For many folks, the subject of industrial safety brings forth visions of signs saying, “SAFETY GLASSES MUST BE WORN BEYOND THIS POINT.” That, and stern instructions to keep hands away from moving parts.
Important instructions, surely, but as static as some attitudes toward safety. In reality, industrial safety today, including in the packaging industry, is a dynamic and rapidly changing field whose trends and debates, though specific to the subject, mirror those that characterize automation as a whole.
Perhaps the most obvious change is in the topology of the safety system itself. Traditionally, production-line safety systems have deployed an array of devices, such as door interlock switches, sensors, safety relays and the like, with the intelligence for the safety system supplied by a programmable logic controller (PLC)—often a dedicated safety PLC. Today, however, automation vendors are imbuing servo-motor drives with intelligence, allowing these formerly dumb devices to handle new tasks, including safety logic.
Some have questioned the usefulness or relevance of this recent trend, but Brian Deal isn’t one of them. “There has been an ongoing debate regarding where exactly to locate a safety function,” acknowledges Deal, packaging market segment manager for automation supplier Schneider Electric, of Palatine, Ill. “However, safety inside the drive will become necessary because the drive, with its moving parts, is the main source of risk in a machine. And if a drive is able to monitor its own safety behavior, it is able to react faster to changing conditions.”
David Arens, food and packaging applications engineer at supplier Bosch Rexroth Corp., in Hoffman Estates, Ill., forcefully seconds that notion. “You can’t have a good handle on the operational condition of the machine unless all of the components can be ensured on their safe and reliable operation, so incorporating safety and/or safety monitoring into all of the devices on a machine is actually, in my opinion, a future critical path.”
Integrating safety functions into the drives, as well as other components, can not only boost safety but also have a positive impact on other aspects of machine operation as well. For instance, it may obviate the need for an external speed-monitoring device or for a contactor, which is a relatively large and costly device. Fewer components can mean less expense, a smaller space requirement, reduced wiring, faster installation, and easier monitoring and maintenance.
Beyond the specific example of the drive lie two factors: the functional safety concept and international standards, both of which are acting to push safety concerns and safety functionality deeper into the guts of the production system. First, the concept.
Functional safety is a holistic, or “end-to-end,” approach to safety. Traditionally, safety systems have been somewhat isolated from the automation system. They were implemented and controlled separately from the automation system, and the criteria for evaluating the safety level of equipment and systems tended to be limited to specific technical inputs. Functional safety, on the other hand, evaluates the safety of a system or piece of equipment in relation to a broader range of “real-world” inputs, including the operation of upstream and downstream systems, as well as likely operator errors and environmental disruptions.
The goal is two-fold: one, to improve the overall level of safety, and two, to improve the functional operation of the machine or system. In the past, equipment safety and productivity have been viewed as separate and generally competing goals; the concept of functional safety brings them together.The role of standards
The question now becomes, how do you evaluate functional safety? You can’t just wing it; there must be standards. Fortunately, there are—IEC 61508, for starters. Developed by the International Electrotechnical Commission, this is a standard for the evaluation of functional safety of products, components and systems, covering electrical/electronic/programmable electronic (E/E/PE) safety-related systems, along with the assessment of the proper safety integrity levels (SILs).
Deriving from that is IEC 61800-5-2, a standard that allows the evaluation and quantification of safety for adjustable speed electrical power drives. The key here is that prior to the promulgation of these and related standards, there was a reluctance to accept electronic and programmable electronic components in safety related functions—just the sorts of components that are being increasingly used in every aspect of today’s packaging operations. With the aid of the methodology provided by IEC 61800-5-2, this is changing.
The overarching standard in this regard is EN ISO 13849-1, promulgated by the International Organization for Standardization, which governs the safety of machinery and safety-related parts of control systems. (The EN in the standard stands for “European Norm.”) This replaces EN 954-1, the standard that has been in place for almost two decades. Or, rather, it will replace it. The new standard was due to take effect on Nov. 30, 2009, but the date for compliance has been pushed back to December 2011 to give machine builders, many of whom have been hard hit by the recession, more time to make the switch. Packaging machines sold in Europe after that date will have to comply.
Though no official body is mandating that U.S. machine builders switch to the new standard, general compliance is a foregone conclusion. After all, in today’s globalized market, only the smallest and most specialized U.S. packaging machine builder can afford to 1) ignore the European market, or 2) engineer and build separate machines for the United States and Europe.
Along with inevitability, there are other good reasons for adoption of EN ISO 13849-1. Like IEC 61508 and IEC 61800-5-2, it encompasses the programmable electronic devices that increasingly characterize today’s machines, and includes software in its safety focus. It also provides a quantifiable methodology for risk assessment of machines and components. This last bit—quantifiable risk assessment—is crucial.
“This is going to have a profound effect on the machines in our industry because it’s going to place more responsibility on builders to calculate safety levels in their machines,” says Leo Petrokonis, business development manager, packaging, for controls vendor Rockwell Automation Inc., Milwaukee. “As a result, they will be more sophisticated and informed about safety, which will ultimately benefit the end-users.”
Dave Kirklen, business developer for the packaging industry for automation supplier Siemens Industry Inc., Alpharetta, Ga., sees the new stress on risk assessment as beneficial to machine builders as well. “Being able to give a component a safety certification makes that component, in effect, a safety module, and this will make it easier for builders to reproduce or adapt that module for additional components. This will speed future testing and certification, and ease the overall design task.”Integrated safety
Siemens and Rockwell agree on another matter as well: the value of integrated safety. Historically, safety has been separated from standard control. Integrated safety (to simplify a complex subject) places both of these functions in the hands of a single powerful controller communicating over high-speed networks. The Rockwell folks point to Gram Equipment A/S, Vojens, Denmark, one of the world’s largest producers of ice cream manufacturing and packaging equipment, as an example of some of the benefits that can be gained from this approach.
Gram wasn’t satisfied with its traditional safety systems, comprising a PLC, a separate safety PLC and a servo system. Staff had to learn how to use three different software programs, and also how to connect the systems so they could communicate with one another. If the equipment had to be modified, this necessitated time-consuming changes to electrical documentation as well as programming changes that could only be carried out by a few, specially trained staff.
To simplify this complexity, Gram Equipment opted for Rockwell’s Allen-Bradley GuardLogix control, which combines standard and safety control in one platform. Gram finds this saves on cabling, components and commissioning time.
“Without an integrated safety solution, an electrician is required to connect all emergency-stop buttons and safety doors to a machine’s main electrical cabinet,” notes Morten Zornow, electrical design department manager for Gram. “Therefore, the electrician had a lot of cable work to do at commissioning. With an integrated safety solution and a decentralized safety I/O (input/ouptut), all safety equipment can be mounted on a machine during an initial test. The electrician has fewer cables to handle during the commissioning process because there is only one bus cable (either DeviceNet or EtherNet/IP), rather than one network for each safety device.”
Additionally, staff training was simplified as only one platform had to be learned, and customer-requested modifications became easier to implement. Also, because the system’s standard and safety I/O modules both communicate via EtherNet/IP, troubleshooting and repair of a customer’s I/O points can be carried out from Denmark—a major savings for all concerned.
“Troubleshooting is easier because you can read everything via the Internet connection and the HMI (human-machine interface) display,” stresses Zornow. “Viewing all system information via the HMI display is possible without an integrated safety system; however, a user must connect individual safety devices, such as emergency-stop buttons, using auxiliary contacts to allow communication to the PAC (programmable automation controller).” However, auxiliary connections often result in error messages or missing information, says Zornow. “With an integrated safety system, you can read the status of the safety equipment directly, thereby ensuring correct messages and accurate information.”I/O-centric
Another alternative to the traditional safety PLC is supplied by Beckhoff Automation LLC, of Burnsville, Minn. Beckhoff markets a PC-based control system that allows machine builders and end-users to create safety systems with e-stops, light curtains, safety doors and similar devices using its TwinSafe safety I/O terminals that can be used without a dedicated safety PLC. Multivac GmbH, Wolfertschwenden, Germany, chose the system for its R 535 series of thermoformers that can pack a variety of food products, such as sausage, fish and cheese, and also industrial goods and sterile medical products in vacuum, protective gas, skin or blister packs.
“Our packaging machines are a standard product, to a large extent. However, no one automated packaging line is like another,” says Alois Allgaier, division manager for control technology at Multivac. “Our machines are constructed on a modular basis so that we can individually configure customized solutions and adapt the modules in the best possible way.” Allgaier believes that the PC-based approach, with its non-traditional safety system, facilitates that goal.
Previously, Multivac wired the safety components in a conventional way. In the R 535, the safety functions are integrated directly in the bus terminal system using the TwinSafe terminals. The safety data are recorded on site and evaluated in the TwinSafe logic terminal.
“TwinSafe drastically reduces the costs and time involved in wiring,” says Allgaier. “The benefits are obvious. We select the necessary TwinSafe terminals depending on the machine and integrate them in the control system. This is simple, convenient and cost-effective as well.”
These are the same benefits—simple, convenient and cost-effective—that Helge Hornis, manager, intelligent systems, for automation components supplier Pepperl+Fuchs Inc., Twinsburg, Ohio, claims for Intelligent AS-interface safe devices. AS-interface is the Actuator Sensor Interface, a networking protocol for use in PLC-, digital control system (DCS)- and PC-based automation systems to connect simple field I/O devices using a single two-conductor cable. It allows safety and standard devices to be connected to the same network cable, typically the AS-interface flat cable, which allows AS-interface modules to be installed anywhere on the network without cutting and preparing the cable first. The result is a faster installation without the chance of inadvertent shorts between the leads.
“The beauty of AS-interface is that you can mix and match safety and conventional I/O on the same cable, and do it quickly, which also improves the ease of building the machine,” says Hornis. It also lends itself to a low-input approach to I/O that Hornis believes could prove beneficial to packaging-machine builders.
“Typically, sensors and safety devices are individually routed, wire by wire, back to a terminal in a metallic enclosure, so you have a very high density of I/O within these enclosures,” says Hornis. However, he believes that there’s a place for a very small I/O module that clips on to the ASi cable and has one or two sensor inputs. “These could be placed in close proximity to the sensors, thereby greatly reducing the interconnected wiring. I’ve seen many machines where I think this will be quite advantageous.”
Clearly, safety has entered an active, dynamic phase as vendors and machine builders employ current technology and standards in an effort to make safety systems more flexible, and easier and cheaper to implement, while also boosting equipment functionality. Still, don’t forget your safety glasses.Related Sidebar - Pioneering a New Era in Paperboard ProductionTo read the article accompanying this story, go towww.automationworld.com/feature-7551.
Subscribe to Automation World's RSS Feeds for Feature Articles
Companies in this Article
Companies in this Article
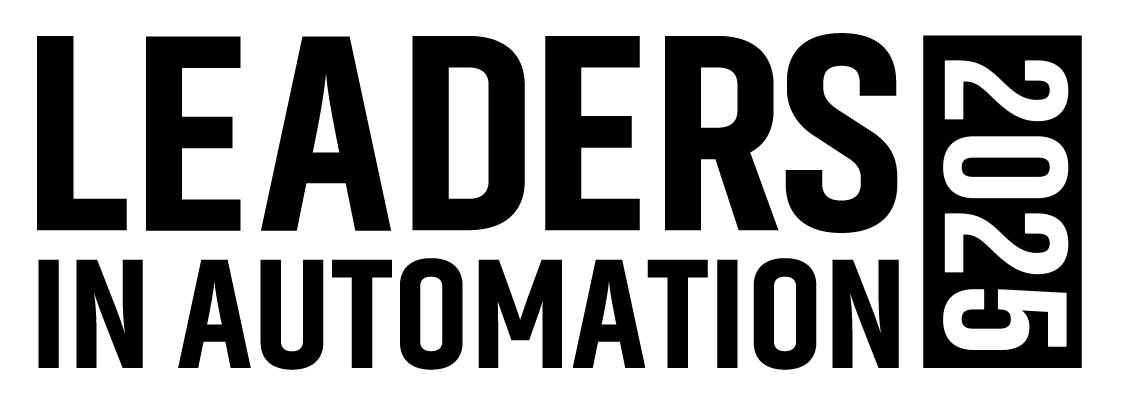
Leaders relevant to this article: