Printing forms, brochures, calendars and mailers with cut inserts is a high-speed job with tight precision requirements. When Jakob Graphic Services GmbH upgraded its operations, motion control and short set-up times were key criteria for its network selection.
These complex printing jobs have many steps, such as slitting, gluing, punching and folding. All of them are closely intertwined. Jakob, based in Pfungstadt, Germany, handles many jobs, so set-up has to be quick, and production can’t stop.
Cutting is also an important job. The separating cuts must be synchronized with the paper web speed to maximize productivity. The networks that link the presses and cutting tools must deliver messages at exactly the right time, or cuts will be at the wrong place, ruining the printed materials. The equipment works with paper rolls that have maximum roll diameter up to 50 inches, and roll widths ranging from four to 27 inches.
Jakob employed hardware and software from Kollmorgen to handle these high-precision jobs. The Radford, Va., equipment manufacturer uses EtherCat networking to meet real-time requirements. That choice is important to Kollmorgen, but most of its customers don’t really care which networking architecture is handling their critical deterministic commands.
“A lot of users don’t really think about determinism. They just know about their application, that they want to trim paper or cut 350 bags a minute with a specific accuracy,” says Carroll Wontrop, senior system engineer at Kollmorgen. Customers do want to know that Ethernet is being used for communications, but only the most focused engineers care which variant is being used for data packets that have extremely time-sensitive instructions.
That’s true with many of the industrial suppliers. There are many applications that require deterministic networks, and their numbers are growing as production equipment runs faster and customers expect extremely precise cuts, folds and seals. In the most demanding of these applications, packet delivery times must be measured in nanoseconds.Timing is everything
The engineers who focus on network design spend a lot of time defining the level of determinism needed so that users can meet their design requirements without worrying about how bits are delivered. When these specialists look at networking architecture, they fret over miniscule fractions of seconds.
“EtherCat is able to achieve real-world jitter numbers of +/- 20 nanoseconds of the actual signal on the wire of the output devices,” says Joey Stubbs, North American Representative for the EtherCat Technology Group’s Austin, Texas, office.
Network developers are taking advantage of a standard promulgated by the Institute of Electrical and Electronics Engineers (IEEE) that’s seen solid acceptance in demanding technical environments. The wordy title of IEEE 1588 explains its basic concept: “Standard for a Precision Clock Synchronization Protocol for Networked Measurement and Control Systems.” It ensures that all actuations take place at a precise time.
“With EtherNet/IP and IEEE 1588 time synchronization, you can synchronize nodes to within 100 nanoseconds,” says Steve Zuponcic, application engineering manager for supplier Rockwell Automation Inc., in Mayfield Heights, Ohio. “When each node knows precisely what time it is, you can tell every drive and every motor to be at a certain point at a certain time. They’ll all be synchronized, giving you very tight control.”
Network developers need to embed these technologies into their equipment and software so that users don’t have to worry about programming steps that happen thousands of times in a second. Even though many control engineers haven’t worked with time-based systems until the past few years, they’ll be able to use well-known programming languages to set up their work nodes.
“Using absolute time is a new concept for coordinating motion control. It is transparent to programmers,” Zuponcic says. “People programming with SERCOS (serial real-time communications system) won’t see any difference, they can use the same instructions they’ve always used.”
When customers are setting up their systems, they generally have to resist the temptation to put the highest priority on all data. If all traffic on the network must be delivered at peak rates, networks will quickly reach a saturation point. “Not everything needs to be deterministic. If you make everything time-critical, you will run out of space,” Wontrop says. “Customers must know their performance needs, which information needs to get from point A to point B in a deterministic fashion.”
Timing is also important in EtherCat networks, where the master synchronizes and locks all the device clocks to a reference clock’s time. That effectively distributes the exact 64-bit time values to all the field slave devices. The master can then synchronize and lock all the clocks throughout the network to the same system time.
“With this approach, the determinism and jitter of the network is divorced from the jitter of the Ethernet frames. This allows EtherCat to work without requiring high-priced, dedicated master controller cards,” Stubbs says.Ring runners
Though there is a strong drive to employ deterministic networks, not all of them require nanosecond delivery times. Dual-port nodes have helped make it much simpler to meet more mainstream networking requirements without adding hardware or software that pushes deterministic speeds to the tiniest fractions of a second.
“We believe that if we get determinism at around 50 to 100 milliseconds, we’re covering 80 percent to 85 percent of the applications we go after,” says Dan DesRuisseaux, manager, for automaton supplier Schneider Electric’s Ethernet Marketing Group, in Raleigh, N.C.
Using dual-port or four-port equipment arranged in ring topologies is a simple way to meet time-sensitive requirements that can accept millisecond data delivery times. This configuration lets nodes send data out one port and receive it in another. The ring architecture also lets signals reverse direction if there’s a broken cable or a node failure, reducing downtime. “When you’ve got two ports on a programmable logic controller (PLC), you have more fault tolerance,” says Marty Jansons, networking consultant for supplier Siemens Industry Inc., in Norcross, Ga.
Another alternative is to put demanding tasks on a network that has very limited traffic. This approach isn’t always practical, but it can provide enough throughput to ensure that data packets arrive in timely fashion. When networks don’t have many nodes, users don’t have to limit themselves to rings or loops.
“The CC-Link IE Field network can be implemented in various topologies to accommodate the user’s application. The layout can be daisy-chain, star, or any combination thereof—or even a loop,” says Chuck Lukasik, director of the CC-Link Partner Association-Americas, based in Vernon Hills, Ill.
Using small, dedicated networks can add some cost, but it can also help control expenses. For example, Schneider can stick with commercial off-the-shelf equipment such as Cisco routers and standard programmable logic controllers (PLCs) by controlling network design. Small rings can have high performance.
“We create dedicated rings that have just a few devices on them,” DesRuisseaux says. “We know their performance, and we don’t put high-bandwidth components like video cameras or PCs (personal computers) on those networks. By controlling the ring and installing just a few devices, you can determine the latency and get it down to 10 to 20 milliseconds.”
Using dual- and four-port nodes, communication can be quite robust. Multiport PLCs can bring data in while they’re transmitting, providing sharp improvements over older gear with only one port. DesRuisseaux notes that a growing number of input/output (I/O) devices are coming in dual-port versions, making it simpler to deploy this architecture down to the fieldbus level.
In many topologies, equipment placement is also important. If signals are far from a centralized controller, there will be more delays as data packets pass through switches. If devices that send and receive many signals are near the end of the network, this can also overload switches. “You don’t want to put a vision system or human-machine interface at the end of the line,” says Carl Henning, deputy director of PI North America, formerly the Profibus Trade Organization, with offices in Scottsdale, Ariz. “They have a lot of traffic. When it goes through a lot of switches, it ties up the available bandwidth.Expanding universe
Another facet of building real-time networks is to make sure that all critical devices can communicate without requiring gateways or converters. Though Ethernet is taking over the industrial world, fieldbuses aren’t disappearing. Many legacy devices are not Ethernet compatible and even many new products keep costs low by eschewing Ethernet ports in favor of simpler fieldbuses.
However, Ethernet connectivity continues to move further from the backbone, as controller costs come down. “We’re building the technology into more products so they all understand the protocols,” Jansons says. “The Profinet protocols are being built into more field devices.”
For deterministic networks to work efficiently, these lower-level devices must be capable of receiving high-speed messages and processing the instructions quickly. If simple devices can’t meet those demands, the network’s capabilities don’t mean much.
“A deterministic network doesn’t necessarily mean a deterministic system,” Stubbs says. “For industrial infrastructure and controls, the entire system needs to meet the requirements of the application, whether this means including time-stamped inputs, ensuring that outputs fire at exact times, including oversampled analog values, or coordinating complicated motion networks. The field devices must be integrated in a way that they can perform as a part of a deterministic system.”
In addition to proper integration, designers must ensure that devices have the memory capacity and processing power to keep up with the speeds that generally come with determinism. Many central processing unit (CPU) chips handle both communications and general purpose computing, so they can get overloaded. As the volume of information sent to the nodes rises, the processing power of the microcontrollers must also rise.
“The more power you’re using to service deterministic Ethernet, the less power you’ll have for tasks like motion control,” Wontrop says. “The ability of the node to handle data is a big factor.”Related Sidebar - Don't Change a ThingTo read the article accompanying this story, go towww.automationworld.com/feature-7863.
Subscribe to Automation World's RSS Feeds for Feature Articles
Companies in this Article
Companies in this Article
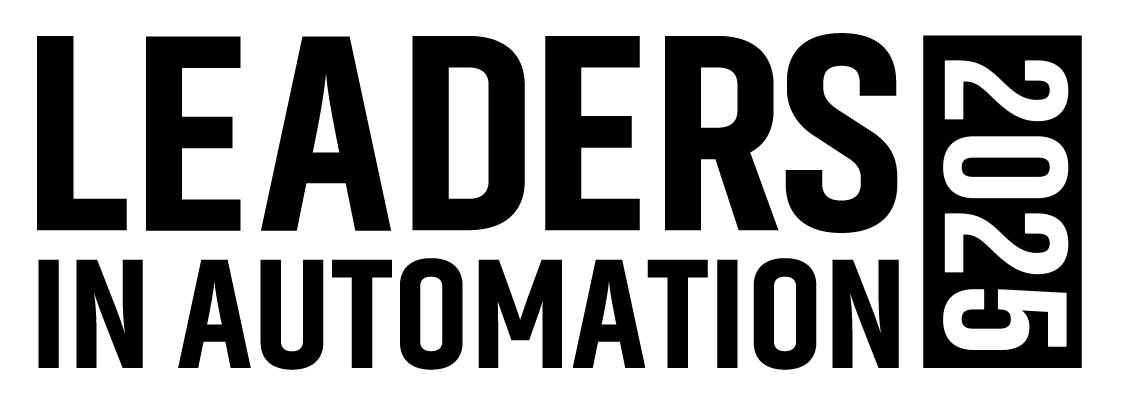
Leaders relevant to this article: