One of the major advantages of the ANSI/ISA-95 standard (promulgated by the International Society of Automation and adopted by the American National Standards Institute) is its ability to provide automated, error-free data exchange. Chevron turned to ISA95 to transform the data collection in its U.S.-based lubricant plants from a manual, error-prone process to an error-free automated system.
Chevron Products Co. is a San Ramon, Calif.-based company that produces lubricants such as oils and greases. The company runs an operational control system (OCS) as its enterprise resource planning (ERP) system, running sales, marketing, inventory and warehousing. The plants also had product control systems that ran the manufacturing. “They were way overdue to be replaced,” says Mark Weinmann, project manager at Chevron. “So we undertook a program and selected Yokogawa as the vendor in 2008.”
Yokogawa introduced the team to ISA95 using business-to-manufacturing markup language (B2MML). Chevron runs a specialized platform of fault-tolerant servers with high uptime. “When we learned about ISA95, we wondered whether the servers had the tools we needed,” says Weinmann. “We found some tools there. We used XML Thunder (for eXtensible Markup Language) that converts the XML-based B2MML to the system so we can read it.”
After the B2MML was set up, the team found it was easy to build and send messages back and forth between the systems. At that point, the connection became a data-mapping exercise. “After we began the exercise and began testing, we found we were missing this data element or that data element, but adding was easy,” says Weinmann. “We didn’t have to rewrite it because the B2MML language made it easy and flexible.”
The plants implemented the new system in May of this year, and the interface to the ERP system was part of the implementation. “It works like a champ—the messages go back and forth,” says Weinmann. He also notes that the team has used the ISA95 standard to help the ERP interface with another system. “Now we have a standard interface and find we can use the same concept. So we can leverage our learning and apply ISA95 to other projects.”
The net result of the interface is considerably fewer errors. “The information from our old custom interface was error-prone and required a lot of manual work. When we put in the new [ISA95] interface, there were virtually no errors,” says Weinmann. “It was vastly different, 50 percent to 60 percent better than the old interface.”
ISA95 has come into its own during recent years. While large manufacturers led the early adoption, it has crossed a wide swath of industries, from refineries and pulp-and-paper to pharmaceuticals and food-and-beverage. Many of the large manufacturers are pushing adoption down their supply chain to Tier One and Tier Two suppliers. While ISA95 was originally developed by process manufacturers, it has gained the attention of discrete manufacturers as well. The growing adoption of ISA95 was also spurred on by ERP vendor SAP AG’s adoption of the standard.
ISA95 is a standard for developing an automated interface between enterprise and control systems. ISA95 was conceived by those involved in the development of ISA88, a standard for addressing batch process control. “The ISA95 work was led by the ISA88 team,” says Bob Lenich, Syncade platform director at Emerson Process Management, an Austin, Texas-based automation supplier. He is also a member of the ISA95 committee. “The new group pulled together to address the gap between the enterprise and control systems.”
Widely adopted
While ISA95 has been in development for 14 years, it’s only been in recent years that it has gained widespread acceptance. “A team started to work on the standard in 1995, but I would estimate it was only about four years ago that we reached a critical mass of vendors to officialize it,” says Don Clark, vice president of global industry solutions for automation supplier Invensys Operations Management (IOM), in Plano, Texas. “Key participants kicked the ball over the line—one was an end-user, BP.”
He notes that SAP, the Waldorf, Germany-based ERP giant, was not initially supportive of the standard. “At first, SAP said the world didn’t need a standard for exchanging data between the plant and the ERP system,” says Clark. “We slogged ahead anyway, and about five years ago, they said, ‘You know, you’re right, it’s too difficult.’ ” SAP ended up implementing ISA95 in its system in 2004.
“The biggest benefit ISA95 has brought is a common language for specifications that allow people to better describe the data exchanges and the workflow requirements that go on in plant systems,” says Charlie Gifford, chief manufacturing consultant at 21st Century Manufacturing Solutions, in Hailey, Idaho. “Now, I use those terms to communicate my needs when I send out an RFP (request for proposal)—ISA95 becomes a reference document, so we all know what I’m asking for.”
That common language allows users to apply the standard outside of the traditional connection between the enterprise system and the plant system. “Our customers are asking if we’re ISA95-compatible,” says Mark Leroux, manager of production for automation vendor ABB U.S., in Norwalk, Conn. “That’s partly because they want to use the standard to get everyone on the same page, even if they’re not using it to connect their manufacturing to the ERP system.”
The adoption of ISA95 has accelerated in the last few years. The growth is due to a number of factors. For one, the standard has gained the attention of smaller manufacturers. For another, the recession has motivated manufacturers to take savings wherever they can be found, and ISA95 supports productivity gains. ISA95 also has a broad audience of industries, and recently, the standard is being used for applications outside of direct connection between the plant and the enterprise. It’s getting used for inventory management, maintenance and quality programs.
One of the major advantages of ISA95 is its ability to take demand data and integrate it with the production system. “The fundamental principle is that ISA95 is translating real demand into balanced execution on the manufacturing side,” says Roddy Martin, senior vice president and research fellow at AMR Research Inc., in Boston. “If ISA95 can help us translate demand into a network of manufacturing sites, we will have achieved nirvana.”
Another motivation for adopting ISA95 is to make it easier to transport best practices from one plant to another. “ISA95 becomes handy in giving plant operators a structure to see where they’re performing well,” says Dennis Brandl, chief consultant at BR&L Consulting, in Cary N.C. “They can use ISA95 to compare one plant to another and to translate best practices.”
ISA95 has gained greater acceptance outside the United States, particularly in Europe. “ISA95 is being used more outside the United States that it’s being used inside our country,” says Gifford, of 21st Century. Gifford notes that manufacturing executives in Europe are more informed about ISA95. “Europe gets it, while we’re 10 years behind.”
The major ERP companies were not behind the drive to develop ISA95, though SAP eventually got on board. Oracle has not embraced the standard to the same degree, likely because ISA95 is often viewed as a process manufacturing standard, and Oracle’s customer base tends to include discrete manufacturers. “SAP has good connection points, but they haven’t been very effective in being an event-driven operation,” says Lenich, at Emerson. “As for Oracle, we’ve started to see integration to Oracle picking up, but we haven’t seen them a lot with our customers.”
ISA95 is not used only in the process world, nor is it only used in manufacturing. “The ISA95 standard has recently been revised and extended, so now it came be used not only to exchange information about production, but also about maintenance, inventory and quality tests,” says Bianca Scholten, principal at TASK24, an IT integration company in The Netherlands.
Future of ISA95
Many believe that the standard is valuable enough to eventually spread throughout discrete manufacturing. “It’s a misconception that ISA95 is just for process,” says Tim Sowell, vice president of product and solutions strategy at Wonderware, an IOM unit based in Lake Forest, Calif. “Our food companies are hybrid. They’re process at one end and discrete at the other end. They’re using ISA95 because it has good definitions of product segments—that gives them the context of the product, not just the process.”
Parts One and Two of ISA95 are complete, but they’re not fixed. “Teams have been updating the documents and each part has a specific review cycle,” says Bob Mick, vice president of emerging technology at ARC Advisory Group Inc., in Dedham, Mass. “They’re bringing the parts up to date and making them consistent with other documents. They also take in feedback from users who have had problems.”
Going forward, the ISA95 standard will likely see even wider adoption as it gains traction among mid-size and smaller manufacturers. Interest on the discrete side is also likely to spur wider adoption. Potential expansion for ISA95 may come as its components are used as a common language outside the enterprise/control connection, for supply chain-to-warehouse management and for connecting to maintenance and quality programs.
Addendum
Oracle has submitted the following statement regarding this story: “Oracle adopted ISA-95 reference model for building the data model in Oracle Manufacturing Operations Center. In addition, Oracle also supports ISA-95 based B2MML as the standard for integration with Oracle Process Manufacturing.”
Subscribe to Automation World's RSS Feeds for Feature Articles
Companies in this Article
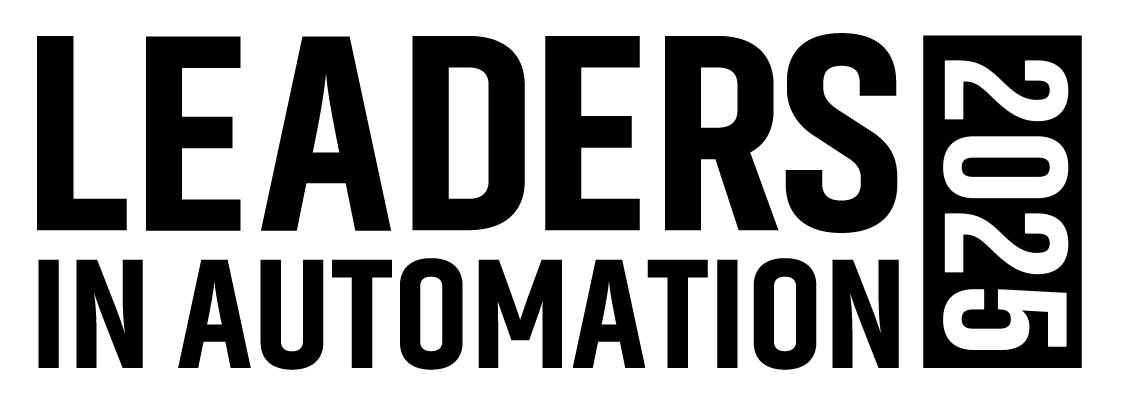
Leaders relevant to this article: