"People don't have a natural instinct for the appreciation of change management that they should," says Bill Wray. "It's unfortunate, but sometimes it takes a tragedy to wake people up to doing the right thing." Wray, a registered Professional Engineer, works at a Bayer MaterialScience LLC polyethers plant in Channelview, Texas. His title is engineering consultant, but he actually does most of the engineering tasks at the plant.
The Bayer plant was previously owned by LyondellBasell Industries and is located in the midst of the larger LyondellBasell facility. It’s operated under contract by Lyondell. Although the name says Bayer, polyethers, not pharmaceuticals, are the plant’s product. Polyethers are used in the manufacture of urethanes. The plant uses automation systems from Yokogawa Corp. of America, a Sugar Land, Texas-based supplier with corporate headquarters in Tokyo. Wray has worked at the plant for about 30 years under four different owners and has been involved with the development of the management-of-change system.
The site experienced a tragedy in 1990—a deadly explosion. This taught everyone from management to operator the importance of a well-established management-of-change process. Adds Wray, “I honestly think this location is one of the safest chemical plants in the industry because of the response we made to the incident.” He’s been in the industry since 1986 and has seen the evolution of control and regulation over the years. One of the things that has gained importance is management of change.
Wray thinks that it takes a combination of people, culture and automation to make a good management-of-change system. “Developing a culture that includes a strong management-of-change program comes from strong procedures,” says Wray. “But before that, everyone must recognize a need for strong procedures. It can be a pain, but seemingly inconsequential changes could have big consequences. You need procedures even just to assure documentation is updated. But even with a well-established management-of-change program, you still run across problems.”
The plant has two types of change procedures—a simplified process change authorization (PCA) and a “full-blown” PCA. “The process is mainly executed on paper,” states Wray, “although we are sliding toward an automated system. Paper forms are scanned into a Documentuum (a document management product from EMC Corp., of Hopkinton, Mass.) repository.”
Change documentation
First, the initiator must identify that the proposed work is indeed a change and not just a replacement in kind, for example, replacing a motor with another motor with the same specifications but manufactured by a different supplier. Then a decision is made as to whether the change can be explained by the simplified version or whether the longer one is needed. Basically, the PCA is a long questionnaire. In the first section is a description of what the change is with any applicable drawings attached. The justification for the change is included. Then a series of questions elicits such details about the change as issues with the process, piping, rotating equipment, control, safety, environment, human factors and more.
Once the PCA form is completed, it goes to a review committee composed of representatives of all affected areas. There is a design safety review, and people from operations, environmental, reliability, process engineering and perhaps others review all elements of the request. “For example, they’ll ask if the change causes any potential for high or low pressure. If the answer is yes to any such question, then you have to document how you’ll mitigate or eliminate the risk,” adds Wray. “We look at process chemistry, valves, rotating equipment and facility siting if a temporary building is required.” The company has also started to execute a PCA when there are personnel or staffing changes. For instance, if a staff reduction is anticipated, a team does a PCA to study the impact.
After everyone signs off on the authorization, then the change is executed. But that doesn’t end the process. Each craft involved in the change must sign off on whether the change was installed to the drawings. If not, redlined drawings must be included in order to complete the paperwork.
Wray believes that companies with a strong management-of-change process have a competitive advantage over those who don’t for one simple, but crucial reason. “If you don’t properly manage change, you’ll have an accident. And an accident can’t be conducive to competitive advantage. You’ll have injuries, bad press, fines, costs of repair—so definitely, a good change process gives you a competitive advantage over someone who doesn’t.”
Every automation supplier interviewed for this article incorporates change management within its automation system. Engineers who aren’t making use of these tools need only contact their vendor representative and find out what tools currently exist for their systems. Given the cutbacks to engineering departments that have happened over the past several years—and probably exacerbated by this recession—sometimes calling in your supplier for help makes sense.
Leading change
Michelle Adkins works with customers as a consultant in the Global Industrial Solutions group of Emerson Process Management, an Austin, Texas-based automation supplier. She says that working with clients in this area incorporates a wide variety of systems from manufacturing execution systems (MES), to electronic batch records (EBR), and document management, master batch records (MBR), standard operating procedures, forms, log books and “lots of paper.”
In the pharmaceutical industry, for example, people need to track a piece of equipment. Is it clean? Sterile? What product did it just run? What is the state of the product there now? “It all leads to bottom-line benefits,” she adds. These benefits include reduced cost and improved quality, along with the ability to focus on the product rather than the documentation. It also leads to agility from research to manufacturing. The system also assures getting “lots” of product produced with the correct MBR, equipment and people, with reduced deviation and product loss. With the end of blockbuster drugs as a business model in pharmaceutical, companies must become more agile with flexible manufacturing.
Adkins goes in at the very beginning of a project, when it’s just an idea. “We do assessments studies to define where a problem lies at the beginning. It’s almost a DMAIC (define, measure, analyze, improve, control, derived from Six Sigma) process,” she says. “We do a value-stream mapping exercise to show how the system works and how proposed solutions would work. The process includes looking at equipment tracking, electronic batch record systems and other elements. The future value stream after proposed changes is mapped. From this, we can go to a project estimate, relating back to the value-stream map to show benefits. The return-on-investment analysis can be developed from this process.”
She has also noticed how people change during the process. First, there is an early buy-in because input is sought from many people. Just by contributing to the study, they see a great opportunity to share and help define the problem. Excitement also builds during the week that the study is actively in process. “There is some resistance at the beginning, but by the end of the week, they start saying things such as, ‘The system can do this, can’t it?’ The technology doesn’t work if the people don’t want it to,” says Adkins.
Working together
Sometimes, a producer and its automation supplier must develop a deep relationship at a level of sharing technology, or at least ideas about development of the technology. The continuing collaboration of The Dow Chemical Co. in Midland, Mich., and Swedish/Swiss automation suppler ABB, with U.S. headquarters in (Raleigh), N.C., exemplifies the power of this type of relationship.
Dow is a leader in science and technology, providing innovative chemical, plastic and agricultural products and services. Consistency and sustainability have always been key elements of the Dow’s operating discipline. In the 1960s, a number of technology development activities throughout Dow converged to ultimately become a standardized, re-deployable process control strategy that supported the company’s goals of overall consistency, productivity improvements, global operating discipline and innovation, all while maintaining high safety performance.
At that time, however, a commercially available solution to help Dow realize its operating discipline did not exist. The Dow team then developed several in-house solutions, including a process control system that came to be known as MOD (Manufacturing Operating Discipline). However, in early 2000, Dow realized it was no longer cost-effective to continue to invest in proprietary hardware and software systems. Instead, the company needed to focus on its core manufacturing business, and therefore decided to seek a commercial solution.
Dow and ABB forged a collaborative relationship signed in 2001 that nurtured ongoing development activities. The relationship consisted of four key elements: shared vision; trust in each other; open communication; and willingness to confront each other and use conflict constructively.
Version 5.0 of ABB’s System 800xA is equipped with new engineering functions that let customers make application changes without interrupting production and without incurring downtime—a common and costly occurrence whenever system modifications are made. These new engineering functions include Multi-User and Distributed Engineering as well as tools such as Load-Evaluate-Go, developed in collaboration with Dow.
Load-Evaluate-Go lets customers add programs, modify configurations and implement software upgrades while production is running, and then simulates and evaluates the impact these changes will have on the production process. Once the application changes have been evaluated, the customer can choose to execute, modify or discard them. This capability significantly reduces the risks associated with making application changes in the running process, and improves overall efficiency by avoiding production stops, missed or delayed product deliveries, and costly downtime.
Andre Schepens, control system architect, Engineering Solutions, Dow Benelux BV, explains the value case for this capability: “LEG (Load-Evaluate-Go) allows for online modifications to a plant control system and doing a last-minute integrity check against the running version of the control application. Because the system warns about any abrupt change that can have an impact on field devices at the moment of activating the new version of the control application, this will detect any hidden problems that surface only at the split second of the transition of the old version to the new version of the control application. Even the best dynamic process simulation cannot provide the exact data of the dynamics of a transition between old and new versions of a control program. Because the ‘Evaluate’ feature flags this while the output is in a passive status (not controlling the field device), the user has the ability to either back out or make a last-minute correction to resolve the delta prior to activating. The added value is translated into less risk (equipment damage, production loss) and faster turnaround and payback of application changes.”
Less risk
Roy Tanner, systems marketing manager for ABB, in Wickliffe, Ohio, adds regarding this change management part of System 800xA, “Change management has always been important in the pharma industry, and for safety. But now, this is crucial for chemicals and power, too. They seem to be always making changes any more. They need to cut costs and make process optimizations. And they don’t want to wait several years for [scheduled] downtime [to make a change]. So they can get the change with less risk and lower cost. They can get the most from their assets. Companies that pay attention to change management will have higher asset utilization.”
Some companies have highly integrated systems, not only from process control to MES, but also to their enterprise resource planning (ERP) system, maintenance management system, laboratory information management systems and perhaps others. Chris Amstutz, manager of the Global Life Sciences Industry Group for Emerson Process Management, says he’s working with a large biotech company with just such integration.
“The client will use our document management for change control,” says Amstutz. “It gives them a single place to sign changes, and it will all be electronic. With the next stop of integrating to MES, they will achieve horizontal management of materials and equipment into the change management workflow. They can route and manage change so records are updated upon approval. This assures all systems are aligned.”
Other companies also have built in tools to help customers manage various changes in their processes. Eric
Kaczor, product marketing manager for software at Siemens Energy & Automation Inc., an Alpharetta, Ga.-based supplier, notes that a recipe inside the human-machine interface provided by his company is saved to a database and uploaded to the process. A built-in tool tracks changes to such things as operation, records, quality control and the like through the HMI. The system is built to easily communicate changes, with everything residing in a single database.
Todd Stauffer, Siemens product marketing manager in process, located in Spring House, Pa., adds, “A new capability regarding batch management is the ability to modify a recipe and sequences as it is running. You might do this if you realize the equipment isn’t running like you thought it should or you are running a new product. You can save this change back to the master record if it’s something that should be added to the knowledge base.”
As systems grow increasingly complex, users depend more upon systems to save configurations and allow the system to revert to a previous program. Rick DeVoe, business manager at Rockwell Software, part of vendor Rockwell Automation Inc., Milwaukee, sees customers responding to such drivers as mean time to repair and time to commission. For example, he describes the situation at a brewing company customer who had a problem and thought the culprit was in the control system. “They brought in a bunch of people over a weekend and made about 150 changes to the automation system only to find that the root cause was a mechanical issue. With AssetCentre (a Rockwell Software product), they were able to go back and restore the line to its original state, saving many hours.”
Huge savings
Sometimes, changing the technology of managing and recording change is a huge benefit just in itself. Take the example of pharmaceutical companies. These companies have massive documentation requirements as set forth by the many regulatory agencies that they work under. Changing to electronic records from paper-based systems can be a huge time and money saver.
Chris Morse is a product marketing manager based in the United Kingdom for Phoenix-based automation supplier Honeywell Process Solutions. He relates the story of one such manufacturer who faced the challenge that a change might have 400 to 500 steps. “It would take an entire binder to hold the documents. But that isn’t the whole story. They couldn’t just print that, but also had to print everything in the large system that was related—8,000 binders full of paper. When they changed to the Honeywell Quality Version Change System, the printing of all but two sheets of paper was eliminated. This amounted to a savings of $300,000 per year. This also eliminated the fear of change, leading to more process improvements.”
Morse notes that people, especially in the quality department, are leery of change until shown that it can be trusted. Gimmi Felice, product manager for Proficy Change Management at GE Fanuc Intelligent Platforms, a Charlottesville, Va.-based automation supplier, comments, “One of the biggest challenges to adopting change-management software is culture. This is especially true in industries where they are not used to logging and documenting. It is a big shock to people in other industries.”
Grant Le Sueur, InFusion product marketing director at Invensys Process Systems, an automation supplier based in Plano, Texas, says the importance of change management has expanded from pharmaceutical to such other industry verticals as oil and gas, and fossil power. Among users, there are two phases of change management—construction and operational. The construction phase has the heaviest engineering activity, and therefore, the heaviest change. “Some contracts involve multiple contractors. Without change management, it would be impossible. You might get some design requirements from Japan and others from Houston. You start to build, then there are other changes you have to incorporate. Then, at acceptance, you need to document changes on the fly to deliver as-built documentation.”
Technologies and culture are converging to manage change in order to improve safety, quality and efficiency—and to help companies improve profitability.
Subscribe to Automation World's RSS Feeds for Feature Articles
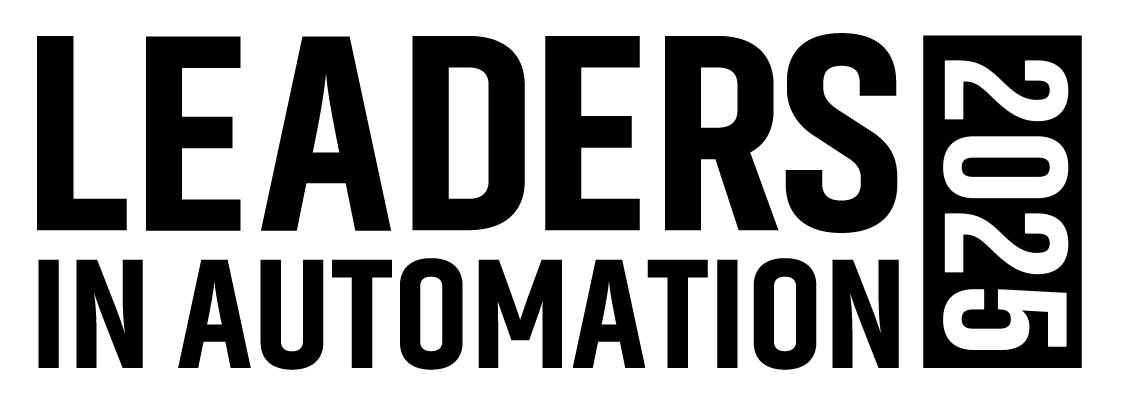
Leaders relevant to this article: