TRANSCRIPT
David Greenfield, Automation World
Welcome to the Automation World Gets Your Questions Answered podcast where we connect with industry experts to get the answers you need about industrial automation technologies. I'm David Greenfield, editor in chief at Automation World. The question will be answering in this episode is what is FDT and joining me to answer this question is Steve Biegacki, managing director of the FDT Group. So thanks for joining me today, Steve.
Steve Biegacki, FDT Group
Yeah. You're welcome. Great to be here. Thanks.
David Greenfield, Automation World
So, you know, let's just start with what is FDT, you know, tell us generally what it is and you know a bit about its history.
Steve Biegacki, FDT Group
Yeah. Sure. So FDT actually stands for field device tool and it was a standard that was started probably 20 plus years ago and it's an open standard. It was created initially to enable multiple devices from multiple manufacturers to become part of a control system without having to have individual tools if you want to configure and monitor those devices. So today its an open standard for industrial automation, integration of networks and also devices. It's an IEC standard 62453. It's an ISA standard 103. It's a Chinese and GPT standard 29618 and there are today, I would say, tens of millions of devices installed in the field that leverage FDT technology and it is supported by all the major control system vendors and device manufacturers.
David Greenfield, Automation World
Alright, thanks for explaining that Steve. So, you know management of plant floor devices from different technology suppliers is definitely not a new issue for the manufacturing and processing industries. And it's an issue that's growing in importance with the digital transformation of industry and the introduction of wearables and the greater use of mobile devices on the plant floor. So how is FDT typically used by manufacturers to address varied device management across industry?
Steve Biegacki, FDT Group
So today, systems that are based on the FDT standard--and that would be both the devices and the actual control systems themselves--that use and embed the FDT specification can provide their users with an integrated environment or an integrated view of what's going on with all the devices in their systems. They can also exchange the information with mobile devices. One thing called out in the latest version of the FDT spec actually provides for the capability to be able to pull up a handheld device or a laptop or your phone and, through a web server, be able to see what's really going on with those devices. So again, devices that utilize the FDT standard now have that capability to share that information wherever it's required.
David Greenfield, Automation World
Now one of the bigger developments to come out of the device interoperability issue is the push towards the greater use of open systems supported by groups like the Open Process Automation Forum and UniversalAutomation.org. How does FDT fit into this?
Steve Biegacki, FDT Group
Yeah, that's a great question. Those standards do a really nice job of identifying how control systems would actually go together, how the actual control algorithms and so on would interoperate together on multiple controllers. But the one thing that the FDT standard does is it actually provides a complement to those systems for this specific purpose of intelligent device management. You know those control systems only act when they get inputs and outputs via sensored information or control. You know, whether it's an actuator or a variable frequency drive or whatever. It might be as an output and the FDT standard enables that connection through the networks to those actual field devices that then provide the information that can be used by those other open standards in the control system space, whether it be in the OPAF standard or the UniversalAutomation.org standard.
David Greenfield, Automation World
OK, understood. This one's kind of a personal question from an editorial point of view—most of the examples that I've seen around the use of FDT tend to be in the processing industries with HART communication devices, etc. But is FDT also applicable in the discrete and batch manufacturing industries?
Steve Biegacki, FDT Group
Yeah, that's a great question. And you know, I think the initial developments, if you will, of the FDT standard really did come out of the process automation space in support of things as you mentioned like the HART protocol and from a network communication standpoint. But one of the ways that the FDT standard is actually configured and architected is that it enables us to communicate over multiple communication standards. So whether that be Profibus, DeviceNet, EtherNet/IP and even EtherCAT. So I would say that the way FDT is used today, it is able to support both factory automation and process automation because of the way it's put together and because of the networks it supports and also the types of devices it can support. It's a little broader than just the process automation space and, by the way, I mean there are process automation applications too that are kind of these hybrid applications that are a mix of both process instrumentation and factory automation. You know, actuators and sensors like, for example, IO-Link, that's more for discrete type of devices, but those could be used in a hybrid application. So FDT supports both factory and process applications.
David Greenfield, Automation World
Thanks for explaining that, Steve. Because based on everything I have seen about it over the years, it seems pretty agnostic in terms of application, but I just kept seeing the process industry examples, so it got me to start to wonder if it is actually more specific to the process industries? So along those lines, can you share an example or two of FDT's use in specific industry applications?
Steve Biegacki, FDT Group
I think one of the one major application that it gets used in is with asset management systems. You know, this is the ability to see what's actually going on with the control system itself and the devices. And, a lot of times, asset management is referred to as monitoring the health and operation of a device. We think of asset management a little broader than that and some of the customers that we talked to are trying to actually manage the ultimate asset. In other words, is the process operating right? And by the way, that process is made up of a bunch of different sensors and actuators. So we're trying to provide a unified view of what that asset looks like to make sure that it's operating at peak performance and that its being the most effective it can be in delivering the results it needs to. So asset management is one application example that we see the FDT technology used in where we're bringing things into that asset management system. The other thing I would mention is the ability to configure multiple devices in a control system. We have a number of people we work with that use the standard, like PACTware for example, which is a kind of a third party tool or another type of standard that embeds FDT technology into it and it is able to do basic device configuration of multiple devices from multiple vendors. And that's one of the things that I think people like about using FDT is that it provides this kind of unified environment to configure interoperable devices in the field, although they may come from different manufacturers. So those are just a couple applications where we see it used quite a bit.
David Greenfield, Automation World
So we talked a little bit earlier about how FDT fits into open automation and the groups involved with that. And I noticed you also work with the OPC Foundation. Can you explain that relationship since you're both focused on industrial device communications and interoperability? Where's the overlap and the separation?
Steve Biegacki, FDT Group
So a couple things…one is I would say that our work today with the OPC Foundation is really around enabling that true seamless connection from the sensor or actuator at the plant level or at the device level up through the cloud. It's really that integration of the IT/OT infrastructure within an enterprise that we're actually collaborating with the OPC organization to enable. We're working on all the device connections and the ability to manage intelligent devices on the factory floor. We do have a connection with OPC and, in fact, part of the FDT standard calls for use of an FDT server and that FDT server has an OPC UA server built into it which enables that IT/OT integration. So we're working with them quite a bit right now and we collaborate with them in most of the trade shows. At these shows you'll find that the FDT group will be part of one of an OPC demonstration. In fact, at Hanover Messe this year we'll be showing how we work together as well as how we work with other technologies like Ethernet-APL and things like that to show that seamless integration from the plant floor up into the IT and the cloud infrastructure.
David Greenfield, Automation World
So one last question, Steve. Though FDT is principally a tool that's used by automation device developers to implant as part of their product, what should end users of industrial equipment know about FDT? How does it matter to them?
Steve Biegacki, FDT Group
I think the biggest thing from an end user standpoint is that the FDT standard was built out of end user use cases -- it was not just a technology in search of a cool way to do things. It was really built out of some specific sets of use cases working with users and user requirements. So I would just say that I think users that specify control systems that embed or use FDT technology or the FDT standard should realize how FDT makes their life easier as a user because it enables this unified environment of intelligent device management to share data up through the IT infrastructure to look at the data, what's happening with the actual devices and the sensors on the machines. So it provides a common environment for the design, configuration, operation and maintenance of their devices and their related control systems that it's hooked up to. The thing that makes it easier for a user is to be able to just request a device that adheres to the IEC 62453 standard or the FDT standard and they will see benefits from doing just that.
David Greenfield, Automation World
Well thank you again for joining me for this podcast, Steve, and thanks of course to all of our listeners. Please keep watching this space for more installments of Automation World Gets Your Questions Answered and remember you can find us online at automationworld.com to stay on top of the latest industrial automation technology insights, trends and news.
Latest In AW Podcasts
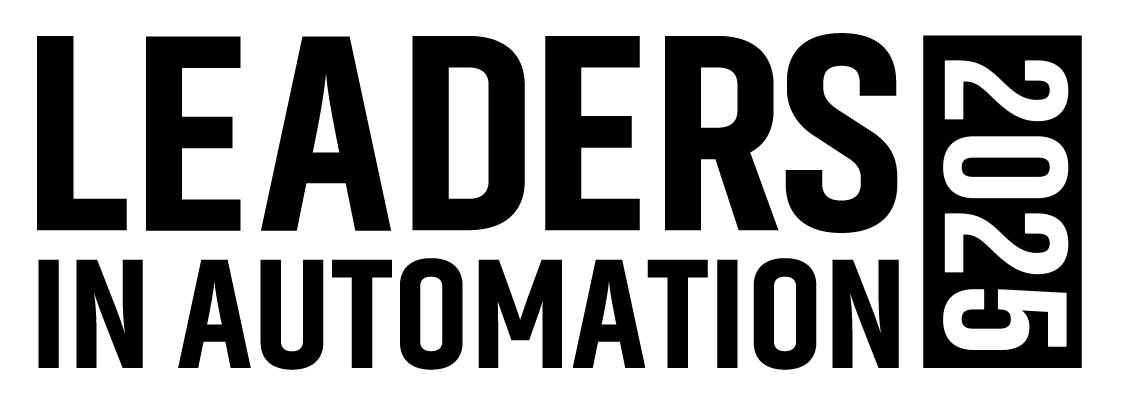
Leaders relevant to this content: