Sustainability is the capability of complex systems to maintain themselves over time. Manufacturers attempt to operate sustainable production lines, to work without creating unnecessary waste products and, when possible, to recycle.
Interest in resource-saving, environment-protective practices abounds in the United States, including proactive moves by the government. The U.S. Dept of Commerce (DOC) has defined sustainable manufacturing as the creation of manufactured products that use processes that minimize negative environmental impacts, conserve energy and natural resources, are safe for employees, communities, and consumers and are economically sound.
The DOC Manufacturing & Services unit has launched a Sustainable Manufacturing Initiative
(www.manufacturing.gov/sustainability) and Public-Private Dialogue to identify American industry’s most pressing sustainable manufacturing challenges and coordinate public and private sector efforts to address these challenges.
Saving forests
Always a strong advocate of sustainability, the Italian company PAL S.r.l. (www.pal.it) leads in the treatment of recycled wood, a business started in 1982 (with escalation of fresh wood prices), installing plants first in Italy and later worldwide.
PAL, founded in 1978, fabricates machines to treat and process fresh and recycled wood for particleboard (PB), medium density fiberboard (MDF) and oriented strand board (OSB) panels used in the production of pellets and biomass preparation for energy plants.
With more than 3,600 machines at work worldwide, PAL has installations in approximately 20 North American plants. The largest U.S. customers include SierraPine, Flakeboard and Louisiana Pacific Corporation.
As a leader on the wood-based panel market with a range of machinery, PAL supplies turnkey solutions for wood panels, pellets and energy production, including products from the log yard to the forming-pressing line: feeding, chipping, crushing, extracting, screening, cleaning, sifting and desanding systems. For feeding lines of energy production plants, PAL machinery improves movement of material enormously, from the first volumetric reduction, through separation, classification, and finally through cleaning wood chips and biomasses from agricultural sources.
The excellent size separation obtained from using the latest-generation roller graders and new technology to select and classify by density, even when extra-fine fractions are needed, allows use of these materials with an extremely high and constant energy yield.
In North and Central Europe, North America, Brazil and elsewhere, while more trees are being planted than ever before, the cost of obtaining those resources, as well as environmental issues, have caused most companies to look for options. The only proven option is urban waste wood (urban forests), of which most is attractively priced and, in some areas, can be collected free of charge.
In 1986, expertise acquired in chips cleaning enabled PAL to become the first company to produce integrated recycling systems for urban wood waste. With more than 200 plants that recycle any variety of urban forest worldwide, PAL leads the market.
The company recently entered the field of biomass energy production with the supply of large-capacity plants to big multinational groups. Its treatment of wood biomasses in wet areas includes:
■ Moving/loading/unloading systems;
■ Machinery for the first volumetric reduction;
■ Machinery for the separation of ferrous and non-ferrous metals;
■ Separation with roller graders which accurately select differing fractions;
■ Dry cleaners to remove pollutants;
■ Machinery for the second volumetric reduction; and
■ Gravitational and centrifugal separators to clean and separate fine particles.
In energy production plants, a key requirement is regular/uniform medium-fine particles so that fuel can be introduced into a burner at a constant rate, as well as the production of heat from the immediate combustion of the particles, and the consequent optimization of the average yield of the system. Excellent selection and elimination of heavy contaminants from the process without the use of water, but with efficient dry cleaning systems, is therefore essential. By means of its Centrifugal Cleaner and gravitational selectors, PAL guarantees effective removal of the finest silica.
New patented systems include a new-generation Air Chip Cleaner designed to clean the recycling wood chip with more than 95 percent efficiency; a Desander developed from the simple and essential idea to save energy and maintenance costs in plants by removing silica/fine pollutants from the dust fraction; and Metal Killer, an innovative machine to replace old equipment for metal removal that separates mechanically (very low power consumption), in only one stage, all kinds of metals such as iron, stainless steel, aluminum, copper and brass from the wood chip flow.
These machines are included in the Cleaning Tower, the system for cleaning recycling chips, which offers low content of wood particles in reject fractions; wood saving by cleaning the very fine fraction; reduced installation footprint; reduced absorbed power to 5-6 kW/ton; reduced maintenance costs; and low investment with higher, long-lasting performance.
Saving resources
Sacmi Imola S.C. (www.sacmi.com) is a leading designer and producer of industrial technologies and systems, specializing in machines and complete plants for ceramics, beverage and packaging, processing and plastics.
Sacmi’s U.S. customers include giant corporations like Pepsi Cola, as well as businesses in specialized industries in compression molding technology—Silgan, Kerr, and Rexam—and others in ceramics, including American Marazzi, Dal-Tile Corp. and Florim USA. A large low-impact, high-efficiency press (7,500 tons) was recently delivered to Crossville Ceramics in Tennessee.
A company-wide commitment to sustainability is reflected in Sacmi’s H.E.R.O. program.
Reduced availability of traditional energy sources and increases in cost make it vital for strategic development to identify the best way of managing production processes and optimizing resources. To meet this need, in environmental and economic terms, Sacmi founded H.E.R.O., High Efficiency Resource Optimiser.
This study and research laboratory is dedicated to developing innovative technologies for achieving the greatest possible resource savings in every phase of the production process. Special applications developed as part of the H.E.R.O. project enable energy consumption of the main machine in the installation to be reduced by more than 20 percent on average. The economic benefits are reflected in company profits from the first year of application, as part of a strategy of respect for the environment and constant raising of quality standards.
As another facet of sustainability, Sacmi documents its social responsibility in the form of a Social Audit, drawn up in compliance with GBS-Gruppo Bilancio Sociale accounting practices. The audit is divided into three theme areas: identity, added value, and social interaction.
On the environmental protection front, Sacmi adopted a management system per ISO 14001, integrating it with VISION 2000 and OHSAS 1801 worker safety quality systems. Among the company’s strategic environmental policy goals are correct disposal and recycling of waste, emissions control and water purification.
Saving waste products
The search continues for new materials with different characteristics and new properties. Thus technical textiles have increasingly gained ground, often replacing traditional textiles and creating new applications. The main driver is the need to respond to worldwide demands to cut production costs, increase energy efficiency, embrace environmentally friendly materials, and boost operating flexibility of machinery and equipment.
Cormatex S.r.l. (www.cormatex.it) has been manufacturing textile machinery for the Italian and international markets since 1938 with an emphasis to reduce costs through sustainability.
For woollen spinning in areas such as fine yarns for knitting products, by using valuable fibers such as cashmere, angora and camel hair, either pure and/or blended with fine wool fibers, Cormatex can supply turnkey solutions for wool deburring, cashmere dehairing, fiber opening and blending, plus complete woollen spinning lines.
For nonwoven machinery, the company offers fiber preparation systems, card-feeding systems, cards and crosslappers, an innovative airlay system, and cutting and winding-up systems, developing comprehensive technical solutions for needle-punching, thermobonding and airlaying lines.
One machine, many applications
Flexible production equipment allows manufacturers to diversify their products with relatively small investment, leading to mass customization and quick changeovers.
Cormatex applied these principles when it vigorously channelled efforts into R&D, leading to the development of its new patented system Lap Formair.
The low investment and operating cost result from a process based on a purely aerodynamic principle. Lower production costs are realized due to high output rates (over 2,000 kg/h), plus high production flexibility due to the absence of carding units and other mechanical components. The high quality of the end product is guaranteed by a state-of-the-art pressure control system that allows formation of laps with a weight inferior to 200 grams per square meter and with control of lap density uniformity.
Lap FormAir is designed for three types of industrial users—manufacturers of airlaid nonwovens, manufacturers of traditional nonwovens, and manufacturers of textiles in segments other than nonwovens.
Excellent performance levels make it possible to process all types of raw materials, fibrous or not. Features such as use of air for the transport and condensation of the material, in the use of a particular method for controlling air pressure inside the condensation chamber, and in the absence of carding units or other mechanical components, play into a primary sustainability goal to add value to poor raw material and wastes of other textile processes.
Lap FormAir was tested with highly heterogeneous blends, where fiber traditionally used in manufacturing of nonwovens was replaced partially or completely with low-quality natural fibers—sugarcane, coconut, recycled cotton, recycled jute hemp and flax, raw hemp, paper and cardboard, low-density polyurethane waste or even waste from other industrial processes (carding, carpet production cuttings, and certain textile finishing processes) not normally used in textile production.
Saving plastics
With more than 30 years in the recycling industry, a Sorema division of Previero N. S.r.l. (www.sorema.it) seeks high efficiency at high capacities. The company, which specializes in turnkey recycling lines, leads in the design, construction and installation of recycling lines for plastic material.
Its more than 280 installations worldwide offer solutions for post-industrial, post-consumer and agriculture polymers including PET/HDPE bottles, PE film and others. Its goal is to foster continuous technical progress to optimize process cost and cushion the environmental impact of recycling lines.
The latest innovation in wet grinding modules is Previero’s double-scissor PRH series, which features total interchangeable wearing parts, a boon for interchangeability of parts subject to wear applicable to all grinders with rotors of blade lengths of 1200-1600 and 2000 mm. Wet grinding is essential in PET bottles and PE film washing lines with a double function: material granulation and removal of contamination through strong mechanical friction on material surfaces.
The PRH series includes high-quality construction material, over-dimensioned bearings with external supports, an absence of water loss in cutting chambers for clean working conditions, nickel plating of the cutting chamber, and wedge blocking of pre-adjusted blades for a quick changing and side-anti-wear disks.
Sorema seeks high efficiency at high capacities. Customers benefit with minimized labor, flexible feedstock selection, higher prices for end products, the use of large quantities of recycled material, and realizing the high performance of plastic products containing or made of recycled materials.
Today the adoption of sustainable practices influences many areas across the manufacturing spectrum. Where innovation is the goal, Italian manufacturers can deliver responsible action that is required to preserve natural resources and human resources around the world.
Sustainable Manufacturing Initiative
www.manufacturing.gov/sustainability
PAL S.r.l.
www.pal.it
Sacmi Imola S.C.
www.sacmi.com
Cormatex S.r.l.
www.cormatex.it
Sorema division of Previero N. S.r.l.
www.sorema.it
Sponsored Recommendations
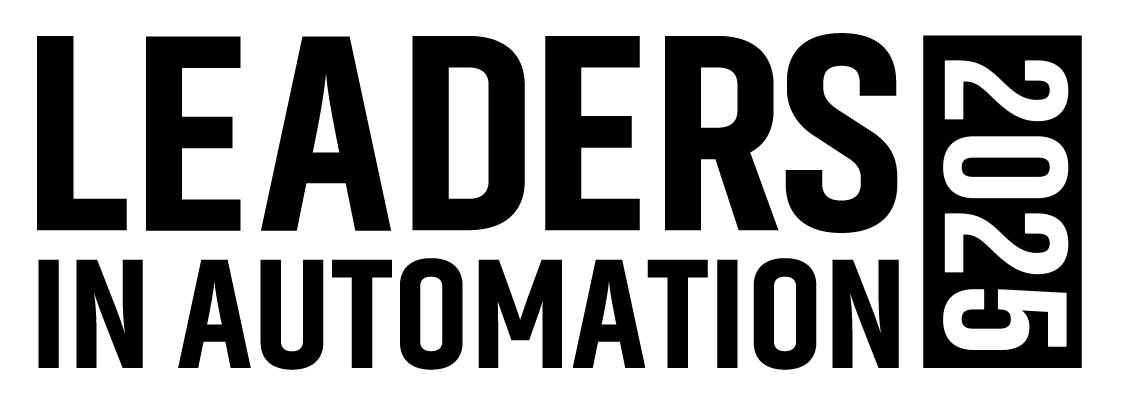
Leaders relevant to this article: