Getting maximum return on net assets essentially equates to improving Overall Equipment Effectiveness (OEE), which is a number derived from multiplying the percentages of throughput, availability and quality of a machine or process. Calculating the number, trending it and comparing it to similar plants, processes or machines all require obtaining information from all the areas of a plant—operations, maintenance and quality.From the biopharmaceutical to petrochemical examples detailed below to any other plant or factory, managers and engineers are discovering the power of breaking silos of information in order to raise performance and wring more productivity from their assets.You must obtain the data before you can use it. Ralph Rio, research director at ARC Advisory Group Inc., in Dedham, Mass., says that the hot topic in enterprise asset management (EAM) is mobility. “Things are happening in the consumer market that we can leverage,” adds Rio. “Mind share and volumes have driven prices down for the handset itself. Consumer smart phones with their apps are getting good enough for technicians to use. Adding RFID (radio-frequency identification) to the smart phone app removes data entry errors. And RFID plus Wi-Fi (wireless fidelity) lets you track moving assets—say, expensive or custom tools, or an expensive valve when you take it out of service and refurbish it and need to track it. We’re forecasting a 14 percent annual growth rate over the next five years in mobile devices because of all this.”Strategic and holisticStuart Harris, vice president and general manager of automation supplier Emerson Process Management’s Asset Optimization business, says, “The addition of asset performance management capabilities enables users to achieve more strategic focus, clarity and vision. In addition to reducing the complexity faced by management, enhancements to asset optimization help users move from reactive states to proactive, strategic and more holistic asset management.”Marc Leroux, manager for collaborative production management for automation supplier ABB in Columbus, Ohio, says, “If someone asks how we use asset management, we talk about marrying process and equipment. For example, what happens when you have an agitator in a process and the instrumentation says you’re drawing more current than yesterday, but the viscosity hasn’t changed? What can you derive? The motor is starting to overheat. It’s not just looking at the equipment but also at the process. A lot of information comes in from the process that helps explain how assets perform. It’s not only about replacing devices with smart devices, but it’s also about looking at the whole process and making judgments about overall health.”ABB has prototyped a demonstration of a system that gets actionable information out to the operator and technician ahead of time. Leroux describes the scenario: “What happens when there is a fault in a piece of equipment? What if you determine some value to know before it happens so the operator can begin taking action? Of course, many do that now. But if you can take that information and create a work request in the computerized maintenance management system (CMMS), now you’re ahead of the curve. You have all the information you need to get the right person with the right tools and parts out to the equipment in a timely manner. It’s not just notification, but also information about the problem. It’s not just creating the work order, but the ability to minimize the amount of time it takes for someone to go out and look at a problem.“Now take this idea further. What is the real objective of Enterprise Resource Planning (ERP) with integrated CMMS? As soon as you put a work order in the system, why does no information get to the production planner? He just talks at the morning meeting with no knowledge of the pending problem. What’s important to maintenance is not necessarily the same as for operations, which is not necessarily the same as for the production planner, who may be working with corporate. So, if the ERP says this is the value, information could get to more people that need it.”Don’t discuss theory with BioMarin’s Jim Kroyer. All he needed was a flexible system to help him get a handle on maintenance. Kroyer, principal engineer for equipment reliability, has been at the Novato, Calif., plant for 11 years, serving as maintenance manager and facilities director. “I felt we needed a high-level commitment for reliability, so I stepped down from my previous position to lead this effort,” he says. BioMarin, a developer of commercialized innovative biopharmaceuticals for rare, serious diseases and medical conditions, knows the importance of compliance. Patient and product safety drives many decisions. “BioMarin started with poor maintenance business processes. We had good compliance maintenance, but just not good business flows, and too much paper,” Kroyer relates. He searched for a software solution to the process with objectives for adopting enterprise asset management including Good Manufacturing Practices (GMP) compliance, to develop good controlled business processes and eliminate paper documentation of work. “EAM is the cornerstone of our ability to do this and we now have a fully validated system that is helping us to redefine our maintenance program.”When Kroyer began his investigatin, the company had no maintenance and reliability software, other than some scheduling applications. “I attended a seminar on the subject and realized we had no way to capture data to get started. So we needed a CMMS. We proceeded on a vendor selection process and eventually focused on Infor, a business applications supplier located in Alpharetta, Ga. We started the process in May 2006 and began implementing the system in July 2009.”BioMarin chose Infor for two specific reasons, both of which held up during implementation. First was the highly configurable development environment. Second was the implementation team that consulted with them.The first thing Kroyer’s team did was develop a business process flow. “We’re regulated. Practices on maintenance were compliant, but not good enough for business process. We developed 35 business process flow charts in both regulated and non-regulated environments. Once we accomplished that, then we figured out how to configure the Infor Enterprise Asset Management (EAM) application to meet our needs. Then we started on validating the process—a bigger project than anyone anticipated. We probably spent nine months on validation all together.”The system went live in two phases. Calibration, equipment management and system administration came up in April 2010. Preventative maintenance, repair maintenance and workflows for notification began at the end of June 2010. Kroyer relates that the results so far have been positive. “It operates well and is robust. We have almost 5,000 work orders generated, and the system handled them without missing a beat. A lot happened beneath the radar on the old system, but now you see everything. It’s all visible. It’s helpful for developing metrics—something we’ll develop more thoroughly as time goes on.”Following the introduction of its InFusion Enterprise Control System in 2006, Invensys Operations Management (IOM), the Plano, Texas, process automation and software supplier, spent the next several years explaining just what it meant with this new direction. And perhaps nothing illustrates the value of integrating information from disparate sources as well as the implementation of a plant information management (PIM) system at Petro Rabigh.Since 2005, Rabigh, Saudi Arabia, a port city on the Red Sea, has been home to a major refinery. The PetroRabigh complex produces fuels and petrochemicals for the domestic market and for exporting to Europe and Asia. Petro Rabigh is one of the largest fully integrated oil refinery and petrochemical production facilities in the region, and it is the largest integrated refinery in the world built at a single time. It is comprised of 23 plants that produce 18.4 million tons per annum (mtpa) of petroleum-based products and 2.4 mtpa of ethylene and propylene-based derivatives.When management decided to expand the facilities, they set a goal of commissioning the plants with integrated operations management and business systems by 2009. The objective of the PIM System Project was to integrate the disparate functional systems in the complex to improve management of the plant operations. In its original iteration, production and corporate business functions were separated. But this did not give executives the overall visibility and access to data that they needed to help them make informed decisions about production levels, supply, demand, use of resources and personnel allocation.To meet this need and to respond to the pressures of a changing global economy, Petro Rabigh required a system that would unite planning, scheduling, operations management, production accounting and other tasks. Ideally, the new platform would enable various plants to share information and communicate. The plant-level systems had to be integrated with the business system, namely, an ERP system supplied by SAP AG, the Walldorf, Germany-based enterprise software supplier.They chose InFusion ECS (for Enterprise Control System), because it was designed on open, industry-standard technologies and could synchronize information from multiple systems and applications. “Invensys Operations Management solutions have demonstrated consistent ROI (return on investment)—paying out in as little as six months, but definitely within 12 months,” says Yadukulatilakam Ramaswamy, IOM senior director.A diverse, global team was assembled, including application engineers, process engineers, and project development and management experts from Invensys Middle East, Europe, India and North America. The Invensys Netherlands group was the hub for the senior technical team, and also hosted the Factory Acceptance Test for the solution. And finally, the development team worked from the Invensys offices in Dubai, United Arab Emirates, as the system migrated toward commissioning. To maximize efficiency and minimize travel costs, much of the work was accomplished via remote network connections.The Invensys InFusion platform integrates multiple components to form the foundation of the PIM System, including:Laboratory Information Management System (LIMS)—This application manages the laboratory and organizes multiple processes into one database where analytical data is entered, stored and managed.Operators Logbook—This application integrates with InFusion to collect real-time data, manage operations and personnel scheduling, plus visualize production orders, handle key performance indicators (KPIs), sample results, downtime and mass balance error events.Mass and Energy Balance—This application provides hourly and daily reporting of reconciled production data.KPI—Key Performance Indicators are computed in the InFusion environment. Calculated results are stored and made available enterprise-wide.Downtime Monitoring—Stops, starts and runtime data are collected and stored by InFusion and reported to the Logbook.Oil Movement and Management—Tankfarm management and oil movement are handled by this part of the system, including inventory, order management, optimization of oil blends, batch tracking and other functions.Alarm Management—The critical data from the monitoring of events and alarms can be viewed from the unified PIM viewer interface. “By harnessing these capabilities under a single, integrated environment, the Invensys solution provides Petro Rabigh with significant improvement in the management of the complex, and substantial financial savings into the future,” says Ramaswamy.Grant LeSueur, IOM director of product marketing, summarizes the project, “They had a quagmire of process control and information solutions. Some business functions had to integrate with the ERP application. In the end, it delivers to the customer a global reporting and information management system irrespective of type of equipment in the plant. One interesting result is that a lot of information we gather went into the ArchestrA Log Book—a type of log chart operators would fill out every so often on paper. Now built into ArchestrA as a digital file, it became a central document of record for review and scheduling meetings. When we supplied it, we didn’t know that’s how it would be used, but the information coalesced and went in the logbook. The InFusion ECS was built for a plant like Petro Rabigh.”Machine OEMs benefitThe idea of obtaining information directly from manufacturing processes in order to generate usable metrics for operations management is not unique to huge refineries or advanced bio-pharma processors. Getting original equipment manufacturers (OEMs) of machines involved in helping their customers gather diagnostics and other metrics results in a win/win situation.Dan Seger, principal application engineer for Rockwell Automation Inc., the Milwaukee automation supplier, discusses how embedding standards directly into the machine control and development software—a technology feature recently released by the company—has the potential to generate those positive results.“Programming templates and power programming are starting to get traction,” says Seger. “Right now, our solution is geared toward packaging. We’re trying to knock out the first 75 percent of code development with these tools. We already have more than 50 engineers trained. OEMs seem to be accepting it. A lot of machine designs are ramping up.”The package includes PackML (packaging machine language) and PackTags, both developed by the Organization for Machine Automation and Control Packaging Working Group (OMAC). This includes standardized state models and definitions of packaging machines. The standards are embedded in the control and in the development software.“This reduces development time for OEM engineers, where they make bread and butter,” Seger adds. “It’s how to quickly build, check out on floor and check out on customer site. This means they make money more quickly. With the embedded PackML and PackTags, our software will extract the information and display it in [Rockwell’s] FactoryTalk. The OEM can collect this information during runoff to help troubleshoot and establish a baseline of performance that can be used at customer acceptance.”So, from hybrid to continuous to machine automation, integrated information improves all aspects of operations management.
Subscribe to Automation World's RSS Feeds for Feature Articles
Sponsored Recommendations
Sponsored Recommendations
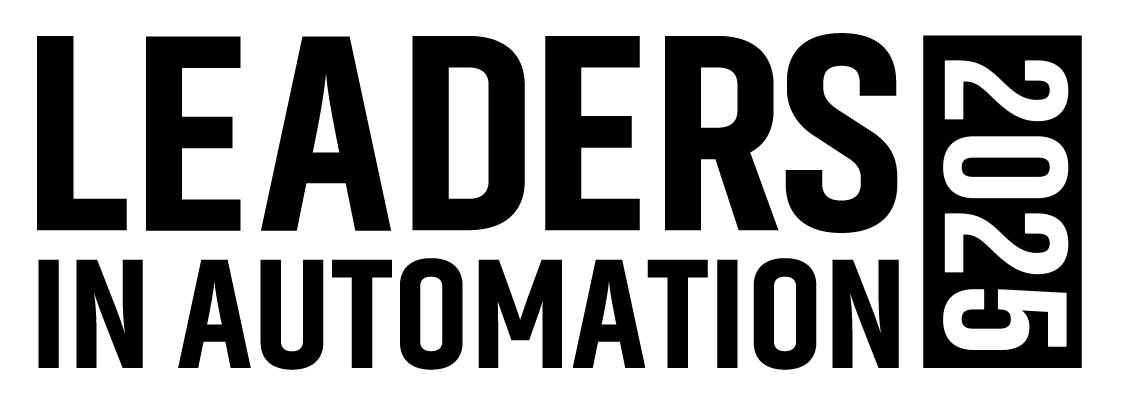
Leaders relevant to this article: