As the industrial world, including industrial equipment manufacturers, undergo digitization, many are looking forward to the new opportunities it is expected to generate. But key to realizing such promise will be determining how to extract the most value from a disruptive period that is radically changing the OEM market.
Digitization is enabling the development of smart, tightly connected and data-driven products that, propelled by the Industrial Internet of Things (IIoT), are redefining the litmus test for product success. It is a fundamental shift from an emphasis on product functionality to a focus on outcomes, experiences and digital services produced from physical products. This shift also is reflective of a larger and growing trend in the form of industrial consumerism, whereby industrial customers increasingly demand constant technical innovation much like consumers are unrelenting in their pursuit of the latest advances in consumer technology, goods and services.
Despite this profound shift, however, some companies might not be responding to the change fast enough. According to research conducted by Accenture, even though two-thirds of industrial executive respondents said they are experiencing digital disruption, half of the automotive companies and 60 percent of the industrial equipment companies acknowledged that they are not yet comprehensively investing in this area as part of their overall business strategy. Those that are slow to adjust their business model to the transition will run the risk of losing market share and profitability.
Accenture has identified six capabilities that form the basis for creating immediate value that can enhance the ability of OEMs to succeed in the emerging market.
Extract value
- Synchronize lifecycles. During digitization, hardware, products, shop floor machinery and other production assets will age more slowly than the digital software that steers them. Increasing integration and synchronization of hardware and software cycles early on will help avoid production complications later.
- Embed software intelligence and connectivity in sheet metal products to enable interaction with the production environment, such as people or machines, and other connected products.
- Use analytics to gain insights and aid decision-making by gathering data from connected products and other data sources. Unhindered data flow, gathering and data analytics will soon be the mainstay of highly digitized businesses. OEMs that do not use data analytics, even at a project level, will be at a major disadvantage.
- Make manufacturing agile by adopting industrial automation wherever possible to increase shop floor speed and flexibility. Automation already is transforming manufacturing in the industrial equipment industry with sensors and control mechanisms now embedded in most machinery.
- Create ecosystems and run them. No single company will be able to own the whole digital value chain in an outcome-driven market. Coordinating ecosystems of suppliers, customers, technology partners, startups, academia, competitors and other stakeholders will be key.
- Transition to an “as-a-service” business to be prepared for the paradigm shift to the market’s focus on outcomes, where combinations of products and services will no longer be acquired as property. Instead, they will be flexibly used as a service when required.
Sustain value
Just as important as creating immediate value will be sustaining it. The key to doing so lies in developing strong innovation processes that will encourage optimal value extraction long-term. There are four approaches to innovation Accenture has identified that include the Market Share Protector, Efficient Executor, Early Innovator and Brilliant Innovator.
The Brilliant Innovator is considered the role model for continually extracting value from digitization, as it combines the best attributes of the three approaches, including systematic innovation efficiency and the use of agile, responsive innovation processes to seize market opportunities and produce the highest innovation returns. Essential to benefiting from any approach, however, will be first deciding to act quickly on the promise of digital technology.
>>Andy Howard, [email protected], is managing director of the Automotive and Industrial Equipment Group at Accenture. Eric Schaeffer, [email protected], is senior managing director and head of Accenture’s Industrial practice. Schaeffer is also author of Industry X.0—Realizing Digital Value in Industrial Sectors.
Companies in this Article
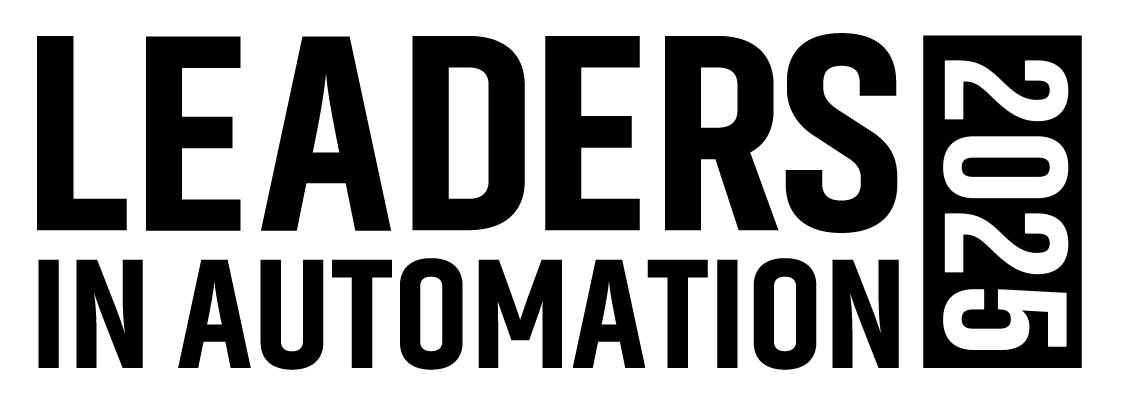
Leaders relevant to this article: