As applied to process sensing and instrumentation, wireless technologies seem to have reached the threshold of a calm middle age. The adolescent struggles for identity, the academic fights, the mind-numbing cramming to learn new ways and means, the two-steps-forward-one-step-back learning curves, all are fading into a comfortable glow of success.“So, where,” Bud Dungan asks, “has everyone been?” Dungan, President of Gastronics Inc., Bedford Heights, Ohio, began leading his company into its solid niche in wireless gas monitoring when wireless was nearly unknown in process settings. As an early convert to the technology, Dungan has worked his way through a number of radio technologies (and a number of listening post and network backbone schemes) since his first installation more than 12 years ago. His company’s products are found in wastewater treatment, oil-and-gas production and processing, chemical production, and pulp and paper. Gastronics sensors detect chlorine, hydrogen sulfide, ammonia, oxygen and volatile organic compounds (VOCs), as well as combustibility and flame.Today, Gastronics is firmly in the standards camp. Its first ISA100 device was released late last year, seen in an ISA100.11a demonstration tour of the Arkema Houston plant the day before ISAExpo 2009 on Oct. 5, 2009. ISA100 is a standard promulgated by the International Society of Automation (ISA).More accurately, the device offers ISA100.11a connectivity among several others. Its transmitter is modular, allowing users to select from a range of standards. Among the gas detector’s options: ISA100.11a 2.4 Gigahertz (GHz) Mesh, UHF/VHF radio (for ultra-high frequency/very high frequency), GPRS, (for General Packet Radio Service), cellular radio and low Earth orbit satellite connectivity.When wireless first crept into industry, of course, standards had no play, for a simple reason—no specific industrial standards were in place. “In 1996, we were freshmen in the school of hard knocks,” Dungan says. “We enrolled the day we got a request to add radio telemetry to our sensors for chlorine monitoring. The customer wanted to get out from under re-trenching and rewiring units on its periphery, because that meant spending hundreds of thousands of dollars. They had never tried our sensing strategies. We had never done wireless. It took six months.”The company’s move to standards had two root causes. First, research and development at Gastronics is averse to re-inventing the wheel. If someone else makes a better radio or network device, Gastronics will find ways to connect with it. Engineering the connection is far easier when the technical details are encapsulated in standards than when the interface must be built from the ground up. Second, beginning a few years ago, Dungan began hearing a plea for standards as he visited customer sites—customers were growing weary of roadblocks to network centralization.“And we kept hearing ISA100,” he explains. “In fact, it’s all that I heard. So, our first industry-specific standard product is ISA100.” That said, modularity of design will enable WirelessHart at some point in 2010. “Our radio manufacturer is working on WirelessHart certification,” Dungan says. “My philosophy is simple: You tell me where you want to be, and I’ll meet you there.” WirelessHart is another industrial wireless networking standard, which is promulgated by the Hart Communication Foundation.Dungan summarizes the situation: “We joined the wireless market a decade ago,” he says. “And for a decade, it’s been an emerging market. Well, it has finally emerged, thanks to standards.”How far wireless has moved beyond any teething pains is signaled in a project delivered jointly by automation suppliers ProSoft Technology Inc., Bakersfield, Calif., and Emerson Process Management, Austin, Texas. A mid-California upstream oil-and-gas-producer sought to instrument its steam pressures at two gas wells, part of a secondary recovery operation to obtain as much gas as possible. The installation was done in less than two weeks.At each well, Emerson supplied devices from the Rosemount 3051S series of instruments. These consist of WirelessHart-enabled, inline pressure transmitters, which send data via a smart wireless gateway to a ProSoft network device, an RLXIB-IHW-66 RadioLinx Industrial Hotspot, positioned near the wells. ProSoft rounded out the application by radioing data from this device to a second RadioLinx hotspot functioning as a data gathering station at the control room a mile away, via ProSoft’s Ethernet-based industrial IEEE 802.11 technology (a standard promulgated by the Institute of Electrical and Electronics Engineers—IEEE). “In most people’s minds, a mile is a stretch for 802.11,” says Jim Schliem, wireless project manager for ProSoft. In other contexts, 802.11 technology is known as Wi-Fi (for Wireless Fidelity), “but our industrial backhaul is designed for distance transmission.” In fact, ProSoft claims a 15-mile range for its 802.11 devices.Significantly, the only hands-on supervision in the application from either ProSoft or Emerson was a brief site survey performed by ProSoft to scope possible radio frequency (RF) interference and to ensure that radio transmissions would reach all points. “The installation was handled by the customer,” explains Bob Karschnia, vice president of wireless solutions for Emerson. “Both Emerson and ProSoft focus on straightforward user interfaces.”“If you think about it, customer installation is the only way to go,” adds Schliem. “The pressure transducer is in-line, and customers need to have control over when and where to break into the system for maintenance or upgrades. The Wi-Fi and gateway all had to be mounted on their field equipment, and they would want control over that as well.”Five years ago, a similar installation might have taken months of work by radio frequency (RF) and automation engineers. Then, to ensure reliability, days or weeks of off-line testing and prove-out might have been necessary to gain confidence that the system would not disrupt processes. Today, the pre-installation engineering is embedded in the devices. In part, this pre-design strategy works because a range of critical elements are locked down by standards, including network topologies, communications timing and clearly-defined functional layers. In part, too, technology is embedded in off-the-shelf network chips (Dust Networks, Hayward, Calif., supplies the self-organizing mesh radio technology in Emerson devices). In the final analysis, software and hardware—programs and chips—inject more and more intelligence in a given device, and more and more flexibility, driving down both costs and installation time. “Learning curves used to be a major element in wireless installations,” says Karschnia. “But for anyone coming to wireless at this point, most of the learning is over. The technology is generic enough to be applied to an increasing range of problems. It’s almost at the point where home-computer Wi-Fi is today—buy it, take it home, put it online.”Almost. There is, of course, still plenty to do in a production environment. Some of this work involves wrapping your mind around your chosen technology. If your radio technology is line-of-sight, for example, you will not have much luck if there are intervening woods or hills (or even heavily falling snow). Much work still must go into scoping and defining the solution. A systems approach is still better than a string of ad hoc or rogue installations; and a flexible, working system takes significant design time. But at least you no longer have to be an expert in networking, antennas or interfacing.Emerson cites a second installation, this one accomplished in two days. Calgary, Alberta-based EnCana Corp. sought better temperature data to maximize heat exchanger efficiency in its steam assisted gravity drainage (SAGD) oil recovery systems at its McMurray formation oil sands reservoir. Rosemount 648 WirelessHart temperature transmitters were added to the heat exchanger runs and tied into the plant’s distributed control system (DCS). The installation uses a wireless data feed to replace periodic manual checks of heat-exchange gauges. A continuous data stream powers a dashboard display of efficiencies, and trending helps flag scale build-up.As an Emerson spokesperson points out, “The self-organizing mesh network technology used in the EnCana installation reduces the effort and infrastructure necessary to set up a successful wireless network. Each field device in a self-organizing network can act as a router for other nearby devices, passing messages along until they reach their destination. As conditions change or new obstacles are encountered in a plant, such as temporary scaffolding, new equipment or a parked construction trailer, the wireless networks simply reorganize and find a new pathway.”Among the trends seen by long-time wireless advocate Jeff Becker, director of global wireless business for Phoenix-based automation supplier Honeywell Process Solutions, is a burgeoning interest in wireless for tank-farm applications. “The greatest movement we’re seeing is in these applications,” he says, “with remote wellhead monitoring and equipment health monitoring as runners-up. And we’ve noticed a lot more interest in ISA100 globally, now that the standard is complete.”As might be expected, the greatest level of interest in wellhead monitoring comes from developing regions, including the Middle and Far East, where the majority of new wells are coming on line. Similarly, interest in tank-farm upgrading is far more prevalent in the United States and Europe. For the latter: “Companies with older tanks often have a dual need—they are combining routine maintenance upgrades with new safety measures. As for equipment health monitoring interest, right now you find that restricted to large multinationals,” Becker says. “They tend to have the most sophisticated plant maintenance approaches, and they’ve taken the time to document the savings in good reliability and maintenance practices.”There are some interesting wrinkles involving hybridizing or mixing-and-matching technologies in both devices and infrastructures. While it is not yet fully certified to be ISA100-compliant (the term used for it today is “ISA100-ready”), Honeywell Enraf’s new SmartRadar FlexLine device combines both IEE802.15.4 wireless communications with a radar tank level gauge. “It was a challenge to put both a radar radio and a communications radio in the same package,” Becker says. “But it adds high precision compared to conventional level gauging methods. That brings it in line with the growing need to be absolutely certain about hydrocarbon and chemical quantities while they’re in the process stream.”For the network infrastructure itself, Becker cites a growing need for multi-protocol routing. “There’s a growing need for a centralized network that can control and isolate data from field instrumentation, traffic from mobile workers with wireless devices, and engineering traffic from mobile personal computers,” he explains. “The critical need is to sequester each type of communication. Engineering needs high-bandwidth access and firewalling to engineering servers for documentation and drawings. Sensor traffic has to connect with the DCS at a much lower bandwidth, but no less security. You need to make sure that data enters and exits the system at the proper layers and with the proper safeguards.”We are likely to see more and more multi-function, multi-network backbones and devices as wireless sensors and instrumentation progresses. There might be more single-minded solutions if, first, existing industrial sites simply packed up their old stuff and bought all new; and, second, all the radio standards melted down into one single gold standard. But, neither one of those things is likely to happen. Even the new standards are resisting amalgamation. The proposed inclusion of WirelessHart in the ISA100 family of standards (ISA100.12) has withdrawn into disquieting silence, suggesting that the disparate underlying technologies are, well, disparate.But the forces for diversity are extremely strong. Industrial equipment runs for decades. Newer and better models of anything used in production, with the exception of their electronics, remain significant capital expenses. While “capital expense” is a particularly bad word in a bad economy, it is never undertaken lightly, even in boom times. The result at most facilities is a mind-numbing assemblage of disparate generations of equipment and control tactics.Then, too, no matter how much age they have on them, control structures, network protocols and device standards generally boast one or more specific strong points. Their installations tend to emphasize those strong points and work around the weak points. Understandably, engineers are slow to replace either the successes or the work-arounds when it means reining in a completely different set of strong and not-so-strong elements.There is at least a partial answer. When everybody wants something different, configured in some different way, the answer is proliferation of options. Long before wireless was added to the mix, instrumentation/sensor purchase specification was already an exercise in configuration—sensor types and ranges, isolating diaphragm materials, mounting profiles, housing types, flange geometry…and this barely scratches the surface.When it comes to the radio, the same modular approach applies. Here, because so many variables fall out of a given technology choice, you have to add a user interface and incredibly flexible, software-controlled electronics. Want WirelessHart? Plug the WirelessHart module into the main board. All the hooks into and out of the sensor voltages, all the data rates and bursts, all the protocol layers specified under WirelessHart come into play. Want ISA100? Plug in the ISA100 module. Want both? Well, maybe not.The next few months will see continued introduction of a growing stream of new wireless sensor and instrumentation devices. It remains to be seen where the emphasis flows, since economic recovery will be a critical contributing factor. Will it be primarily maintenance-driven replacement across open ground, where trenched wiring is deteriorating? Primarily new installations in developing areas? New devices in response to new ideas? Whatever the final tally, 2010 should be one of the most exciting years in industrial wireless.
Subscribe to Automation World's RSS Feeds for Feature Articles
Sponsored Recommendations
Sponsored Recommendations
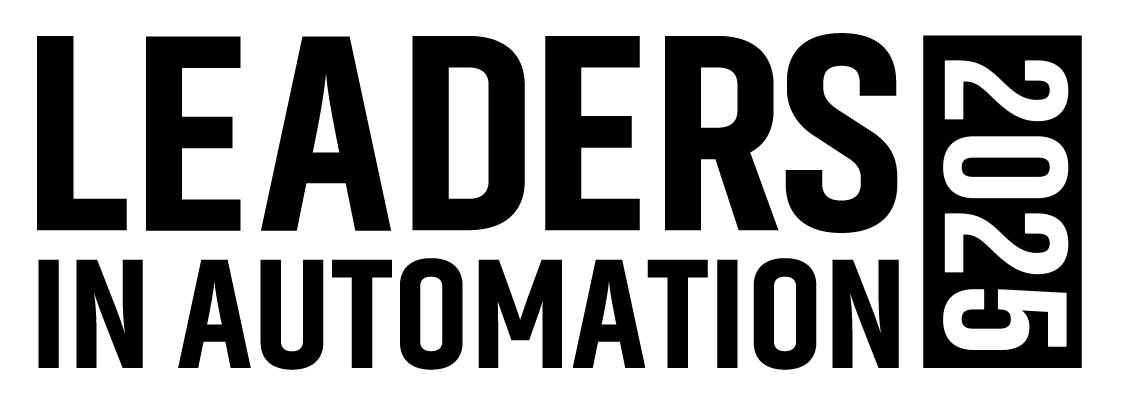
Leaders relevant to this article: