Italy boasts a rich cultural heritage in many areas, including art, science, and environmental responsibility. The latter should come as no surprise—Italy was one of the first countries to harness geothermal power, an energy resource.
At the same time, the United States participates as a member of the Organisation for Economic Co-Operation and Development (www.oecd.org), an organization of 30 democracies that also includes the United Kingdom and Italy. While concern about the environment underlies all of its efforts, OECD has turned its attention to the issue of manufacturing efficiency. The OECD points out that manufacturing industries account for a significant part of the world’s consumption of resources and generation of waste. Worldwide, the energy consumption of manufacturing industries grew by 61 percent from 1971 to 2004 and accounts for nearly one-third of today’s global energy usage and is responsible for 36 percent of global carbon dioxide emissions.
Italy’s environmentally friendly legacy has percolated throughout its renowned manufacturing sector where companies have innovated through the development of green machines. These are machines engineered to meet today’s market demands to use less resources, save energy, and reduce pollution. The machines allow customers to help the environment and reduce operating costs. As the following examples show, the creative paths of innovation taken by Italian manufacturers of environmentally attuned and engineered systems are as varied as the fountains of Rome.
Rock, water, and the environment
Fountains, geothermal springs, and even life itself are all impossible without water. Although it covers 70 percent of the earth, it is a precious resource that is gaining importance. As a result, water management throughout Europe and elsewhere is an important issue, including how it relates to quarry processes.
Europe’s Water Framework Directive (WFD, 2000/60/EC) set requirements for the management and protection of surface water against water pollution. That was followed in early 2009 by the so-called “daughter directive” aimed at protecting groundwater. Quarry operators have long worked to reduce the impact on the environment from the discharge of surface water, but under the new directive the impact on groundwater must also be assessed.
The Italian firm Fraccaroli e Balzan S.p.A. (www.fraccarolibalzan.it) is seeing a growing market for its innovative solutions for wastewater treatment in quarrying applications, particularly now that environmental legislation is becoming more rigidly enforced and per-liter taxes on water have been enacted in some countries.
Its well-proven technology was developed for use in marble quarries, but has now been broadened to an array of aggregate applications as well. These systems allow a significant portion of the water to be reused, with up to 90 percent recycling in marble quarrying applications and 80 percent in aggregates duties. The systems are particularly important in areas where water is in short supply and its use poses additional operating costs.
In some applications and areas, recycling plants can pay for themselves within a year. For example, the Nordic Countries as well as Germany, Northern Italy, and other regions have strict enforcement of regulations on wastewater from quarrying operations. Enforcement is likely to appear elsewhere, such as Eastern Europe, in the near future.
For every cubic meter of aggregate produced, quarries need 1.5 to 2 cubic meters of water. A throughput of 2,000 to 5,000 liters/min is the most common size for a dewatering plant. The largest plant built by Fraccaroli e Balzan, in Switzerland, can handle 14,000 liters of water/min, and another 10,000 liters/min plant has been built in Germany. The aim of a dewatering plant is to yield more clean water and less mud. Wastewater enters the plant and is agitated, chemicals are added, and the heavy particles sink to the bottom allowing clean water to be drawn from the top. Sensor-equipped, programmable logic controller (PLC)-controlled presses detect when the water stops dropping out of the material under pressure and then open to let the dried cakes fall out as neutralized waste. The waste can then be used as backfill or as a sub-base for road construction. The biggest press Fraccaroli e Balzan has built has 100 plates measuring 1.5 x 1.5 meters.
The use of these filter presses to recycle process water in quarries can not only reduce operational costs at the site, but can also significantly lower the environmental risks associated with ground- and surface-water pollution.
Melding environmental and commercial interests
It is the machine tool sector upon which the manufacturing industry largely depends for the means to plan, execute and commercialize products. In fact, it is the foundation of almost all production processes worldwide. Italy’s exceptional expertise in this market makes it the preferred technology partner for users around the world: It has 25 percent of the global production output and 33 percent of exports in this sector.
However, machine tool producers cannot develop solutions based on conventional designs or solely on operational consistency and flexibility. They must combine their specialized know-how with other factors to compete as problem solvers rather than as machinery suppliers.
Making production eco-compatible is one of these problems that must be solved: it is an area of ongoing entrepreneurial development that was begun in 1974 by Giancarlo Losma, founder and president of LOSMA S.p.A. (www.losma.com).He is also president of UCIMU-SISTEMI PER PRODURRE (www.ucimu.it), the Association of Italian Manufacturers of machine tools, robots, automation systems, and auxiliary technologies.
LOSMA is a company specializing in air filtration and purification of industrial effluents from metalworking to meet ecological requirements inside and outside the factory.
Giancarlo Losma states, “Getting started was awful: a potential client told me, ‘Thank you, but I have no use for an exhaust fan for oil vapor or liquid purifiers for my machinery. I already have thirty operators that breathe in gas and breathe out clean air...’
“Today, that would be considered an [outrageous] statement, but it captures the lack of interest, if not irritation, that had developed at that time. Yet this was a market, and a world, that needed to be educated. Over time, environmental awareness has [proliferated] in civil and manufacturing sectors, translating my youthful ‘bet’ into an activity that is profitable and, in its small way, useful to society.”
Today, the company has subsidiaries in the United States, Germany, and Great Britain; its 2008 sales were 11.5 million Euros (approximately U.S.$16 million).
Seeking improvements in the quality of life associated with manufacturing operations has led to an “eco-industry” of companies dedicated to controlling air pollution, treating liquid effluents, managing solid waste, controlling noise and vibrations, recovering contaminated soil, and controlling pollution of the oceans.
According to studies, the eco-industry has annual sales of 270 billion Euros (approximately U.S.$383 billion), confirming its widespread growth and importance.
Additionally, many believe that by acknowledging ecological parameters in analyzing production factors and a product’s yield over its lifecycle, companies can obtain significant advantages: in terms of efficiency, by optimizing resources; and in reducing energy consumption and therefore costs.
“‘Image return’ is not to be underestimated. It makes it easier for a large company to build customer loyalty, gain credibility with public and private institutions, and retain the most qualified staff,” observes Losma. “The entrepreneur must not let the opportunity escape to blend commercial and environmental interests. Targeting ‘eco-efficiency’ is increasingly often the key to success. My company’s history attests to this.”
Environmental concerns and the recession
It’s one thing to be eco-minded, it’s yet another to maintain a green outlook in the midst of an economic crisis such as the world is experiencing. Remaining on a path of sustainability can be considered particularly virtuous in today’s economy, according to managers with Denver s.a. (www.denver.sm), a company that provides cutting and polishing machines for stone, glass, and other materials.
“Denver began producing systems for the control of the environmental quality in stone workshops. We were the first ones to produce large numbers of dust collector systems and clarifying water systems—attention to the environment is engraved in our DNA!” declares Adolfo Fabbri, Denver technical department and environmental manager. “Our machines have helped assure recyclability, simpler processes of production, less pollutants, the reduction of painting cycles and acoustic comfort for the operator.
“We have as an option in all our machines a speed control system or inverter,” reports Fabbri. “This device regulates power to the electric motor as demand dictates, without waste. Also, cooling on our Electrospindles uses a hydraulic, closed-loop system that drastically reduces water consumption.
“Additionally, a software option for customers simulates the process and optimizes machines to save marble, stone, and glass otherwise used for the tests. And remember that Denver introduced the concept of the monobloc sawing machine that’s easy to transport and install. All Denver products can be transported in a 40-foot container to reduce the impact on the environment.”
The company’s commitment to the environment includes its own facilities. “The entire new facility in Gualdicciolo is cooled without the use of air conditioning systems by controlling the humidity,” states general manager Roberto Nori. “This sophisticated system produces less pollution and saves energy. This year we have also reduced drastically the use of paper in our offices and the sending of paper materials. We prefer to talk more to our clients rather than to flood them with brochures, with the double goal to consume less resources and to aim more at the value of relationships.”
What kind of results can customers expect? “Those who purchase a Denver product can verify the eco-advantages in terms of smaller electric costs and water requirements, ideal acoustic and environmental comfort, transport cost reduction, less waste of stone and glass materials, and a drastic reduction of the costs of assembling and disassembling of the machinery,” concludes Nori.
A converting cure yields energy conservation
UVRay by Cefla Finishing Group (www.ceflafinishinggroup.com) represents state-of-the-art ultraviolet curing and offers significant energy savings compared to traditional UV ovens. A new design concept lets UVRay integrate in one module all process components: conveyor, UV lamps and an advanced PLC that controls all operations and diagnostics, with a user-friendly touch-screen programmer allowing an easy management of all functions.
“We have always believed in product and technology innovation of finishing lines as a key factor for sustainable manufacturing,” states Roberto Scala, managing director of Cefla Finishing Group. “Our Research & Development team has a real focus on responsible design. Cefla engineers work with tomorrow’s user in mind, developing new finishing systems with low environmental impact.”
UVRay can provide energy-resource savings up to 30 percent compared to traditional systems:
An electronic control unit on transformers ensures efficient power management, enabling savings of approximately 10 percent when compared to a standard solid-state supply. The electronic control optimizes lamps power delivery and consumption according to manufacturing requirements and self-adjusts accordingly in the case of gaps in production. Tests on production lines show energy savings of approximately 20 percent for short runs and approximately 30 percent for long runs.
Food for thought
Still another take on green comes from Cavanna S.p.A. (www.cavanna.com), which has a 49-year history in packaging machinery building. In March 2009, the company’s exhibit at Ipack-Ima in Milan, Italy, promoted the slogan: “We are building the future of packaging.” It was, with two interrelated developments that combine to put those words into action. Cavanna has invested in the development and introduction of the Model Zero 5 Flowsonic flow wrapper. Although it resembles a conventional flow wrapper, it belies the strong environmental technology found “under the hood,” ultrasonic longitudinal sealing. The machine can accept sustainable biofilm materials, including the innovative Bioflowpack, the first high-barrier totally biodegradable and compostable flowpack introduced at the last Italian Packaging Exhibition.
It represents the cooperation of three partners: composed by Mater-Bi from Novamont S.p.A. (www.materbi.com), NatureFlex from Innovia Films (www.innoviafilms.com), printed and laminated by Sacchital S.p.A. (www.sacchital.it), developed thanks to the ultrasonic sealing technology. A green alternative to traditional plastics, the flowpack is made up of a layer of Mater-Bi laminated to cellulose film that give the necessary high oxygen and water vapor barrier properties. It meets all technical and hygiene requirements in food packaging. This guarantees the integrity and sturdiness of the seal and provides visual appeal. It is appropriate to any kind of food, especially temperature-sensitive products that benefit from the cold contact sealing of ultrasonic technology.
Where the rubber meets the road
Another green approach is to provide equipment with features that maximize efficiency.
Founded in 1885, COMERIO ERCOLE S.p.A. (www.comercole.it) is constantly innovating industrial processes related to the rubber, plastic, and nonwovens business. The company has developed and patented a fully hydraulic nip adjustment. Such a device has been equipped on a new calendering plant—one of the world’s largest—that produces rubber conveyor belts.
The plant is suitable for the production of both rubberized webs that compose the conveyor structure and final rubber coatings of large thickness. Advantages of the hydraulic system include:
■ Elimination of wear of mechanical parts and of clearances due to moving parts;
■ Constructive simplification and managing simplification of the required automation;
■ Reduction of commissioning times and of management and maintenance costs;
■ High roll positioning speed during recipe change;
■ Possibility of fast opening in case of emergency;
■ Highly accurate positioning; and
■ Protection of rolls integrity in case of particularly hard raw materials.
The company has also developed technology for its ETP family of recycling extrusion plants. This technology combines a thermoplastic matrix with filler such as rubber pieces from tire waste, thermoplastic scrap from nonwovens, mineral fibers, or up to 75 percent wood particles. The end products provide good insulation properties, a welcome feature in a time of sensitivity to energy conservation.
Colorful textile technologies turn green
Eco-innovation comes in many forms and many colors besides green. Such as indigo—as in IndigoGenius, new yarn dyeing technology from MASTER S.r.l. (www.mastermacherio.it) that is used for yarn materials that produce denim fabric. Based on integrated dyeing modules, the new patented technology eliminates many typical problems of traditional dyeing technology while increasing the environmental aspects.
In addition to better operational performance, including higher dyeing yield and a process independent of external variables, IndigoGenius offers eco-centric advantages with reductions in:
■ The use of caustic soda and other chemicals;
■ The number of dye vats required;
■ Yarn waste;
■ Waste water reduction;
■ Electric power; and
■ The amount of sodium sulfite amounts in effluents.
This overview of testimonials of machinery engineering provides a taste of eco-minded Italian ingenuity. As a memory aid, consider the Italian flag, where the color of green echoes in the country’s machinery offerings to meet the demands of today’s marketplace.
Organisation for Economic Co-Operation and Development
www.oecd.org
Fraccaroli e Balzan S.p.A.
www.fraccarolibalzan.it
LOSMA S.p.A.
www.losma.com
UCIMU-SISTEMI PER PRODURRE
www.ucimu.it
Denver s.a.
www.denver.sm
Cefla Finishing Group
www.ceflafinishinggroup.com
Cavanna S.p.A.
www.cavanna.com
Novamont S.p.A.
www.materbi.com
Sacchital S.p.A.
www.sacchital.it
COMERIO ERCOLE S.p.A.
www.comercole.it
MASTER S.r.l.
www.mastermacherio.it
Sponsored Recommendations
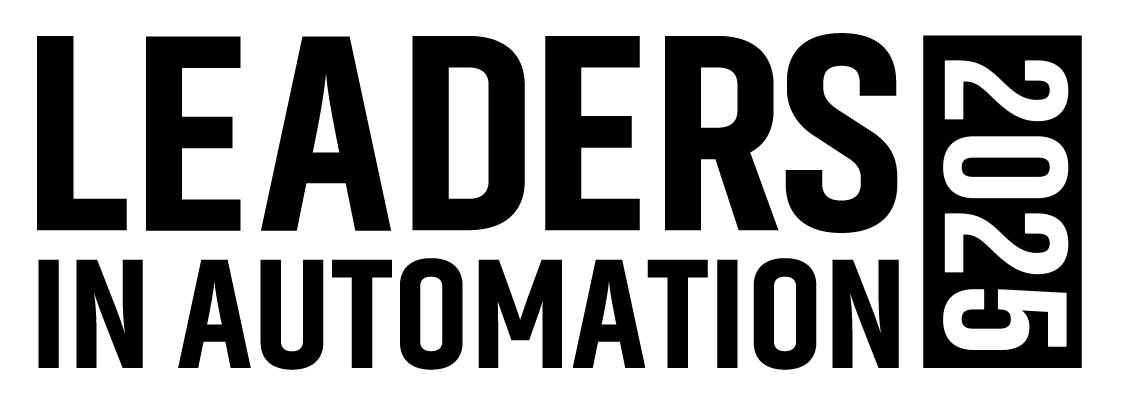
Leaders relevant to this article: