Adco Manufacturing, Sanger, Calif., makes hand and auto-load cartoners, carton formers, sleevers and other packaging machines. They also make decisions about the future direction of the packaging industry. As Adco sees it, that future involves the triumvirate of automation, standards and connectivity.
Colin Warnes, mechanical engineering manager for Adco, notes that the company prides itself on building machines for a wide range of needs. But the value proposition behind these linked concepts seems clear and compelling, and Adco has acted on it.
“All of our upper-end machines incorporate EtherNet/IP, for our own communication between the HMIs (human-machine interfaces) and the PLCs (programmable logic controllers), occasionally some positional I/O (input/output points),” notes Kevin Gilpin, Adco’s electrical engineering manager. Ethernet’s speed and bandwith enables this communication, letting needed data about each connected point flow upward while still allowing operating instructions to flow to the machines—an advance over fieldbus technologies that have previously played such a vital part in automation. The advantages in terms of reduced downtime and greater operational efficiency are manifold. As noted by Robb Clarke, Ph.D., an associate professor at Michigan State University’s School of Packaging who has been involved with packaging for decades, “The more information you have, the more agile you can be.”
Putting a real-world face on these advantages, Gilpin observes, “For one thing, it allows someone to sit in their office and troubleshoot without having to drag a laptop down to the plant floor and connect up. This not only saves you time and money, but in practice, it means that a lot more data is available.”
It is also a potential benefit for the original equipment manufacturer (OEM) as well. “With remote access, I can go online and troubleshoot a customer’s machine. This is quicker and cheaper for both of us than sending someone out on a service call.”Keep out
Sounds like a win-win proposition, one that has received its fair share of ink in trade magazines as well as OEM and automation vendor press releases. Is it catching on? “No it’s not, unfortunately,” says Gilpin. “Most customers really don’t want outsiders in their network. We’ve espoused the idea of remote maintenance for a long time, but most corporate IT (information technology) departments still won’t have anything to do with it.”
Granted, a somewhat larger number of companies are performing remote diagnostics and preventive maintenance on their own, within the secure confines of their IT department walls, but the potential of the technology remains underutilized. The same can be said for what is arguably the key standards initiative in packaging today: PackML.
“We build our machines to PackML guidelines,” says Gilpin, referring to the Packaging Machine Language developed by the OMAC Packaging Workgroup (OPW). OMAC, by the way, stands for the Organization for Machine Automation and Control. PackML sets out a common machine language for automated machines in order to ease the integration of equipment from different vendors, simplify customization, lower engineering and training costs, and reap other benefits that occur when packaging machines are easier to program, link and communicate with. The guidelines were adopted in August 2008 as part of the International Society of Automation’s ISA88 standard.
“PackML can make a great deal of machine-level data available to the customer’s higher-level systems,” Gilpin observes. That’s because the standardized terminology makes it easier to connect packaging machines to enterprise resource planning (ERP) and other higher level systems, facilitating remote troubleshooting and allowing users to drill down to the level of detail they need. The result, typically, is greater machine and packaging-line efficiency.
“However, from my experience, few people are using it.” Gilpin’s colleague, Colin Warnes, largely concurs, saying a great deal depends on the size of the company. “At the large multinational companies, the engineers are on board with it, they love the concept. At the medium-sized companies, they usually know very little about it. It’s simply not on their radar yet. That’s something OPW is working to change.”
Warnes characterizes the current state of PackML implementation as a “which comes first, the chicken or the egg” proposition.
“You need the customers to request it for it to get implemented among the OEMs, but the OEMs also have to offer the standard on their machines, and to offer it for free.” Warnes, who has served on the OPW executive committee as a machine builder representative, sketches out what he says is an all too common scenario. “A customer requests that their new machine be PackML compliant. The customer decides they don’t want to pay extra for that feature, so they pass on it. So the customer never achieves full implementation of PackML standards and the OEM never fully integrates PackML into their way of life.”Commitment
Far better, he says, is for OEMs to bite the bullet and commit to PackML, making it available at no cost. Customers then receive more value for their dollar, and, after the initial pain and expense of mastering and implementing the standard, OEMs can begin to benefit from reduced engineering and customization time and cost, easier connectivity and faster time to market.
Warnes and Gilpin agree that there is a learning curve associated with PackML. “It hurts for the first six months or more, depending on the electrical engineers who are working on it, but once the standards click with those particular engineers, they really fall in love with the robust nature of the logic and the fact that it makes it easy to add modules.”
One of the largest of the multinationals, The Procter & Gamble Co., has recently taken a giant step toward easing that learning curve. They’ve unveiled a free, downloadable guide to help companies efficiently implement PackML. The guide, together with software and help files for PackML implementation on the ControlLogix platform of Rockwell Automation Inc., Milwaukee, is available on the OMAC Web site. Many other automation providers are following suit, and P&G implementation guides with their software and help files should soon be available for downloading from the OMAC site.
“Companies don’t have to do it alone,” stresses Gilpin who speaks approvingly of the software help (“templates”) available from the major automation providers. “Implementing PackML on your own, without help, can be a daunting task, but because we’re a Rockwell customer, Rockwell helped us out, got us a good set of templates to work with. Most of the other automation vendors can do the same. So work with your primary supplier to get yourself a set of templates.”
“Optimizing packaging lines is a major focus today,” agrees Leo Petrokonis, business development manager, packaging industry, for Rockwell, “and getting the real-time data that remote connectivity makes possible is critical in order to optimize the performance of those lines.” He also insists that the new technical possibilities are reshaping our ideas about concepts like optimization. Why, for instance, be content with simply doing a better job of what we’ve done in the past? Why not use the new technology in new ways?
For example, operator instructions or machine manuals are a humble but important part of efficient machine operation. “Sometimes these are printed, sometimes they are downloaded into an operator interface, but wouldn’t it be nice if an operator or an engineer who needed to consult this material, and quickly drill down to a very specific part of it, could simply go to the Web and find it on the OEM’s Web site?
“Conversely,” Petrokonis continues, “think of an OEM who has 500 machines out there and he just made a change to his manual. Instead of making that change 500 times, why not just do it once, on the Web? It saves the OEM money and it brings the information instantly to the people who need it. The majority of OEMs are just starting to realize the power that’s inherent in this new level of connectivity.”Convergence
It is a level of connectivity that opens the door to what Petrokonis and others are calling convergence. This, he says, has two different components. First there is network convergence, with multiple device level networks converging into a single Ethernet network integrated with the enterprise level.
This is still a work in progress, and in some quarters still highly controversial. Not, however, for packaging machine builders like Itec GmbH, Beckum, Germany. Itec’s core business is building automated systems for cutting and handling ready-to-eat sausage products. “We sell the systems as stand-alone solutions or as complete plants linked via conveying and handling facilities,” explains Olaf Kahl, Itec’s sales and project manager for automatic and ergonomical systems. “We can assemble the plants from proven components, as if from a kit, to suit the customer’s individual wishes.” And part of the success of these systems stems from their reliance on remote maintenance and Ethernet.
With Itec’s Logo-Scan system, for example, the surface of the sausage product is detected by a line-scan camera, then positioned accordingly and subsequently printed with the date of production and the expiration date. An embedded personal computer (PC) from Beckhoff Automation, with Beckhoff’s TwinCat automation platform, controls the system. Beckhoff’s U.S. headquarters are in Burnsville, Minn. “The use of the embedded PC gives us many advantages,” says Kahl, such as plant-level documentation.
The embedded PC and the Itec-specific touch panel communicate with one another via a DVI/USB (digital visual interface/universal serial bus) system interface. “Various possibilities for remote maintenance assist us in reducing service expenditures,” notes Kahl. “To this end, we integrate the machines in superordinated (multiple unit) systems via Ethernet TCP/IP.”
All sensor data is acquired and evaluated via EtherCat. The system’s servo drives support EtherCat,says Kahl, and are driven directly with no loss of performance. All data points are integrated in the EtherCat bus system via EtherCat terminals. “The system is not only more powerful than before, it is also simple to configure,” says Ralf Wiesbrock, Itec’s product developer for automation equipment.
The other aspect of the convergence that Rockwell’s Petrokonis speaks of is cultural, and this, for many North American companies, is proving harder than the manufacturing aspect. To make it work, he says, “you need a robust infrastructure to ensure remote access to the machines on the floor while also ensuring security. That takes careful planning, and the IT guys, the enterprise-system-level guys, have to be involved in this. These groups have different outlooks and some plants are still struggling with this.”
The Wonderware business unit of automation vendor Invensys Operations Management (IOM), in Lake Forest, Calif., seeks to tap the power of connectivity from a slightly different angle, while providing a pre-engineered pathway to enterprise-level integration. “Because there are so many OEMs providing packaging lines, it’s the nature of the industry that they are, typically, disconnected from one another,” notes Maryanne Steidinger, commercialization director, operations & information portfolio, for IOM.
Wonderware’s PackML-compliant operations management software product called Industry Application for Packaging seeks to bridge those gaps by running atop existing systems and providing reporting, alarms and data visualization for the packaging operation as a whole. Moving from the general to the specific, Steidinger zeros in on one of the concrete ways in which greater connectivity, in this case through the mechanism of her company’s product, can improve efficiency.
“You can look at uptime for different lines or different machines at specific times of day and make some correlations. You might find, for example, that one line is plagued by micro-stoppages—little glitches that cause the equipment to stop for just a fleeting instant. By identifying precisely when that happens, you can begin to figure out why it happens.”
Looking more closely, you might find it’s a case of wrappers getting briefly stuck and needing to be yanked free. Is it because of a specific vendor’s packaging materials, or perhaps because of the viscosity of the product at that point? “These are stoppages that would be invisible to other forms of monitoring except to a skilled operator or engineer standing right there watching. Knowing that they are occurring allows you to discern their cause and correct it.”
Coda is a musical term standing for a short segment that, while formally distinct, nonetheless serves to both round out and summarize what precedes it. Perhaps MSU’s Robb Clarke provides one when he observes that, “Essentially, machinery mechanics haven’t changed much in 50 years. Sure, there have been improvements, but the interior functions are still largely based on cams, levers, gears, chains and so on. What has changed is control and the function of control, and that is where the greatest improvements are taking place.”Related Sidebar - Automating a Beverage LineTo read the article accompanying this story, go towww.automationworld.com/feature-6347.
Subscribe to Automation World's RSS Feeds for Feature Articles
Sponsored Recommendations
Sponsored Recommendations
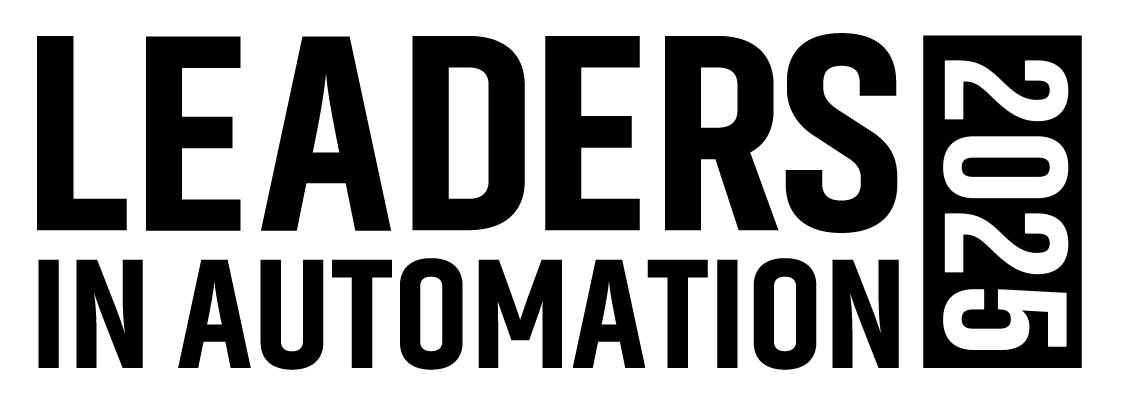
Leaders relevant to this article: