Casa Herrera, Pomona, Calif., builds tortilla preparation equipment for the corn and flour tortilla industry, provides equipment for the bakery and snack food industries, and is the preferred supplier to several national brands. The company builds several varieties of its machines to meet customer specifications, and installs and services all of the equipment it manufactures.
For one of Casa Herrera’s current-design tortilla-making machines, the company wanted to upgrade the control system. Casa Herrera had been building the same machine for seven years, and mechanically, it is proven and reliable. The problem was with the programmable logic controller (PLC) control system. Although the PLC that Casa Herrera had been using was reputed to be the best in the world, the company had experienced limitations due to slow speeds and information streaming interference, and the service was adequate, at best, says Ron Meade, Casa Herrera chief executive officer.
“We wanted to upgrade to a control system that was capable and reliable, and also flexible enough to install on different machines. The control system also had to be easy to maintain, diagnose and repair in the field,” Meade says. After evaluating all of the leading competitors, including PLCs, industrial personal computers (IPCs) and Programmable Automation Controllers (PACs), Casa Herrera selected and recently installed a control system from Automation Direct, an online supplier of controls and automation components.
For assistance with control system design and implementation, Casa Herrera called in local control systems integrator, Memco. The integrator works closely with Casa Herrera’s Automation Direct value-added reseller, Quantum Automation, on complex control projects such as this one. Memco designed, fabricated, programmed and installed the tortilla control system based on a Productivity3000 programmable controller, C-More human-machine interface (HMI) panels and GS variable speed motor drives—all supplied by Automation Direct.
The Productivity3000 monitors and controls the entire machine via 365 discrete and analog inputs and outputs. Each of the 27 motor drives is interfaced to the controller via a high-speed Ethernet data link. The two C-more HMI panels are also connected to the controller via Ethernet. As shown in the figure (below left), industrial Ethernet hubs are provided to control and coordinate all data exchange.
Complex control
With modern automated tortilla machinery, there are many critical timing points throughout the production line. The product is very sticky at the beginning, slippery in the middle, and flexible at the end—making the equipment set-up for each area very exacting. The Productivity3000 helps everything stay in sync by controlling all parts of the production line.
The control system components are networked together using Ethernet communications. The network is reliable, very fast, and easy to connect and maintain. The entire database is stored in the controller’s memory, so technicians have full system documentation online.
The HMIs have extensive graphic capabilities, providing the ability to display pictures of the machine and of the sub-panels to assist maintenance personnel with troubleshooting.
“The Productivity3000 is one of the fastest processors I have ever programmed,” notes Phil McCall, a Memco control system designer. “With the entire line programmed and running, the scan time of the processor and all I/O is 0.6 milliseconds (ms). This makes the machine very responsive to the operator. On this application, we used approximately 5 percent of the system resources. I have no doubt that this system could run multiple lines or even an entire plant, with performance exceeding other PLCs, and at lower cost to boot.”
The Productivity3000, C-more HMIs and motor drives are very straightforward to set up and program. Tag names from the controller program can be imported into the HMI programming software, saving time. The analog cards have displays that show the status of each channel and its configuration, so technicians don’t need a meter to perform checks.
The HMIs have the capability for remote viewing, or even full remote control from a standard Web browser. They also have multi-language support—so the names and words on the screen can be changed to one of nine languages at the push of a button—including character or script-based languages such as Chinese, Japanese and Arabic.
These capabilities proved valuable in meeting Casa Herrera’s requirements. “We wanted a control system that had a cutting-edge, intuitive diagnostic system, got around language barriers and was able to implement remote servicing capabilities over the Internet,” Meade relates. Because virtually all control system information is stored in the controller’s central processing unit (CPU), Memco was able to develop a troubleshooting system that was very elaborate. It makes use of high-resolution photographs of the machine with associated graphics that can clearly identify problem areas when faults occur.
The troubleshooting system usually enables quick repair to be performed by a mid-level maintenance person. But if the problem cannot be solved quickly on site, the Productivity3000 and the HMIs feature full remote access. With this feature, every I/O module, motor drive and sub-component connected to any of the communication ports can be accessed through the Ethernet data port—either locally or remotely through a standard Internet connection.
As a result, Casa Herrera can remotely view every motor drive parameter as well as every status register. The same goes for every rack, power supply and I/O module. The HMI screens also allow live, real-time remote viewing and control so the screen faults can be seen from anywhere. For detailed off-line analysis, the data logs, fault logs and event logs stored on a local USB memory stick can be viewed and downloaded using FTP.
“Since the commissioning of the first Productivity3000 tortilla line for True Foods, in Melbourne, Australia, we have gone online from California to monitor the control system in real time,” says Meade. “We have added customer-specific changes to the program, and we’ve tuned motor drive parameters. We also added new screen buttons and data trending features to the HMI, all in a matter of minutes.”
Future perfect
Casa Herrera sells many variants of this tortilla line: bigger, smaller, single line and double line. To accommodate these various types of lines, Memco devised a scheme by which the operating logic in each type of machine on the line is in a separate file. These files are called to action upon the system recognizing various control system components connected to the Productvity3000 via the Ethernet network.
The controller has the ability to ignore a completely disconnected rack or motor drive, and not fault the system. This means that end-users have the entire software program already loaded for any future possible expansion. All they need to do is power the equipment and plug it into the network.
This also means that Casa Herrera only needs to maintain one program for all tortilla lines sold with the Automation Direct control system. “We are currently working on control system additions to integrate machine vision and robotic handling to the product line. This will allow us to provide our customers with a complete turnkey manufacturing solution,” Meade concludes.
Subscribe to Automation World's RSS Feeds for Feature Articles
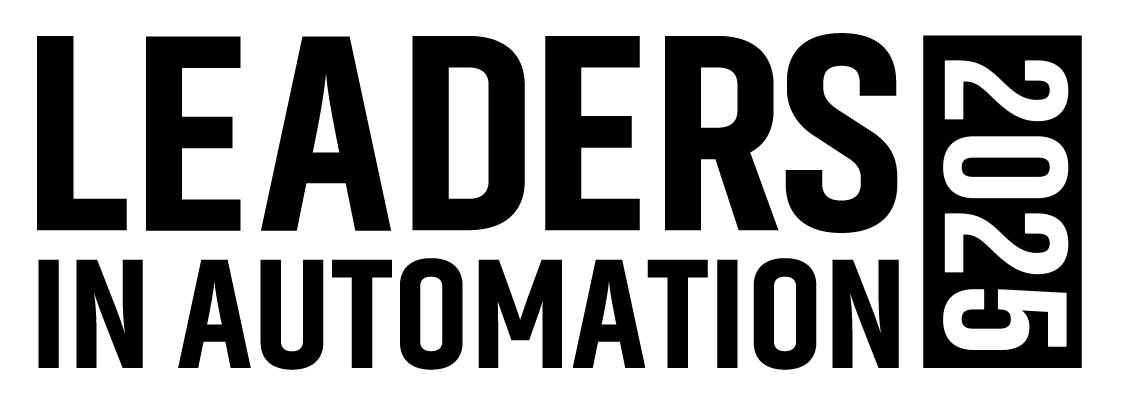
Leaders relevant to this article: