information industry, in sales, marketing and business development as well as engineering positions. In his current role as the director of market development for Rockwell Automation’s software business, he leads a global team responsible for commercial marketing, technical sales, software delivery channels and go-to market strategies.
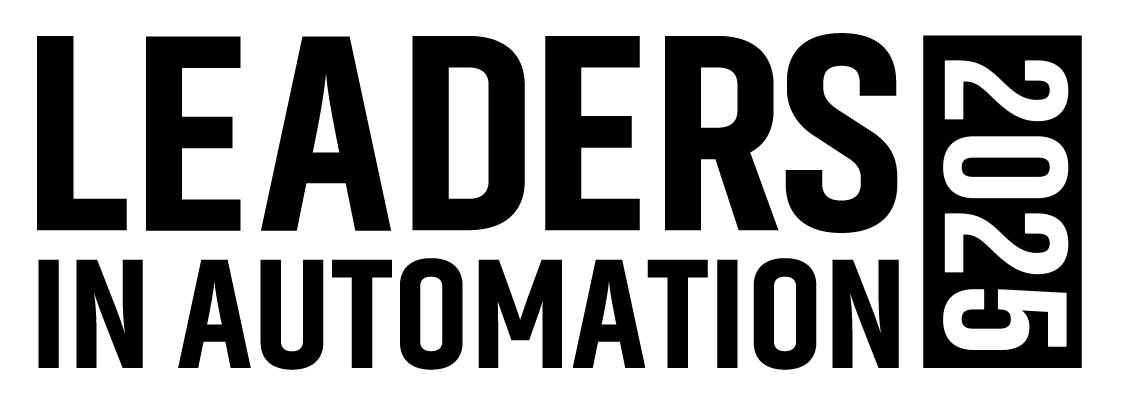
Leaders relevant to this article: