FDI: The Next Nirvana for Process Engineers
April 7, 2010
The promise of effortless sensor installation and network configuration, along with effortless diagnostics when something goes wrong, are all only one little specification away. And that specification, FDI, or field device interface, is due to be born soon. To thoroughly mix metaphors, heaven is but a step away for automation and instrumentation engineers.“Everyone wins,” says Terry Krouth, chief technology officer for Emerson Process Management, the Austin, Texas-based automation supplier. The intent of FDI is to specify uniform integration features within automation devices for process industries, across all major host systems, devices and protocols. “FDI will make it extremely easy for customers to integrate devices and systems. For suppliers, it means vastly reduced efforts in creating device drivers. Without FDI, device integration sinks back to a nightmare.”FDI is a joint effort by, well, just about everyone. Participants in the FDI Cooperation, which has in part grown out of the EDDL Cooperation Team, include FDT Group, Fieldbus Foundation, Hart Communication Foundation, OPC Foundation and Profibus Nutzerorganisation. On the supplier side, there are ABB, Emerson, Endress+Hauser, Honeywell, Invensys, Siemens and Yokogawa. And that is just a small sample of the names involved, as FDI includes end-users as well, among them Chevron and Shell.There are two realities driving the push behind FDI. The first is that since manufacturing began, when a group determines that it needs new equipment, the need is for something to perform a task, not necessarily for integration into any system. The result can be anything but integration.After all, if we ignore all-new sites or simple replacement of previous performers, the primary need is for some sort of new or newly-expanded functionality. Seamless integration is not a functionality. Integration into a multi-disciplinary, top-down system is not a functionality. Integration into a complex network is not a functionality. Stripped down to its bare bones, the functionality is for putting something to work for a specific need. Integration? Until very recently, plant-wide integration (let alone multi-plant-wide integration) simply was not practiced.The result is that there are a huge number of sites that are museums of historical solutions to historical needs. Some sub-systems in these are well documented and rational. Some, less documented, are at least capable of reverse engineering. But some require industrial archeology. Even when everything is being controlled on a rationalized 4-20-milliamp (mA) backbone or a foundation protocol, every part and parcel could easily have some wrinkle, some connector, some tweak that makes it (unfortunately) unique. A universal installer-fixer such as FDI would be the very definition of sweet.The second driver behind FDI is the continuing and rapid development of digital solutions. Every week, day and hour, new capabilities climb over the shoulders of earlier ones. The result is a combinatorial explosion, a situation in which, unless a device is standards-based, engineers have to expend a lot of sweat to harness all of the device’s capabilities and integration hooks.But, because FDI is still future tech, what is the automation engineer to do in the meantime? Says Charles (Charlie) Piper, program manager, systems DCS group for Plano, Texas-based vendor Invensys Operations Management, much of the drive behind sophistication in device and network configuration and diagnosis is due to asset management needs. “And these have evolved quickly,” he adds.“If a device is certified for Foundation Fieldbus or Profibus, or any of the current industrial standards, it should be relatively easy to hook up, if you don’t need a lot of depth to diagnostics,” Piper points out. “You need only three things for basic connections. First, you want consistent power, whether it’s power over the network or a device-specific power supply. Second is a device coupler, which conceptually is little more than a glorified terminal strip. Auto termination, short-circuit protection and other bells and whistles are available here. Finally, especially in hazardous areas, you need safety elements—explosion-proof enclosures, that kind of thing—that make the installation intrinsically safe.”Basic diagnostics are built into such devices, such as when a device falls off the network. “But more sophisticated diagnosis is demanded when you take an asset-management view,” Piper says. “You want more than just something that says that the DVs (data values from the sensor) are wrong or missing. The more you depend on an asset, the more you want to know why something has gone wrong and what the right fix might be.”More diagnostics means more electronics at the sensor. “When plants migrate from hand-held diagnostics,” Piper says, “mobile solutions provide more powerful capabilities, so you might get a USB (universal serial bus) port for maintenance connection to a laptop computer. Interface cards inside sensors have taken on greater and greater capabilities, and you begin to see network connectivity and sensor diagnostics migrating to a single, multipurpose card.”But, he points out, it takes more than intelligence at the sensor to make it all work. “Advanced diagnostics is tricky,” he observes. “The greater the capability for various levels of diagnosis, the greater the need for a user interface and diagnostic tools. What good is a network or a diagnostic if you can’t interact? And interaction is typically the domain of a system in the control room, or even higher in the manufacturing IT (information technology) system. You want visualization tools and asset-management tools.“There’s no doubt that the next step is FDI,” Piper concludes. “But you have to remember technological history, and that history tells you that everything changes. The future will bring even more wrinkles. All along, people have tended to think that you’re done when you’ve brought the current thing into operability. The real challenge to suppliers is to make it simple, and standards contribute to simplicity—but they don’t mean that technology stays constant. Every month, there’s something new, something more to fold into the automation scene.”Andrew Nolan, network and wireless sales consultant for vendor Honeywell Process Solutions, in Phoenix, agrees that time and sophistication has brought increased need for diagnostics. “Diagnostics are relatively new,” he says. “Wired Hart gives you the PV [process variable] and diagnostics, but most don’t wire up the diagnostics, because it’s still a new concept in DCS (distributed control systems). Foundation Fieldbus has diagnostics built in as well, but again, the diagnostic side doesn’t seem to have grown all that much. Contrast that with wireless, where diagnostics were built in from the start.”Part of the reason that wireless contained diagnostics was the need for specialized networking and instrumentation approaches. For one thing, basic implementation requires plenty of information on signal availability, continuity and strength. It was better to include the means for this kind of diagnosis in the device, where you could be sure the device’s needs are met, than to leave everything to random external equipment and teams.Plus, as Nolan says, “There was a hands-off mindset from the start. The first installations were for instrumenting areas that were hard to reach with a wire, which usually means hard to reach physically as well. So, very early on, device designs included remote ability to change parameters, upgrade firmware, perform calibration—in other words, do things without having to touch the instrument itself. Diagnostics is naturally a part of that approach, and diagnostics is a solid part of ISA100 devices.” (ISA100 is a wireless standard of the International Society of Automation.)While sites often justify wireless on the basis of installation costs, Nolan adds, “the real savings over time can be the benefits of proactive maintenance. You need pretty thorough diagnostics to keep tabs on the often small variations in performance that can foretell a problem before it brings a production system down—or lets you know that an instrument is about to fail before it fails.”Nolan pegs the rapid growth of asset-management systems to the much-bandied experience drain in automation. “Experience is retiring in record numbers,” he says, “so the remaining force has to do more and more with less and less staff. The only way to do that is with better tools. Asset-management systems, and all the diagnostics and interactive tools that come with them, allow engineers to stay on top of things proactively, and minimize unplanned outages.“It’s almost a good thing that wireless made a late entry into industry,” he says. “By the time wireless was becoming mainstream for us, all of the underpinning had become intuitive, from networking to distributed control to asset management. Meanwhile, the radio side had evolved into an intuitive technology, thanks to widespread consumer acceptance of wireless.“It’s an interesting thing about technology,” he says. “At first, a given technology is hard to use, hard to understand. But, as more and more people get involved, ways to simplify it become clearer, and equipment designers get better and better at making it easier to use.”Emerson’s Krouth agrees. “You can have all the features, all the bells and whistles, but if it’s not easy to use, it won’t be used,” he says. “Our challenge as a supplier is to step up to the value creation implicit in that statement—in other words, make our equipment as intuitive as possible.”Krouth is a strong FDI advocate. “When it was first proposed, I was skeptical,” he says. “FDI is very ambitious. But what turned me around was its broad support for protocols, from Foundation Fieldbus to OPC (an open connectivity standard) and beyond, and for suppliers—and everyone wants to do it at this point, Emerson, Siemens, Honeywell, Invensys, Yokogawa, everyone.”Ultimately, he believes, FDI’s strength is its device-driver approach. “Sensors with software can be thought of in the same way you think about computer peripherals,” he explains. “All of the features and power of a given peripheral is controlled by its device driver. That driver is a chunk of software that takes all the hardware requirements and hooks on the device side and handles timing and input/output communication, and maps it all into the operating system. In effect, FDI queries a sensor or instrument on the device’s operability. What diagnostics are available? What sensor capabilities? What process variables for each sensor? Once that information is gathered, FDI then presents it to the host system.”FDI is in essence a new device driver, enabling the simplest possible integration on any and all levels the user wants. “As sensor and instruments become more intelligent, with growing functionality and new levels of diagnostics, FDI software will quickly map everything new into an existing system” he says. “And, as long as the device contains built-in FDI descriptors, there’s no need for firmware updates, or card swaps, or fiddling inside the sensor housing itself.”One of the cornerstones of FDI development is cooperation among suppliers. “Interoperability is something of a mystery to most people,” Krouth says. “It begins with some sort of common standard, but the real work is in testing, testing, testing. Right now, interoperability has to cover a broad range of standards and protocols—Hart, Foundation Fieldbus and so on. And even if a new device is fully compliant with every current protocol, there is still the need for extensive testing with devices from competitors.”To effect this, Emerson sends new devices to competitors; competitors send their new devices to Emerson. “We work well together,” he says. “We’re a bunch of engineers, and the standards are clear. If we run into problems, we can figure out which component or device needs to change. There is a lot of effort behind the scenes.“Instead of a welter of protocols, FDI gives us a single, focused target to hit,” Krouth says. “Our benefit is the potential for quicker development of new devices. The end-user’s benefit will be the ability to integrate FDI-compliant devices with minimum effort.”In common with Piper and Nolan, Krouth emphasizes that intuitive device integration remains incomplete without an equally intuitive human interface. “Automation should be like an iPod,” he says. “I can buy an iPod, turn it on, and be downloading music and applications in minutes. The next frontier in industrial systems is to make them as easy as that to use.”Emerson has put together its Human Centered Design Institute, an internal resource for interface development groups across its range of offerings. “It’s progressing in conjunction with the Carnegie Mellon Usability and Software Architecture Project,” Krouth says. “Carnegie Mellon brings us years of research into how people interact effectively with computers, and we’ve done a lot of evaluation around how customers relate to our devices. After decades of industry focus on features and functionality, usability will be the next differentiator.”As standards development goes, FDI is proceeding at breakneck speed. But what about right now? “System integration is still engineering,” says Krouth. “Right now, much depends on training—you have to provide intensive training or bring outside resources to engineering groups to help them understand and configure all the options. The good news is that industry trends are on the customer’s side.”A model of those trends is the mesh technology in [the] WirelessHart [standard], he points out. In a mesh network, each device works in conjunction with an embedded network manager. When a new system first starts, each device has the ability to discover others within range, and the manager assembles a working network automatically. If something occurs to interrupt network transmission, affected components re-route transmissions within milliseconds, allowing process variables to once again reach the access points or systems that gather those variables.“The idea behind mesh is that the customer gets the benefit without the pain,” he says. “The same kind of automatic configuration needs to be carried into every network and device in our sphere. FDI is a key step in that direction.”
Subscribe to Automation World's RSS Feeds for Feature Articles
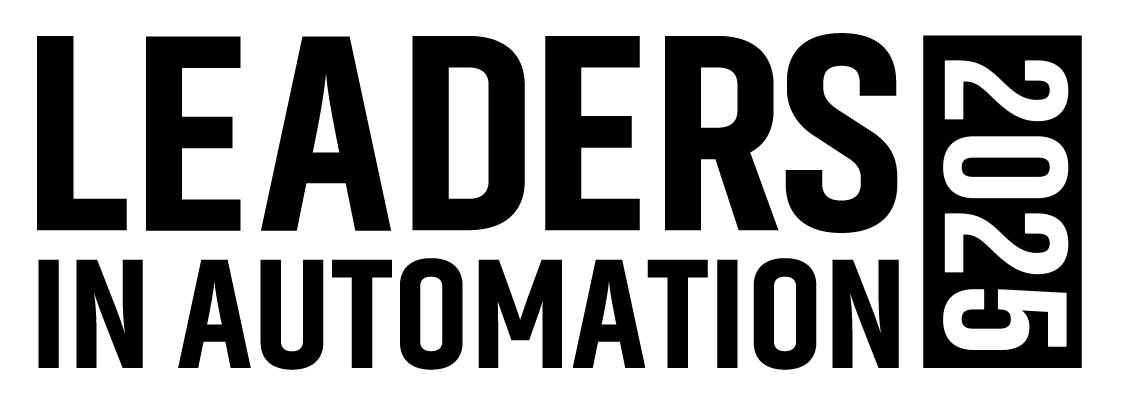
Leaders relevant to this article: