Over the past several years, the City of Orlando Public Works Department has installed extensive high-technology upgrades and automation systems in its three wastewater treatment plants, vastly improving the capacity and efficiency of its operations. Orlando’s 320-acre Iron Bridge wastewater plant, for example—the largest of the three—was originally built in the 1980s to treat about 5 million gallons of wastewater per day. But after several modifications and upgrades, it can now treat and reclaim up to 40 million gallons in that same 24 hours.
Yet despite that growth, the plant today can be operated with significantly fewer employees than in the past, says Guy Mecabe, wastewater system manager. Indeed, Iron Bridge has gone from more than 20 operators needed to run the plant just a few years ago to as few as three per shift today, Mecabe says.
The primary driver for that productivity gain has been the automation system put in place beginning in 2005. Based on programmable logic controllers (PLCs) linked by Profibus and Industrial Ethernet networks supplied by Siemens Industry Inc., Alpharetta, Ga., the automation platform controls everything from the flow of electricity to the amount of reclaimed water being discharged from the plant. Operators can monitor and manage the entire operation from any of 10 on-site Siemens human-machine interfaces (HMI), or remotely using Siemens WinCC supervisory control and data acquisition (SCADA) software.
Video connection
But in addition to the extensive amount of real-time process data made available to operators through the HMI/SCADA system, the displays also include a still somewhat unusual capability in the industrial space—access to real-time and recorded video. With a single mouse click, operators can access live, streaming video from any of 18 digital Internet protocol (IP) video cameras mounted in strategic locations throughout Iron Bridge and the other two plants, known as Water Conserv I and Water Conserv II. Traveling over the same broadband fiber optic-based Ethernet network as the process data, the live video feeds can appear as pop-ups directly on operators’ HMI screens, enabling them to keep tabs on what’s happening across the facility.
“We actually started looking into video about three years ago,” says Mecabe. “We were looking for something that would handle both the security aspect of video surveillance and also the process aspect.” Because plant managers knew that they would be operating with significantly fewer employees, “we wanted to give our operators some eyes and ears out in the field,” he explains.
On the security side, the digital video system replaces an earlier analog closed-circuit TV (CCTV) system. IP video cameras are located at all three plant front gates, enabling control-room operators to handle gate duties while also monitoring operations. When a vehicle pulls up to a front gate, the driver pushes a button, signaling the control-room operator to bring up the gate camera video pop-up on his or her HMI screen. The operator can control the camera to zoom in on the vehicle license plate and the driver’s face, and can carry on a two-way conversation over the network using the camera’s audio capability, finally opening and closing the gate through the HMI system to allow vehicle passage. Video is archived on servers at each site for access later as needed.
Other cameras are used to improve process operations. At Iron Bridge, for example, four cameras are trained on the plant’s sludge processing operations, where solids are separated from the water and carried on conveyor belts through a building and up an incline to be dropped into trucks. Operators in an upstairs control room can switch the sludge flow from one conveyor to another, and on some occasions in the past, “they switched it when there wasn’t a truck there, so it piled up on the floor and made a big mess,” Mecabe says. But with the IP video cameras in place, operators can now check to be sure that a truck is in position before making the switch. “Since we put in the cameras, we haven’t had any messes.”
Mecabe also points out that having the video integrated into the WinCC SCADA system has been an important time saver, given the plants’ reduced staffing levels. “The video gives these guys the ability to quickly check and see something, rather than having to jump in a truck and drive out,” he observes.
The Orlando wastewater plant system is one example of an emerging industrial trend involving wider use of digital video technology for applications ranging from industrial security and safety to compliance, process monitoring and productivity improvement. In many cases, video is being integrated into HMI/SCADA networks for display when needed on operator control panels. In some cases, video shot by legacy analog CCTV cameras is digitized for network transport, but the trend is toward use of modern, all-digital IP cameras, sources say.
The trends are driven by several converging factors, including advances in video digitization, improved video compression technologies and larger network bandwidths. This means that as industrial networks migrate increasingly to Ethernet-based transmission control protocol/Internet protocol (TCP/IP) networks, high-quality IP video can be easily added for transmission along with process data and other network traffic.
“The idea of surveillance has been around industrial automation for a while, but from a security perspective only. And what people are starting to realize is that it’s possible to integrate video surveillance into HMI/SCADA systems, which can really change the way you monitor and control devices in the field,” says Jim Toepper, product marketing manager, industrial Ethernet and video networking solutions, for Moxa Americas Inc., a Brea, Calif.-based industrial network components vendor.
One-shot payback
Today, for example, if an alarm goes off in an HMI/SCADA system that says pump 33 is frozen, the operator might see only a red light or other similar indicator, Toepper says. “But with some of the technology that we’ve developed to help integrate cameras with the HMI/SCADA networks, we are literally able to pop up a window of live video as a plug-in to that SCADA system itself.” This enables the operator to make a visual assessment of the situation and make a better decision on what, if any, actions to take. “The big benefit is knowing how to respond to alarms. It’s just more information,” says Toepper. “This can certainly pay for itself in one shot, if you get a visual cue that helps you react to a situation faster that might prevent a catastrophe.”
Steve Rubin, chairman and chief executive officer (CEO) at Longwatch Inc., a Norwood, Mass., provider of industrial video technology, is quick to agree that video can be a powerful source of added intelligence for operators. Among other things, the Longwatch Video Surveillance System can provide a snippet of video associated with an alarm that—when clicked on by the operator—shows what happened just prior to, during and after the event that triggered the alarm. “This removes a lot of having to go digging back through alarm logs and trends,” says Rubin. “You look at that picture, and you know what’s going on. It turns data into information, quickly and unambiguously.”
While Longwatch focuses on video software, Moxa’s ultimate goal is to drive sales of network hardware components, Toepper says. Among other things, Moxa sells ruggedized IP video cameras and also supplies industrial-grade encoders that can translate analog signals from legacy analog CCTV cameras into digital signals for IP network transmission. As a way to promote the idea, Moxa has also developed software plug-ins that can be used to enable video pop-up windows in various popular HMI/SCADA systems, including Citect, GE Intelligent Platforms’ Proficy and Wonderware, from Invensys Operations Management.
Moxa is also working with major process controls vendors in the field. Japan-based automation supplier Yokogawa, for example, relies on Moxa encoders as part of its FieldEye camera system, which integrates video with HMI/SCADA for use in the oil-and-gas industry, says Francis Go Shiang Ko, Yokogawa product manager for CCTV integration, based in Singapore.
Introduced about two years ago, the FieldEye camera relies on analog video camera technology using a CCD (charged-coupled device) image sensor, which Go Shiang Ko says provides better light sensitivity than the CMOS (complementary metal-oxide-semiconductor) image sensors used in digital IP video cameras. This is particularly important in oil and gas, he says, where nighttime, low-light levels on offshore platforms and other facilities are not unusual.
Yokogawa has so far sold between five and seven FieldEye systems into the field, some with up to 250 cameras attached, according to Go Shiang Ko. And demand for the technology is running strong among oil-and-gas customers, he adds. The vendor has developed its own video-to-HMI/SCADA interface. “The whole idea is to make use of these CCTV cameras to match with all the detectors, such as fire and gas detectors,” Go Shiang Ko explains. “In the event of an alarm, then the camera will pan to the area where there is a problem, and we pop the video up in front of the operators, so they can take action immediately.” The system can serve a safety function, by letting operators see when it is too dangerous to send personnel into a trouble area where fire is occurring.
Other FieldEye applications include monitoring of day-to-day operations, such as watching contractors at a field site, or checking on equipment such as valves or transmitters that are physically hard to access, says Go Shiang Ko. Another common oil-and-gas application is real-time video viewing of gas flares, he adds, as an added process and environmental check. Besides receiving continuous emission monitoring data via their control panels, operators can use video to “look at the flare to tell whether there is trouble or not,” says the Yokogawa manager. “If it’s burning a lot or there is a lot of black smoke, then they know they have to take quick action to balance the process.”
Video analytics
Honeywell Process Solutions (HPS), the Phoenix-based process control vendor, also sees a demand for video flare monitoring among its oil-and-gas customers. As part of its Digital Video Manager (DVM) system, sold as a component to its Experion controls platform, Honeywell has developed video analytics that can automatically detect a flare upset—based on flame size, color and other factors—and then send an alarm to operators, points out Annemarie Diepenbroek, Honeywell global product manager, DVM for Experion, who is based in Sydney, Australia.
HPS has been a pioneer in digital video, starting around the year 2000, and has some 3,000 installations in the field, according to Diepenbroek, with some linking thousands of cameras. The company has lately seen “a huge interest in video,” among its process industry customers, she says, due in part to dramatic cost reductions related to digitization. “We now have customers looking at a video solution first, and our Experion solution second.”
Beyond the added value that integrated IP video can bring to operators, another important feature is that video is no longer limited to a single control room or security gatehouse, Diepenbroek points out. “It’s available anywhere, to anyone in the plant, so there is a lot of information that even a plant manager can get from video when a situation arises,” she notes. “He may not look daily at all the videos. But he will definitely have an interest.”
HPS on June 7 announced an enhanced version of the DVM system, featuring “an upgraded system architecture that allows operators to more easily manage multiple video subsystems deployed across global facilities from a central location.” The new DVM R400 also integrates with Honeywell’s OneWireless technology, enabling more flexibility through the installation of wireless cameras in virtually any location.
Despite the trend cited by many toward integrating video with HMI/SCADA, some industry participants raise questions about the idea. At Apprion Inc., for example, a Mountain View, Calif., industrial wireless technology supplier, Steve Lambright, vice president of marketing and services, says that his company’s process industry customers haven’t asked for such integration. The company currently has between 10 and 15 systems installed in the field that include video.
Apprion—which on June 15 unveiled the third release of its ION Video Application—favors the use of a separate monitor for video. Using video analytics, predefined events, such as motion in an area or a release valve going off, can be set to notify an operator to go look at a separate video monitor, Lambright says. “Your video system should be smart enough to allow you to define the alerts and alarms that will tell you when to look at the video,” he declares. “The last thing a busy operator needs is to have a distraction such as a video screen that’s constantly showing things popping up in front of him.”
Likewise at automation supplier Rockwell Automation Inc., Bradford Hegrat notes that if video is integrated into an HMI system, asset owners must “ensure that the HMI is engineered not to overwhelm the operator,” and that all operators have been appropriately trained to use the technology. “You also have to engineer the HMI for a worst-case scenario,” adds Hegrat, who is principal security consultant for Rockwell’s Network and Security Services unit, based in Mayfield Heights, Ohio. “What happens if there’s a major control system event and a major external security event happening at the same time?” he asks. “Will that operator still be able to function appropriately?”
Honeywell’s Diepenbroek, for one, is quick to agree that operator overload must be avoided. But when designed correctly, integrated video/HMI systems offer advantages, she says.
Diepenbroek notes that a more traditional approach of providing video on a separate system may require a separate log-in and a different set of controls for an operator to learn. By contrast, the Honeywell DVM system integrates video into the same custom display that the operator is already familiar with, and the video is provided only when needed, she says. Operators can control the size and location of the video, so “it integrates neatly without overpowering the operator.”
Among other features, the DVM system associates small video clips as part of alarm summaries so that video recordings of an event are shown only when the operator clicks on them, Diepenbroek adds. DVM improves operators’ effectiveness by allowing them to easily toggle between process information and video streams, or see video and process data combined into a single view, she says.
Rubin, the Longwatch CEO, also touts the integrated approach. “I think that five years from now, 80 percent of HMI will have integrated video, because it provides fast information unambiguously, it doesn’t require any native language support, and it doesn’t need a whole lot of training for the operator to see what’s going on and make a conclusion,” he declares.
Founded in 2004 by a team that included engineers who worked previously at pioneering HMI supplier Intellution, Longwatch initially focused on the water treatment market. The company started out by developing technology for transmitting low-resolution video surveillance images from remote water industry transfer stations over low-bandwidth, 9,600-baud (bits per second) phone lines, Rubin says. That remote video expertise remains a unique advantage for the company today, he contends. But the firm has also lately embraced local, high-bandwidth industrial networking as well, and has developed some additional technologies that Rubin says speak to the company’s manufacturing background.
One came with the release of Version 5.1 of the Longwatch Video Surveillance System on April 17. Known as the Console Recorder Platform, the system monitors what operators are watching on HMI displays and records their keystroke actions, so that a video playback reveals what operators saw on the screen during an “event” and what they did about it.
The Console Recorder can serve as a training tool for new operators, and also helps with troubleshooting and root-cause analysis, says Rubin, particularly when it is used in conjunction with the Longwatch Video Historian Platform. This tool, introduced with an earlier 5.0 release, automatically links and synchronizes historical trend information and stored video from multiple cameras in the field or process, enabling users to actually see what happened when various trend conditions occurred.
Bright future
While the Video Historian and Console Recorder technologies are relatively new, Rubin says that Longwatch currently has about 150 installations in the field using its Surveillance technology that can integrate video feeds with HMI/SCADA. These encompass both lower bandwidth remote video installations as well as local high-speed network applications.
Not surprisingly, Rubin foresees a bright future for video integration in the industrial environment. “I did kind of a back-of-the-envelope analysis,” he reveals. “And an extremely conservative [market] estimate that I came up with for this technology was in the neighborhood of about a half billion dollars, just in the United States, over the next five years.”
On The Web: Two kids with a rifle jump a security gate and wander around for a while inside a facility before being arrested. An intruder attempts to tear down a security camera, and shows his face in the process. Both are among industrial security videos that you can watch, provided courtesy of Longwatch Inc. To view the videos,
see http://bit.ly/securityvideos.
Subscribe to Automation World's RSS Feeds for Feature Articles
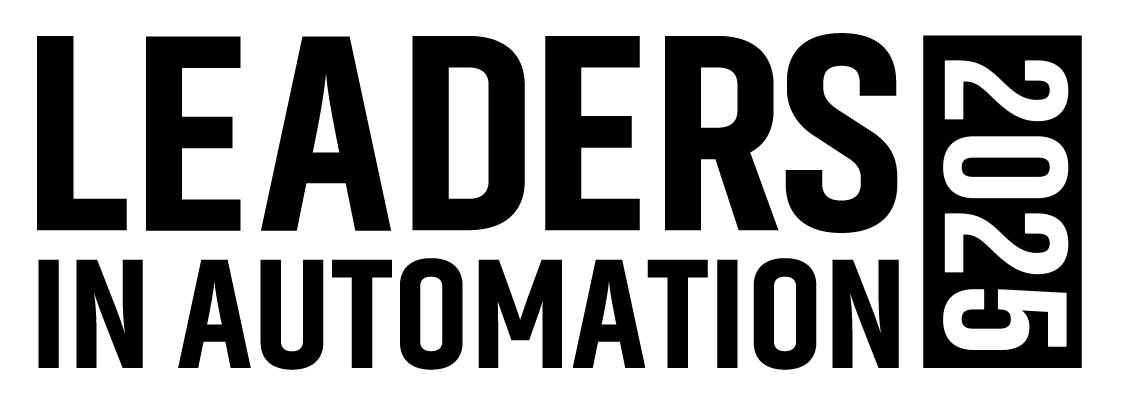
Leaders relevant to this article: