In the wings, a most unusual set of standards is being born. If all works out, not only will operators be more effective, but taking control room projects from design to deployment will be as simple and quick as possible. What make these nascent standards unusual is that, despite springing from initiatives originating from competing vendors, everyone building them seems to be in a mellow mood, and most agree on one relatively clear overall schema and basically similar visual approaches.
But, nothing, you might say, is that simple and smooth in manufacturing. You are of course right, but the fact remains that there is very deep agreement around what research has revealed about operator interfaces vis-à-vis fast, effective control action when action is required. Behind it all: safety, faster flows of data—and dwindling experience.
The chief driver behind the initiative for standards-based HMIs is safety. “There’s a groundswell of interest in control interfaces that are engineered for clarity and human factors,” says Grant Le Seuer, portfolio director of supervisory software products for Invensys Operations Management (http://iom.invensys.com), a maker of automation and visualization software based in Plano, Texas. “It’s no longer a vague wish among theoreticians but a strong customer demand to respond rapidly and appropriately to situations where safety is involved. They seek a more acute sense of situation awareness, and above all, they want to provide operators with the tools required to operate the plant.”
A second driver is what might be called point explosions. Peter Bullemer is senior partner at Human Centered Solutions (www.applyhcs.com) based in Lone Tree, Colo. and a key HMI architect. He says, “Today, there is a huge complexity in operations, with continuous expansion in the number of instrumentation, control and I/O points. The potential data flow is large, to say the least.” Ironically, as Le Seuer points out, “there are fewer operators each doing more work today than a decade ago.” More data bombarding fewer people amplifies the need for greater clarity in HMIs.
Finally, there is a growing need to train relatively inexperienced operators quickly so that they can respond to situations appropriately. Experienced personnel are retiring, taking with them decades-long assimilation of causes and effects—and their ability to spot out-of-control situations from the least of clues. If the HMI can act as a guide through episodes, walking operators through possible causes and recommended actions, it can in part offset the experience drain with smart computer algorithms.
Various initiatives
Guidance in high-performance HMIs is available from a number of sources. Focused on standards development, the ISA101 initiative of the International Society of Automation (ISA) (www.isa.org) is sorting out software-based HMI design criteria for industrial control and information systems. Aspects under consideration include information display, process visualization, user interaction, system performance, and documentation and training. The initiative was formed in 2005.
Standardization of HMIs is also a sizeable part of the work undertaken by Abnormal Situation Management Consortium (ASM). ASM’s informal beginning occurred in 1992, with formal organization two years later. Founders in 1992 included Honeywell Process Solutions, Amoco, Chevron, Exxon and Shell, with BP, Mobil (now ExxonMobil), NOVA Chemicals and Texaco coming on board at the formal organization stage. Others have joined since then, including Sasol, ConocoPhillips and Total, as well as several universities including the Mary Kay O’Connor Process Safety Center at Texas A&M University, Penn State, Nanyang Technological University (Singapore) and UCLA.
HMIs are but one aspect of ASM’s work, which concerns itself as well with daily operations metrics and root cause analysis of processes gone awry, definition of operator roles and responsibilities, maintenance and operations management, simulation, communications (both human and digital), procedure lifecycle management, and monitoring. Many of the ASM players are contributing to ISA101 development, and ASM published its landmark Effective Operator Display Guidelines in 2009, with Bullemer as one of its authors.
There are other organizations looking into HMIs: the Center for Operator Performance, various initiatives within the International Electrotechnical Commission (IEC) and, of course, individual companies—Emerson’s human-centered design initiative comes to mind here, as well as Rockwell Automation’s moves to integrate and align common capabilities across all control products. Virtually every company involved in products and software for operations management has something brewing
For a while, beginning in the 1980s and still to be found today, HMIs flirted with visual simulation. When computers took the place of relays and custom electronics, operator interfaces became miniature pantomimes of processes. On screen and increasingly in color, tanks filled, stirrers turned, valves opened and closed, motors ran.
Now, says ISA101 co-chair Maurice Wilkins of Yokogawa Automation (www.us.yokogawa.com), “Today’s ideal HMI minimizes distractions and maximizes relevance. Flames flickering from burners and tanks filling are distracting, taking your attention away from things that count. The data we gathered around a number of accidents reveal that in many cases, operators were simply overwhelmed by control panel distractions.”
“If automobiles had been invented in the 1980s,” says David Strobhar, founder and president of Beville Engineering Inc. (www.operatorperformance.org), Dayton, Ohio (and a founding member of the Center for Operator Performance), you’d have a picture of pistons going up and down on the instrument panel. Unfortunately, the drive for realism, for displays that are visually appealing, is a naïve one. Air control personnel in one Navy study did 70 percent better when displays used numbers inside triangles to identify aircraft types versus little pictures of aircraft, even though the users indicated a much stronger preference for the miniature aircraft. The reason? At a quick glance, an F-16 looks a lot like an F/A-18, where a number in a triangle is quite clear. Operators take longer to determine aircraft from pictures and longer to initiate an appropriate response.
Peter Bullemer adds that “designs should be tuned for perception and not cognition. For example, what happens when you choose to show a tank level going down? Yes, it mirrors what’s happening and it may be a key predictor of impending problems—but operators have to determine how much time is left before something has to be done about feed. You’re asking them to do mental calculations, the kind of thing that’s handled well by computers but poorly by people. If, on the other hand, your display shows numbers—level plus the time remaining based on draw—the operator knows exactly when to bring another pump on line or switch to an alternate feed.”
Color means trouble
In this new HMI world, color is reserved only for situations that require immediate attention. Normal operations display in gray, at least when following ASM’s guidelines. Bullemer says, “You can’t have red for an off-line pump in one part of a display, then use red for a critical alarm in another section. When you use the same color for different things, you turn a search for critical things into an exhaustive and potentially error-prone search.”
According to Bullemer, using a neutral or gray background with color for critical information helps tie into a primary human strength, the ability to learn patterns. “The ability to see patterns seems to be an innate characteristic, and learned patterns lead to expertise. Color makes a strong contrast against a neutral background, so you can use it to draw attention automatically to what’s critical.”
Significant challenges
While this all seems simple, creating the clearest possible HMI—one that is consistently effective in presenting both normal processes and critical, must-respond incidents—is far from easy.
“Some things [about high-performance HMIs] can be standardized,” says Wilkins, “but other elements can only be covered by general recommendations or guidelines. We can say that we’ll have x number of screens, require only so many clicks, and assign standard colors to standard elements, but at the end of the day, the design of each HMI has to be operator-driven.”
Strobhar agrees. “Content is critical,” he says, “and the content changes widely depending on the processes involved. You start with the person, not the system. As an HMI designer, you have to know what you want the person to do. What decisions have to be made? What information has to be on the screen to make those decisions?”
The basic methodology, he says, is to go through individual operators, “but you can’t simply ask, ‘what do you want to see?’ because they can’t fully articulate what’s needed. You have to sit with them, see everything they do and ask them about their jobs. When they describe what they do, they’re beginning to articulate their requirements, and it’s up to the designer to flesh it out. For example, if someone says, ‘I’m seeing how close I am to thus-and-such heat limit,’ a designer knows that the HMI should display both the current temperature and the limit.”
Existing control parameters may or may not be useful. “We ran across one console that included a graphic for Wobbe index,” Strobhar said. “We asked what it was, but the operators didn’t know. The head operator suggested trending it and, whatever it was, they were making a lot of them. It turned out to be a measure of BTUs in fuel gas streams, and it was there because someone, some time, decided to measure it. The Wobbe index was meaningless to the operators. But it’s a good example of the mentality, if I measure it, I’ll display it. The real question? It’s not what do you measure, but what do you want operators to do, or what do you want them to see?”
Strobhar has found shift change procedures to be especially useful for indicating what operators need to see. By noting what operators going off-shift page through and explain to those coming on, the designer has an excellent window on what questions to answer in the display.
“Once you understand what needs to be displayed,” says Bullemer, “there’s still work to be done. Operations are complex to the point where display hierarchies are mandatory. First-level displays might be restricted to the most critical health indicators across an entire operation. If something is going wrong, then you can drill down to level two, revealing major process units or main controllers. The ideal situation is to contain 80 percent of control moves from this display. If still more detail is needed, level three takes you to instrumentation and equipment levels—and may be used only in a troubleshooting mode.”
The design process acts as an opportunity to rationalize (and possibly change) control philosophies. Not surprisingly, it follows a pattern familiar to those who facilitate any sort of change: bring every stakeholder into the design process. “Everyone needs to agree on the vision and the direction of the control management,” Bullemer says. “The engineering staff might own the control project, but operations management and operators have to own it as well.”
Bruce Fuller, director of product management for visualization and information software for Milwaukee-based Rockwell Automation (www.rockwellautomation.com), sees a follow-on need: inclusion of enough information to effect diagnosis. “Customers have grown in sophistication not in HMIs but in data and what to do with the data,” he says. “At the same time, we’re seeing growing demand for flexible software interfaces, enabling HMIs that align with an end-user’s corporate standard, or with an external standard like the upcoming ISA101. But whatever’s on the screen, the real need is to key the switch from visualization to information.”
“Certainly the amount of data has grown,” Fuller says, “but what to do with the data hasn’t changed a lot. The best interfaces will make clear what’s important—even who should receive the information. Operator intervention becomes more effective when you include, decision support, in the control interface. Operators can be far more effective when the HMI not only presents a need clearly, but also includes what the operator should do to bring things back to the norm.”
Beville Engineering Inc. (www.operatorperformance.org)
Human Centered Solutions (www.applyhcs.com)
Invensys Operations Management (http://iom.invensys.com)
Rockwell Automation (www.rockwellautomation.com)
Yokogawa Automation (www.us.yokogawa.com)
Companies in this Article
Sponsored Recommendations
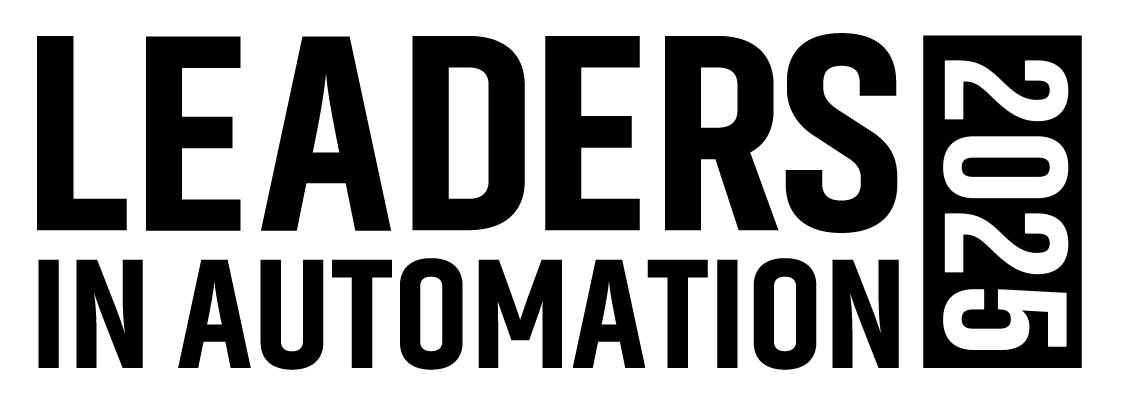
Leaders relevant to this article: