UnPACKed with AW Podcast: Getting along (and ahead) with Robots
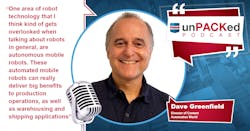
In the first episode of UnPACKed with Automation World, Director of Content, David Greenfield takes us into some of the truths and myths about automation during the past year. Were robots adopted at a higher pace over the past year or did use stay the same? What vertical markets saw the largest benefit? Are there specific robotic technologies he sees as offering the most potential for CPG production operations? Dave knows the answers to these and many other questions as he takes a seat on the opposite side of the microphone.
For more information on robotics access the Robotics Playbook from Packaging World.
To subscribe and find more unPACKED podcast episodes, visit pmmi.org/podcast.
Sean Riley:
Our guest, Greenfield, is not only the Director of Content of Automation World, but he also hosts the hugely successful podcast, Automation World Gets Your Questions Answered. We're excited to turn the tables and pick his brain a bit about all things around robotics and automation. Welcome to the podcast, David.
Greenfield:
Hey, thanks, Sean. Yeah, it's fun to be here on the other side of the mic, so I'll get my turn in the barrel here, as they say.
Riley:
We'll try to be as gentle as possible. A lot of the industry experts were expecting this big uptick in robotic sales in response to COVID, whether it's for the need of social distancing in production facilities or to support production as more people are out of work due to illness. Now that we're a year into it, what's the truth? Were robots adopted at a higher pace over the past year, did it stay the same? What did you see from your end?
Greenfield:
Well, it's a bit of a mixed bag, like most things about automation. There's no one answer, but we all heard a lot about how COVID, as you mentioned, was going to boost robot sales and from what we heard you, that sounded like a reasonable assumption, from everything we heard and the data around that. And while there was certainly a lot of robotic technology adoption going on in response to the pandemic, we were surprised to learn in a survey that we conducted on Automation World readers, which as you know reaches across multiple industry verticals, we found that about 76% of respondents said the pandemic did not drive any purchases of new robots within their facilities. And of those who did bring in robots in response to the pandemic, 80% of those purchased five or less.
So, it seems like robot buying that did go on during the pandemic was more for targeted applications than any widespread robot implementations. And when it comes to adopting robots for social distancing purposes specifically, the overall response of those surveyed was actually weak in this area. Only about 16% of respondents indicated that social distancing was a factor that drove their decision to purchase new robots. More prominent reasons for robot purchases were more the typical reasons like reducing labor costs, that was noted by 62% of respondents. Increasing capacity, 54% of respondents cited that. And navigating the lack of available workers for industry, 38% of respondents mentioned that. But I should mention here on a related note, that of those who did purchase robots in response to COVID-19, 45% of those indicated that they purchased collaborative robots or cobots with the remaining 55% opting for industrial traditional robots, if you will.
And cobots have been held up this past year as the best robotics solution for social distancing, due to their ability to flexibly work alongside humans when attempting to space out a line or a work cell. So their lower than expected adoption rates among those responding to the pandemic with the purchase of robots, it seems to further highlight that concerns about labor cost and availability, quality and throughput were greater concerns for manufacturers this past year, than specific social distancing concerns.
But one industry vertical that did see a significant uptick in robot investment in 2020 was of medical equipment and device manufacturers. I know that's outside the realm a bit of PMMI, but they of course faced soaring demand in the need for personal protective equipment. And even then, a representative from Epson Robots we talked to said that even in this industry, robots were still largely bought this past year as a way to boost throughput rather than using robots to space out production for social distancing purposes. And you'd almost think in an industry like that, that would be a bigger reason and it wasn't even so much for them.
Riley:
Do you think that's a case of, and this is more your opinion, I guess, is it a case where maybe people weren't expecting it to be this long, whether or not it's the pandemic or the changes in manufacturing? Can you point to a specific reason why they didn't come in for social distancing type purposes? Was it just a case of these were already robots that people were thinking of buying ahead of time? It makes sense, but it doesn't sort of line up with what everybody was, quote, unquote, expecting.
Greenfield:
Yeah, and one thing, I mean, we don't know for sure what specific reasons are, because they will vary from industry to industry and plant to plant. But, I mean, as we know, as we heard in some of the cases through the news the past year in some plants, they didn't really do much social distancing, even though they knew they should, so that's certainly a factor in that.
And I think another factor in that is just uncertainty about where things were headed during this past year. Those two things probably factored in the uncertainty and in some cases, just that, that was surprisingly not high up on the deciding factors for a lot of manufacturers.
Riley:
Yeah, and I didn't want to frame it that way. I was thinking that it gives that little bit of impression that the safety of the worker wasn't necessarily driving, wasn't the impetus for getting these robotics, even though everybody knew this was an issue, but it wasn't the priority that yeah, we need to space everybody out. So, we'll move on to more technical manufacturing things rather than try to deal with social issues right now.
Greenfield:
Yeah, because we're inferring that, because they didn't say why they didn't, they just said that was not an issue for them, so we have to infer from there, so yeah.
Riley:
So, let's say, going forward, now we know and this is where we are and things have changed and new normal is the word, but things have moved to a different place in terms of how manufacturers and operations work. So what are the expectations around robotics use in production operations that you're going to see ramping up now that we are slowly but surely coming out of this?
Greenfield:
Well, all the robotic suppliers that I've spoken with, they still remain very bullish on the future for their technologies. This past year may have represented a slow down as it did for most businesses, but it has not changed their outlook. And that's especially true as news around the COVID vaccine rollout keeps getting better and better. So, these suppliers are expecting that demand will return in industry, where some nervousness about the overall business outlook had slowed robotic adoption.
But one potential caveat to suppliers' high expectations is that our survey results were a bit more modest than what I've been hearing in general. And the survey results showed that slightly less than a quarter of respondents were reporting that they plan to add robots in the next year. Now, of those respondents, 56% plan to purchase cobots and 43% plan to purchase industrial robots, which is interesting since these numbers indicate something of a reversal from what we saw in 2020 with industrial robots selling at a faster pace than cobots.
And with that said, I should point out that some suppliers we spoke with suggested the lower expectations we're seeing lined up now for 2021 in our survey, might be a bit misleading and one of the reasons they gave for that is one supplier noted that installations of traditional fixed industrial robot systems sometimes take as long as nine to 15 months. So, that can mean that many respondents who indicated they don't plan to add more robots this year in terms of buying, may already have big projects underway that are going to take them through this year, so that was something to consider as well.
Riley:
Yeah, I wonder if that also goes to our previous discussion where if these things were already in motion to happen in 2021 and this stuff all started happening in 2020, maybe people had already sort of started down this path for whatever reason, and that's why they weren't adding them at a quicker pace as you just indicated, so that makes sense.
Greenfield:
Yep.
Riley:
Outside of the robotic arms for pick and place or end of the packaging or processing line palletizing operations, you've touched a little bit on cobots and they are the new big thing that everybody seems to talk about when talking about robots, but are there other robotic technologies that are getting ready now for prime time now that could help CPG production operations?
Greenfield:
Absolutely, and one area of robot technology that I think gets overlooked when talking about robots in general, and those are autonomous mobile robots. And I guess since these robots are essentially moving platforms, they don't generate the same level of interest as high-speed pick and place robots or the highly dexterous six-axis robots that we all see at industry events. But these automated mobile robots can really deliver big benefits to production operations, as well as warehousing and shipping applications. Not only for their ability to carry heavy loads and navigate safely throughout a facility, but also to help address social distancing concerns, where that is an issue, as we saw from the respondents, that was an issue for a decent number of them, just not as high as we thought.
Greenfield:
But these robots, these autonomous mobile robots, they automatically calculate the best route for material transportation as they navigate safely around people and obstacles without requiring the magnetic floor tapes and other guides that previous versions, the automated guided vehicles that were not autonomous, required. And these core capabilities make these types of robots a really effective tool for companies looking to improve flexibility, maximize floor layout options. And a good example of this is one that was highlighted really prominently at PACK EXPO Connects this year and that's the HD-1500 from Omron. And as you can infer from his name, it can carry up to 1500 kilograms, which is about 3,300 pounds, so that's definitely in the packaging and palletizing sweet spot for being able to carry that level of a payload.
Riley:
Absolutely, so we're basically, if I'm picturing this correctly, we're talking about a robot moving on its own, that's going to take a load that big, like you said, 3000 pounds plus, and move it wherever it needs to be in the plant around people, other objects, things like that.
Greenfield:
Yeah, it's outfitted with sensors, Lidar, a type of radar essentially and multiple sensors all around the front bank. So as it moves around, as people walk in its path, I mean, you've probably some of these videos of this, they slow and or stop as necessary. They can move around poles, so it's whether the obstacles are fixed or moving, it really doesn't matter with these. You just basically tell it where to go and it figures out the best way to go there based on the internal mapping technology in it, of how it knows to navigate the facility, so it's very interesting.
Riley:
Yeah, it's really cool. A guy driving a forklift around, honking the horn around the corner and stuff like that, versus this sensors, which I guess, like you explained saying it was an autonomous vehicle, it's like the cars without the people driving them, where they have the setup for you to just sit back and it just takes you where you need to go. And I could see that being an application that would absolutely work in CPG plants at the very least at the end of the line with palletizing and things like that, so that's really interesting.
Greenfield:
And carrying materials to the different work cells. I saw this, it wasn't at a CPG plant, it was at ValPak in Florida, where they print all the coupons you get in the mail. It's a massive, massive printing operation. And every work cell had people in it manning, operating the machines and reviewing production and doing that. But in between the work cells, about the only people walking through were the people in the tour group that I was in, that was being shown this facility. The workers pretty much stay at their work cell locations and observe and interact with the machinery. They're not running back and forth between work cells. There was all of these autonomous mobile robots, moving materials to the workers where needed, moving finished goods to shipping, what have you. But yeah, people weren't running around the facilities, but the mobile robots certainly were.
Riley:
That's cool. And you touched on it, but it doesn't have, I remember the previous iteration of this had to have tracks on the ground for them to run along almost like little trains or things like that, or magnetic guides, like you said, but these being more free-flowing with the sensors, almost like a Roomba running through the house.
Greenfield:
Exactly.
Riley:
Okay. Well, as the Director of Content at Automation World, you're looking at trends across a whole bunch of industries, and for people that are listening, that covers things from huge oil operations and things like that down to our packaging and processing type plants. So, for the CPG market, what would you say are the biggest trends that we should be paying most attention to today?
Greenfield:
I would advise watching two things. And one of those is end of arm tooling trends and the other is the increasing incorporation of vision technologies into collaborative robots. And, I guess, we'll start off talking about the end of arm tooling. Vendors have made big leaps in increasing the agility and intelligence at the end of the robot arm here over the past several years. And this is particularly crucial in applications such as food and beverage, where things like tomatoes or baked goods can't be grabbed with force. And the human hand has been the preferred method for handling these kinds of items, because we can adjust our grip based on feedback between the hand and the brain to tell what's happening when we grip an object. And based on that feedback, we readjust or hold the item differently as we handle it and move it from one location to the next.
Greenfield:
And now, that can be done using sensors in the end effector and feeding that information back into the robot controller, so it can readjust its grip before and while making a motion based on input from the sensors in the end of arm tooling. And new gripper designs are also helping robots perform better. For example, changeovers of tooling are becoming much, much easier. This used to be a really time-consuming, labor intensive process where workers would unbolt one tool and then bolt on another to process a different batch of goods. And that could involve switching of the robot programming for the robot to be able to recognize and operate properly with a new tool. But now, these end of arm tooling changes are much easier. For example, Universal Robots has its UR+ line for making end of arm tooling changes easier and it works with tooling from multiple suppliers as the tools have been designed to work in a plugin produce fashion with Universal Robots.
Greenfield:
And some end of arm tools can now be more easily adjusted to handle an array of different sized products without being switched over, so this is a big advance when you need to do a change over in seconds rather than hours. And the other thing that I mentioned was about the incorporation of vision with cobots and to mentioned Omron again at PACK EXPO Connects this year, they highlighted another good example of this with the company's incorporation of its own FH series, 3D vision system with its TM collaborative robot. And Omron developed this 3D camera to solve robotic bin picking applications so that it can guide a robot in picking known objects with random overlapping positions out of a bin.
Greenfield:
And traditionally, that had been a very difficult task to automate due to the varying weights, shapes and orientations of the objects in the bin that require 3D location and responding different forces during the picking process. And that FH series 3D camera locates the various objects in the bin, sends their coordinates and positions to the robot and then the cobot software makes the advanced calculations required for optimized trajectory of the robot arm and then the force with end effector to pick up the objects based on input from the camera. And this camera can be integrated with a variety of robots. For example, Omron explained that the combination of the 3D camera and the collaborative robot can be assembled on top of Omron's mobile robot, like the HD 1500 that we were talking about earlier, to pick parts from a row of multiple bins and place them in another location.
Riley:
It almost sounds like it's making, or the way the technology has evolved is that robotics and automation are, and I want to use the word, but it's way less intimidating than it seemed a few years ago. It's not the big industrial cages with the robot in it that you're like, it's almost, again, you see them either on a trade show floor in a plant and it's like, hands-off, this is this big, intimidating, highly technical piece of equipment that could, quote, unquote, hurt you if you got too close or whatever.
And now it just seems like it's advanced to where, like you said, with the vision technology and the sensors, that it can tell where humans are. It can tell where things are and just move and adapt around us. It can pick up things of different size and shape and density. And it's amazing how quickly that window have opened to possibilities.
Greenfield:
Yeah, absolutely. I mean, it's probably been five or six years ago now, but when some of the first early ease of collaborative robotic programming systems were coming out, I actually did an article about how easy it was to program that even a journalist could do it. I actually programmed a robot to do a... And it was just by moving the arm through the paces. I mean, it was very rudimentary obviously, on a trade show floor, but just goes to show to your point exactly, that it's much easier to interact with them and program them and operate them than it ever has been historically.
Riley:
Interesting. Okay, so you sort of are usually on the ground floor with most of this, because you follow the industry so closely, so this will be our last thing to wrap it up. Are there any particular things in the pipeline that our audience should be aware of that could have an impact on their operations in the next few years beyond the things you've already touched on?
Greenfield:
Well, it's actually an extension of something we were just talking about, that I think is something really interesting to keep an eye on and that's what I'm calling, for lack of a better word, the “cobotitization” of industrial robots and that's where-
Riley:
I like that.
Greenfield:
Okay, we'll make that word happen. It's basically where collaborative robot capabilities, like you were just talking about, are brought into high-speed heavy payload industrial robots, the ones typically behind the cages, as you were mentioning. And this is important, because despite the headway cobots have made in industry, they're designed basically really relegates them to performing fairly simple, repetitive tasks that are typically done by humans. But the high-speed, heavy lifting that's done by industrial robots remains outside the scope of most cobot designs, but that's changing with work being done by a number of companies from established companies like Mitsubishi to new startups, like Veo Robotics.
Greenfield:
And to give an example of what Mitsubishi is doing, they're working with startup Realtime Robotics to bring its technological capabilities into Mitsubishi's range of industrial robotic applications. And I should note here that Mitsubishi does not offer a specially designed cobot, they prefer to use a combination of sensor and safety technologies to ensure collaborative use of industrial robots, working alongside people. And Mitsubishi says they prefer this approach so that users can still have access to the high precision capabilities of its industrial robots, but use them in cobot type applications, alongside people. And cameras used in this system detect and send information about the presence and position of people and objects in the work cell and the motion of the robots are controlled by Realtime Robotics' motion planning software to avoid collisions with each other, as they're performing their duties. And of course, with people that may be in the work cell.
Greenfield:
And with the Realtime Robotics software, the robots can react to each other's presence by recognizing when collisions are possible, based on positioning of the objects to be picked, as well as the positions of the robots themselves moving across that plane. And this motion planning software from Realtime Robotics is what's referred to as robot agnostic, meaning that it can work with any type of robot, not just the Mitsubishi one that they're working with in the demonstration they provided so far. And the other company, I mentioned, Veo Robotics, they've developed a system to make industrial robots operate collaboratively as well and that's with their FreeMove system, which is composed of four to eight cameras, sensors and a computing platform that uses algorithms specifically built for this application.
Greenfield:
And the FreeMove system, what it does, it uses computer vision to do a 3D analysis of the workspace to determine placement of fixed machinery, robots and people and then it projects all of the robot's potential positions over time in that work cell. And using the ISO 10 to 18 robot work cell safety standard as its base, FreeMove is designed to basically ensure that robots are never a hazard to a person so that a work cell can be designed in which humans and machines can work together. And Clara Vu, who's the co-founder and Chief Technology Officer at Veo told me that FreeMove is not just for application and for work cell safety, but it can be applied to applications through an entire line or an entire factory, so it's almost like a plant wide safety system, wherever you might have any type of moving machinery or robots in place.
Greenfield:
And just to show how seriously this is being taken, Veo currently has relationships with ABB, FANUC, KUKA, Yaskawa and their system is currently being used in an aerospace, automotive, household appliance and construction equipment manufacturing sites, though none of the current end-users are allowing the company to divulge their names just yet, but that's not surprising with a new technology. But the Advanced Robotics for Manufacturing Institute, which is a government funded consortium, has made its use of the FreeMove system public and if you're interested in seeing more about that, and you can access that info at the Advanced Robotics for Manufacturing site at arminstitute.org.
Riley:
Fantastic. Well, this was great and then I just want to, before we sign off, to make sure for our listeners to head over to iTunes or Spotify or wherever you get your podcasts and make sure you smash that subscribe button for Automation World Gets Your Questions Answered with David Greenfield. I want to thank you for taking the time today to come on here and talk robots and automation with us, David.
Greenfield:
Yeah, thanks for having me. This was fun being on the other side of the microphone. I like this.
Latest In Robotics
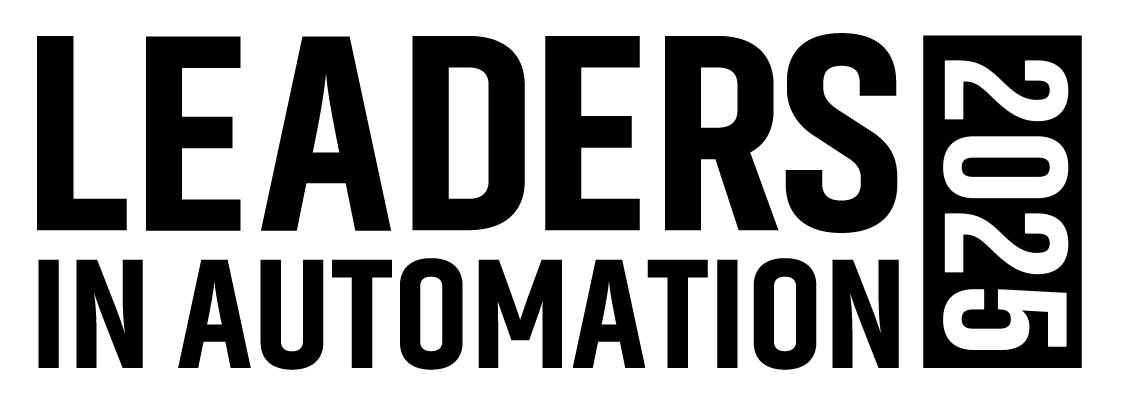
Leaders relevant to this content: