If you’re an automation professional working in the process industries, you may or may not be familiar with the acronym CPAS. But even if you don’t know that CPAS stands for Collaborative Process Automation System—a term coined at ARC Advisory Group Inc., Dedham, Mass., in 2002—it’s likely that you are familiar with some, if not all, of its precepts.Indeed, while CPAS does not describe a particular commercially available system, it does provide a template or a vision for the use of technology that has arguably had a big impact on the direction of process control systems architectures during much of the last decade. Engineers at companies including Dow Chemical and DuPont, for example, confirm that they use language lifted directly from CPAS documents when crafting requests for proposals (RFPs). And control systems vendors often claim compliance to CPAS principles in the design of their product architectures.The original 2002 CPAS study, about 185 pages long, is the highest-selling ARC report in history, reports Dave Woll, ARC vice president, consulting services, and the principal author of the study. “I’ve done a number of presentations on the [CPAS] subject at ARC Forums, and I’ve gotten a lot of contracts as a result of it to help user clients develop their automation strategies around it,” Woll says.Benchmarking toolThe CPAS concept was born shortly after the turn of the century at the request of several large end-users in the hydrocarbon processing industry, who retained ARC to help them achieve a better understanding of the latest process automation systems. “It was meant to be ARC’s view of how current automation is evolving, so users could use it as a benchmark when they were looking at systems,” Woll explains. And while some applications have grown up around it over the years, CPAS “core principles and the core technology are still exactly the same,” he relates.Woll’s co-authors on the original CPAS report were Dick Hill, vice president and general manager for ARC manufacturing services, and Dick Caro, today an independent consultant. Woll today continues to work with both end-users and vendors in the pursuit and understanding of CPAS. And he is also planning to extend the concept with the release of a new market study covering CPAS 2.0, due out in the next few weeks.CPAS is a big topic, covering everything from the sensors and actuators on a plant floor all the way up to the interfaces that connect to enterprise resource planning (ERP) systems. One recent look at the concept comes in a book titled “Collaborative Process Automation Systems,” written by Martin Hollender and others, and published in 2009 by the International Society of Automation (ISA). Hollender, principal scientist, ABB Corporate Research Center, Ladenburg, Germany, tells Automation World that he decided to put together the book, more than 400 pages long, when he was teaching a class on control systems and noticed that there were few good books available on the subject. One basis for CPAS, according to Hollender, is the fact that today’s distributed control systems (DCS) have evolved beyond simply process control. Through standards-based programming, integration and connectivity, control systems today are able to facilitate a wealth of further functions that allow the safe, secure and efficient operation of an automated plant and deliver significant benefits to plant owners and operators.“A key aspect of CPAS is the ability to present information in context to the right people at the right time from any point within the system, to include a single, unified environment for the presentation of information to the operator,” Hollender writes in his book’s introduction. “In addition, a key strength of a CPAS is the ability to extend its reach beyond the traditional capabilities of the DCS to include functions such as production management, safety and production-critical control, advanced control, information management, smart instrumentation, smart drives and motor control centers, asset management, and documentation management capabilities.”Beyond controlThat’s in line with the view of automation taken at The Dow Chemical Co., in Midland, Mich. “In Dow’s parlance, we use automation to refer to a broader term than control,” says Eric Cosman, a Dow engineering solutions information technology (IT) consultant who was an early CPAS adherent. “Control is basic regulatory control, loop control, that sort of thing. But when you start looking at automating all facets of the plant, from start-up to shutdown, running, and all the rest, we use the broader term. And in our terminology, automation includes what the industry would call the MES (manufacturing execution system) layer,” Cosman notes.“I think CPAS really articulates the basic principles and some of the salient characteristics of what a really broadly competent control system should be able to accomplish,” Cosman observes. As such, he says, CPAS can provide a kind of strategy document that process manufacturers can use in determining how far they want to go—and can afford to go—in pursuit of a comprehensive, state-of-the-art automation strategy.Woll, for his part, doesn’t subscribe to the concept of an MES as a separate subsystem, but rather views CPAS as a single automation system with different applications. The only two systems in a process plant are the business system and the automation system, he declares. “Primarily, CPAS should be considered an environment that enables applications including Process Control, Advanced Process Control, and Operations Management complemented by human empowerment applications such as decision support and advanced analytics,” Woll says in a section written for Hollender’s book. A variety of technologies and standards have evolved and come together to make a CPAS possible. Standards including ISA88 and ISA95 provide a common reference model for CPAS, while the International Electrotechnical Commission’s IEC 61131-3 standard is the basis for programming and configuration. The development of the Internet and standard networking technologies such as Ethernet and TCP/IP (transmission control protocol/Internet protocol) are key, enabling the standards-based exchange of information. And while CPAS encompasses only a plant’s automation system, the common logical backbone provided by Ethernet TCP/IP, along with other elements of a common information infrastructure, enables it to communicate natively with the plant’s business system as well.The latter characteristic is key to Dow Chemical’s Cosman. “One of the things in my mind that separates a basic, plain old process control system from a more comprehensive automation system is the degree to which [the latter] is integrated into your business process,” he says. Having that integration in place is fundamental, Cosman notes, so that business decisions can flow seamlessly to the manufacturing operation level, while operational results can be pulled all the way back up to the business level.Automation motherhoodIf CPAS principles sound to some experienced automation professionals like obvious goals, and perhaps a bit akin to proclamations about the goodness of motherhood, Woll doesn’t necessarily disagree. “It’s not rocket science,” he says. All of the technologies necessary to achieve the CPAS vision are available today, he notes. But to this date, he adds, “a lot of it is still not done.”Consider the concept that Woll says is fundamental to CPAS, that of Global Data Access (GDA). GDA makes possible what Woll refers to as “the five anys”—namely, the ability to access “any information from anywhere to anywhere at any time for any valid purpose.” It’s a universal desire among process automation users. “Whenever I do a workshop and I ask people, ‘What are the things that you need?’ everybody says, ‘I need to get any information any time I need it,’ and that’s the five anys,” Woll observes. Despite that stated user desire, however—that all employees should be able to access the information they need to most effectively do their jobs—it’s a capability that is still not fully realized in most systems, Woll observes. One reason, he says, is that some process automation vendors still do not provide true object-based systems, which are a requirement for GDA. So-called “early-binding” systems provided by some vendors require a path to be written between the source of the data being accessed and the user of the data, Woll says. “Those paths can’t change, so you can’t satisfy the five anys,” he observes. By contrast, the use of “late-binding” technology employed in object-based systems from some suppliers can accommodate the five anys, Woll explains, because the sources of the data are linked dynamically to the user of the data during each process cycle.Long roadSupplier shortcomings are not the only reason that CPAS systems are still typically incomplete in the field. Another reason relates to challenges faced by asset owners. Ray Walker, a veteran enterprise architect at DuPont Co., the Wilmington, Del.-based chemicals and materials company, notes that DuPont has been building its automation information systems based on CPAS principles since the early 2000s. But the company has hundreds of plants worldwide, so “it’s not something that happens overnight,” says Walker, a recently retired, limited-service employee who has 37 years of service at DuPont.In general, process controls suppliers are increasingly providing solutions that include attributes of the CPAS framework, says Walker. “Most of our suppliers offer object-based solutions, configuration languages based on international standards, presentation layers built on ISA standards and Web-based interfaces based on international and de facto standards,” he observes. “So I would say that in general, there’s been a fair amount of convergence with some of those basic attributes.”But Walker notes too that users don’t always set up their systems to take full advantage of CPAS capabilities. For example, some suppliers now offer extensible equipment hierarchies out-of-the-box, which makes it easier to build systems that can achieve the five anys, Walker says. ”But if you don’t configure those systems to take advantage of that, you don’t get the benefit,” he observes.Likewise, to gain the full advantage of CPAS, users need to employ consistent naming conventions, such as International Organization for Standardization (ISO) equipment class definitions, for their data sources, Walker adds. “But you’ve got to have the discipline to go through that when you build solutions. And that takes effort,” he points out. “So I’d say the capability to satisfy the five anys is increasing, but the adoption by owner/operators is still lagging.”Collaborative decisionsThe DuPont veteran notes that as a template or road map for enterprise architects, CPAS does a very good job up through Level 3 of the ISA95 reference model, covering the plant floor through manufacturing operations and control. “For Level 4 enterprise systems, which CPAS really doesn’t address, we use other models and frameworks,” Walker says. But when the topic turns to the integration of automation systems with business systems, Walker is quick to praise the CPAS model for it focus on “the collaboration piece.” The ability to facilitate collaboration across the various roles in your enterprise is key, he says. “It enables you to get the information available to all of your best thinkers, so that they can make collaborative decisions in a way that is more effective and efficient than your competitors,” Walker notes.It’s been the focus on collaboration that has enabled DuPont to achieve the reality of interoperable distributed control systems around the world, he says, such that “someone can sit in corporate headquarters and view that information, along with enterprise information, all on the same screen.” And in the future, Walker adds, the addition of more analytics, consistent with the CPAS vision, will make that information even more valuable.Woll also emphasizes the bottom-line focus of CPAS. “We can talk about the technology—the five anys, common executable information and all the other stuff,” he says. “But the number-one objective for CPAS is to facilitate the delivery of applications that help end-users make money.”Among the primary benefits of end-user adoption of CPAS concepts, he lists: a more empowered plant staff relieved of manual tasks, making more correct decisions; higher asset utilization as a result of fewer unscheduled slowdowns and shutdowns; and higher performance as a result of accessing capacity that previously was obscured.What’s next?Woll has lately turned his attention to extending the CPAS vision, and ARC is expected to release a new market study covering “CPAS 2.0,” authored by Woll, in early July.Over the past 20 years, says Woll, advances in process automation have been incremental, with no “radical innovation” occurring, and end-users lately have been asking ARC what they should expect to see in the next generation of process automation. The CPAS 2.0 report is intended to answer that question. It will take a detailed look at a number of anticipated advances “that we would consider to be revolutionary in nature,” Woll says. He agreed to briefly discuss a few of those topics for this story.One topic relates to intelligent field devices. “We don’t believe that intelligent field devices are smart enough, and we’ve been waiting 20 years for them to become smarter,” Woll declares. Today, some 75 percent of field device downtime occurs because the user doesn’t consider the signal from the device to be reliable, according to Woll. Current intelligent field devices can report when they are healthy, and when they have failed. “But that’s not good enough,” says Woll. “We believe that smart field devices should be able to tell you quantitatively how the healthy they are, and provide a prediction of how long you’re going to be able to rely on their output.”There are a few products available today that meet this requirement using SEVA, or self-evaluating, technology, based on the British Standards Institution BS-7986 standard, says Woll. Users should watch for the emergence of more such intelligent devices in the future.For another CPAS 2.0 topic, Woll asks the question, “When will distributed control systems become truly distributed?” Current leading DCSs and the original CPAS don’t provide true distributed control, says Woll. Based on the IEC 61131-3 configuration standard, today’s major process control systems use a single model with distributed processing and shared services. The architecture is limited to a single domain with all resources operating in unison, and resources cannot act autonomously.The next generation of CPAS will be based on the IEC 61499 configuration and programming standard, which does not require shared services. This will provide a standardized basis to develop automation systems that are single model with distributed processes and independent services, says Woll. These true distributed processing systems will provide autonomy for different system resources and will support the new Foundation for Intelligent Physical Agents (FIPA) technology standard.With this technology, if an abnormality develops in the automation system, it will be able to autonomously reconfigure itself in real time to compensate for the abnormality, so that it continues to operate. “This means that we would have the potential for automation systems with zero downtime,” Woll points out. Similarly, these systems will be able to reconfigure to accommodate abnormalities detected in the assets they are controlling, providing more stability in the manufacturing assets themselves, he adds.Three stepsThe third and final CPAS 2.0 topic shared here by Woll involves the challenges faced by users who need to make changes or updates to systems without shutting down plants or processes. That procedure today is typically a two-step process that involves loading a new version of software into a redundant or back-up controller and then committing that software to the process. It’s an approach can be very risky, and “doesn’t make a lot of sense,” according to Woll.“We believe it should be a three-step process where you load it into the redundant controller, you exercise it to make sure that it operates predictably, and when you’re satisfied that it’s operating predictably, then you commit it to the process,” Woll says.In fact, according Cosman, Dow Chemical built this kind of capability into its proprietary control system as far back as the mid-1980s. And when Dow developed a collaborative relationship with ABB in 2001 to develop a commercial solution, the capability was on the list of features that Dow insisted upon, Cosman confirms. The result was the feature known as Load-Evaluate-Go that is available today as part of ABB’s System 800xA product line.Consequently, as Woll observes, the work on this kind of technology has been done. “It’s commercially available right now, so it’s not a technical challenge,” he asserts. “We believe that all of the automation companies should have this capability.”Related Sidebar - CPAS Guiding PrinciplesTo read the article accompanying this story, go towww.automationworld.com/feature-7142.
Subscribe to Automation World's RSS Feeds for Feature Articles
Companies in this Article
Companies in this Article
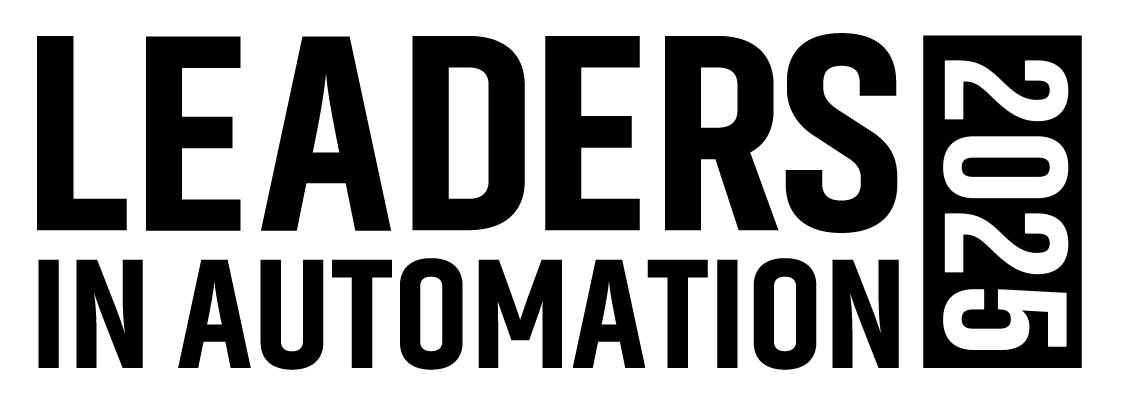
Leaders relevant to this article: