Is there a manufacturing work sequence that does not, somewhere along the line, need to monitor levels of something? Certainly not in the process world. Perhaps there is in discrete manufacturing, but even here, cutting fluids, plastic resin pellets, paint reservoirs, pickling tanks and the like usually require reliable information about the levels of whatever is in them.No wonder, then, that the technology is everywhere and in one way or another known by everyone. To be honest, there are few surprises. Over thousands of years, humankind—at least those organizing, rationalizing members of the race with an interest in ensuring a ready supply of desired goods—has evolved from simply looking down into a well or depression for drinking water, to sending a kid with a dipstick, to eyeing a sight-glass, to reading a meter, to automatically feeding levels information into control systems.The list of technologies behind level sensing is a long one. Open tanks and clear glass vessels need only an eyeball (though admittedly, intelligent eyeball carriers are becoming scarce). But once tops are closed and walls are made from opaque plastics or metals, “seeing” into tanks and vessels takes all sorts of forms. Like mechanized eyes, some work on spectra of electromagnetic radiation, some with visible light (converging light beams), some outside the visible range: radar, LED (light-emitting diode) pulse, laser. Mechanical ears listen to ultrasound. Pressure sensors weigh containment vessels like giant scales, or they measure gas pressure. Finally, magnet- or rheostat-based arms and sliders ride on top of liquids.Over the last three decades, just as with all things electronic, the engineering behind each of the types of sensors has seen continuous improvements in capability, mainly in the accuracy and granularity of measurement, combined with package and cost reduction.“There are many technologies for reporting levels,” says Tony Udelhoven, director, sensor division, for components vendor Turck Inc., in Plymouth, Minn., “because needs are application-specific and ever-changing. Are you measuring oil? Wheat? Resin pellets? You could use capacitive sensors for all of these, but there can be significant differences in strategies for selecting the sensor package or sub-type, and for sensor placement and tuning, depending on site and application specifics.”There is less design revolution going on than steady evolution. “One thing that’s evolved is the level of automation,” Udelhoven continues. “And that has affected sensor environments, where the level of electrical noise from automation devices has increased greatly. Capacitive sensors depend on electrical forces, some when capacitance is interrupted, some when capacitance increases, and automation equipment can be electrically noisy. So we came up with our BCF series, which incorporates new types of filters—the principle involves a fixed oscillator frequency combined with a rectifier filter—as well as improved circuits that are, as much as possible, immune to noise.”Comparison of Turck BCF product performance against a couple of Conformité Européenne (CE) mark limits proves the point. The CE product standard IEC 1000-4-2/EN 61000-4-2 for immunity to electrostatic discharges (ESD) is 4 kilovolts (kV) direct contact, 8 kV airborne; BCF products withstand 8 kV direct, 30 kV airborne. CE immunity to radiated electromagnetic fields (radio frequency interference, RFI) is 3 volts per meter (V/M) at 80-1000 megahertz (MHz); BCF products are immune up to 15 V/M at those frequencies. “Conventional capacitive sensor designs find it hard to pass any of the CE standards, let alone exceed them,” Udelhoven says.Almost regardless of technology type, physics has a way of posing challenges. Temperature can affect electronics, to the point of barring the way—as Udelhoven says, “I’m not aware of a good technology for level sensing of hot glue at 400 degrees Fahrenheit.” But even far more moderate temperature can combine with pressure to induce variability.This is especially true with differential pressure (DP) sensors, which compare internal and external pressure to gauge fill levels in closed tanks. In an application note, Plano, Texas-based automation supplier Invensys Operations Management (IOM) points out, “DP transmitters are low cost, easy to install, and useable with a wide variety of liquids, but in certain applications, accuracy can be limited.”As Invensys points out, conventional DP meters do not, for example, account for density variations caused by temperature changes, which have a significant impact on levels. Users often assume density is constant, but in measurement environments in which temperatures rise and fall, density can change significantly, varying by as much as 30 percent.One solution is to install three devices, one measuring absolute pressure, one measuring differential pressure and one measuring temperature. Obvious problems are installation complexity and challenges around integrating the devices into a coherent sensing functionality.To simplify the problem, IOM’s Foxboro brand IMV31 density-compensated level transmitter incorporates all three devices in a single package. In addition to smoothing installation (and reducing the number of points of penetration in a given liquid flow), it offers a claimed +/-0.3 percent margin of error. In applications with wide excursions of pressure or temperature, or both, the margin of error for conventional DP sensors can range from +/-3 percent to 30 percent or more—a clear case of less is more.If the technology of measurement changes slowly, the means and modes for delivering measurements to their destinations (whether that be controller, control room, automation engineer or even a trainee with a clipboard) are showing far more rapid development—or at least, change. Talk of radios and Ethernet have supplanted debates around industrial protocols, and the Internet has largely infiltrated even the most conservative of industrial sites.Products have quickly adopted Ethernet and Web protocols. Example in point: Automation Products Group Inc. (APG), Logan, Utah, last year launched its LOE series of Web-enabled ultrasonic level sensors, so thoroughly integrated into Ethernet that it can receive its power over the Ethernet cable. It essentially contains its own Web server, broadcasting levels data to any computer with Internet access, via a built-in, password-protected Web page. The LOE-2126 provides a detection range in tanks of liquids or solids of one to 25 feet (0.3 to 7.6 meters); the LOE-3136, 1.5 to 40 feet (0.46 to 12.2 meters); and the LOE-6126, 4 to 180 inches (0.1 to 4.6 meters). “Collection fleets and remote tanks are especially suited to the LOE family,” says Ramiro Garcia, APG regional sales manager. “Take, for example, waste-oil tanks. The combination of growing economic rewards for recycling and tough economic times has resulted in increasing theft from remotely sited waste-oil storage tanks. Remote level sensors can alarm if a tank is draining at unplanned times—say, midnight—and they can alert distribution personnel to alter pick-up routes, rather than sending trucks to empty tanks.”APG cites savings over conventional remote sensing alternatives. “Traditional telemetry normally transmits data over licensed-band radio,” Garcia says, “racking up license fees and maintenance expenses. Private network monitoring requires payment for cellular hook-up. Having Web access to the data bypasses these costs.” APG offers a low-cost, adjunct data historian service through a hosting service, which currently costs between $37 and $100 per year.For remote monitoring and areas in which the cost of new wiring is high, wireless level sensing products are finding their way to market. One example is the UK-based Deeter Group’s battery-powered wireless liquid sensor, LVCS-RF, which connects to a Deeter base station over an IEEE 802.15.4 wireless network.The LVCS-RF circuitry is housed in an IP65 rated die-cast aluminum head with an external antenna. An optional 3-meter (m) extension lead and bracket are available for mounting the antenna, allowing placement for data transmission in many otherwise wireless-resistant locations. The sensor circuit is fitted inside a 316L stainless steel tube attached to the head, with a 55 millimeter (mm) magnetic ball-float. Standard sensing lengths are 250 mm, 500 mm, 750 mm and 1 m. The unit is powered by a single 3.6-volt lithium thionyl chloride battery with a claimed life up to nine months, based on a transmission interval of 10 seconds and an uninterrupted wireless link to the base station.As well, Austin, Texas-based automation vendor Emerson Process Management announced in January of this year that its radar-based Rosemount TankRadarRex and Pro families are available in wireless configurations. The technology employed is WirelessHart, again on the Institute of Electrical and Electronics Engineers’ IEEE 802.15.4 standard. “Many tank storage facilities that would benefit from non-contact gauging have obsolete or nonexistent signal wiring from the tank storage area,” Emerson says. “Retrofit would be expensive and time consuming as the distance between storage tanks and the control room can be more than a kilometer, requiring extensive trenching and cabling. Emerson’s Smart Wireless data transmission enables cost-effective ways to gain new measurement points.”Despite the ongoing adoption of open standards-based products, not all wireless level sensing is standardized. Minneapolis supplier Banner Engineering Corp. uses its own, proprietary wireless network for its ultrasonic level sensor series, the Ultrasonic T30UF with serial interface, and the U-Gage QT50U long-range ultrasonic sensor. “We tuned these to work with very low power consumption,” says Mark Lampert, food and beverage business development manager for Banner Engineering. “Our protocol uses spread-spectrum multi-hopping to avoid other wireless in the area. We can provide a battery-powered ultrasound wireless node that will broadcast for more than two years.”Banner opted for proprietary radio technology primarily for full control over data quality and reliable connectivity. “Food and beverage has a full range of special needs,” Lampert explains. “High and low pressure washdown, aggressive hygiene cleaning chemicals, food acids—all of these are part of the picture. We even have our share of Class 1 Div 1 [Class 1, Division 1 within the U.S. National Electrical Code] needs, including explosion proofing around grain elevators. We wanted to make sure that the technologies packaged for these needs were tightly integrated with the embedded radio equipment.”While it is hard to say whether more wireless installations have occurred in magazines than in industry—wireless is found everywhere in both—one thing is certain: there are still many wired installations.“Turck doesn’t offer wireless sensors,” says Turck’s Udelhoven. “We concentrate on [discrete] factory automation and OEM (original equipment manufacturer) applications, and don’t see the type of far-flung tank farms or acres-wide flow systems you find in process manufacturing. For our relatively compact applications, compact geographically, wired sensors are more reliable.”Many of Turck’s offerings go into customized systems. “That brings us in contact with many very different needs,” Udelhoven explains. “And because packaging and accuracy are generally specified by end-users, we work in the broadest possible range of costs, from a few dollars to hundreds of dollars per unit. We’ve looked at wireless, but so far, it doesn’t make sense for us—we don’t experience the demand.”Turck’s range of products is as broad as their application. Level sensing technologies include capacitive, ultrasonic (in its Levelprox family), linear displacement transducers that employ magnetic floats in magnetorestrictive probes, and conductive level probes and controllers.In the final analysis, level sensing is all over the place—both in terms of application variety and in terms of nearly universal usage throughout manufacturing. Whether simple or complex, the technology behind level sensors and the engineering applied to their installation and integration into factory systems, all contribute quite literally to the global flow of products.
Subscribe to Automation World's RSS Feeds for Feature Articles
Sponsored Recommendations
Sponsored Recommendations
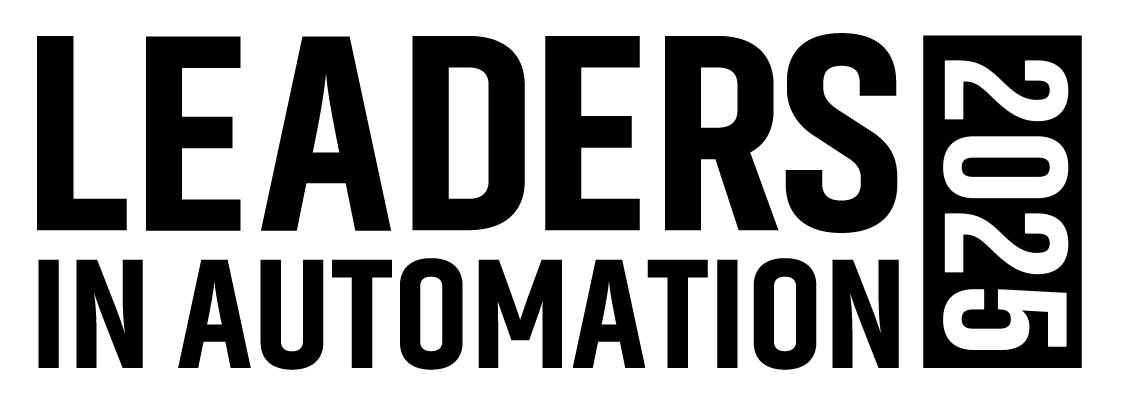
Leaders relevant to this article: