There are still far too many injuries and deaths in the industrial work place. During the writing of this article and just a half mile from the writer’s office, a forklift operator got down from the machine and walked in front of it, according to news reports in the “Sidney Daily News,” and was crushed by the moving vehicle, dying as a result of the injuries. This is sobering to the remaining workers. But, will this shock make them behave more safely?
How can a company get employees—from the shop floor to the executive suite—to see the risks in what they do and think safety at all times? This is not an easy task, but several leaders in manufacturing are accomplishing the objective of establishing a culture of safety within their organizations and are willing to share their stories.
“We basically use persuasion and motivation,” says Michael Douglas, senior manager/consultant, Global Health & Safety, Design/Standards/Technologies, at General Motors LLC, in Detroit. “You identify the key players. I draw a Venn diagram with four intersecting circles representing groups within a company. The classifications are leaders, creators or designers, integrators and producers. They overlap with one idea in the middle. The groups specific to auto manufacturing are leadership, execution teams and suppliers, global engineering centers, and manufacturing facility, or plant floor. What I’m trying to get through is the intersection. You have one consistent idea you push—in this case, safety.”
Douglas is one of several people who cited the ideas of Malcolm Gladwell as foundational to their work as change agents in companies. Gladwell explained how ideas take off, in his book, “The Tipping Point.” Douglas adds, “Gladwell pointed out the three things you need to get things to take off—The Law of the Few, Stickiness and The Power of Context. (see “Reaching The Tipping Point,” for details on these ideas) Another key thing is that you have to give people a choice. You have to speak to each group differently. Then you have to get them all moving in the same direction.”
Avoid rigidity
One problem in getting people to change behaviors is that they tend to be too rigid about a new program in the beginning. “You have to allow the variables to converge over time. People have to say to themselves, ‘Oh, yeah, we’ll get better as time goes on. We can figure out the details as we proceed.’ ”
Gladwell’s The Power of the Few discusses finding a few people who are well connected and enthusiastic. Douglas talks of figuring out the major players in each of the categories. Stickiness entails coming up with a way to express the idea that is memorable. In Douglas’ case, he developed a graphic with two cylinders to picture the two-stage approach to safety—calling it the double barrel. “You can apply the double barrel to safety, sustainability or whatever,” he adds.
Stage one, the first barrel, seeks to eliminate situations. Action steps include such items as changing a task, function or layout, or substituting materials. Stage two’s goal is balance. It can use technology for engineering controls or personal protective equipment or human factors such as awareness with warnings, signs and the like; safe operating procedures; and training. A combination of actions within stage one eliminates hazards. A combination of actions within stage two reduces risk to a safe and acceptable level.
Douglas and his team then developed a risk-assessment worksheet to document situations. This document also shows the contribution or benefit of the change—the value proposition. Safety changes often also have a positive impact on plant operations.
“The idea of a flex risk assessment optimizes your bottom line,” concludes Douglas. “People make it too complicated. Using the two-stage approach with quick risk assessment will capture business benefits. When you get down to building things, engineers just want to build. The leader wants ‘on-time, on-budget.’ The plant wants to be safe. By identifying groups and figuring out what resonates, you succeed. Flexibility is key. With two-stage and scrap paper, you can capture all the data you need in a conversation. You don’t need a big official meeting. You can use this idea to diminish the bureaucracy.”
Start at the top
Phoenix Contact is not only a supplier of automation and control components, but it also has manufacturing/distribution operations at its U.S. headquarters in Middletown, Pa. Larry Wasser, vice president of operations, discusses how the company has instilled a safety culture.
“It does start at the top,” says Wasser. “We have in our mission/vision statement that employees are important to the company. We let them know that we value employees and that we’ll help them be safe. And the first and most important step in this process is communication to help people understand.”
One of the first actions the company took was to become OHSAS 18001 certified (for Occupational Health and Safety Assessment Series). This is the international standard for health and safety management systems that has been developed to be compatible with International Organization for Standardization (ISO) standards that are more well known, such as ISO 9000 for quality management systems and ISO 14000 for environmental management systems.
Wasser adds, “As a European company, we have been ISO 14000 certified in Germany for many years. We were the first company site outside of Europe to achieve certification. It took some work to get all the appropriate policies and procedures in place, but it was worth it. I look at all three (ISO 9000, ISO 14000, OHSAS 18000) equally as important processes. If not right, it’s non-conforming. You need to look at processes.”
The Occupational Safety and Health Administration (OSHA) of the U.S. government is charged with protecting people in the workplace. It promulgates regulations that are prescriptive in approach, seeking to define hazards with requirements to protect against them. The international approach is process oriented. Wasser considers OHSAS 18000 to be an important tool. “It goes much beyond OSHA,” he says. “If I were ever at a company that had statistics for injuries above industry norms, there obviously would be a systemic problem. I’d use it as a technique to get people to understand the process before jumping in to start ‘fire fighting.’ ”
At Phoenix Contact, there is a job-hazard analysis that is more than just a form—it’s a process that involves many people, with management sign-off. Wasser describes the process: “Even though we may have taken delivery of a machine that meets OHSA requirements for such things as guarding and pinch points, the job-hazard analysis, must be done before starting the machine. Management and users look at the machine, its guarding, training required—everything involved in operating that machine—before signing off.”
Involve everyone
Safety committee work involves office workers, as well as production people, supervisors and management. The Commonwealth of Pennsylvania has a safety program tied to its Workman’s Compensation program. Phoenix Contact’s committee has been certified and audited for six years. The committee reviews past accidents and conducts walk-throughs, documenting what they do and find. It also publishes an internal newsletter several times per year to keep everyone updated on safety.
Wasser offers a final caution. “By building the process that management has to account for injuries, when operators and the supervisor check out something, the supervisor knows that management takes it seriously. If you don’t believe in the process, you only do the forms. But if everyone takes things seriously, then the safety culture builds.”
Safety is core to the U.S. operations of the French power and automation supplier Schneider Electric. According to Rich Widdowson, vice president of safety, real estate and environment, in Palatine, Ill., the process begins with messaging and communications. “We’ve had strong messaging from our CEO (chief executive officer) since 2003 to get this intense safety process started and continuing. But it takes continual messaging, or people will think we’ve solved the problem,” Widdowson says. “We lean on managers and supervisors to drive safety daily—and to lead by example. And we challenge all people to be a part of the process.”
Schneider uses a program called Safestart, from Eletrolab Ltd., of Belleville, Ontario, Canada. Widdowson says it helps with communicating safety to people. “It ties in everything. It makes you look into state of mind—things like rushing, fatigue, frustration and complacency. First, we take everyone through the initial training that includes five one-hour modules. Then there is a follow up DVD presentation once a quarter at every site. We combine this with onsite awareness by everyone of where we are in regard to safety. If you talk to people about safety, they can tell you when the last case was—not just lost time, but also a doctor’s visit. We use a variety of ways to get people involved and aware. One site has a Bingo type of program. Go a day without an incident and you get a number.”
The safety process at Schneider does not stop with time in the plant. According to Widdowson, “We want them to think safety not just at the job, but at home and on the way in between. Twenty-four hours a day. Safety is all about creating safe habits, about trying to get them to take it into their lives. For example, if work requires the use of safety glasses, then if they are at home, it’s the same thing. We want them to instill safe habits in life so that when they come to work, it’s a habit.”
Go home uninjured
Senior management is crucial to the effectiveness of the program. Widdowson says, “We want them going home uninjured. The senior team has done a fantastic job of sending messages, and they want to be notified on all cases. If someone goes to the hospital, the information goes right to the CEO. Yes, we want productive and efficient factories, but that doesn’t matter if you are doing it in an unsafe manner.”
These three examples from continuing processes show the importance of continual communication, building trust, getting key people on board and finding ways to get people to remember what you’re trying to do. Some industry veterans who work closely with customers to improve safety also weigh in with tips and advice they’ve gleaned.
George Schuster, senior industry consultant, Safety and Sustainability Solutions, with automation supplier Rockwell Automation Inc., in Detroit, thinks the topic of building a culture doesn’t get enough play with engineers. “Engineers aren’t psychologists,” says Schuster, “but they need to understand the people aspect of safety. It’s not all about technology, specifications and standards. Safety has much more to do with company culture.”
The first factor in building a safety culture cited by Schuster is credibility. “If people think it’s just a marketing ploy or nice words without backing, then it will fail,” he says. Credibility comes from commitment—from the top. And it must be both words and deeds.
Another issue is ownership of the process and accountability for it. “Some organizations may say their human resources department is responsible. Or maybe facilities. Or engineering. But in any successful safety culture, everyone is a stakeholder,” Schuster observes. “To adopt that philosophy takes time and commitment.”
A senior manager of a company must have a defining moment. Says Schuster, “When I try to help, I try to ascertain, in their own language, if that moment has happened. If it has, it looks like this example. The senior manager is in a meeting with all operations managers. They are bemoaning the situation of complying with safety. It’s time and money problems. The CEO finally says, ‘If you do not comply and implement by this date, I’ll shut your plant down. We cannot afford noncompliance. It’s not acceptable. There is no excuse—not money or time.’ When he (the senior manager) finally understood the real cost associated with safety and noncompliance in terms of injuries, lost work, social reportables, litigation, insurance and more, he began to see. Then, couple that with softer measures such as employee retention as a cost, turnover rate and best place to work surveys, he starts seeing things a successful safety program can bring.”
Misperception
Subscribe to Automation World's RSS Feeds for Feature Articles
Companies in this Article
Sponsored Recommendations
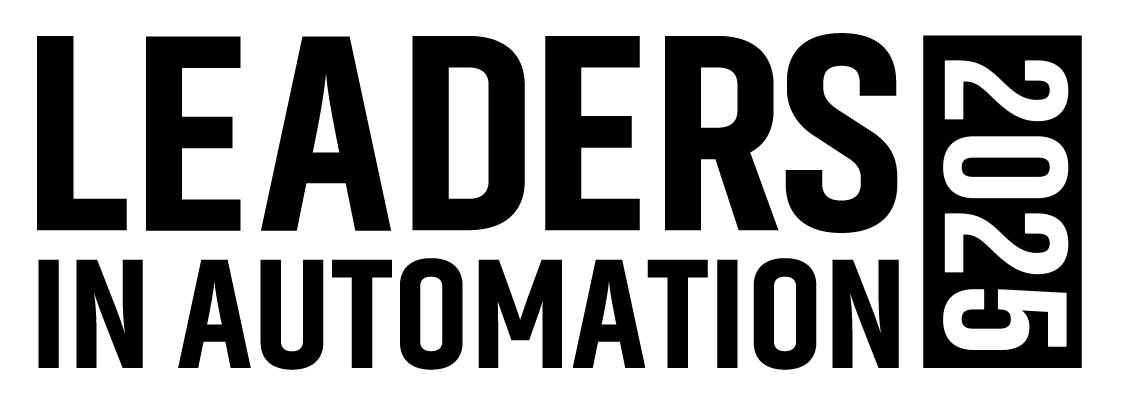
Leaders relevant to this article: