Recycling is a global phenomenon, which has been described as a basic application towards the concept of green technology. Recycling is the reuse of materials that can create useful items. Governments worldwide encourage recycling in order to protect the environment through the intelligent use of waste products to serve a new function. Coming full circle, a Canadian company will build its own Polyethylene Terephthalate (PET) recycling plant to produce 100 percent recycled PET water bottles. Ice River Springs Co., Inc. (www.iceriversprings.ca), Feversham, Ontario, Canada, will provide what it calls a world-class facility and close the loop for recycling in North America. This is the first time a water bottle company will make its own PET resin from dirty post-consumer bottles.“We believe this to be a great step in our sustainability program,” says Jamie Gott, president and co-founder of Ice River Springs (IRS). “It provides our consumers with an environmentally friendly option in their bottled water. Our goal is to eliminate our dependency upon foreign virgin PET resin by self-manufacturing recycled resin (RPET) from baled post-consumer plastic purchased from Municipal Recycling Centers.”Ice River Springs has manufacturing plants in eight locations across Canada and the United States. The company is committed to going green with its new “Go Eco” campaign. The Feversham facility has recently installed its first phase of a solar system consisting of 128 panels; it is rated to produce 90 kWh/day. Plans are to expand the system to offset electrical usage. Pollution offsets for the system are 28 tons per year of annual greenhouse gas offsets and 56 tons per year of other pollution.Because the company has developed a new lightweight bottle cap that uses 44 percent less plastic, it is reducing its carbon footprint. Geothermal chilling also reduces the footprint. The firm’s tri-axle trailers deliver more per load, reducing truck trip miles by 40 percent. Only recycled cardboard is used in production, which saves 84,000 trees per year, winning an Environmental Sustainability Award. IRS has also planted more than 70,000 trees.The use of 100 percent RPET for beverage bottles is highly innovative. This will be the first food-grade RPET manufacturing facility in Canada, diversifying the firm’s market by self-manufacturing its resin needs for beverage production, plus selling food-grade RPET resin to other food and beverage companies for a variety of packaging requirements.The project involves securing an industrial building in Shelburne, Ontario and the purchase of specialized plastics processing equipment. The equipment cleans the Blue Box materials, and purifies and converts the plastic back into a food-grade product that can be used in beverage and food applications that employ new (virgin) PET.During the last decade, IRS has decreased the amount of plastic in its bottles by approximately 40 percent and in its caps by 300 percent. It currently leads the beverage industry with one of the lightest-weight 500mL bottles in North America.The company has reduced its carbon footprint through high-efficiency lighting, geothermal chilling, high- and low-pressure air recovery and the use of alternative energy. The site in Shelburne is located on the shipping lane from the location in Feversham, permitting raw materials to be back-hauled on trucks that would normally come back empty.Ice River Springs will be the first major water bottler in North America to use a water bottle made of fully recycled plastic. Recycled food-grade PET can produce more than 20 successful generations of water bottles.There are multiple environmental advantages. The company would no longer need to purchase virgin PET resin, thereby reducing the overall demand for oil. Additionally, the recycling process uses much less energy than producing virgin PET from fossil fuels. And since most of the virgin plastic resins come from Asia, it will reduce transportation requirements and fossil fuel emissions.Jamie Gott says, “We evaluated several manufacturers of this technology for both the sorting and cleaning of the post-consumer PET bottles as well as the purification of the clean RPET materials. The choice for the washing was AMUT S.p.A. (www.amut.it), an Italian provider of extruding and thermoforming equipment, whose technology had proved to be extremely cost-effective and utilized a minimum amount of water, chemicals and energy in the cleaning process.“For the purification process, we selected a European machine manufacturer. The SSP (solid state poly-condensation) technology from the manufacturer for the purification of the flakes is excellent and demonstrates excellent attention to minimizing energy costs to convert the clean RPET flakes from the AMUT washing line into high-quality PET pellets, which are then utilized in our injection molding machinery to make the pre-forms for our new water bottles. The combination of the systems will be the first of its kind in operation in North America; they have successfully teamed up to recycle PET post-consumer bottles in France already. As such, we are very confident that our recycling plant will be a benefit to all, encouraging more recycling in North America.”This will be the first combined plant for the two equipment manufacturers in North America, although they have worked together in France to recycle post-consumer bottles. Ariostea SpA (www.ariostea.com), an Italian manufacturer of material handling equipment, is supplying material handling technology for the plant. According to Anthony Georges of AMUT North America, “Being a person who grew up in Ontario and has been involved in the environmental movement for decades, and plastics recycling for years, I can say we are extremely excited about being selected as a key technological and machinery partner. What excites me most is the opportunity to create a totally ‘closed-loop recycling’ solution for Ontario, working with Ice River Springs, a respected supplier of high-quality bottled water throughout North America.”HPSS process makes a differenceHPSS (high-performance solidification and stabilization) technology is a remarkable industrial process used for the production of stabilized, de-contaminated granules from sediments and excavation material.This is a synopsis of a report from Professor Amilcare Collina, The Expert’s Opinion, writing in Realta Mapei International. The process is the result of an original Mapei (www.mapei.it) research project based on the company’s experience about the effect of super-plasticizing additives on various hydraulic binders.Founded in Milan in 1937, Mapei is today the world leader in the production of adhesives and complementary products for the installation of all types of floor and wall coverings. The company also specializes in other chemical products for building: from waterproofers to special mortars, from admixtures for concrete to products for the restoration of ancient buildings.The two-step process was developed in Mapei’s R&D labs for treating earth and sediments contaminated by heavy metals and/or organic products. Step one is the granulation in a rotating disk, and step two is the distillation of granules in a stream of superheated steam under vacuum to eliminate organic contaminants.The outcome is the transformation of sediment/earth into a new decontaminated, stabilized granular material with good mechanical strength, which complies with the legal limits for the release of the contaminating substances present into the environment.The use of Mapei’s super-plasticizing additives allows granules to reach certain mechanical characteristics to make them suitable for various applications and eliminates the organic contaminants through an emission-free process.The company’s technology partner, In.T.Ec, transformed this process into an industrial process and built the first industrial-scale treatment plant on the Island of Murano (in the Venice lagoon) to treat the ground contaminated by heavy metals from glassworks.The contaminated ground to be disposed of (classified as hazardous waters before treatment) requires transport costs and disposal costs to be put into waste sites. It now it can be transformed into new, usable materials with a certain value.The reclamation of 6,000 m3 of ground on the island was successful. Granules were used as filler and to form screeds on the same site. Operations on a second lot got underway in 2008. The technology is covered by two patents registered in Italy; two European patents have been applied for, jointly owned by the partnering companies.Applications for by-products include filler material, aggregates for screeds, decorative stones (introduced on the market by Mapei under the name of DYNASTONE COLOR), and aggregates to make concrete.The inertization, decontamination and stabilization plant is located where reclamation takes place, avoiding transport of contaminated materials offsite. The process is emission-free and the liquid effluent, the only by-product, is sent to a waste-water treatment plant.Using it allSince 1947, Grede Iron Mountain Foundry (www.grede.com) has specialized in valves and other gray iron castings with complex internal shape requirements. Its markets encompass automotive, heavy trucks, appliances and other industrial applications.As an environmentally focused company, in 2008, recycling/reuse of Grede’s production by-products saved more than 220,000 tons of material from being landfilled. Some of the recycled materials include gates and risers, slag, sand, coke, fines, used oil, wood pallets, used grinding stones, dust collection particles, parts washer solvent and acid scrubber sludge. Many of these are reused at the plants and many of the materials that cannot be used by the company are sold or given to organizations that can reclaim or recycle them.Grede is also able to use by-products from other manufacturing processes and industries, such as shredded automobiles and appliances, railroad tracks and leftover materials from demolition projects. Just about anything made from iron or steel can be used by the foundries to produce castings.Scott Flaminio, project engineer, was responsible for the installation of the SAM 300, a 3-axis automated casting grinding cell manufactured by MAUS S.p.A. (www.maus.it), as well as its successful start-up, and initial part fixtures and operator training.The SAM 300 was on display at the 2008 CastExpo show in Atlanta, Georgia, where MAUS and Grede agreed to a three-month trial of the equipment prior to purchase.“During the initial tooling period,” says Flaminio, “we were successful with two part numbers fixtured for the cell by MAUS. The original estimated savings for two part numbers was $288,715. A time study at the end of the trial period proved the annual savings were $296,285 for the same part numbers.”Asked if he would consider additional Italian equipment, Flaminio replied, “Yes, this is very dependable equipment. It’s operator-friendly and easily programmable with the MAUS bench programmer. New part programming can be accomplished offline, allowing maximum equipment uptime.”MAUS S.p.A. is an Italian manufacturer of a variety of grinding and riser cutting machinery for the foundry business and heavy metalworking machineries. MAUS’s North American market is growing. The company has stated that it is investing 6 percent of its gross revenue into R&D, to keep pushing the envelope for its customers with new and better methods of achieving faster throughput, more flexibility in manufacturing and higher margins through advanced automation and control.EU moves to integrate environmental and energy policies
Political interest and action are increasing in the European Union as integrated environmental and energy policies go on a timeline to reduce fossil fuel consumption, save energy and develop alternative sources. The EU wants to produce half of the energy needs for electricity, industry, transport and civil applications by 2050, and hopes to accomplish it through use of renewables and with carbon dioxide emissions.Sources include wind and solar energy, hydraulic energy, biomass, organic biofuels and hydrogen as fuel. The EU also underwrites a variety of supporting research programs.The Umbrian region is especially pro-active in programs created by the Italian Trade Commission (ITC), Region Umbria Offices, in conjunction with the Italian Ministry of Economical Development. Umbrian companies prominent in the photovoltaic sector should reach production objectives sufficient to cover 10 percent of what is installed and commercialized in Italy. This potential permits Umbria to penetrate international markets. The number of research centers in the territory enables a strong competitive stance.The ITC is continually adding promotional activities to promote Umbrian-based and other companies throughout Italy to foreign markets. As in this example of Umbria’s expertise in solar photovoltaic and solar thermal sectors, knowledge exchanges can take place internationally. Visit the ITC website (www.italtrade.com) for more information.Ice River Springs Co., Inc.www.iceriversprings.caAMUT S.p.A.www.amut.itAriostea SpAwww.ariostea.comMapeiwww.mapei.itGrede Iron Mountain Foundrywww.grede.comMAUS S.p.A.www.maus.itRelated Sidebar - Update on Global P.E.T.To read the article accompanying this story, go towww.automationworld.com/feature-6886.
Political interest and action are increasing in the European Union as integrated environmental and energy policies go on a timeline to reduce fossil fuel consumption, save energy and develop alternative sources. The EU wants to produce half of the energy needs for electricity, industry, transport and civil applications by 2050, and hopes to accomplish it through use of renewables and with carbon dioxide emissions.Sources include wind and solar energy, hydraulic energy, biomass, organic biofuels and hydrogen as fuel. The EU also underwrites a variety of supporting research programs.The Umbrian region is especially pro-active in programs created by the Italian Trade Commission (ITC), Region Umbria Offices, in conjunction with the Italian Ministry of Economical Development. Umbrian companies prominent in the photovoltaic sector should reach production objectives sufficient to cover 10 percent of what is installed and commercialized in Italy. This potential permits Umbria to penetrate international markets. The number of research centers in the territory enables a strong competitive stance.The ITC is continually adding promotional activities to promote Umbrian-based and other companies throughout Italy to foreign markets. As in this example of Umbria’s expertise in solar photovoltaic and solar thermal sectors, knowledge exchanges can take place internationally. Visit the ITC website (www.italtrade.com) for more information.Ice River Springs Co., Inc.www.iceriversprings.caAMUT S.p.A.www.amut.itAriostea SpAwww.ariostea.comMapeiwww.mapei.itGrede Iron Mountain Foundrywww.grede.comMAUS S.p.A.www.maus.itRelated Sidebar - Update on Global P.E.T.To read the article accompanying this story, go towww.automationworld.com/feature-6886.
Companies in this Article
Companies in this Article
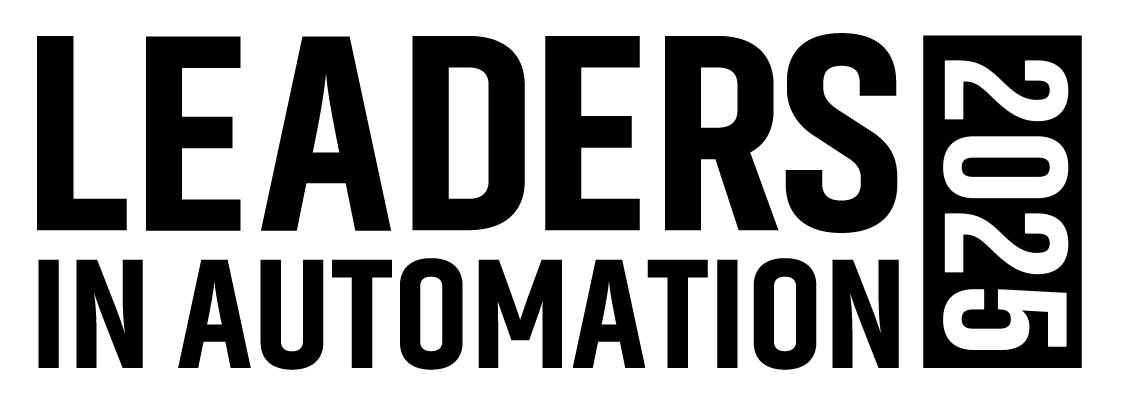
Leaders relevant to this article: