What’s New in Integrated Logic and Motion Control? Vendors Respond
Responses from Daniel Ghizoni, Product Engineer, B&R Industrial Automation Corp.
Automation World: We have been hearing about integrated logic and motion control for a decade or more. What is new on that front and what do you see as the major trends?
Daniel Ghizoni: B&R’s philosophy has always been of providing a truly integrated IDE (Integrated Design Environment) and, as a company, providing complete system solutions for its customers. With Automation Studio, our customers have an integrated logic, visualization and motion development platform.
The recent addition of the motion control package SDC (Smart Device Controller) offers integration of motion control algorithms across different hardware platforms. The same software packages and programs can thus be reused for different machine types, ranging from a low-cost, stepper motor-based solution, to a high-performance, servo-based design.
One trend we are seeing in the marketplace is the integration of high-precision motion controllers into the PLC. The PLC is now able to perform calculation-intensive control, such as computer numeric (CNC) and robotic controls. B&R offers a CNC kernel with its platform (and has for quite some time), and has integrated it with its motion control package so that a CNC software application for servos can be easily migrated to use stepper motors. While CNC itself is not a new trend, the precision requirements of new applications are significantly higher.
AW: What are the primary product lines or solutions that your company offers in this space?
Ghizoni: Automation Studio, our IDE, has always offered integrated logic, motion control and visualization design within a single tool. Our controllers, ranging from low-cost PLCs, to high-end Intel-based industrial PC’s, are all capable of performing both logic and motion control within a single solution. Communication to the motor drives is established via the real-time Ethernet POWERLINK fieldbus.
AW: How broadly is integrated logic/motion control being adopted by machine builders, integrators and/or end users? Are there any particular industries in which this technology is being more widely used?
Ghizoni: Since integrated logic and motion control is an integral part of our philosophy and technology, it is used by all of our customers who have motion applications. There is a growing number of machine builders which have migrated from using dedicated motion controllers to performing the CNC application in their B&R PLCs.
AW: What are the major drivers and/or enablers for broader use of integrated logic/motion control technology?
Ghizoni: One of the drivers for the integration of numerically intensive control techniques into the PLC has been the vast expansion of the PLC’s computational power. B&R’s Industrial PCs are available with Intel Core2 Duo and Atom-based processors, with clock speeds of up to 2.6GHz. That kind of processing power enables quite a bit of control tasks, at vastly faster cycle times, which the PLC of the past was simply not fast enough to handle. The advantage to the customer is simplicity—there is only one piece of hardware that handles all of the machine tasks, one piece of software to develop, and one unit to interface to the plant supervisory control software.
AW: What are the major benefits to customers of using this technology? Please provide quantification of the benefits, and some specific customer examples, if possible.
Ghizoni: The benefits of integrating the motion control algorithms into the visualization and logic controller fall largely on the ease-of-use that comes from centralization. There is a single development platform, the visualization has direct access to motion-related variables and diagnostics, and the end-user benefits from having a single gateway to the machine for plant management applications.
Responses from Corey McAtee, Technical Marketing Manager, Beckhoff Automation LLC
Automation World: We have been hearing about integrated logic and motion control for a decade or more. What is new on that front and what do you see as the major trends?
Corey McAtee: Beckhoff Automation introduced the company’s first integrated logic and motion control solution in 1988 with the DOS-based S1000 software platform. For some automation and controls vendors, Beckhoff included, this is not a new technology in any way.
With the advent of multi-core Industrial PCs (IPCs) Beckhoff had to find a practical use for the extra horsepower these processors provide and the next logical step was the inclusion of robotics control into the mix. Beckhoff recently released a kinematics software library for TwinCAT NC I, which facilitates integration of robotics in addition to basic PLC logic and motion control functionality. TwinCAT was already ideally suited for logic and motion control systems so adding a basic kinematic library for robotic control such as SCARA, 3D Delta and more was the natural progression.
When looking for the benefits of this integration, you need to take a step back and look at the overall machine. For example, let’s examine the savings on a packaging line with a Delta robot picking from a conveyor and placing into a container. With a traditional control system the machine builder would source the robotic controls separately and use fieldbus system to asynchronously communicate to the PLC and motion controller. Synchronizing communications between the motion controller, robotic controller and the PLC reduces overall system code and eliminates a considerable amount of [now] unnecessary hardware. For example, all camming and gearing can be done electronically so there’s no need for secondary encoders to be run.
AW: What are the primary product lines or solutions that your company offers in this space?
McAtee: TwinCAT NC I software platform with the TwinCAT Kinematic Transformation library
AW: How broadly is integrated logic/motion control being adopted by machine builders, integrators and/or end users? Are there any particular industries in which this technology is being more widely used?
McAtee: Beckhoff isn’t strictly devoted to specific industries, so in our book, all industries that require logic and motion control have adopted the integration to varying degrees. Users are starting to implement and understand the ease at which an integrated motion controller and PLC can simplify project development time. This time reduction is typically seen though the configuration stage in the TwinCAT system software where abstracting the hardware configuration from software configuration, allows the user to apply one program to multiple drive types—from stepper to servo to VFD—without any motion code changes.
AW: What are the major drivers and/or enablers for broader use of integrated logic/motion control technology?
McAtee: Standard, off-the-shelf technology advancements have led to “Scientific Automation,” a leading edge approach from Beckhoff. This approach allows one to remove those black boxes that people would normally use on a machine for functions like high precision temperature measurement, condition monitoring, and robotics. Scientific Automation is executed by taking advantage of all the extra CPU cycles that are now available on newer multi-core Industrial PCs (IPCs) and combining that with the high speed fieldbus EtherCAT.
AW: What are the major benefits to customers of using this technology? Please provide quantification of the benefits, and some specific customer examples, if possible.
McAtee: The numerous benefits include the previously mentioned elimination of expensive black boxes, reduction in system complexity, smaller machine footprint, fewer points of failure, more reliable systems and reduced time to market. Additional efficiencies are gained by using one control platform, one common software package without yearly licensing upgrades (TwinCAT) and one network (EtherCAT).
By using high speed I/O with an integrated high-performance drive that has no on-board intelligence, we’re offloading the control back to the IPC. In this way, users can reduce system complexity and cost. Users no longer need a special drive or special I/O to talk to that drive, they can use off-the-shelf components which allows them to build the system exactly the way they want. It also provides the ability to easily debug the system through the use of one standard control package versus specialized software for the drives, the PLC and everything else.
It may seem obvious, but it’s an important reminder that overall system savings comes in different ways—these are most significant in system implementation and ongoing system support which are often the forgotten costs. A more integrated, software-rich control system that can provide more functionality with less logic/motion control hardware will help facilitate more profitable operations up front, but more importantly, in the long run as well.
Responses from Joaquin Ocampo, Drives & Controls Product Manager, Bosch Rexroth Corp.
Automation World: We have been hearing about integrated logic and motion control for a decade or more. What is new on that front and what do you see as major trends?
Joaquin Ocampo: One of the major trends is utilizing one bus, Ethernet based fieldbus communication solutions are now the trend. Bosch Rexroth uses SERCOS III, for motion, I/O, and other peripherals instead of the traditional architecture of having one bus for the motion control and another one for the I/O and other peripheral devices.
AW: What are the primary product lines or solutions that your company offers in this space?
Ocampo: Bosch Rexroth offers the IndraMotion MLD - Motion Logic in the Drive.
IndraMotion MLD-S for single axis solutions.
IndraMotion MLD-M for multiple axes solutions.
The IndraDrive wide range of sizes from 50W to 630KW.
The IndraDrive Compact, IndraDrive Modular and IndraDrive Compact Series (Cs) with integrated PLC.
The IndraDrive with integrated motion control can control up to 10 axes. Complex motions likes: electronic cams, motion profiles, and electronic synchronization can be done with the PLC in the IndraDrive. Our IndraDrive, as a master, uses SERCOS III Ethernet to communicate to the slaves and accomplish the necessary motion. In turn, this master, can be a slave to a higher order control by virtually any fieldbus communication, for example: SERCOS III, EtherNet/IP™, EtherCAT®, or ProfiNet®. This gives flexibility to the machine builder. Which makes it easier to add a module, with complex motion, to his machine without having to do the programming on the higher order PLC. The program is done, using standard IEC61131 languages, in the IndraDrive and the drives takes care of the motion of up to 10 axes.
Bosch Rexroth also offers IndraMotion MLC—Motion Logic Control for general automation and for application for up to 64 axes.
We offer IndraMotion MTX—For Machine Tool applications, or where true interpolation is needed for the application like, stone cutting or water-jet cutting.
AW: How broadly is integrated logic/motion control being adopted by machine builders, integrators and/or end-users? Are there any particular industries in which this technology is being more widely used?
Ocampo: It seems that all industries are using this technology. Currently, I have seen this used in general automation or work cells applications. Some of the applications have been in the plastics industry, packaging industry, automotive, aerospace, metal forming, appliances, and metal piping.
AW: What are the major drivers and/or enablers for broader use of integrated logic/motion control technology?
Ocampo: Reduced panel size, less wiring, common software and programming tools, and not having to know a specialized programming language.
Standard IEC 61131 programming languages and PLCOpen compliant function blocks for specific applications; make it easier to use Bosch Rexroth IndraMotion MLD.
AW: What are the major benefits to customers of using this technology? Please provide quantification of the benefits, and some specific customer examples, if possible.
Ocampo: One supplier for their motion needs.
Savings in cabinet space, design, and wiring. Cabinet size can be reduced by up to 20%.
Single software solution for setting drive parameters, commissioning, programming, and diagnostics.
Responses from Chris Radley, Senior Product Line Manager, Kollmorgen
Automation World: We have been hearing about integrated logic and motion control for a decade or more. What is new on that front and what do you see as the major trends?
Chris Radley: A key element that has changed is the advent of high speed deterministic networks for supporting both the soft PLC (integrated logic via IEC61131-3) and motion.
With Ethernet solutions like EtherCAT®, it is no longer necessary to have separate networks for the PLC machine control and the motion control. More importantly, new generation solutions like Kollmorgen Automation Suite truly integrate the PLC and motion engines to provide one programming environment, with tight coupling between the motion and process control for higher performance.
AW: What are the primary technologies/solutions that your company offers in this space?
Radley: Kollmorgen’s newest offering is Kollmorgen Automation Suite™, which combines software, hardware and services for complete machine automation solutions.
The software includes a full IEC61131-3 soft PLC, with both the industry standard PLCopen motion engine and Kollmorgen’s unique Pipe Network™ motion solution that provides a simple and elegant graphical motion programming capability that is particularly well suited to complex gearing and camming applications. The software suite is a single environment for all programming—whether process, motion, HMI, etc. Built-in ease-of-use features, such as auto recognition of the connected network devices, make it fast and easy to build the system solution.
Kollmorgen’s hardware products include controllers, drives, motors, I/O, HMI’s, gearheads and linear positioners, which are preconfigured and tested to work together for optimum performance and ease of integration. Kollmorgen also offers support services for application development, startup and training.
AW: How broadly is integrated logic/motion control being adopted by machine builders, integrators and/or end users? Are there any particular industries in which this technology is being more widely used?
Radley: Integrated logic/motion control is generally a consideration for most new machine applications. While some customers will continue to use separate logic and motion control, these customers are at least evaluating the benefits of switching to an integrated solution.
The packaging, converting and flexographic printing industries are widely using integrated solutions. At this time we see a slower adoption curve in the semiconductor and electronics assembly markets.
AW: What are the major drivers and/or enablers for broader use of integrated logic/motion control technology?
Radley: There are several factors driving integrated solutions:
* (1) Faster time to market resulting from the single programming environment that handles all of the machine and motion control. The developer learns just one tool, which can perform all of the tasks needed for the machine application.
* (2) Lower cost by having a single environment, single network and common hardware (one controller for both machine and motion control instead of a separate PLC and motion controller).
* (3) The use of common standards such as IEC61131-3 for the soft PLC and PLCopen for the motion control. For OEM’s who may need to work with more than one supplier, they can still benefit from not having to relearn completely different tools.
* (4) Single supplier to work with for all of the software, hardware and services.
* (5) Integrated systems can achieve higher performance via the tight coupling of the process and motion engines.
AW: What are the major benefits to customers of using this technology? Please provide quantification of the benefits, and some specific customer examples, if possible.
Radley: The two primary benefits are faster time to market and higher performance.
As noted above, faster time to market comes from using a single programming environment to do all aspects of the machine application. It is no longer necessary to develop the process programming in one tool, motion programming in another, HMI in still a third, and possibly other tools for handling things like I/O integration and drive setup. With the separate tools, even after the machine builder has learned them and become proficient, they still needed to integrate the separate results together and manage the issues of debugging and supporting the system across all its independent elements. When a single integrated development environment is combined with pre-configured components that are auto recognized by the software and automatically setup, development and deployment time is dramatically reduced. It is not unusual to see 30% to 50% reductions in the time from concept to machine deployment.
High performance comes from being able to run the entire program as an integrated entity rather than having to pass commands between separate controllers for the process logic and motion control.
Responses from Bob Hirschinger, Principal Engineer, Rockwell Automation Inc.
Automation World: We have been hearing about integrated logic and motion control for a decade or more. What is new on that front and what do you see as the major trends?
Bob Hirschinger: Advances in motion control functionality are continuous. A recent innovation includes the embedded kinematics for control of non-linear mechanical systems. Our PAC support for robotics eliminates the need for dedicated-purpose robot controllers. In addition, drive-based and network-based drive safety—SIL2, PLd & SIL3, PLe safe-off, safe-direction and safe-speed—have been incorporated for improved productivity.
Another significant trend is integrated motion over an Ethernet/IP network. This solution provides a single network for complete machine control, simplifying and enhancing machine design. Customers can now configure, commission, program and maintain the Allen-Bradley® Kinetix® 6500 servo drive and PowerFlex® 755 AC drives on EtherNet/IP using motion profiles and instruction sets within a single software environment—RSLogix™ 5000. A key attribute of this solution is that it uses CIP Motion and CIP Sync technology from ODVA, all built on the Common Industrial Protocol (CIP). EtherNet/IP uses standard, unmodified Ethernet, and it allows you to effectively manage real-time control and information flow for improved plant-wide optimization, more informed decision-making and better business performance. It also includes time synchronized control for Ethernet networked devices for high performance, including position drive outputs and multiple sequence event detection.
The Rockwell Automation Motion Analyzer software helps machine builders obtain the full benefits of a mechatronic design approach by making it faster and easier to analyze, optimize, simulate and select motion control systems. The software enables machine builders to model mechatronic systems in a virtual environment and predict energy consumption and cost for their system.
AW: What are the primary product lines or solutions that your company offers in this space?
Hirschinger: Currently, we offer PACs with integrated motion functionality for a broad range of AC and servo drives, a variety of motor and actuator products, and mechatronics design tools, including specifically:
* Logix PAC controls and RSLogix 5000 software
* Servo (Kinetix) and AC drives (PowerFlex) 1-700hp
* Kinetix rotary motors, direct drive motors, linear stages and motors
* Motion Analyzer mechatronic design, simulation, optimization software tools
AW: How broadly is integrated logic/motion control being adopted by machine builders, integrators and/or end users? Are there any particular industries in which this technology is being more widely used?
Hirschinger: Integrated motion control is being adopted globally across a wide range of industries by machine builders, integrators and end users. It’s shown particular strength in a number of industries including food and beverage, consumer goods packaging, material handling, assembly, converting/print/Web, as well as tire and rubber.
AW: What are the major drivers and/or enablers for broader use of integrated logic/motion control technology?Hirschinger: Integrated motion control is driven by many key areas; however, the major enablers are:
* Enhanced ease-of-use design, implementation, optimization and maintenance
* Improved line performance—increased line speeds and machine uptime via improved OEE
* Flexibility—multiple product lines and product switch over time
* Compliance with industry standards, e.g. IEC 61131-3
* Regulatory compliance requirements, e.g. 21 CFR 11
* Real-time access to large amounts of data for process and equipment monitoring
AW: What are the major benefits to customers of using this technology? Please provide quantification of the benefits and some specific customer examples, if possible.
Hirschinger: One key benefit is that it provides a common solution (hardware, software, tools, methodologies) for discrete, drive, motion and process control, which helps reduce training and inventory, provides easier line integration and allows the use of common standards.
In addition, by reducing redundant components and controls, the equipment acquisition costs are lower. People have broader access to process and equipment status and diagnostics information, which allows for real-time process monitoring, for improved product quality and machine OEE.
Responses from Zuri H. Evans, Motion Controllers Product Manager, Siemens Industry Inc., Drive Technologies
Automation World: We have been hearing about integrated logic and motion control for a decade or more. What is new on that front and what do you see as the major trends?
Zuri H. Evans: In the past, multiple dedicated hardware components and a PLC were required to properly monitor and control a machine. Today, one Simotion motion controller can handle all the functionality required by a machine in a single controller including: PLC logic, drive control, synchronous motion control, 3D interpolation, robotic control, hydraulic control, temperature control, PID control, integrated motion safety, and a full function integrated web server. Not only does this greatly reduce panel space and wiring, but it also simplifies (and sometimes eliminates) field-bus configuration,
With the integrated web server and the continued shift toward Ethernet based field-bus technology like Profinet, end-users can now fully support their machines without special software. All they need are a web browser and Ethernet connectivity. This allows them to monitor and write to variables, run traces with the web-based oscilloscope, view all alarm history and diagnostics, update FW, and even update the entire machine project on any PC with a web browser. Password protected pages with SSL encryption keep the machine secure yet accessible.
This expanded capability is not only the result of hardware improvements, such as faster processors and expanding the working memory up to 70MB. Just as important is the innovative architecture of Simotion. Using compiled code rather than interpreted code allows much faster execution of user code, down to cyclic calls every 250µs (4,000 times per second). Programming in an object-oriented environment allows Simotion to convert from running a third-party drive to running a Siemens Sinamics drive with no changes to the user-code. Users simply reconfigure the axis object to communicate with the Sinamics drive for fast, easy retrofitting.
Additionally, in this object-oriented environment, a user no longer needs to deal directly with hardware addresses. Everything is referenced by variable names and Simotion handles the hardware address allocations automatically (I/O is optional). This concept greatly simplifies the re-use of user-code—all user-code—because nothing is hard-coded.
This modern architecture also gives users more flexibility in executing code. Users can use cyclic-events for PLC logic, sequential-events for motion logic, timer-events for communication and data management, interrupt-events for quick response to high-speed inputs and deterministic-events (down to 250µs) for adaptive position corrections. The benefit is that quick machine response no longer only depends on fast cycle times.
AW: What are the primary product lines or solutions that your company offers in this space?
Evans: The Simotion Family includes three HW (hardware) platforms:
* Controller based—includes four onboard analog ports ideal for retrofit applications and hydraulic control
* PC based—includes a high performance controller that runs WinXP with an isolated Simotion kernel running in parallel. This is ideal for high axis counts (up to 64 axis) and solutions that require windows applications to interface with the machine. A Windows embedded version is available as well on an industrial PC with no moving parts for high reliability.
* Drive based—includes an integrated Sinamics drive for the most compact solution. With 5 performance levels, the drive based Simotion controller is optimized for anything from single axis control up to 128 axis per controller with the release of the D455-2.
The Simatic Family includes the T-CPU which integrates the Simotion kernel into a Simatic PLC. This includes the TF-CPU that also integrates a fail-safe PLC to combine logic, motion and safety in a single HW platform.
AW: How broadly is integrated logic/motion control being adopted by machine builders, integrators and/or end users? Are there any particular industries in which this technology is being more widely used?
Evans: All applications with motion are adopting this integrated technology to simplify engineering and support, reduce panel space and improve performance by reducing (even eliminating) interfaces between dedicated components.
Specific industries include: printing, packaging, converting, renewable energy, aerospace, entertainment, metal forming, plastics, woodworking, glass and general motion control.
AW: What are the major drivers and/or enablers for broader use of integrated logic/motion control technology?
Evans: The Mechatronics trend is one of the major drivers of this technology. In the past, machines used mechanical components for motion control of line shafts, clutches, cams, and gears connected to a main drive. It had been expensive to maintain these mechanical components. Small changes required major mechanical redesigns.
By replacing these mechanical components with servo motors, the machines became much more reliable and flexible. This change, however, shifted machine design from mechanical to electrical. The shift required motion controllers that enabled easy programming and coordination of these servo motors as well as the standard logic usually handled by a PLC. Now, the entire machine control can be handled by a single controller such as Simotion.
AW: What are the major benefits to customers of using this technology? Please provide quantification of the benefits, and some specific customer examples, if possible.
Evans: * Single point connection for programming/troubleshooting/drive system tuning.
* Fast access to drive system & process data to user program.
* Reduced development time utilizing open standard application.
* Increased accuracy of the tension control from Motion based winder and web control.
Related Feature - Control Venders Put More in the Box
To read the feature article relating to this story, go to http://www.automationworld.com/feature-8231.
Subscribe to Automation World's RSS Feeds for Feature Articles
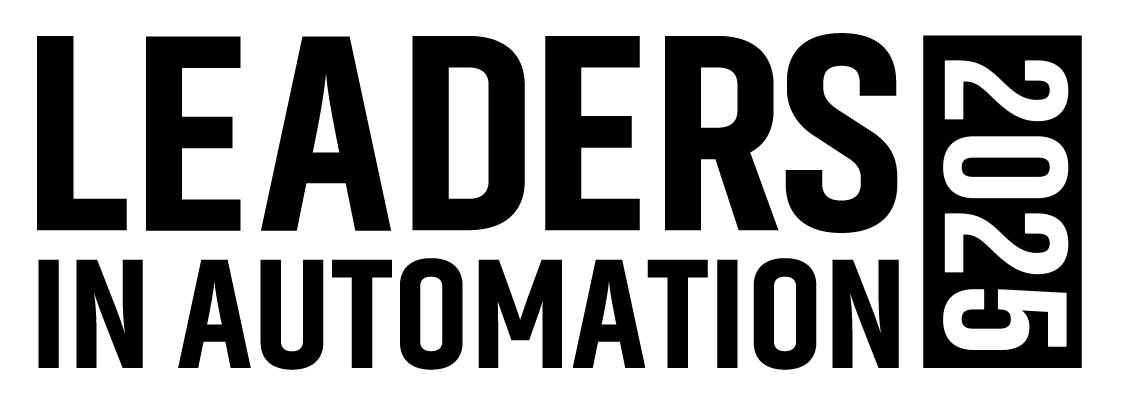
Leaders relevant to this article: