Wireless Control in the Process Industries: Blasphemy or Common Sense?
Feb. 8, 2010
“Blasphemy is an epithet bestowed by superstition upon common sense.” —Robert Green Ingersoll, American statesman and oratorNo one would equate the cautious nature of process engineers to superstition. After all, they are often dealing with things that can blow up and kill people, among other dire consequences, so an insistence upon absolutely dead-solid technologies that have been proven to work before installation in a plant is not only prudent, but essential.Yet, an idea that some might have considered almost blasphemous just a few years ago—that of using wireless technology for industrial process applications—is today gaining broader acceptance. Much of the recent focus is on wireless deployment for monitoring and data gathering based on wireless sensor networks (WSNs) using the WirelessHart standard, ratified by the Hart Communication Foundation (HCF) in 2007. Also gaining momentum is the ISA100.11a industrial wireless standard, developed by the International Society of Automation (ISA) and released last September.Early work is showing that these and other wireless technologies can be reliable in real-world industrial environments. And as users gain more confidence, many would agree that for certain monitoring applications at least, wireless is beginning to look like a common-sense alternative for the future, given the potentially huge benefits in wiring cost savings and the increased process knowledge to be gained.Mixed viewsNow comes what for many may require the next leap of faith—consideration and use of wireless for control applications. As part of the “Control” focus for this issue of Automation World, we decided to take a look at the status and prospects for industrial wireless control. It is not a topic that many process end-users are anxious to discuss openly, for fear of controversy, perhaps. And according to vendors, there is still a mixed bag of opinion in the field. “Most of our customers today are OK with the idea of wireless for monitoring. There might be some caveats on where they would or would not use it, but generally speaking, it’s considered an acceptable approach,” says Jeff Becker, global wireless business director for automation supplier Honeywell Process Solutions, in Phoenix. But users have a much less universal response when the topic turns to wireless control, Becker concedes. “You still get people who say, ‘No way. Never for control.’ ” Becker notes. “But you also get some customers who say, ‘Yep, I’m doing it right now,’ ” he adds. “And a lot of the customers are still somewhere in between.”Yes, according to vendors, wireless technology is already being deployed in control applications at some process plants. In fact, between 20 percent and 30 percent of all wireless products sold by Emerson Process Management, the Austin, Texas-based automation supplier, are today being used in control applications, says Bob Karschnia, Emerson vice president, wireless.But that statement requires some definition. There are different levels of control, of course, and neither Karschnia nor other supplier representatives are suggesting that wireless is close to being deployed for critical, high-speed control loops. Instead, users are building confidence in wireless technologies one step at a time, initially with monitoring, then by starting with the least critical control applications first and working their way up toward more critical control jobs. Early wireless control applications typically involve non-critical, open-loop control tasks, or closed-loop control applications with longer time constants such as tank level control, temperature control of heated jackets, or control of oil field steam injection for secondary recovery operations, says Karschnia.Brain checkSupervisory control applications in which operators can provide a layer of common-sense back-up in case of problems are among the early wireless candidates. “If you’re an operator in a control room and I’m sending you a data point that’s coming in on wireless, and you get to use your brain and make a decision on what you’re going to do, that’s a form of control, and I’m okay with that,” says an engineer at one process manufacturer who asks not to be named. “But for my critical control loops, I’m a long way from doing that on wireless. I don’t think any of the vendors are quite there yet.”Whenever process users are ready to try out wireless control, however, the standards are in place to help them do it.WirelessHart was designed specifically to support a wide range of process-industry use cases, from simple monitoring to closed-loop control using a mesh network topology. And last year, the Hart Communication Foundation published a White Paper, “Control with WirelessHart,” available on the HCF Web site, that addresses user questions on the topic. The paper discusses issues including sampling intervals, jitter and latency, and concludes that the overall control performance of a typical WirelessHart network is comparable to that of traditional wired fieldbuses.The ISA100.11a wireless standard, meanwhile, is aimed at the process industries and is suitable for non-critical monitoring, alerting, supervisory control, open-loop control and closed-loop control where latencies of about 100 milliseconds can be tolerated. As such, ISA100.11a—which can use either mesh or non-mesh topologies—is not intended for critical closed-loop regulatory control, says Wayne Manges, ISA100 committee co-chair, and a program manager at Oak Ridge National Laboratory, Oak Ridge, Tenn. Subsequent standards planned for the ISA100 family will address critical control.InevitableManges, for his part, believes that eventual widespread use of wireless technology for control is “inevitable.” Within the next two to three years, he foresees “test cases” using wireless control becoming common across industry. “If I run an oil refinery, I’m putting in my [wireless] monitoring network right now, and over the next two years, I will start running some first control over that network, though it will all be set-point control,” Manges says. “I think regulatory control, or tight, closed-loop control, is going to take longer than that.” Down the road though, Manges believes that even safety-critical applications will be entrusted to wireless. “I’ve told people over and over that I can demonstrate that wireless is more reliable than wired,” he says, by using various non-commercially available approaches such as multiple frequencies, multiple transmissions and multipath resistant technologies. Perhaps one harbinger of things to come is that Manges says he has even heard of one nuclear power plant operator that is already using wireless for a control application, though for a backhaul application, and not within the nuclear plant itself.Besides reliability, cyber security is another concern for users considering wireless control, vendors confirm. “They’re more concerned about doing control over wireless from a security point of view than they are about monitoring,” observes Emerson’s Karschnia. “If you’re just getting ahold of my outbound loop bearing temperatures on a fan, I’m probably not all that concerned about it. If, however, I’m controlling feedstock or an overflow protection system, those would be bigger concerns.”Honeywell’s Becker agrees that security surrounding wireless remains an issue for users, though, he adds, “I’d say it’s less of a concern now that it was even a couple of years ago.” Both Karschnia and Becker note that various security features built into their respective wireless platforms, including encryption, defense-in-depth procedures and others—as well as security testing done by third-parties—have generally been enough to allay users’ security concerns.Wireless redundancyAs industrial users begin taking a closer look at wireless, automation vendors are rolling out products intended to encourage and help customers move up the wireless-control learning curve. Honeywell’s OneWireless R120 solution introduced last June, for example, features a redundant wireless system gateway, which the company calls “a critical prerequisite for wireless process control.” By offering end-to-end hardware and radio-frequency redundancy from the wireless field instruments to the process-control network connection, along with “unique failure recovery features,” the R120 can recover in less than two seconds from any field-hardware failure, Honeywell says.The R120 is “ISA100.11a-ready,” awaiting the availability of conformance tests for the new ISA standard, according to Becker. He notes that the wireless redundancy is a feature that customers have been asking for. “Plants will control critical processes over wireless networks, which must be as reliable as wired networks. OneWireless is ready for these new demands with built-in features that enhance data availability and system reliability.” Emerson made a similar move last October when it unveiled full redundancy for its Smart Wireless system, available with the company’s DeltaV S-series controllers. Wireless is already deployed readily for monitoring, the company says, and customers have asked for redundancy for control, as well as for critical monitoring points.What are vendor plans for pricing on wireless instrumentation? See “Will Wireless Device Prices Come Down? The Vendors Respond,” at www.automationworld.com/feature-6502.Smart Wireless, which is based on the WirelessHart standard, already delivers 99.9 percent reliability, according to Karschnia. “So does having redundant gateways actually increase your communications reliability?” he asks. “In reality, not really all that much,” he says. “But what it does do is bolster a lot of confidence in people. And probably the biggest reason that people are a little bit concerned about using wireless for control is that level of confidence.” Another approach to building wireless confidence, or minimizing risk, comes from Opto 22, a Temecula, Calif., automation supplier. The company does not use IEEE 802.15.4—the Institute of Electrical and Electronics Engineers wireless standard upon which both WirelessHart and ISA100.11a are built. Instead, Opto 22 bases its wireless offerings on the ubiquitous IEEE 802.11 standard, known commercially as Wi-Fi (for Wireless Fidelity), which is increasingly finding use in factories and plants.Last April, Opto 22 introduced a version of its Snap PAC programmable automation controllers and input/output (I/O) systems that incorporate both wired and wireless networking options—based on the IEEE 802.3 Ethernet standard for the wired link, and on 802.11a, b and g, often commonly referred to as “wireless Ethernet,” for the wireless option.While “control” is defined differently by different people, Opto 22 customers are “certainly considering doing control with wireless,” says Benson Hougland, vice president, marketing. “But they’re not willing to step into that realm without some assurance that if it doesn’t work out, they’ve got a back-up plan.”And that, says Hougland, is the “beauty” of the Opto 22 solution. “Rather than making people choose between wireless or wired, we can give them a solution that offers both. If they elect to go wireless, and then find for whatever reason that something is not working as they expected, then they can go ahead and move to a traditional wired network—without changing out any of the hardware.”Not so fastDespite growing discussion about wireless control, some wireless proponents are quick to describe control as no more than a niche application for wireless in the near term. “Wireless control is beginning to start,” allows Hesh Kagan, treasurer and past president of the Wireless Industrial Networking Alliance (WINA), a consortium that promotes industrial wireless solutions. In industries such as wastewater management, “we’re seeing some wireless control in noncritical, loosely coupled control loops,” he observes. “But it’s almost an extension of how we do traditional SCADA (supervisory control and data acquisition).” Kagan, who is systems architect, New Initiatives, for automation vendor Invensys Operations Management (IOM), in Foxboro, Mass., says he is also seeing significant interest from users in deploying wireless as a redundant control communications path to existing wired links in safety-critical systems.But Kagan predicts that the biggest near-term applications for wireless will come in areas surrounding condition monitoring, asset management, material flow, maintenance and operator mobility. “That stuff I think is going to be almost ubiquitous in the next two, three or four years.” Use of wireless for “tight, closed-loop control” will happen, he says, but only “opportunistically” in the near term. Users will not replace today’s wired systems with wireless, so there will have to be a compelling reason to use wireless for control, he says. The only candidates for critical wireless control might be niche applications involving mobility, or applications in which “the cost of running wires is just too exorbitant…like maybe you’re trying to get a little process unit on the other side of the railroad tracks and you’ve got to bridge the tracks,” says Kagan. Even in a greenfield plant situation in which use of wireless could produce significant installation costs savings, “the marketplace is not ready for wireless actuation on a broad-scale basis,” Kagan asserts.All-wireless plants?Looking into the future, however, some vendors are willing to step further out onto the wireless limb. Honeywell’s Becker says that he gets questions from customers about whether there will ever be a completely wireless plant. “I think the answer to that is no,” he says, “because there are just some points in a plant that are so critical that you’re never going to want to take the risk.” Regulatory control points on critical high-speed processes such as catalytic crackers, for example, as well as safety shutdown systems, may fall into that category.“But I think the number of points that meet that definition are probably pretty low,” Becker continues. “Depending upon who you ask and what type of plant it is, we can pretty easily get ourselves to half the points in the plant going wireless today, and I think you might be able to increase that percentage even higher in the future,” he ventures. “But I don’t think it will ever get to 100 percent.”For more on the position of the Hart Communication Foundation on wireless control, see “HCF’s Ed Ladd Responds to Wireless Control Questions,” atwww.automationworld.com/webonly-6503. Emerson’s Karschnia goes further. “I think in the future, you’ll see plants move heavily toward wireless,” he predicts. “What the exact percentage is, I don’t know, but my gut instinct tells me that in the future, you’ll see 80 percent of the plant being wireless and 20 percent being wired.” Even 10 years from now, this is unlikely to be the norm, Karschnia concedes. “But I think you’ll see some cutting-edge people who are doing it.”The incentive, he says, will be financial, citing a typical 60 percent to 90 percent savings today for installing a wireless transmitter vs. a wired one. When multiplied across 80 percent of a typical large plant’s I/O points, that equals a reduction of tens of millions of dollars. “The cost savings associated with this are so staggering that customers will have to look at it, just because they’re saving so much money,” says Karschnia. Becker points out too that the savings from wireless come not just from reduced wireless installation costs. Plant implementation times can be dramatically faster without the need to run wires, he notes, reducing project risk. And by taking advantage of additional measurement points made possible by wireless technology, plants can run more efficiently and reliably.Once more plants do make the move to wider use of wireless, including wireless control, Becker figures that other plants will be forced to follow. “If all of your competitors are using wireless and it’s resulting in lower costs, higher reliability and greater profits to the bottom line, how long can you afford not to take advantage of that?”
Subscribe to Automation World's RSS Feeds for Feature Articles
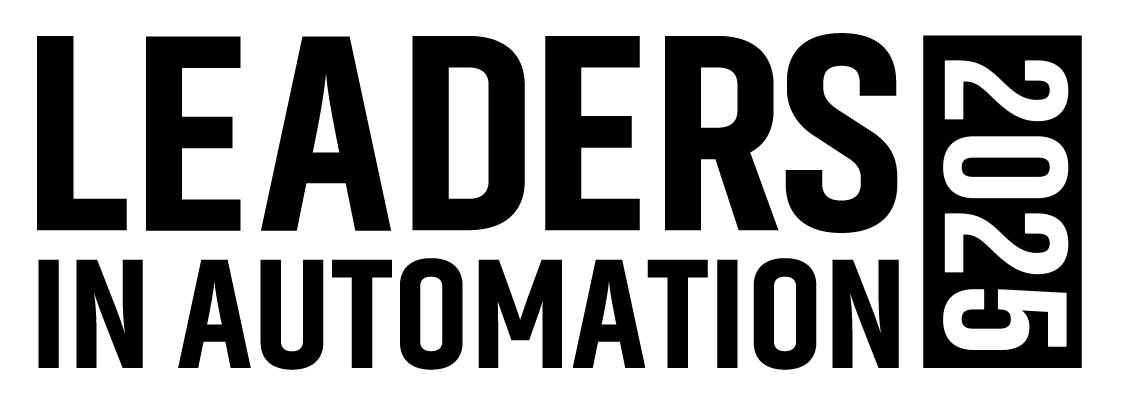
Leaders relevant to this article: