When thinking about how to best address the problem of plant downtime, one must first identify the causes. The first thing that comes to mind is machine failure; something on the line breaks, bringing production to a shuddering, unceremonious and potentially expensive halt. Despite being the most significant issue, however, machine failure is only one of many.For Raleigh, N.C.-based Pepsi Bottling Ventures LLC (PBV), the primary problem was product changeover. PBV, North America’s third largest manufacturer and distributor of Pepsi-Cola products, makes and ships more than 100 different soft drink products from 27 bottling and distribution facilities in six states. With such a wide variety of products being produced, smooth switchover from one to another is vital to each plant’s productivity. The PBV facility in Nampa, Idaho, was a particular sore spot. Built in 2005 and acquired by PBV earlier this year, the plant employed a mix of legacy and new systems, leading to waste and downtime problems. A home-grown data-collection system designed to accommodate the legacy equipment didn’t play well with the newer gear, while operators relied on manual methods to track downtime, recording it on clipboards during their shifts. Without real intelligence about the process, engineers estimated that the changeover process took about an hour, which wasn’t bad, but could be better. To tighten things up, the company rolled out a performance-management-and-downtime-tracking system from Lake Forest, Calif.-based Wonderware, a unit of Invensys Operations Management. The first thing engineers learned was that their changeover process didn’t take them 60 minutes...it took them 90! And that was unacceptable.According to Scott Jamison, PBV’s vice president of engineering, the plant used the Wonderware system to identify the primary constraints and their root causes, and found that the most critical bottleneck was in the filler process. Correcting this issue reduced changeover time by up to 45 minutes and had a cascade effect, with additional savings realized in raw materials and packaging. Efficiency on the filler line increased by 10 percent.Accurate data“The main thing we are trying to do is get data that is very accurate,” says Jamison. “What is the downtime and what is the cause? By taking information directly from the machines, we are now getting [this rich, reliable information].” For example, he adds, they now get a view of all the micro stops—interruptions of less than a minute that nobody had time to write up in the past and were therefore invisible—that occur every day and take action to correct them.“Now that we have taken care of most of the low hanging fruit, we are able to dial in on the most minute things and make informed decisions to improve things. It is helping us evaluate not only the machinery but the people who are running it. We can now see very quickly if an operator is in the wrong position. Can we reassign him or give him more training to make him more effective? All of that ultimately leads to less downtime,” concludes Jamison.Schwäbische Maschinenwerkzeuge GmbH (SW) in Schramberg-Waldmössingen, Germany, is doing something similar, but with a much closer tie to the maintenance process. The machine-tool maker has rolled out ePS Network Services, a solution from Siemens’ Motion Control Systems group, which provides an Internet-based remote condition monitoring service. Each of the roughly 160 high-performance, multi-spindle machining centers the company makes for the automotive industry each year comes with the service as a combined offering. ePS constantly mines operational data directly from the equipment and analyzes it to provide useful insight and decision support for not only the maintenance group, but also production and management. Should a specific condition be met—an indicator of an impending failure, for example—an alarm can be issued and corrective action taken to prevent the problem from escalating into an incident that interrupts production. According to Peter Siegel, the champion for online services at SW, ePS simplifies and accelerates maintenance, eliminating downtime in the process. “The maintenance staff no longer needs to wait for alerts and updates, because they can also work with the data themselves.” While the initial value to the maintenance function is obvious, Siegel stresses that once you have the information, you can subject it to numerous analyses to get a clearer picture of the business and generate important value for production and management teams.For example, the production team may want to know how often a given operation is selected; or how long set-up takes; or how long the machine is stopped without a malfunction; or how long it takes to respond to a malfunction. Says Siegel, “All this data makes it possible to determine the causes of qualitative problems, why processes are unstable or why the number of produced parts falls suddenly. Ultimately, a process optimization and/or a productivity increase can be achieved.” At the management level, visibility into what’s happening on the shop floor translates into better strategic decisions in a number of areas. Because they have a better picture of production, managers have a better idea of the total cost of ownership (TCO) of their capital equipment investments and the return on those investments. Additionally, they can be proactive when it comes to issues such as spare parts. If the condition monitoring informs you that a given number of parts are going to wear out in three months, you can arrange to have them on hand ahead of time and schedule their replacement rather than waiting for breakage, and then waiting for the parts to be shipped. “This is really moving from a preventative maintenance model into a predictive model,” says John Cruthers, a spokesperson for Siemens. “If you do that effectively, you can diagnose problems before they occur and avoid the problem in the first place.”Three modelsBill Polk, a research director at Boston-based AMR Research Inc., identifies three primary maintenance models. In addition to the aforementioned predictive maintenance, you have reactive maintenance, which basically means you run the machine until something fails and then scramble around for the right parts and people to get the machine back up and running as quickly as possible. This model, still the most common, is the most expensive in terms recovery time and hard dollars. The third option is planned maintenance, through which you schedule work based on the projected lifetime of the given machine or part. It’s vastly superior to being purely reactive, but the drawback is that you may be taking components out of service that are perfectly good and don’t need replacement or maintenance. You will also miss unforeseen failures due to defective parts. The predictive model is clearly Polk’s Holy Grail and he recommends companies adopt it—usually as part of an overall enterprise asset and maintenance (EAM) program—if at all possible. “People want to improve their return on assets,” says Polk. “They look at these assets not just as costs, but investments that have to show ROI. You also have to consider the aging workforce. With this economy, people aren’t retiring as they were expecting, but manufacturers are still expecting a real problem to come up over the next five years. They also want to improve the efficiency of their maintenance departments.” Polk identifies a number of benefits a decent EAM approach can deliver. “Maintenance expenses can be reduced by 25 percent. You can reduce breakdowns by 75 percent. Asset utilization can go up 15 percent to 20 percent. You can reduce working capital with MRO (maintenance, repairs and operations) inventory by 10 percent to 15 percent,” he says. “It’s a very highly evolved form of maintenance.” An evolution was exactly what DP World Southampton was looking for when it rethought its approach to maintenance. DP World Southampton is the second largest container terminal in the United Kingdom. The 200-acre facility relies on 14 ship-to-shore gantry cranes, one mobile harbor crane and more than 100 straddle carriers to tranship thousands of cargo containers carrying everything from perishable foods to dangerous chemicals from all over the world from ships onto trucks and trains and vice versa. “Every time a crane breaks down, it slows our throughput and ultimately costs us money,” says David Bowers, DP World Southampton’s engineering planning and quality manager. “We realized that if we could find a way to be more proactive in our maintenance work, we could keep the terminal fully operational for longer periods—reducing delays and boosting efficiencies.”DP World Southampton was relying on a legacy computerized maintenance management system, which was not well adapted to the company’s business processes. According to Bowers, the old system had never been correctly configured to meet the operation’s needs. “As a result, we found it difficult to manage our maintenance workload intelligently. We wanted to ensure that we were servicing our equipment often enough to meet our ISO 9001:2000 quality standards and to comply with health and safety regulations, but not so often as to create unnecessary work.” The solution came in the form of IBM Tivoli’s Maximo Asset Management system. Going preventativeWith the new solution in place, the operation has been able to move from a break-fix maintenance model to a more preventative approach. Technicians now log maintenance reports directly into the system as they work, so there is less risk of a job being forgotten or entered incorrectly. As well as minimizing mistakes, this also helps to improve traceability—helping with audits, inspections and regulatory compliance.“We have a strict workflow now that governs all planned maintenance,” adds Bowers. “Each job starts out with a Maximo work order—and you need an order number to get spare parts. This makes it much easier for us to keep track of inventory and ensure that the right parts are used for the right jobs.” Since the deployment, Bowers has noted a 10 percent increase in the amount of preventative maintenance being done and a corresponding 10 percent reduction in actual breakdowns. “You’ve definitely got an idea whose time has come,” says John Boville, market segment manager for automation supplier Schneider Electric, with U.S. headquarters in Palatine, Ill. “You’re dealing with a mind shift here. I don’t think people really understand what’s at stake when a machine stops running. We are talking about big, big benefits. Instead of fixing something after you have a catastrophic failure, have a system that’s smart enough to tell where to go to avoid the breakdown in the first place.”
Subscribe to Automation World's RSS Feeds for Feature Articles
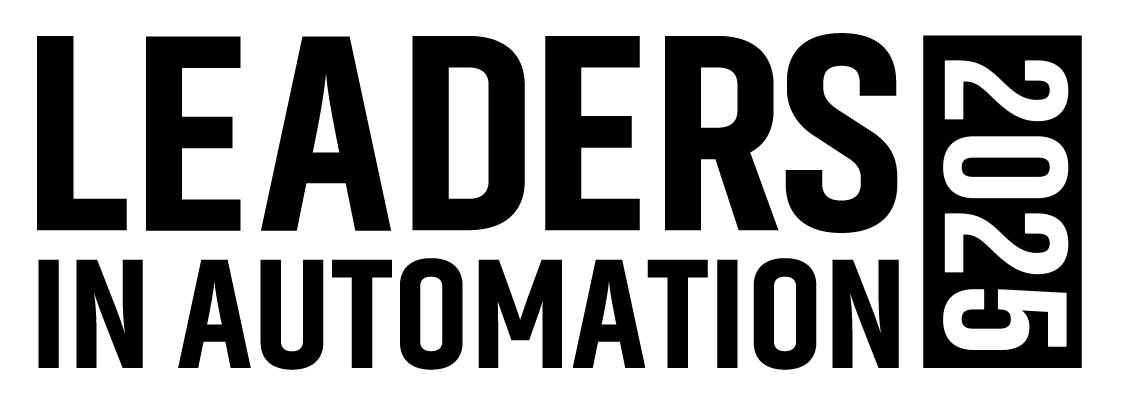
Leaders relevant to this article: