It’s been called the new world of motion control—namely, the integration of motion control with discrete control and perhaps even safety in a single controller and a single control program. Consumers, whether of phones or factory automation, are rightly wary of the claims of those with something to sell, who sometimes seem to find a new world around every corner. Still, there’s a compelling case to be made, one which seems to align with the general thrust of automation technology.
“We believe this is part of the natural evolution of plant floor technology,” says Brian Deal, packaging manager for controls supplier Schneider Electric, Palatine, Ill. He cites, as one of the prime movers in this evolution: the ongoing growth in computing power.
“Today, we are able to provide the controller with a great deal of information from the drive, and from the motor itself. For instance, we load an electronic nameplate into the encoder so that whenever you wire up and power up a system, you get information about that motor, its model number and serial number and so forth, back at the controller level.”
The potential advantages of this integrated, information-rich motion environment are many. Mike Burrows, director, market development for Rockwell Automation Inc., the Milwaukee-based automation vendor, supplies another one. “Once you are able to perform the functions of time synchronization and high-speed motion control in the same box and the same program with your discrete control and your safety control, you get much better interaction between the pieces of your overall system.”
He stresses that integration simplifies. This is not only in terms of programming and engineering time, but physically as well. “You reduce the number of components, wiring, and communication interfaces and gain a smaller control cabinet.” It can also aid in machine and packaging-line optimization. Consider motor selection. This can be automated, and made more precise, through evaluation routines resident on the controller. Users can quickly pinpoint the right combination of performance and energy efficiency for their range of applications, while assuring that they are not buying larger and more expensive motors than they really need.Electronic line shafting
All of this translates into cost savings. Perhaps even more importantly, it promotes flexibility.
Computer-aided advances in motion control technology have been aiding the packaging industry’s market-driven quest for greater flexibility for some time. The move away from mechanical line shafting to electronic line shafting is a case in point.
“Electronic line shafting is becoming much more common,” notes Rob Rawlyk, applications manager for Beckhoff Automation LLC, a Burnsville, Minn., automation supplier. “The big reason, of course, is flexibility.” By replacing cam plates and other mechanical line-shafting components with controller-driven electronic functionality, changeover times can often be reduced from hours to minutes. “Our customers are saying the batch sizes of the products they make are becoming smaller and smaller, so this sort of flexibility is becoming increasingly desirable.”
David Kirklen, packaging industry business developer for vendor Siemens Industry Inc., Alpharetta, Ga., concurs. “We’ve been seeing a lot of interest by packaging companies whose machines demand greater flexibility, and electronic line shafting is a part of that. Companies don’t want to have to go through a huge mechanical reengineering effort to be able to produce a new product.” He notes that electronic line shafting has other benefits as well. “By reducing the number of mechanical couplings and linkages in a packaging machine, you are reducing your maintenance requirements as well. In addition, it allows you to reduce the machine’s size.”
Good…but not good enough, maintains Schneider’s Deal, whose company is pushing its own take on the electronic line-shafting concept. The company calls it Intelligent Line Shafting (ILS). “ELS (electronic line shafting) has been enhancing packaging machine performance by replacing mechanical line shafts. However, because most machines run off the virtual master axis, the speed of the machine is fixed. This can limit the performance of a machine.”
He observes that by increasing the virtual master’s velocity, all cycle times are reduced—motor speeds, accelerations and decelerations—for all axes equally. This limits the performance of the system to the “weakest link,” even if the remaining axes are capable of higher performance. “To put this in real-life terms, it’s like telling a NASCAR driver that he has to drive the track at the same speed all the way around. The driver would be limited by the maximum speed of the toughest corner on the track.”
One additional drawback of ELS, Deal continues, is that if critical motion profiles during a machine cycle increase mechanical wear and tear, thereby impacting maintenance requirements and, potentially, packaging quality, often, the only workaround is to reduce cycle rates and machine throughput.
With ILS, on the other hand, the master axis receives feedback from each of the axes and calculates whether an individual axis is about to exceed its maximum speed or acceleration during the next machine cycle. During the critical phases of the motion profile, the ILS-enabled master will slow that axis down to avoid exceeding the set limit. Outside the critical motion phases, the virtual master may even increase the axis’ speed to a value significantly above the previous set speed to compensate for the slower segment. Thus, with ILS, the virtual master adjusts the motion profiles of individual axes to optimize overall performance. “To return to the NASCAR example, ILS allows the machine to slow down around the toughest corners of the racetrack and speed up in the straightaways.”
Deal claims that changing the virtual master from a constant to a variable speed can result in throughput increases of up to 30 percent with no changes other than in software. Additionally, he believes this approach can be used to lower power consumption as well.Integrated control
It’s important to note that neither ELS nor its ILS variant require integrated control, they simply require a powerful controller. “Some of the old PLCs (programmable logic controllers) may not have the processing horsepower to perform these calculations,” says Deal. “I think some of the PACs (programmable automation controllers) on the market would have some trouble performing these calculations as well, but this is only going to push the market to bring out more intelligent control systems.”
Similarly, any increase in the popularity of an ILS-type approach would seem to push the market toward greater adoption of integrated motion control. The logic of the case goes like this: If a powerful controller is required to take advantage of electronically variable axes, why be content with a powerful motion controller? Why not opt for a powerful multidisciplinary controller that can perform these functions, plus other tasks, such as simulation? A powerful integrated control can give engineers access to simulation programs that can quickly test complex motion routines. It also helps programmers who may lack specialized motion-control expertise to create or change motion routines. The result in both cases is shorter response times to product changes.
Relatedly, today’s powerful controllers can, in some cases, provide users with access to analysis tools linked to both the control program and a 3D computer-aided design (CAD) environment. “Based on the application, what size motor do I need to move this product?” asks Leo Petrokonis, Rockwell’s business development manager, packaging industry. “What kind of gearbox will I need? What’s my ratio?”
He notes that analysis tools can allow users to answer those questions, then, in an iterative process, take that information back into the 3D CAD package and experiment. “What if I change the metal from steel to aluminum, or hollow out a certain section of the load? Could I then reduce the gearbox? Could I reduce the motor size? How much power would this save me? What’s my cost? I can also optimize my move profile data and then pull all that information back into my controller, so integrating the design function into the controller helps you optimize your machine.”Betting on information
Moving information between different parts of the enterprise is, of course, key to modern manufacturing. There’s nothing new about that; it’s been a fact of life for a number of years. What is relatively new, however, is the fact that motion control is now a part of this scenario. Increasingly, the device-level information of the motion control world is being captured by other functions and levels of the enterprise. It’s a trend that will only accelerate.
The scalability of this information will bring tremendous benefits in terms of machine and line efficiency, remote monitoring and maintenance, and cost reduction, says Petrokonis. And what do you need to make this happen? “Ethernet, both above and below the controller. I think everybody would agree that it is happening above the controller level, but you need it everywhere, and you need the same version of Ethernet below the controller connecting to your servo drives and your I/O (input/output).”
And which version should that be? Rockwell has thrown its weight behind EtherNet/IP. Beckhoff supports EtherCat. Siemens supports the Ethernet-compatible protocol Profinet. Other companies support Modbus TCP or Ethernet PowerLink. Which version will come out on top? One could speculate that EtherNet/IP seems to have the inside track with more than 250 automation vendors already supplying product for it, but no one really knows. In addition, these protocols already have a great deal of compatibility and that could very well increase in the future, so picking winners and losers in the Ethernet sweepstakes may not be as relevant as it might seem.
Finally, Schneider’s Brian Deal adds a key word to the discussion: convergence. Machine controllers have typically dealt with three or more different networks—one for motion, one for automation devices and general I/O, one for communication with other plant systems and perhaps another for safety. “With the advent of higher-speed networks, you are going to see a single network on a machine with motion, I/O and safety all running on it.”
Running safety control on a single network with motion and other functions remains a controversial idea. But just a few years ago, it seemed an outlandish idea.
“Certainly, the protocols will be layered so that safety will have the highest priority,” he continues, “but all will be running at very high speeds, getting more information back to the controller, which will then be available for use at the operations level.”
Predicting, as noted above, is a shaky business, but Deal’s vision of motion control information becoming more available for use at the operations level seems right on the money. And you can take that to the bank.Related Sidebar - Leveraging Motion TechnologiesTo read the article accompanying this story, go towww.automationworld.com/feature-7180.
Subscribe to Automation World's RSS Feeds for Feature Articles
Companies in this Article
Companies in this Article
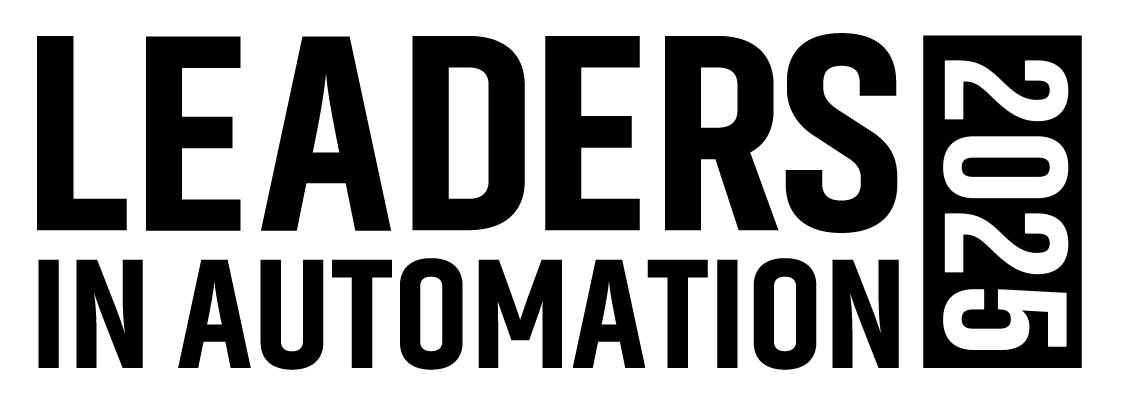
Leaders relevant to this article: