This kind of information is the lifeblood of almost all the systems that run manufacturing processes—manufacturing execution, supply chain management, demand management, maintenance, and even safety and security systems are all reliant on detailed operational data.There are numerous challenges associated with this, starting with the integral problem of getting access to the required data, most of which is traditionally buried in silos. The sheer volume of valuable data an enterprise produces can be overwhelming, so organizing and managing that data presents its own challenges. However, the companies that have started down the path to overcoming these issues have a better grip on their operations, and are better equipped to ride out the recession and better positioned to grow as the economy bounces back.“Now, we are seeing people really trying to set themselves up for the recovery,” says Vivek Bapat, a vice president for Walldorf, Germany-based enterprise resource planning (ERP) supplier SAP AG, although he confesses that he is hesitant to use the word “recovery.” Different companies see that recovery through different lenses, he explains, so while the past 12 to 16 months have been very difficult, and companies are being challenged to demonstrate a route to growth, they still have to keep on top of their costs. “They can’t just focus on expanding revenue the way they might have in the past, and that’s where the complexity lies.”AMR Research Inc. analyst Simon Jacobson, in Boston, agrees. “All participants in today’s multi-tier product supply networks need real-time information in order to profitably capitalize on market opportunities and mitigate risk. Demand volatility isn’t ceasing, and agility is needed. Whether it’s wholly owned or contracted manufacturing, visibility from site to enterprise is required to make the right tradeoffs.”But before considering any kind of optimization project, you need to know what you are optimizing, and that means having better intelligence about your operation. Increased visibilityDow Corning Corp. was an early adopter of this kind of enterprise manufacturing intelligence (EMI). According to Keith Carey, an associate architecture consultant with the Midland, Mich.-based specialty chemicals giant, who worked on the project, the company was looking for a number of strategic outcomes, starting with gaining better visibility into data and the analytics required to make sense of it, and then running through to streamlined production and delivery on a global basis—all of which really boiled down to having the information available to make better decisions. “We had limited visibility to our product quality, manufacturing processes and business systems,” he says.Dow Corning deployed SAP’s Manufacturing Integration and Intelligence (MII) package in 2007 and followed that up with xApp Manufacturing Integration and Intelligence (xMII) composite application development platform. Essentially, xApp is a module that links manufacturing operations with the ERP system to get access to process, business, and quality data throughout Dow Corning’s global value chain. That intelligence is then rolled up into a dashboard that helps inform decisions at all levels of the organization.The impact for Dow Corning was substantial. Customer inquiry response time went from as long as seven days down to one hour, greatly improving customer satisfaction, while millions of dollars were saved in reduced scrap material costs. Carey also credits access to more accurate, timely information for enhanced decision-making and greater employee productivity through the reduction or elimination of non-value adding activities. Dow Corning is merely one example of a growing trend in manufacturing. When Raleigh, N.C.-based Pepsi Bottling Ventures went looking for better insight into downtime at its Garner, N.C., plant, it deployed a solution from Wonderware, the Lake Forest, Calif.-based unit of automation supplier Invensys Operations Management. The Wonderware solution replaced a 100 percent manual, paper-based system that had usually generated more questions than it answered. Management wanted to eliminate guesswork and assumptions and improve overall equipment effectiveness (OEE)—such as filler throughput. In other words, they wanted to become leaner. “We have to make the right decisions every day because it has a huge impact on our bottom line,” says Scott Jamison, vice president of engineering. As with Dow Corning, the impact of having greater visibility into key operations was dramatic. The plant was able to add a fifth production line and increase its throughput to the point that it now produces more than 30 million cases of 500 different Pepsi products each year. Additionally, with better process data readily available, staffers are now able to make faster changeovers—no small feat considering the range of products involved.Get controlWhen Ford Motor Co., Dearborn, Mich., set out to get better control over its parts supply and logistics, it decided to restructure its warehousing, going from a handful of very large, centralized facilities to 26 smaller ones located closer to the plants. The primary concern for the automaker was that such a move would damage its labor efficiencies. But Ford avoided those problems when it deployed an EMI system from SAP, which led to notable results. Says Raymond Damerow, director, parts supply and logistics, Ford Europe, “We were able to gain real-time insight into global service parts inventory and customer orders, and take action based on changing business dynamics and events, resulting in reduced inventory and increased parts sales.” There really isn’t anything new to the concepts surrounding the need to break through silo walls and mine and use the data buried there. In fact, AMR analyst Alison Smith first introduced the idea of EMI in 2003 in a report called “Enterprise Manufacturing Intelligence Helps Global Manufacturers Raise Performance and Responsiveness.” At that time, EMI was a gradually coalescing concept based on a then-emerging set of applications, capabilities and architectures that provided manufacturers with an aggregate view of production performance across the breadth of the organization in business terms rather than the usual speeds, feeds, and counts of traditional production performance reporting.By focusing on strategic, business-related performance metrics, executives gained meaningful insights within the context of greater supply chain and business performance. “Demand-driven manufacturers seeking to enhance the responsiveness and profitability of their businesses need insights that allow them to decide when and where to make a product, as well as which products to outsource, based on margins, spot market commodity prices, logistics tradeoffs, and contract penalties,” Smith wrote in 2008, when she revisited the subject to outline a framework that AMR’s Jacobson still recommends that companies use to evaluate their EMI architectures.According to Smith, an EMI solution should deliver a set of five core capabilities:• Aggregate real-time and historical data from a variety of sources, including historians, manufacturing execution system (MES) operational databases, laboratory information management systems, the automation equipment and relational database systems. • Contextualize that data in terms of its strategic importance to the organization. What does it mean in relation to other key factors, such as time, yield and product quality? • Analyze the data, turning it into usable performance intelligence (key performance indicators, or KPIs) by applying business rules. • Visualize the KPIs in an intuitive, graphical way. • Propagate relevant performance information to the appropriate business-level systems (such as enterprise asset management, supply chain planning, sales and operations planning, product lifecycle management, resource planning or supplier management) as needed, or by exception.Extended capabilities that users should look for in their EMI architecture include data mining (which relies on sophisticated algorithms to go beyond simple analysis to uncover trends within the data), process modeling and simulation/scenario analysis.Suppliers scramblingIn Smith’s 2003 report, only a handful of vendors were identified as working in the space, and most were there for tangential reasons, not because they specifically focused on EMI. Today, that has changed. According to AMR, more and more manufacturers are moving in this direction, and vendors are scrambling to help them on their way.SAP has made significant announcements over the past year, but the ERP giant is far from alone. Invensys Operations Management (IOM) and CDC are other examples of vendors that have made major moves to deliver solutions that close the gap between the enterprise and the production floor.Both Plano, Tex.-based IOM and Atlanta, Ga.-based CDC Software made major acquisitions to expand the scope of their offerings—just two vendors to do so. IOM acquired business process management vendor Skelta Software, in Bangalore, India, extended its partnership with Microsoft Business Solutions to continue to marry its operations pieces with a broad ERP solution, and released its EMI platform, Wonderware Intelligence. Meanwhile, CDC Software acquired Activplant, London, Ontario, Canada, an EMI vendor focused specifically on the automotive industry with a respectable installed base and strong EMI capabilities.“We have a lot of companies that have struggled with data collection and reporting, and even with how to communicate. A lot of them are looking for ways to do this, to provide real-time monitoring and find ways to reduce these costs,” says David Cahn, vice president, Technology Strategy, CDC Software.“It’s not just monitoring equipment,” he adds. “The idea is that as you move forward with analysis and dashboards, you get to the point where taking action is unavoidable.” If you know how you want to behave, then the system can alert you when you get out of those set parameters very quickly, triggering a corrective response.Again, the company claims some eye-opening results. “We see companies achieving 25 percent improvement in output per shift, reduced outsourcing and overtime costs. So even though it starts with info at the shop floor level, we are seeing the benefits of the communications extending outward throughout the enterprise. Everyone is on the same page.”“With the downturn, what we saw was companies reviewing the state of their business and looking at how they could put in systems and products that would help them optimize their existing assets,” says Maryanne Steidinger, director of product marketing for IOM, adding that productivity improvement starts with getting access to the information from the plant floor.“[EMI] looks at all of the systems in the enterprise that create data,” she adds. “That could be real-time data, or time- and event-based from a data historian, or it could be track-and-trace data from MES or material consumption data from ERP, and it provides an overlay and a performance dashboard that will give you advanced warning of systems or processes or procedures that are falling out of regulated bounds. Then you can do root cause analysis and determine what is happening, why and how you can fix it. When you talk about connecting the enterprise, then this is really what you are talking about. [EMI] can connect to anything that has data. You can drill down all the way to the PLC (programmable logic controller) layer.” According to AMR’s Jacobson, the bottom line is clear. “Manufacturing operations must no longer be the constraint that causes sluggish supply network responsiveness. To remain competitive, companies need real-time visibility into manufacturing performance and resources. Leading organizations are becoming smarter in how they design manufacturing architectures that create common ways to visualize, analyze, and contextualize performance across multiple manufacturing lines and sites.
Subscribe to Automation World's RSS Feeds for Feature Articles
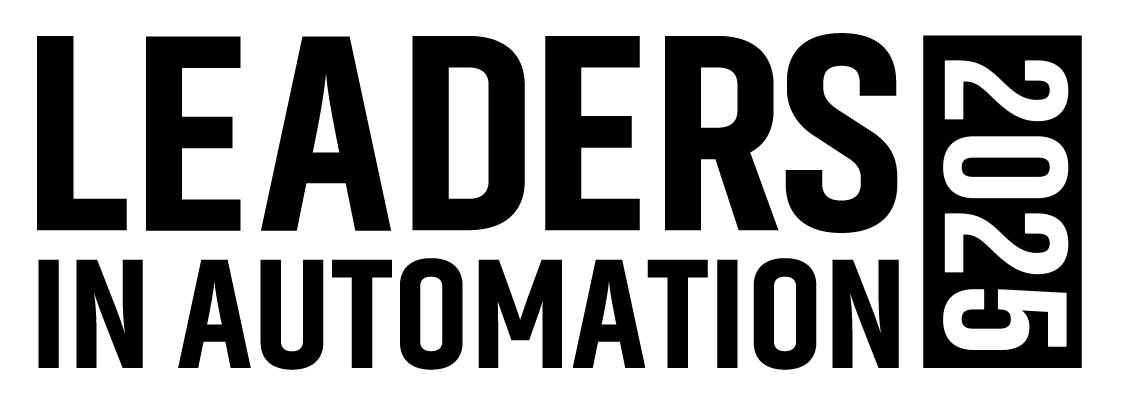
Leaders relevant to this article: