As the green movement blankets the globe, manufacturers race to produce green equipment and products. Among companies across North America, a large percentage look to green machines manufactured in Italy to help them meet environmental goals.Streamlining production
Growing demand for building projects that reflect green initiatives is impacting the ventilation industry. According to Bruce A. Bohr, principal manufacturing engineer at Greenheck Fan Corp. (www.greenheck.com), his company now posts sales of approximately $500 million annually, employs more than 2,850 people, and utilizes more than 1.5 million sq ft of manufacturing space. Greenheck has come a long way since 1947 when it began business as a tiny sheet metal shop in Schofield, Wisconsin. Known worldwide as a leading manufacturer of air-movement and control equipment, the company’s flagship ventilation products are typically found behind walls, in ductwork or on the roofs of hospitals, office buildings, hotels, shopping malls, restaurants, schools, industrial plants and other commercial buildings. Today, the company’s products are shipped around the globe.Greenheck was one of the first manufacturers of air-moving and control equipment to join the U.S. Green Building Council. Greenheck also references USGBC and ASHRAE guidelines and standards to identify specific products that mechanical engineers can use when designing ventilation systems for sustainable-design projects and for those adhering to LEED certification guidelines.Bohr was responsible for specifying, purchasing and managing the installation of two Salvagnini Italia S.p.A. P-4 CNC panel formers (www.salvagninigroup.com). He explains, “One was installed in 2004 and the other was installed in 2008. These machines form doors, cabinet panels and other sheet metal components of integrated HVAC systems for ventilating commercial and industrial buildings.“Salvagnini P-4 panel benders replace press brakes that formerly formed the same sheet metal components. They require much less time to change from one part to another. This feature makes it possible to reduce inventory and decrease response time.”Bohr notes that his company would consider the purchase of similar machinery in the future. He adds, “There are other product lines at the company that could benefit from changing from conventional press brake forming to CNC panel forming. The installation of the Salvagnini P-4 panel benders has been a key factor in streamlining the production of the Greenheck Fan Corporation Make-up Air and Kitchen Systems Make-up Air units.”Reducing weight and sizeGaseous emissions, referred to as greenhouse gases, are one of many environmental challenges that today’s manufacturers face. Experts caution that a significant reduction of the gases is a necessity, and the goal of cutting such emissions is familiar in industry.Ritmo S.p.A. (www.ritmo.it), a global leader in plastic welding equipment manufacturing, looked at ways to reduce its gas emissions. The Italian company prides itself on producing fast, accurate, versatile, modular and easy-to-use welding machines. The product range includes butt fusion, electrofusion and extrusion equipment, as well as a complete line of accessories and instruments for pipe cutting and weld preparation.Ritmo has designed the new RAM 824 All Terrain, a totally independent fusion machine with an on-board generator for butt fusion of plastic pipes for the transport of fluids under pressure.Since beginning development of the All Terrain, the company examined its environmental impact at a number of levels, not only in order to provide a functional product, but also with the objective of “going green.”Two key aspects of the new product are weight reduction and implementation of a smaller engine. An approximate 2,200-lb weight reduction permits use of a turbocharged diesel engine from 2,200 cc with four inline cylinders and direct injection. Four-wheel drive steering allows the vehicle to climb easily across rough terrain.Because the engine is set for developing 22.7 kW at 1,500 rpm, running at a speed of rotation lower than its maximum power, it is possible to substantially reduce wear and periodic maintenance and to significantly drive down the value of noise. Such features result in reduced fuel consumption and, consequently, a decrease in greenhouse gas emissions. Compared to similar equipment, in a 12-hour time period, it is possible to cut emissions of 120 lbs of carbon dioxide, or more than eight tons per year. The company cites recent studies which claim that an “average tree” can filter about 44 lbs of carbon dioxide in a year, so for those eight tons, more than 400 trees would have been required.Another solution that helps achieve the company’s environmental goals is the electronic Easy Life fusion system, which manages the fusion cycle and helps an operator avoid errors and material waste. The electronic control unit optimizes power consumption by the engine during critical phases of fusion, restoring pressure in the hydraulic system when any kind of drops occur (only when necessary) due to an additional rotational system.According to Tres Tuttle, Ritmo America LLC manager, one of his company’s good customers in the water and waste industry, Latham, New York-based Vellano Bros. Inc. (www.vellano.com), was renting the RAM to use in their installation of municipal piping; however, they were so impressed with its many efficiencies that they recently purchased the machine.Cutting timeStanley Furniture Company (www.stanleyfurniture.com) dates back to 1924 when Thomas B. Stanley, a young dairy farmer, founded the company. His vision was to create furniture that boasted superior craftsmanship and style, as well as affordability. He began by shipping the finest lumber from the Northeast to a small town in western Virginia, later to be named Stanleytown, where he employed highly skilled craftsmen.Today, more than 1,300 associates carry out Thomas Stanley’s vision of quality, American-made furniture. Stanley has two manufacturing locations, one in Robbinsville, North Carolina, where the majority of its youth products are manufactured, and another in Stanleytown, Virginia, where the adult collections and baby cribs are made.“We purchased two Paolino Bacci Srl (www.bacci.com) machines last fall,” reports Eric Jones, Stanley’s corporate industrial engineer, “and they were installed at the beginning of December. One is a 5-axis CNC machine center called the JET. This machine enables us to complete all of the machining requirements for the bed posts including the boring and slotting for the bed lock on our ‘Built to Grow’ cribs.”Founded in 1918, Paolino Bacci Srl is one of the oldest and most respected woodworking machinery manufacturers in Italy and the world. The JET is suitable for applications such as tenoning, finger jointing, drilling, mortasing, milling and 4/5 axis profiling. The particular axes motion allows the machining of five faces of a wooden piece with little movement but with high acceleration due to the strong rigidity of the machine. Support is placed at an ergonomic height on which machined pieces are lined up in order and without collisions. R.H. pieces are separated from L.H. pieces.Stanley’s Jones adds, “We also have Bacci shapers and sanders for furniture heads and to make contours for caprioles. We bought a number of smaller machines, and even have purchased some used Italian machines from a Canadian company. The sander is Italian; it seems to fit really well. Italy has a nice niche for crib manufacturing equipment. We sent a group of three people over to Italy to visit Bacci and other companies and they were very impressed.“By combining as many as six or seven different operations at one machine, we can efficiently produce the posts needed with less lead time, better and consistent quality and in about a fourth of the time required if operations were done individually. When business picks up, I would imagine we would be very interested in purchasing additional machines.”Pursuing efficienciesAnother company wanting to save time and increase efficiency is Sacmi Imola S.C. (www.sacmi.com). Its goal is to complete the CCM range while taking the compression world to unprecedented levels with a machine that can produce 2,000 caps per minute with a cycle time of 2.4 seconds. This is the CCM 80 (Continuous Compression Molding), which joins the company’s CCM 48 and 64 models of beverage cap production systems.This machine offers the advantages of compression technology, that is, maximum homogeneity of the bottle cap output guaranteed by the fact that the punches work independently of each other. This is not so with injection technology, which, while providing high output rates, struggles to ensure uniform output quality. Injection technology (usually featuring 128-cavity molds) makes it extremely difficult to maintain uniform temperatures and to ensure uniform distribution of plastic. Outgoing pieces are not all the same and, because bottling lines are increasingly faster, any downtime caused by cap quality problems can inflict economic damage on the producers that are much higher than the unit cost of the individual cap. Therefore, compression and thus dimensional consistency and qualitative excellence are imperative.CCM 80 has received encouraging market feedback. Previewed at Chinaplas, it was immediately purchased by a Chinese customer, Tin Hsin, one of the major local bottle and pre-form producers. The machine became fully operational at the start of 2010.When Sacmi displayed CCM 80 again at Drinktec in Munich, it attracted the attention of Hana Water, one of Saudi Arabia’s biggest bottling concerns. They too purchased it. The CCM 80 is perfect for companies with high output volumes, often the case in emerging markets. The machine covers the high-volume production segment with very short cycle times while offering advantages in terms of energy resource optimization. It features new extrusion control systems, which adjust energy consumption according to speed, which, in turn, depends on cap type and geometry – with the result that the unit cost of the individual cap drops. This “variable consumption system” makes using the machine profitable in any production situation, thus allowing it to take its place among a new range of the company’s machines specially developed to enhance quality while simultaneously cutting energy costs and reducing environmental impact.Embracing the “green heart”In recent years, the topic of sustainability has strongly entered the market, with an impact on all sectors. The development and diffusion of environmental technologies is a central element of European Union politics concerning environment and sustainable growth. Environmental technologies prevent, reduce and recover pollution, with new materials, new processes and methods at a low environmental impact. In this effort, Losma S.p.A. (www.losma.com) represents a small but important reality in the control and elimination of environmental pollution.Since 1974, Losma has produced and distributed air and coolant filtration systems for machine tools. Air filters clean the air from oil mist, vapors, micro-mists and smoke and recover oil during manufacturing processes.Coolant filters clean coolants and other liquids used during machining from magnetic and a-magnetic particles that could lower machining tolerances. Many products for both air and coolant filtration are patented and all are conceived on a modular base, in order to meet customer needs with the addition of different filtration, pre-filtration or after-filtration modules.At the European trade event EMO 2009 (www.emo-milano.it), the theme around which Losma focused its presence was the “green heart.” The campaign is related to the vision of the company, increasingly involved in the sustainability of industry itself and the belief that mechanical industry must “go green.” Losma’s “green heart” speaks about the challenging themes of innovation, environment, bio-compatibility and eco-sustainability.The most important innovation Losma presented at EMO was a new way of looking at industrial filtration, through its new patented biofilter, GREEN, an innovative filtration kit.Based on the use of natural materials, it provides a way of filtering air contaminated by oil mist produced during manufacturing; “green hearts” are put into Losma’s Gemini and Newton Series filtration systems.Made of 100 percent natural fibers, the new biofilter was permitted to use the FAO (Food and Agriculture Organization of the United Nations) logo for the International Year of Natural Fibers 2009.The product offers very high filtration efficiency and long life and prolongs the life of other filters in the machine. GREEN does not need any packing system (plastic or otherwise) because the kit is transported ready for use.Losma already has an order from a manufacturing electronic connector company supplying the military, aerospace industries and medical and commercial aviation in Texas. Several proposals have been made with existing customers to retrofit older Losma air filtration equipment with the GREEN biofilter. Some of the customers are located in North Carolina, manufacturing door controls; in Oregon, treating a solvent spray recovery system on a wood treatment facility; and in Oklahoma at a manufacturer serving the lifting and material handling industry.Galdi offers energy-saving filling machinesGaldi Srl (www.galdi.it) designs and manufactures filling machines for the food industry, particularly for milk, dairy products and fruit juice. Throughout its 25-year history, Galdi has established itself as a leader in the European market of gable-top filling and cartoning machines for liquid foodstuffs. The company has been constantly engaged in ambitious R&D projects to renew its ongoing product portfolio. It maintains long-term partnerships with multinational suppliers of paper containers. Galdi’s new frontier is the development of machines that feature lower consumption and higher performance through a combination of traditional mechanics and the potential of the latest IT and electronic technologies, using state-of-the-art materials.The filling machines are developed with clear energy-saving rationales as a priority, from compressed air use being dramatically cut in the company’s latest models through servo-motor-assisted control systems, down to considerably reduced acoustic pollution, compared to traditional production processes.The minimal design and ergonomics of Galdi machines provide user-friendliness, reduced overall dimensions, elevated production standards, and minimum machine operation and maintenance costs. The result realized by customers is extremely versatile machines, an increased number of filled cartons per hour, easy and quick format changing and optimal timing of production processes.Vetraco goes greenerVE.TRA.CO Group Srl (www.vetraco.com) has designed and manufactured processing and packaging machines for the cosmetics industry, assembly lines, automation solutions with vision robotics and QC systems since 1975.In the past three years, Vetraco has focused on building greener machines, engineered to use fewer resources and to save energy to improve the working environment. The company’s goal was achieved through converting to electronics with the exclusive use of motors that featured low power consumption, as well as replacement of hydraulic solutions in order to completely eliminate use of oils to prevent environmental pollution and product contamination.Electronic solutions also contribute to a drastic reduction of the noise level to produce a more operator-friendly environment. Machine efficiency and remote assistance via modem reduce downtime and operational costs. Other resource-savings practices involve a limited use of pneumatics.SMI shrinking tunnel gives North American manufacturers pollution-free solutionsSMI S.p.A. (www.smigroup.it) has developed a new tunnel type; thermoshrinking film has become the most used packaging material to pack food, beverages and non-food products. Therefore, shrinkwrappers have become popular in bottling and packaging lines of large and small producers. This packaging process requires a thermoshrinking tunnel which, by means of heat generated by electric resistances, gets plastic film shrunk around bottles to make a solid, compact pack. Smiflexi shrinkwrappers (LSK and SK Series) can be equipped with a standard electrically powered shrinking tunnel or with a new methane-heated model.The new tunnel type, through combustion of natural gas, instead of electric resistances, produces heat for the operation. Methane advantages are that it provides smogless and pollution-free combustion, is environmentally friendly, and, in countries where it is available at a low price, it dramatically cuts costs in energy procurement. In the SMI machine testing department, technicians have carried out trials to calculate actual natural gas consumption during thermoshrinking; then, results of the testing have been compared with electricity consumption to perform the same operations.Tests were performed according to a variety of parameters. Under the same working conditions, the consumption monitored was equal to 3 m3 of methane and 25 Kw/h of electricity.Analysis proves that, at least in Italy, use of the natural gas-heated shrinking tunnel ensures a 70 percent saving in energy consumption costs. Time for reaching the working temperature is shorter by 75 percent in comparison with the electricity-powered tunnel.Laser not only cuts coil, but North American manufacturers’ costsIRON S.p.A. (www.iron.it) Temnos is a laser cutting system to cut parts from strip or coil input. Using hybrid-cutting technology, strip fed being the X-axis, Temnos offers material savings and flexibility in cutting blanks for automotive and other industry sectors. The strip specifications at maximum, based on mild steel, are 1,540 mm width, with thickness to 3 mm. Laser technology can be either carbon dioxide or fiber sources. IRON offers a system that delivers precision parts with repeatable accuracy and laser-cut edge quality, across a selection of materials and thicknesses, with no tooling issues. The versatile system permits kit making. Greenheck Fan Corp.www.greenheck.comSalvagnini Italia S.p.A.
www.salvagninigroup.comRitmo S.p.A.www.ritmo.itVellano Bros. Inc.www.vellano.comStanley Furniture Companywww.stanleyfurniture.comPaolino Bacci Srlwww.bacci.comSacmi Imola S.C.www.sacmi.comLosma S.p.A.www.losma.comEMO 2009www.emo-milano.itGaldi Srlwww.galdi.itVE.TRA.CO Group Srlwww.vetraco.comSMI S.p.A.www.smigroup.itIRON S.p.A.www.iron.it
Growing demand for building projects that reflect green initiatives is impacting the ventilation industry. According to Bruce A. Bohr, principal manufacturing engineer at Greenheck Fan Corp. (www.greenheck.com), his company now posts sales of approximately $500 million annually, employs more than 2,850 people, and utilizes more than 1.5 million sq ft of manufacturing space. Greenheck has come a long way since 1947 when it began business as a tiny sheet metal shop in Schofield, Wisconsin. Known worldwide as a leading manufacturer of air-movement and control equipment, the company’s flagship ventilation products are typically found behind walls, in ductwork or on the roofs of hospitals, office buildings, hotels, shopping malls, restaurants, schools, industrial plants and other commercial buildings. Today, the company’s products are shipped around the globe.Greenheck was one of the first manufacturers of air-moving and control equipment to join the U.S. Green Building Council. Greenheck also references USGBC and ASHRAE guidelines and standards to identify specific products that mechanical engineers can use when designing ventilation systems for sustainable-design projects and for those adhering to LEED certification guidelines.Bohr was responsible for specifying, purchasing and managing the installation of two Salvagnini Italia S.p.A. P-4 CNC panel formers (www.salvagninigroup.com). He explains, “One was installed in 2004 and the other was installed in 2008. These machines form doors, cabinet panels and other sheet metal components of integrated HVAC systems for ventilating commercial and industrial buildings.“Salvagnini P-4 panel benders replace press brakes that formerly formed the same sheet metal components. They require much less time to change from one part to another. This feature makes it possible to reduce inventory and decrease response time.”Bohr notes that his company would consider the purchase of similar machinery in the future. He adds, “There are other product lines at the company that could benefit from changing from conventional press brake forming to CNC panel forming. The installation of the Salvagnini P-4 panel benders has been a key factor in streamlining the production of the Greenheck Fan Corporation Make-up Air and Kitchen Systems Make-up Air units.”Reducing weight and sizeGaseous emissions, referred to as greenhouse gases, are one of many environmental challenges that today’s manufacturers face. Experts caution that a significant reduction of the gases is a necessity, and the goal of cutting such emissions is familiar in industry.Ritmo S.p.A. (www.ritmo.it), a global leader in plastic welding equipment manufacturing, looked at ways to reduce its gas emissions. The Italian company prides itself on producing fast, accurate, versatile, modular and easy-to-use welding machines. The product range includes butt fusion, electrofusion and extrusion equipment, as well as a complete line of accessories and instruments for pipe cutting and weld preparation.Ritmo has designed the new RAM 824 All Terrain, a totally independent fusion machine with an on-board generator for butt fusion of plastic pipes for the transport of fluids under pressure.Since beginning development of the All Terrain, the company examined its environmental impact at a number of levels, not only in order to provide a functional product, but also with the objective of “going green.”Two key aspects of the new product are weight reduction and implementation of a smaller engine. An approximate 2,200-lb weight reduction permits use of a turbocharged diesel engine from 2,200 cc with four inline cylinders and direct injection. Four-wheel drive steering allows the vehicle to climb easily across rough terrain.Because the engine is set for developing 22.7 kW at 1,500 rpm, running at a speed of rotation lower than its maximum power, it is possible to substantially reduce wear and periodic maintenance and to significantly drive down the value of noise. Such features result in reduced fuel consumption and, consequently, a decrease in greenhouse gas emissions. Compared to similar equipment, in a 12-hour time period, it is possible to cut emissions of 120 lbs of carbon dioxide, or more than eight tons per year. The company cites recent studies which claim that an “average tree” can filter about 44 lbs of carbon dioxide in a year, so for those eight tons, more than 400 trees would have been required.Another solution that helps achieve the company’s environmental goals is the electronic Easy Life fusion system, which manages the fusion cycle and helps an operator avoid errors and material waste. The electronic control unit optimizes power consumption by the engine during critical phases of fusion, restoring pressure in the hydraulic system when any kind of drops occur (only when necessary) due to an additional rotational system.According to Tres Tuttle, Ritmo America LLC manager, one of his company’s good customers in the water and waste industry, Latham, New York-based Vellano Bros. Inc. (www.vellano.com), was renting the RAM to use in their installation of municipal piping; however, they were so impressed with its many efficiencies that they recently purchased the machine.Cutting timeStanley Furniture Company (www.stanleyfurniture.com) dates back to 1924 when Thomas B. Stanley, a young dairy farmer, founded the company. His vision was to create furniture that boasted superior craftsmanship and style, as well as affordability. He began by shipping the finest lumber from the Northeast to a small town in western Virginia, later to be named Stanleytown, where he employed highly skilled craftsmen.Today, more than 1,300 associates carry out Thomas Stanley’s vision of quality, American-made furniture. Stanley has two manufacturing locations, one in Robbinsville, North Carolina, where the majority of its youth products are manufactured, and another in Stanleytown, Virginia, where the adult collections and baby cribs are made.“We purchased two Paolino Bacci Srl (www.bacci.com) machines last fall,” reports Eric Jones, Stanley’s corporate industrial engineer, “and they were installed at the beginning of December. One is a 5-axis CNC machine center called the JET. This machine enables us to complete all of the machining requirements for the bed posts including the boring and slotting for the bed lock on our ‘Built to Grow’ cribs.”Founded in 1918, Paolino Bacci Srl is one of the oldest and most respected woodworking machinery manufacturers in Italy and the world. The JET is suitable for applications such as tenoning, finger jointing, drilling, mortasing, milling and 4/5 axis profiling. The particular axes motion allows the machining of five faces of a wooden piece with little movement but with high acceleration due to the strong rigidity of the machine. Support is placed at an ergonomic height on which machined pieces are lined up in order and without collisions. R.H. pieces are separated from L.H. pieces.Stanley’s Jones adds, “We also have Bacci shapers and sanders for furniture heads and to make contours for caprioles. We bought a number of smaller machines, and even have purchased some used Italian machines from a Canadian company. The sander is Italian; it seems to fit really well. Italy has a nice niche for crib manufacturing equipment. We sent a group of three people over to Italy to visit Bacci and other companies and they were very impressed.“By combining as many as six or seven different operations at one machine, we can efficiently produce the posts needed with less lead time, better and consistent quality and in about a fourth of the time required if operations were done individually. When business picks up, I would imagine we would be very interested in purchasing additional machines.”Pursuing efficienciesAnother company wanting to save time and increase efficiency is Sacmi Imola S.C. (www.sacmi.com). Its goal is to complete the CCM range while taking the compression world to unprecedented levels with a machine that can produce 2,000 caps per minute with a cycle time of 2.4 seconds. This is the CCM 80 (Continuous Compression Molding), which joins the company’s CCM 48 and 64 models of beverage cap production systems.This machine offers the advantages of compression technology, that is, maximum homogeneity of the bottle cap output guaranteed by the fact that the punches work independently of each other. This is not so with injection technology, which, while providing high output rates, struggles to ensure uniform output quality. Injection technology (usually featuring 128-cavity molds) makes it extremely difficult to maintain uniform temperatures and to ensure uniform distribution of plastic. Outgoing pieces are not all the same and, because bottling lines are increasingly faster, any downtime caused by cap quality problems can inflict economic damage on the producers that are much higher than the unit cost of the individual cap. Therefore, compression and thus dimensional consistency and qualitative excellence are imperative.CCM 80 has received encouraging market feedback. Previewed at Chinaplas, it was immediately purchased by a Chinese customer, Tin Hsin, one of the major local bottle and pre-form producers. The machine became fully operational at the start of 2010.When Sacmi displayed CCM 80 again at Drinktec in Munich, it attracted the attention of Hana Water, one of Saudi Arabia’s biggest bottling concerns. They too purchased it. The CCM 80 is perfect for companies with high output volumes, often the case in emerging markets. The machine covers the high-volume production segment with very short cycle times while offering advantages in terms of energy resource optimization. It features new extrusion control systems, which adjust energy consumption according to speed, which, in turn, depends on cap type and geometry – with the result that the unit cost of the individual cap drops. This “variable consumption system” makes using the machine profitable in any production situation, thus allowing it to take its place among a new range of the company’s machines specially developed to enhance quality while simultaneously cutting energy costs and reducing environmental impact.Embracing the “green heart”In recent years, the topic of sustainability has strongly entered the market, with an impact on all sectors. The development and diffusion of environmental technologies is a central element of European Union politics concerning environment and sustainable growth. Environmental technologies prevent, reduce and recover pollution, with new materials, new processes and methods at a low environmental impact. In this effort, Losma S.p.A. (www.losma.com) represents a small but important reality in the control and elimination of environmental pollution.Since 1974, Losma has produced and distributed air and coolant filtration systems for machine tools. Air filters clean the air from oil mist, vapors, micro-mists and smoke and recover oil during manufacturing processes.Coolant filters clean coolants and other liquids used during machining from magnetic and a-magnetic particles that could lower machining tolerances. Many products for both air and coolant filtration are patented and all are conceived on a modular base, in order to meet customer needs with the addition of different filtration, pre-filtration or after-filtration modules.At the European trade event EMO 2009 (www.emo-milano.it), the theme around which Losma focused its presence was the “green heart.” The campaign is related to the vision of the company, increasingly involved in the sustainability of industry itself and the belief that mechanical industry must “go green.” Losma’s “green heart” speaks about the challenging themes of innovation, environment, bio-compatibility and eco-sustainability.The most important innovation Losma presented at EMO was a new way of looking at industrial filtration, through its new patented biofilter, GREEN, an innovative filtration kit.Based on the use of natural materials, it provides a way of filtering air contaminated by oil mist produced during manufacturing; “green hearts” are put into Losma’s Gemini and Newton Series filtration systems.Made of 100 percent natural fibers, the new biofilter was permitted to use the FAO (Food and Agriculture Organization of the United Nations) logo for the International Year of Natural Fibers 2009.The product offers very high filtration efficiency and long life and prolongs the life of other filters in the machine. GREEN does not need any packing system (plastic or otherwise) because the kit is transported ready for use.Losma already has an order from a manufacturing electronic connector company supplying the military, aerospace industries and medical and commercial aviation in Texas. Several proposals have been made with existing customers to retrofit older Losma air filtration equipment with the GREEN biofilter. Some of the customers are located in North Carolina, manufacturing door controls; in Oregon, treating a solvent spray recovery system on a wood treatment facility; and in Oklahoma at a manufacturer serving the lifting and material handling industry.Galdi offers energy-saving filling machinesGaldi Srl (www.galdi.it) designs and manufactures filling machines for the food industry, particularly for milk, dairy products and fruit juice. Throughout its 25-year history, Galdi has established itself as a leader in the European market of gable-top filling and cartoning machines for liquid foodstuffs. The company has been constantly engaged in ambitious R&D projects to renew its ongoing product portfolio. It maintains long-term partnerships with multinational suppliers of paper containers. Galdi’s new frontier is the development of machines that feature lower consumption and higher performance through a combination of traditional mechanics and the potential of the latest IT and electronic technologies, using state-of-the-art materials.The filling machines are developed with clear energy-saving rationales as a priority, from compressed air use being dramatically cut in the company’s latest models through servo-motor-assisted control systems, down to considerably reduced acoustic pollution, compared to traditional production processes.The minimal design and ergonomics of Galdi machines provide user-friendliness, reduced overall dimensions, elevated production standards, and minimum machine operation and maintenance costs. The result realized by customers is extremely versatile machines, an increased number of filled cartons per hour, easy and quick format changing and optimal timing of production processes.Vetraco goes greenerVE.TRA.CO Group Srl (www.vetraco.com) has designed and manufactured processing and packaging machines for the cosmetics industry, assembly lines, automation solutions with vision robotics and QC systems since 1975.In the past three years, Vetraco has focused on building greener machines, engineered to use fewer resources and to save energy to improve the working environment. The company’s goal was achieved through converting to electronics with the exclusive use of motors that featured low power consumption, as well as replacement of hydraulic solutions in order to completely eliminate use of oils to prevent environmental pollution and product contamination.Electronic solutions also contribute to a drastic reduction of the noise level to produce a more operator-friendly environment. Machine efficiency and remote assistance via modem reduce downtime and operational costs. Other resource-savings practices involve a limited use of pneumatics.SMI shrinking tunnel gives North American manufacturers pollution-free solutionsSMI S.p.A. (www.smigroup.it) has developed a new tunnel type; thermoshrinking film has become the most used packaging material to pack food, beverages and non-food products. Therefore, shrinkwrappers have become popular in bottling and packaging lines of large and small producers. This packaging process requires a thermoshrinking tunnel which, by means of heat generated by electric resistances, gets plastic film shrunk around bottles to make a solid, compact pack. Smiflexi shrinkwrappers (LSK and SK Series) can be equipped with a standard electrically powered shrinking tunnel or with a new methane-heated model.The new tunnel type, through combustion of natural gas, instead of electric resistances, produces heat for the operation. Methane advantages are that it provides smogless and pollution-free combustion, is environmentally friendly, and, in countries where it is available at a low price, it dramatically cuts costs in energy procurement. In the SMI machine testing department, technicians have carried out trials to calculate actual natural gas consumption during thermoshrinking; then, results of the testing have been compared with electricity consumption to perform the same operations.Tests were performed according to a variety of parameters. Under the same working conditions, the consumption monitored was equal to 3 m3 of methane and 25 Kw/h of electricity.Analysis proves that, at least in Italy, use of the natural gas-heated shrinking tunnel ensures a 70 percent saving in energy consumption costs. Time for reaching the working temperature is shorter by 75 percent in comparison with the electricity-powered tunnel.Laser not only cuts coil, but North American manufacturers’ costsIRON S.p.A. (www.iron.it) Temnos is a laser cutting system to cut parts from strip or coil input. Using hybrid-cutting technology, strip fed being the X-axis, Temnos offers material savings and flexibility in cutting blanks for automotive and other industry sectors. The strip specifications at maximum, based on mild steel, are 1,540 mm width, with thickness to 3 mm. Laser technology can be either carbon dioxide or fiber sources. IRON offers a system that delivers precision parts with repeatable accuracy and laser-cut edge quality, across a selection of materials and thicknesses, with no tooling issues. The versatile system permits kit making. Greenheck Fan Corp.www.greenheck.comSalvagnini Italia S.p.A.
www.salvagninigroup.comRitmo S.p.A.www.ritmo.itVellano Bros. Inc.www.vellano.comStanley Furniture Companywww.stanleyfurniture.comPaolino Bacci Srlwww.bacci.comSacmi Imola S.C.www.sacmi.comLosma S.p.A.www.losma.comEMO 2009www.emo-milano.itGaldi Srlwww.galdi.itVE.TRA.CO Group Srlwww.vetraco.comSMI S.p.A.www.smigroup.itIRON S.p.A.www.iron.it
Sponsored Recommendations
Sponsored Recommendations
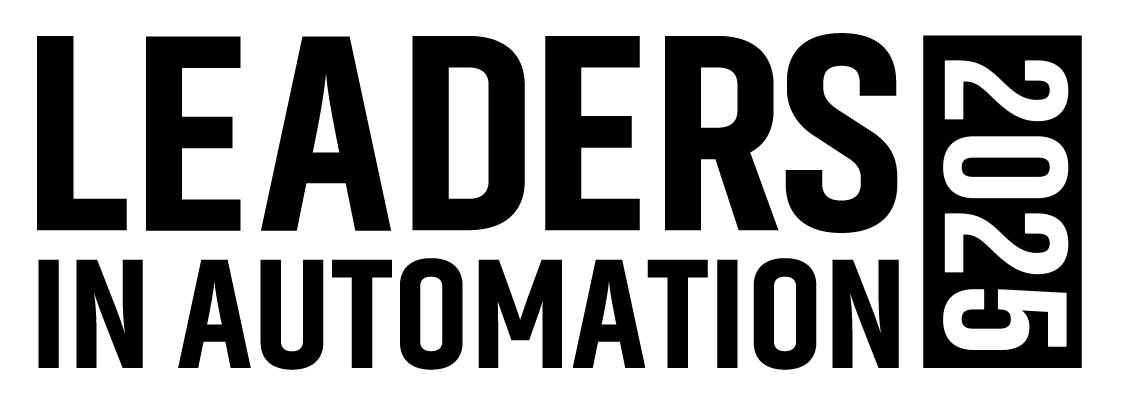
Leaders relevant to this article: