TURCK and CODESYS IEC 61131-3 automation software are changing the design and production of Innocar's specialized tank trucks and trailers. Innocar’s main products are trucks and trailers for transporting petroleum products, street flusher trucks, fire trucks and refueling trucks at airports. Those tankers are defined by several standards and regulations and mainly in the case of refuellers. There are many sensors necessary to ensure the proper function of the system. Until very recently Innocar used an intelligent relay to pick up signals and carry out the logic of operations on the truck. However, this way of doing things was not optimal. A solution was needed to reduce the complexity of the electrical installation by approaching certain PLC suppliers while making it possible to offer advantages of functions and data to customers. Read why CODESYS Automation Software allows both the manufacturer and its customer to select products from many different suppliers, with the flexibility to use the optimal components for its configuration without being dependent on manufacturers and their delivery times.
THE CHALLENGE: How it started, why a PLC
Tankers are defined by several standards and regulations and mainly in the case of refuellers. There are many sensors necessary to ensure the proper functioning of the system: Water detection sensors, proximity sensors, anti-overflow, position sensors. Until very recently Innocar used an intelligent relay to pick up signals and carry out the logic of operations on the truck.
- Old system for control.
- Lots of wires.
- Difficult Troubleshooting.
- No redundancy.
- No smart features.
- Device replacement requires configuration.
ON THE WAY TO FIND A SOLUTION: Constraints
Innocar looked for a solution to reduce the complexity of the electrical installation by approaching certain PLC suppliers while making it possible to offer advantages of functions and data to customers. There were constraints to be respected in order to choose the right managers:
- Some customers are located very far and may not have a lot of support.
- Some will operate in areas where the equipment will need to withstand cold temperatures.
- The equipment will be exposed to the elements and must be sturdy.
- Some tanks carry hazardous materials and blocks, like some sensors, must be able to withstand the explosive atmosphere.
- The vibration of a mobile unit.
THE SOLUTION: CODESYS Automation Software and TURCK
It is a compact PLC which supports several types of protocols and programming - all can be done using CODESYS Automation Software. So due to these characteristics Innocar are not limited and can install the PLC both inside the cab and outside the truck.
SOLUTION and ADVANTAGES
With the ease of having remote IO blocks, we therefore began to put more sensors on the unit.
- Analogue temperature sensors for pumps instead of a simple temperature switch sensor.
- Analogue hydraulic level sensor
- Analog pressure sensor
- Buttons and IOL lights with programming that is done directly on CODESYS instead of holding dozens of combinations of lights and buttons of different colors.
- Analogue level sensor for the tank compartments.
- Analogue outputs for the control of the hydraulic load sensing valve by proportional solenoid.
- IOL output to control an electric pilot pneumatic valve manifold.
- Inductive position sensors / limitation sensor.
Thus, we were able to add functions that were not previously offered to the customer thanks to the CODESYS HMI and the advantages were very tangible:
SUMMARY
- TURCK had in his possession an ideal PLC for Innocar’s application, the TBEN series. The TBEN series has a low operating temperature limit of -40 Celsius, a robust housing against vibrations and an IP69K protection class. This compact PLC supports several types of protocols and programming - all can be done using CODESYS Automation Software. So due to these characteristics we are not limited and can install the PLC both inside the cab and outside the truck
- CODESYS is a very interesting programming tool because it allows us, through its accessibility and flexibility, to program in the language that is already familiar to us, either in FBD or ladder.
- In addition, the CODESYS software can be downloaded by the customer, and we can provide access to programming in order to offer the customer the possibility of customizing the HMI display or the data outputs without being dependent on Innocar.
- Thanks to Codesys IEC 61131-3 Automation Software, both the customer and Innocar can select parts from many suppliers. This gives us the flexibility to choose different components without being dependent on a manufacturer and his delivery.
CODESYS
CODESYS is the global market leader of manufacturer-independent IEC 61131-3-automation software, with over 5 million device licenses sold worldwide. More than 500 control system manufacturers, and tens of thousands of companies worldwide use CODESYS’ products. CODESYS is a software platform for industrial automation technology. The core of the platform is the IEC-61131-3 programming tool ‘CODESYS Development System’. It offers users practice-oriented, integrated solutions for the convenient configuration of automation applications. The goal is to provide them with practical support for their daily tasks. Open interfaces, comprehensive security features, and a convenient connection to a cloud-based administration platform make CODESYS a natural Industry 4.0 platform. Edge, fog, or cloud controllers can be developed with CODESYS. Data exchange between any Industrial Internet of Things (IIoT) networks can also be carried out easily. Device manufacturers such as TURCK use CODESYS to implement their own programmable or configurable automation components. For this purpose, they install a runtime system. Using the available product options, the functional scope of their device can be flexibly defined. The options include integrated products for visualization, coordinated motion control, and connection to fieldbus and Industrial Ethernet systems. CODESYS CORPORATION 200 Cummings Center, Suite 272-D Beverly, MA 01915 USA Phone: +1-978-473-7600 E-Mail: [email protected] Store: us.store.codesys.com www.codesys.us
TURCK
TURCK has become a pioneer in industrial automation technology. Their mission, as a leading value-added supplier of products to the factory and process automation markets, is to provide customers with a comprehensive line of quality and advanced technology products in a fast, flexible, and accurate manner. TURCK is focused on the factory and process automation industries and producing products that uphold uncompromising standards for reliability and functionality. TURCK’s products and automation solutions increase the availability and efficiency of your systems, whether they are applied in the chemical and pharmaceutical industry, transport and handling, food and packaging, or in-machine and plant construction. TURCK’S extensive line of products includes thousands of sensors, interface, cord set and connector combinations that meet clients’ needs. Through intensive dialog with customers, we can pair industry-specific knowledge with electronics development and production of the highest level to ensure optimal solutions for all your automation challenges. www.turck.us
INNOCAR
Innocar designs and manufactures specialized trucks. Using the best technology and cutting-edge fabrication techniques, Innocar ensures that every truck is customized for their client. www.innocar.ca
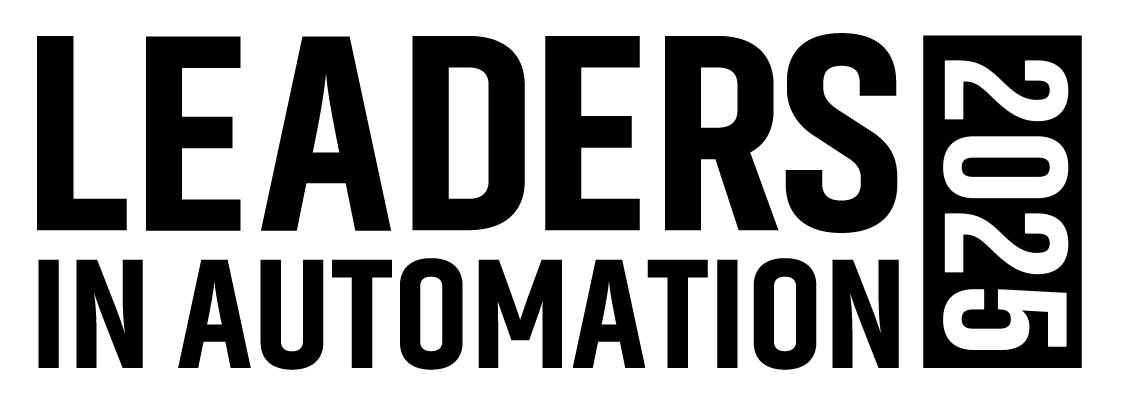
Leaders relevant to this article: