Process and Packaging Integration: The Challenge and the Promise
Not long ago, greater integration between the processing and packaging functions was seen partly as an emerging trend and partly as an interesting possibility—an intriguing “if” out there on the horizon. Increasingly, however, the focus is no longer if, but when and how.
In terms of when, there is a clear answer to at least part of that. The pharmaceutical industry is the most immediately affected. California’s “e-pedigree” law (SB 1307), which mandates that 50 percent of the drugs sold in the state will be subject to unit, case and pallet serialization, will kick in on Jan. 1, 2015, with the rest subject to these requirements a year later. Wholesalers are required to be in compliance by July 1, 2016, and pharmacies in the state by July 1, 2017. As California is one of the world’s largest markets, manufacturers can ill-afford to ignore the demands of the state.
There is activity at the federal level as well. Responding to a slew of highly publicized contamination incidents, Uncle Sam has also made his voice heard, primarily through two laws from 2007. These are the Food and Drug Administration (FDA) Amendments Act and the Federal Food, Drug, and Cosmetic Act. Together they phase in stiffer documentation and tracking requirements for drugs, food and other commodities. The zeal for consumer safety regulations could wax and wane depending on the political climate in Washington, but given the fact that these products affect all Americans on an intimate and daily basis, it is difficult to imagine their being rolled back significantly. In addition, Europe and other large markets such as Brazil are also stiffening documentation and traceability requirements.
Rodger Brisso, global program manager for the process OEM business at supplier Rockwell Automation Inc., Milwaukee, summarizes the cumulative result of these and other regulatory initiatives this way: “The reality now for many types of products is that when you sell something, you’ve got to be able to document everything that went into it all the way to the consumer, and I think you’re going to see these requirements get tighter and tighter, especially on anything that people consume.”
David Kirklen, business development manager for packaging at automation supplier Siemens Industry Inc., of Alpharetta, Ga., concurs. “The ability to track and trace, along with optimize, is where things are headed globally as food safety requirements increase and the need to know where things end up after production is completed. In the near future, it will be paramount that the two sections work together.”
Communication between the two functions is not new, but as Kirken notes, in the past “the interaction of the two areas primarily consisted of sending discrete signals to alert downstream packaging equipment of possible interruptions in the process that may require an increase, decrease or stop actions.” That, he says, is changing to a more complex and dynamic scenario that will enhance “a producer’s ability to not only control the entire process, but also to have real-time feedback to implement changes to increase uptime, eliminate waste or even conserve energy.”
Control complexity
Achieving this goal, says Andy Hansbrough, vertical market manager, packaging, for vendor Kollmorgen, of Radford, Va., a provider of motion systems and related products, requires “tight control synchronization within each machine, from machine-to-machine and from each machine to the plant control. Flexible production requirements on volume, machine-to-machine processing speeds, product changeovers, tighter temperature controls, machine-to-machine configurations and merging lines are all raising control complexity.”
Handling that complexity, he believes, demands more capability than is provided by traditional programmable logic controllers (PLCs). He favors “soft PLCs,” or software systems incorporating the IEC 61131-3 standard promulgated by the International Electrotechnical Commission allowing programming in five major languages and resident on industrial personal computers (IPCs) or programmable automation controllers (PACs). Among other advantages, “these address this increasing complexity by greatly simplifying and shortening the design process so that lines may be built and/or changed over quickly and easily. Built-in simulators in the software offer the ability to simulate the interaction amongst each machine and motion element, which greatly increases the ability to iterate designs.”
Like Hansbrough, Joe Martin believes that PC-based control has a key role to play in this coming era of greater integration. Martin, who is packaging and converting manager for Beckhoff Automation LLC, a Burnsville, Minn., automation supplier, observes that “PC-based control is facilitating the convergence of processing and packaging by collapsing previously segmented controls architectures into more centralized solutions. With a modern industrial PC with automation software, it is possible to cover more machine components and even control multiple machines, from processing to packaging, with a single piece of control hardware.”
With a traditional hardware PLC approach, he notes, it is often necessary to utilize multiple PLCs, then “add on expensive cards for functions like motion, and rely on intelligent drives that also need to be programmed. This can result in overweight and cumbersome systems afflicted with complex handshaking routines between multiple master controllers. They require more specialist programmers for the various hardware controls devices and are harder to debug and troubleshoot.”
He goes on to assert that “it is absolutely more sustainable to remove the intelligence from as many devices as possible—especially from drives—and focus the logic, motion, human-machine interface (HMI) and the like into one powerful controls centerpiece. PC-based programming can lower the burden on engineering departments through the ability to add functionality more quickly and cost-effectively in software.”
Martin foresees processing and packaging “pushed together into one streamlined and integrated system running on an IPC.” This would simplify communication and coordination by having only one master controller managing the functionality of slave devices throughout the line. “This boosts uptime by removing points of failure, promotes faster changeovers and increases performance, leading to higher throughput, among other benefits.”
Convergence
Rockwell’s Brisso terms this streamlined and integrated approach “convergence,” and sees it happening across the process/packaging world, though generally in incremental steps. Not surprisingly, he favors his company’s approach to the issue, one that utilizes Rockwell’s multidisciplinary controllers and Logix platform to provide a common control, programming and communication environment. “Coupling this with a network infrastructure built around EtherNet/IP allows you to seamlessly communicate and roll-up information from packaging machines and process skids into the process side of the space to a single operator interface, or to a server collecting all the data that can be used for plant-wide optimization. It also facilitates plant-level access to timely diagnostic information.
“The previously acceptable solution of having two separate control systems,” Brisso maintains, “one for process and one for packaging, is an antiquated way of doing things when one group of people and one set of products can do both.” Antiquated and, he adds, unnecessarily costly when one considers that an integrated approach has the potential to reduce hardware, software, programming, training and spares costs, as well as the bottom-line benefits that accrue from getting new equipment, new applications or entire new lines up and running more quickly.
Brisso doesn’t need to evangelize about the benefits of greater process/packaging integration to Fargo Automation Inc., Fargo, N.D., a company that designs and builds packaging lines and packaging machinery for the pharmaceutical and medical device industry—it’s already a part of Fargo Automation’s tool kit. The company has standardized on Rockwell controllers and the Logix platform to help do it.
“With these companies (Fargo customers), the need for validation of product integrity is already great and it’s increasing,” says Dustin Hanson, spokesman for Fargo. “Integration makes that easier.” He cites one of Fargo’s applications as an example.
“Some bioscience companies keep their lot sizes very small. They want to keep these lots segregated to help them assure lot integrity. They will only send one lot through to packaging and upload that lot information directly to the MES (manufacturing execution system). Our packaging system connects to that data in the MES ‘live,’ in real time, and pulls it down to the machine level.”
That data, says Hanson, could include the information that only seven of the eight products coming through in this small lot are acceptable. “Our system would then package only those seven good products. Similarly, that updated live information would also be loaded into the print queue. That’s an example of the type of capability we’ve gained from increased standardization and integration.” Savings, he notes, are quickly seen in terms of less wasted time and packaging material, and, most importantly, greater assuredness regarding product verification.
Hanson is quick to point out that the advantages of this approach are not limited to small-lot production. “High-speed information sharing is also very critical in high-speed applications such as the production and packaging of hypodermic needles, which can run at rates of up to 600 a minute.”
In this application, the newly produced needles are fed into a horizontal form, fill and seal machine, emerging as blister packs that are handed off by a servo-driven pick arm to servo-driven flip arms that invert the packages. Next, the packages are stacked into corrugated cases using robotics to pick and place the packages in groups. The packages are verified and cleared to go from the pick point to the place point using sensors mounted inside the robot’s end-of-arm-tooling. The corrugated boxes exit the system and are sent to a case-closing machine. Then comes a print-and-apply labeler that also monitors for low labels, no labels, low ribbon and other nonstandard conditions. Finally comes an accumulation buffer that was created by use of a conveyor and back pressure.
“We were dealing with machines from different vendors and a lot of high-speed communication was required,” says Hanson. As part of its solution, Fargo installed one of its PLCs on the backplane of a different vendor’s process controller, giving it immediate access to process information. “As a result, communication from their system to our downstream machines was hyperfast.”
Facilitating the transfer of data from its point of origination to other components of the production system is also a concern of automation components supplier Sick Inc., Minneapolis. “What we try to do is to get more information on what’s actually going on at the point of detection, or the point of reading, to provide more process and/or status information to downstream machines to the quality guys, or to a higher level system,” says Mark Langridge, Sick’s manager for food, beverage and commercial accounts. Like Fargo’s Hanson, Langridge believes that there are great advantages to be gained from sharing that information, in an immediately useable form, across process and packaging boundaries. Thus, information on variations in the process would be available to the packaging machine operator as well as to higher-level systems.
One of the ways that Sick is trying to do this is through an initiative it calls IO Link, a fieldbus-neutral sensor/actuator communication interface supported by a consortium of German manufacturers that allows a controller to communicate directly with the sensor. It permits the transfer of considerably more information than just digital switching states and digitalized analog values. For the pharmaceutical industry, this could facilitate rapid batch changes and machine validation, and could help packaging lines change some key parameters on the fly.
Case made?
So has the case for greater integration between process and packaging been made? According to many automation professionals, the answer is yes. “I don’t think you’ll find anyone disagreeing that better integration makes sense,” says John Kowal, market development manager for vendor B&R Industrial Automation Corp., Roswell, Ga. He predicts, “As we emerge from the economic downturn, we’ll see more emphasis on investment in technologies to fundamentally improve manufacturing processes, including the integration of processing with packaging.”
Of course, this won’t happen overnight. “We’ll see the integration first where it’s most critical,“ he continues. “If I have a continuous fryer or a beverage line, I want the downstream packaging processes as synchronized as possible because I can’t stop the upstream process. “
Fundamentally, Kowal concludes, these issues go beyond processing or packaging and affect manufacturing itself, where he sees “the convergence of manufacturing management functions—quality control, sustainability, safety, security, OEE (overall equipment effectiveness), MES, diagnostics and PM (preventive maintenance)—that are inherently interrelated. These should be viewed holistically, both figuratively and literally on the same dashboard.”
March 2011, Related Feature Blood Testing Packaging System Handles Multiple Challenges
To read the feature article, visit www.automationworld.com/feature-8452
Subscribe to Automation World's RSS Feeds for Feature Articles
Companies in this Article
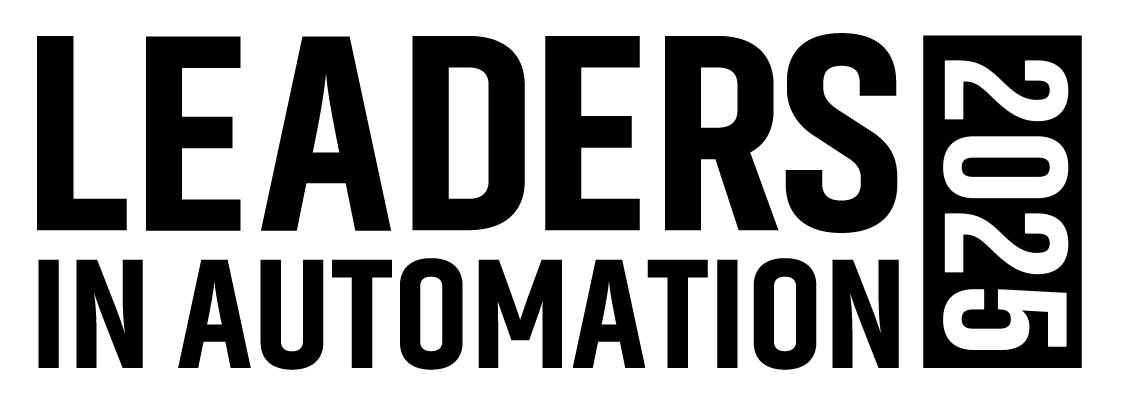
Leaders relevant to this article: