Do Collaborative Robots Need Safety Risk Assessments?
TRANSCRIPT
David Greenfield
Welcome to the Automation World Gets Your Questions Answered podcast where we connect with industry experts to get the answers you need about industrial automation technologies.
I'm David Greenfield, editor in chief of Automation World and the question will be answering in this episode is: Do collaborative robots need safety risk assessments? And joining me to answer this question is Devin Murray with Schmersal USA, a supplier of safety switch gear devices and systems for personnel and machine protection. Devin works in Schmersal's technical engineering services division called tec.nicum, which focuses on machine safety such as risk assessments, validations and training.
So thanks for joining me today, Devin.
Devin Murray
Yeah. My pleasure. Thanks for having me.
David Greenfield
So you know Devin, let's make sure everyone understands you know what we're talking about here today. You know, what defines a collaborative robot, which are often referred to as cobots, and how are they different from regular industrial robots?
Devin Murray
So a collaborative robot, as you mentioned commonly called a cobot, is a robot which is essentially designed in introduced to the industry to work directly with the human operator in a safe manner. Technically speaking, it's a robot designed to work in a collaborative operation which is defined as a state in which purposely designed robot systems and an operator work concurrently in a space during production operations. Basically, characteristics of a collaborative robot include smooth, round edges to minimize pinch points, slow speed and lighter load capabilities, which differs from the typical industrial robot.
David Greenfield
So what about safety standards? Cause you know, we all know about the safety standards, you know, with the standard industrial robots. And they often have to be caged. And you know, light curtains around them and all that. What about safety standards related to cobots? Are there any of those that have been implemented yet?
Devin Murray
Yes, uh, typically I've seen with industrial settings there were vast advancements in this case with the collaborative robot technology followed by safety regulations to help ensure a safe working environment. The first documented cobot was introduced in the mid to late ‘90s and some of the well-known industrial robot manufacturers that we know today released their versions of collaborative robots in the early 2000s. In 2012, the standard which defined safety requirements for industrial robots, which is ISO 10218, which is harmonized to our North American standard ANSI/RIA 15.06 referenced collaborative robots. And then in 2016, the technical standard ISO/TS15066 was released to provide further guidance on safe implementation of collaborative applications. So yes, there are definitely standards and regulations in place today.
David Greenfield
OK, so it's not a grey area anymore. Like uh, it was a while back. Where I can remember some discussions of that. It's like, yeah, it's safe. It's got all these protective mechanisms on it, but OSHA might see it differently.
Devin Murray
Yeah. There's things in place now for sure.
David Greenfield
So since cobots are you know designed to be safe for humans to work alongside, I mean that's their whole purpose and intent of these types of robots, are risk assessments of a cobot installation needed before work begins.
Devin Murray
So referring back to ISO/TS15066 which I just mentioned, it clearly calls out in black and white that a risk assessment is necessary to identify the hazards and risk associated with a collaborative robot system application. You'll read that the integrator shall conduct a risk assessment as described by ISO 10218 and ANSI/RIA15.06. So yes, a risk assessment is absolutely needed for a collaborative robot application.
David Greenfield
It has the word, shall there and shall means, will, should, and all of the above.
Devin Murray
Yep, they must do it.
David Greenfield
So, you know, based on your experience, what are some hazards that are common or often overlooked when it comes to users implementing cobot applications.
Devin Murray
The risk assessment I just mentioned is commonly overlooked for sure. Uh, I will say typical application hazards, impact questions, trapping, projectiles, and I say these typical hazards because they are often overlooked once the term collaborative robot is used, I mentioned earlier about, you know, smooth edges, minimizing the pinch points, slow speeds and low payload capabilities, and sometimes that's taken as this is a safe piece of equipment and all is good. So those typical common hazards are missed, but this is why a risk assessment is required. So we gotta look at the loads, the materials, the robot torque. One of the the biggest overlook has its I've probably seen is the actual cobot location. So you have to look at now, are you creating a crushing or a trapping hazard with the cobot or is that cobot position high enough where it can come into contact with an operator’s head which is not allowed at all. So I would say the risk assessment, those basic ISO 12100 hazards and the position of the cobot are commonly overlooked.
David Greenfield
And you mentioned too, they're just a side question off of this is you mentioned that the risk assessments are often overlooked. Is that something that's particular to cobots based on what you've seen or is this something that's often kind of overlooked for other industrial machinery as well?
Devin Murray
So I would say it's often overlooked, but more so with the cobot. Just because of that, that misconception that you know, it's inherently safe, so we're good to go. So risk assessment in my experience are typically overlooked, but I'm seeing it more so with with cobots nowadays.
David Greenfield
So are there any options that you recommend to help ensure safe cobot operations alongside humans?
Devin Murray
Yes, so ISO/TS15066 — they define four methods of collaborative operation which are safe rated monitor stop, hand guiding, speed and separation monitoring, and power and force limiting. And we look at each one of those individually, there's the safety rated monitor stop is where the cobot motion is stopped while the operator is within that collaborative workspace; hand guiding here the motion of the collaborative robot is controlled completely by the operator, and this can be during a point-based teaching where the operator is, you know, physically showing the robot or programming the robot for a defined motion or path. This can also be seen with applications such as a lift assist where an operator is guiding a robot arm to move a load. With speed and separation monitoring, now we begin seeing that that robot and human moving concurrently within the collaborative workspace, so that that's true collaborative, you know, robot application. As the human approaches the cobot, the cobot will decrease its speed to a slower safe pace. And once the operator enters that define protective separation distance, the cobot will enter into a protective stop. And the last one would be the power and force limiting where you have identified that there will be contact with the cobot and operator either by accident or on purpose. And as such, the cobot power and force will be limited so that it will not exceed the allowable thresholds defined by the standard. ISO/TS15066 looks at different regions of the human body lists the maximum pressures and forces allowed that can be experienced by the operator and that the cobot cannot exceed. OK, now my explanation of these four methods are simplified to say the least, but the standards state that you have to select the one or more of these methods depending on your application to help ensure a safe operation with cobots and humans.
David Greenfield
Your answers were, you know, uh, you know basic and you know, structured down because each of these could be books on their own, of course.
Devin Murray
Exactly.
David Greenfield
So yeah, so you know speaking that let me ask you about a side question about one of those. You mentioned the speed and separation monitoring I've been seeing quite a bit about that over the past few years now in terms of because that's being applied to industrial robots to allow them to operate collaboratively. Again, from your based on your experience, you know as a risk assessment machine safety expert in this, do those seem to be as of as effective in enabling industrial robots to work collaboratively as your standard collaborative robots that are designed as such to operate alongside humans.
Devin Murray
That very dependent on the application, right? So we're going back to, you know, one of the first things we spoke about was the design of the collaborative robot where either again we have those smooth edges and the slow speeds and the lower payloads, where the industrial robot was designed and put into production to handle those tasks which are not really acceptable for the human or not for human not to be able to do. So we look at those typical applications and they are inherently dangerous to the operator. So that's one of the reasons why you would typically see, you know those industrial robots fully engaged with the fencing. And now again, it completely depends on the application right cause. Because you can't have an industrial robot that's doing a task that is of a, you know, slower speed perhaps, or moving a payload that’s not dangerous where you can incorporate, you know, laser scanner like you mentioned to do speed and a separation monitoring. You can apply some of these collaborative robot methods to industrial robots, but it completely depends on the application and then more than likely when you start looking into, you know like speed and separation monitoring is going fall back into the collaborate realm.
David Greenfield
Well, you know it makes sense and it's not too surprising after all these years covering automation is that I find out when I ask questions like: can this do that or this do that or will this work here? The answer almost 90% of the time is: It depends. You know, it really does depend on the application. There's lots of things to consider.
Devin Murray
For sure for sure.
David Greenfield
So Devin, is there anything about these cobot safety standards that we've been speaking about that are more difficult to implement than other machinery risk assessment procedures?
Devin Murray
At the core of every Type C standard, such as you know the ISO 10218 or safety specification like the ISO/TS15066 lies the same method or approach, right? It's identify the hazards, identify the risk, and then use this safety standard or document as a guidance to design safe measures. And from that aspect, the cobot safety standards, are just like any other. But what makes it unique, and perhaps you know slightly more difficult is the fact that contact with the point of operation or with, you know, a moving machine, which is the cobot, can be expected and accepted, which is different than most other safety standards where you know the main goal is to guard against the point of operation. So you know, being able to validate and document the justification for one of the four methods we just spoke about, to say that, you know, we're going to allow this human and cobot to work concurrently together in the same workspace is probably the most challenging, you know, especially if you're looking at something like power and force limiting where there are no other protective safeguarding measures like a scanner or a light curtain. And so that can be difficult. But you know the implementation is definitely achievable.
David Greenfield
So one last question, Devin, you know, considering everything we've spoken about here today, would you say that collaborative robots are safe to use?
Devin Murray
I would say that if implemented correctly, collaborative robots can offer a safe means to many industrial applications. You just have to remember that even though collaborative robots were intended to be an inherently safe, a collaborative operation is only as safe as you make it.
David Greenfield
So again, it depends, right?
Devin Murray
Yes, it depends, for sure.
David Greenfield
Well, thank you again for joining me for this podcast, Devin, and thanks of course to all of our listeners and please keep watching this space for more installments of Automation World Gets Your Questions Answered and remember you can find us online at automationworld.com to stay on top of the latest industrial automation technology insights, trends and news.
Companies in this Article
Latest In Robotics
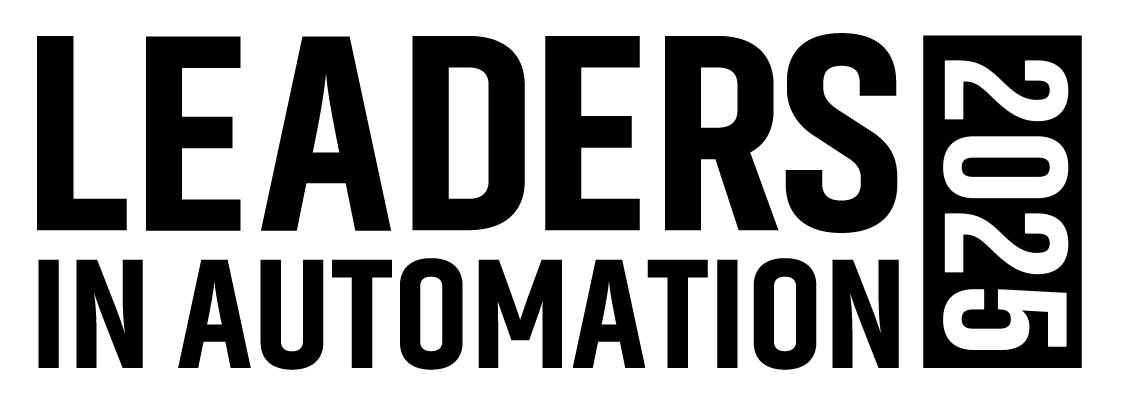
Leaders relevant to this content: