Read the full transcript below
David Greenfield: Welcome to the Automation World Gets Your Questions Answered podcast, where we connect with industry experts to get the answers you need about industrial automation technologies. And you can find even more answers by subscribing to automation world at Subscribe AutomationWorld.com
I'm David Greenfield, Director of Content for Automation World. And the question we'll be answering in this episode is, what is the machine risk assessment? Joining me to answer this question is Devin Murray from Schmersal, a supplier of safety switchgear devices and systems for personal and machine protection, and Devin works specifically in Schmersal's technical engineering services division, which focuses on machine safety, such as risk assessments, validations, and training. So thanks for joining me today, Devin.
Devin Murray: Oh, my pleasure. Thanks for having me.
David Greenfield: Absolutely. So, you know, let's get right to the question at hand, Devin, you know, just what is a machine risk assessment?
Devin Murray: Sure thing. So essentially, machine risk assessment is a systematic approach to identify reasonably foreseeable hazards. And I want to emphasize those words ready reasonably foreseeable hazards to evaluate and and quantify the risks associated with those hazards. And then also to provide a solution to eliminate or minimize exposure to those hazards, and essentially, also re evaluating to make sure that all hazards have been addressed and guarded to an acceptable level. But with that, right, I wanted to just take a quick second and go over a misconception with the idea of a risk assessment, right? Because a lot of times, I have the discussion where we look at a machine, and we identify the hazards and identify the risks, and some things that that itself is the risk assessment where it's not. Right, that's the first part, right? The first part is identifying those reasonable foreseeable hazards. That's actually the view risk analysis, identifying those hazards and the risks, and then finding that solution to help minimize or eliminate those hazards and risk. That overall process is the machine or risk assessment.
David Greenfield: Okay, thanks for clarifying those aspects of that. So are these machine risk assessments? Are they required for manufacturers?
Devin Murray: Well, to answer that, I want to focus on OSHA, right because OSHA as we all know, that's the the law of the land here in the United States. And as you know, they have the Occupational Safety and Health Act that was established in 1970s. Right. And with that, there's the general duty clause. And under regulation 29 CFR 1910. It states that the employer shall provide a workplace free of recognized hazards, right, shall and if we know anything from standards, when we see shout, I mean that we have to do it. Right. So OSHA says we have to provide a workplace free to recognize hazards. And if we, you dig deeper into this app, and we look at CFR 19 10.2 12. What are the requirements for all machines? They start off for that regulation starts off by stating that hazard shall be guarded. Right. So again, we have that shell statement. And if we go back to you know what a risk assessment is, it's identifying hazards. As you know, OSHA says we shall do and it's gardeners hazards, as OSHA says, We shall do so when we look at those requirements from OSHA. Yes, right or written seven is required. The actual process and you know, what it looks like? That's completely up to you. There's regulations and standards in the industry that you can use as guidance. But the actual, you know, the process itself that that is required?
David Greenfield: Yeah, there's not a lot of gray area with a word like shall. So based on the OSHA regulations, you're mentioning there, you know, it sounds like all equipment in a manufacturing or a processing plant does require a risk assessment. Is that a correct assumption? Or is it just certain types of equipment that fall within the scope of machine risk assessment?
Devin Murray: So, so even within that, you know, I want to, again, go back to to OSHA, right, because, again, they're the law of the land, right. And, you know, OSHA gives us the definition of a machine. And they state that, you know, the three fundamental areas, the, the point of operation, the power transmission device, and the operating controls. And if we look at, you know, your equipment, and if they have these three fundamental areas, then that's a machine. And that would fall under, you know, the machine risk assessment. And if you look at some other standards, like ISO 12 100, for example, or even anti b 11.0, they give you definitions of a machine as well. And they have that same fundamental definition for the three areas, and they elaborate a little more. But again, you have a definition of a machine. So if it falls within this definition, you know, that's gonna require a machine and risk assessment. Now, in saying that, though, no, there are going to be some machines that require a more in depth evaluation. Maybe be some machines that, you know, may not have or may not pose any significant injuries. Well, we can document that right, you can document that and say, okay, you know, this machine was assessed on this date by these individuals. And it was concluded that there were no, you know, reasonably foreseeable hazards to take into consideration. But in order to get to that point, you have to first assess it. Right. So any machine like you have to do a risk assessment on for sure.
David Greenfield: So, we've been talking about machine risk assessments in the OSHA regulation at a pretty high general level, you know, but drilling in a little more specifically, you know, what about machines that are designed to be inherently safe, like a collaborative robot, for example, you know, does the OSHA regulation around machine risk assessment applied to them, too?
Devin Murray: Oh, absolutely. Absolutely, for sure. And so if we go back to that, that general duty clause, right, it states that, you know, the employee shall make sure that we have a safe working environment. So that includes collab robots as well. And now, again, I look at the misconception with collaborative robots, because like you said, They're designed to be inherently safe. So a lot of times, I've seen situations where, you know, and usually with the by collab robot, right, inside the manuals, it says it meets these standards, it says it's inherently safe. So, you know, they, they buy it, they purchase it, they plop it into the application, and they automatically assume that it's safe. And that's not the case. When you look at the standards, surrounding collabora, robots, such as ISO TS 15066 and ISO 10218, and, you know, bring it back home ANSI R15.06, they all state, a risk assessment shall be carried out, right, again, that shell statement. And that's really because the cloud robot can be used in an application that's unsafe, right? So if you're using the Collaborate robot, and it's true collaborative form, where it's in the same and working envelope as the operator, and that club robot that's been designed to be inherently safe is now you know, moving apart, that's, you know, 400 degrees Fahrenheit. That's a hazard. And we have to do an assessment to identify that hazard. So, so yes, even, you know, collateral blocks or equipment that's been designed to be inherently safe, we still have to assess those in the environment.
David Greenfield: So since there's clearly no escaping the regulation, as you made very clear here, you know, how are the completed risk assessments that shall be performed? How were those filed and recorded in order to be in compliance?
Devin Murray: Yeah, so so so again, the process for the risk assessment, it's completely up to you, how do you want to go about doing it, you know, what are going to be your parameters for for the risk? You know, what are you using for that arbitrary quantitative number? That HRM number, that hazard rating number, right? That's completely up to you. Right? But whatever you use, you want to make sure that it's standardized throughout the company and throughout your site, right. You want to make sure that you have something that you can use for the machines for your company or for your site. So you want to make sure that it makes sense, right because If you cannot take the principles and concepts surrounding a CNC lathe, right, and then try to apply them to a printing press, right, so you want to make sure that you have something that standardizes. And that makes sense for for your company, and to show that you are doing your due diligence, again to, to fulfill that that general duty close.
David Greenfield: Okay. So, you know, since this is something that again, it will hit on the shall thing that shall be performed, but it's fairly wide open as to how it's done. There's not a lot of as you said, there's not a lot of specific guidelines about how you go about it, or how you record it, you know, but who is ultimately responsible for the machine risk assessment in a typical manufacturing or processing facility?
Devin Murray: Yeah. So, again, according to the OSHA is the employer, right, so the employee responsible for the safe working right in the for this machine. However, if you, you know, look into ANSI B11, which is a recognized relevant safety standard ANSI B11.0. Specifically, that calls out requirements for both the supplier or the machine builder and the end user. So we'll see that there's requirements for both the OEM and the end user to conduct this risk assessment. And you'll also see inside ANSI B11.0, that up until the actual installation, there's potential for the OEM and the end user to collaborate on the risk assessment. As far as like the individual people who should be part of the risk assessment team, but like you said, going back to the manufacturing side, you want to have people that know the machine, right. So definitely operators, maintenance personnel, you want to have management there are they management may not use the machine, but you know, safety should be driven from the top down if you want to have a you know, a true safety culture. And so this should be part of the, the assessment team, as well as EHS personnel. So it's definitely a team effort. But yeah, that's who should be a part of it. And again, the the OEM has a part of it for the risk assessment, as well as the end user.
David Greenfield: Okay, so now that we know who let's get to the where, you know, where do you recommend the manufacturers? You know, start with the risk assessment process?
Devin Murray: Yeah. So, again, you want to start by finding something that as a manufacturer, you can standardize on, right. So you want to see if there's a Type C standard that's out there that applies to your machine. And I guess I should explain what a Type C standard is. So a safety standard can be broken up into two four types. There's a type ace, then it watches for for general safety. So I've been referring back to anti b 11.0, whether that's for safety or machinery as well, Joe, let's take a standard. Then there's a type B, one standard, which is for certain aspects of safety, such as ISO 13849, for example, that looks at the safety functions on a machine, there's a certain aspect of safety. Then there's also a B to standard was looks at the requirements for a safety device, such as ISO 13850, requirement for an E style. And then there's a Type C standard that looks at a specific machine, right. So if you're a manufacturer of you know, CNC lathes, then you want to look at, for example, ANSI B11.22. Right. Or if you are making robots and robot cells, then there's that ANSI RA1506. So you want to you want to start with that right? See what type C standards apply to your machine, because that's going to give you some some guidance on those reasonable foreseeable hazards that you want to take into consideration for your risk assessment.
David Greenfield: So one last question and we've covered in our conversation, we've covered the what the who and the where, so to speak. So So let's hit the when you know, when should the risk assessment process actually start?
Devin Murray: Perfect, good question. So honestly, the sooner the better. Right so the risk assessment ship again, early and the concepts of designs and when you look at the the hierarchy of machine safety, you first want to see if you can design the hazard out, right and if you can't design it out, then you move on to Okay, can we can we substitute the hazards for something that's dangerous or it can we provide some type of control measures like Hardy guards or I see the light curtain for example, right? But the first thing is can we design it out. So, if we are, you know, having this assessment process started during the design conversation, then you know we can we can identify these these hazards and try our best to design them out or or make them even less hazardous. So the earlier the better. And again, going back to the anti B 11.0. They stayed in there too, that this segment should begin as early as possible and then, you know, updated and validated as the design matures. So there should be milestones in place where you are revisiting, though the hazards and risks of that machine as you continue that design process up until installation.
David Greenfield: Well, thank you for joining me for this podcast. Devin. I really appreciate it. And thanks, of course to all of our listeners. And please keep watching this space for more installments of Automation World Gets Your Questions Answered. And remember that you can find us online at AutomationWorld.com. And subscribe to our print magazine at SubscribeAW.com to stay on top of the latest industrial automation technology insights, trends, and news.
Companies in this Article
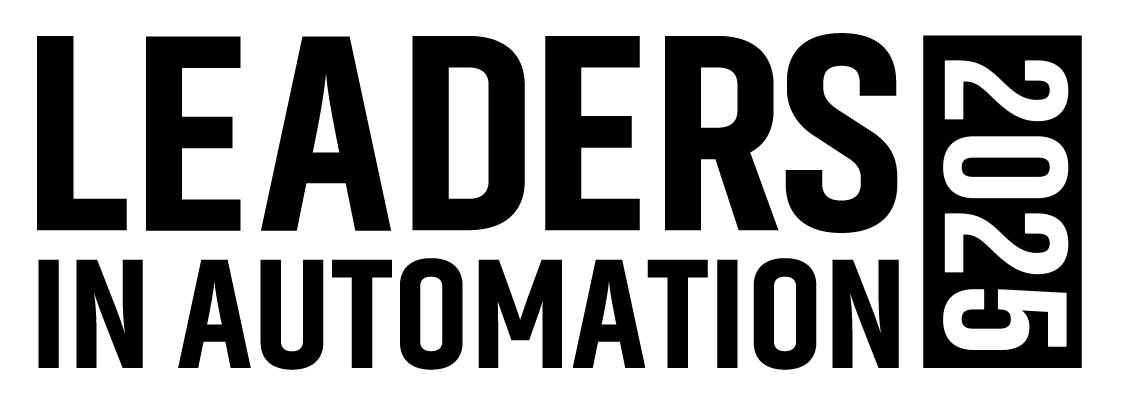
Leaders relevant to this content: