When internal inspectors at Georgia Nut Co. discovered salmonella in the company’s pistachio products in March, they immediately instigated a product recall downstream to their customers—including Back to Nature Foods, a Wisconsin firm owned by Kraft Foods Inc. that used the nuts in trail mix—and launched an inquisition to locate and eradicate the source of the contamination.
Consumer confidence is a delicate issue, especially considering the recent spate of similar recalls affecting a variety of products, and executives understood the potential damage such an incident would do to the company’s brand. However, Kraft was prepared and had the ability to track and trace ingredients and products both downstream to retailers and upstream through its supply chain, and rapidly identified and recalled suspect shipments, and traced the contamination to its source—a supplier in California.
“As part of our food safety program, we have systems in place at both Kraft plants and external manufacturers that help identify potential issues before they become problems,” says Adrienne Dimopoulos, a spokesperson for Northfield, Ill.-based Kraft Foods. “We require extensive monitoring and quality testing throughout the production process, and we require that each supplier and external manufacturer have a food safety plan in place.”
Because Kraft caught the problem early, it was able to avert the potential damage to the company’s brand. However, other companies haven’t been as diligent about their supply chain practices, or as fortunate when issues arise.
More recently, Peanut Corp. of America (PCA), Lynchburg, Va., filed for bankruptcy under Chapter 7 in a Virginia court after salmonella in its products led to 600 people falling ill, and as many as eight deaths in the United States. Some 1,800 products were stripped from retail shelves in one of the largest recalls in U.S. history. The contaminant was traced to irrigation water at a Mexican farm that supplied the company. Under Chapter 7, the company liquidates its assets to repay creditors, rather than reorganize. PCA will cease to exist.
Risk exposure
These are just a few examples of risks that manufacturers are exposed to through their supply chains. Others include pathogenic outbreaks such as H1N1 flu (originally referred to as swine flu) closing factories or—even worse—borders; Somali pirates seizing the ship transporting your materials; earthquakes and hurricanes; wildly fluctuating transport and commodity prices; and, last but not nearly least, the economy. The survivability of one of your key component suppliers has become more than another “what-if” scenario in too many cases. And these are just the acute factors, the headline grabbers.
“Risk management has become a tremendous issue for the global supply chain,” says Bob Ferrari, an independent supply chain analyst and blogger. “[A severe incident] could literally take down your brand.”
The economic crisis has been particularly bad for manufacturers, says Ferrari. “In the age of Just-In-Time, a lot of companies really embraced Lean Manufacturing processes. When the downturn hit in the late part of 2008, production literally just stopped all over the globe. So now, basically, supply chains are sitting there without inventory, waiting for signs of recovery. In China, there are reports of thousands of factories that have shut down. This started in low-margin businesses like toys and apparel, and has spread to more robust industries like consumer electronics.”
Analyst Noha Tohamy at analyst firm AMR Research Inc., in Boston, agrees. Supply Chain Risk (SCR) has become one of her primary focus areas, and she conducts a quarterly survey of procurement executives to see what risks are top-of-mind and what strategies they are implementing to ameliorate them. “A lot of companies have seen a lot of their suppliers file for bankruptcy,” she says. For example, Toyota has more than 100 suppliers at risk of becoming financially insolvent.
The results of the most recent AMR survey, conducted in February, showed that reduced consumer spending had become the top risk. In December, this issue was a distant sixth, following rising fuel costs, rising transportation costs, commodity price volatility, intellectual property infringement and supplier product quality failures. “This was the first time a demand issue became the top concern. It’s usually on the supply side. [Supply chain managers] don’t know what demand is going to look like post-recovery. They need to plan for the recovery and don’t know how to change their manufacturing or sourcing because they don’t know what’s going to come next.”
Collaboration key
The top mitigation strategy in that survey was closer collaboration with suppliers. “People have been doing collaborative business continuity planning for a long time, but what’s really new is the granularity they are going to. Dual sourcing and multi-sourcing for critical components is also on the rise. They don’t want to be reliant on one or a few suppliers, so if something bad happens to them, they aren’t compromised,” Tohamy says.
Mike Mekanik is trying to address just such a risk right now. As a project manager with Virginia’s Philpott Manufacturing Extension Partnership, Mekanik is trying to design a program for a major shipbuilder supplying the U.S. government. “They have a supply chain of about 2,000 suppliers, down from 3,600 18 months ago,” he says. “They have some suppliers where they represent 80 percent of the supplier’s business. But in many cases where they represent a smaller proportion of the output, the rest of it has disappeared and they are in trouble. That’s really frightening for the shipbuilder because they can’t just snap their fingers and materialize another source of components.”
According to Ferrari, the whole multi-sourcing approach is in the middle of an economic tug of war. “In some industries where supply chain is seen as a cost of doing business (rather than a core skill), their first reaction to the economy is to reduce costs and squeeze the supply chain to reduce the number of suppliers they are supporting. However, that increases risk to the brand and to the business. Whittling down the supplier base isn’t a good idea. Maybe the ones you keep won’t survive the economy. Maybe they are cutting their own costs and that will impact their service to you. All of that is becoming part of the executive agenda and giving a lot of procurement people sleepless nights.”
“Generally speaking, companies don’t spend enough time with their suppliers,” says Julie Fraser, principal industry analyst and president of U.S. operations for Cambashi Inc., in Boston. She adds that with the recent H1N1 flu issue and reduced travel budgets, they will be spending even less in the foreseeable future. “People who have implemented some kind of collaborative tools will have a huge competitive advantage. The people who have made the investment are pointing to it and saying, ‘This is my pay-off.’ There are a lot of vendors that offer these kinds of systems, but our research indicates that they haven’t been spread deeply into the supply chain.”
In fact, Datacraft Solutions Chief Executive Officer Stephen Parker estimates that actual market penetration of any kind of kanban system is only around 20 percent, with less than 10 percent actually automated. Durham, N.C.-based Datacraft provides supply chain management solutions in a “software as a service” or SaaS, model. Parker says that in their rush to adopt Lean Manufacturing processes such as Six Sigma, many manufacturers have neglected the supply chain. “The build process is only one part of manufacturing. They’ve left out the supply chain.”
Attain traceability
Attilio Bellman, Ph.D., senior director, process industries, at Siemens IT Solutions and Services, in Norwalk, Conn., agrees with Parker’s estimates. “Even some packaging lines are very manual. The lack of control around track-and-traceability of products in the supply chain is a common denominator across all supply chains,” Bellman says. “I’ve visited many clients in the food industry. They don’t have automated ways to track recipes, for example. The work is mostly manual. The ability for very detailed track-and-trace of raw materials up and downstream is there. They just aren’t using it. People will tell you it’s OK to use manual solutions, but then they’ll tell you there are delays, and that they have to do larger recalls ‘to be sure’ they don’t allow contaminated or defective product into the market. I think companies generally don’t have the right tools in place.”
However, that is gradually changing. In November 2008, AMR Research estimated that the supply chain management applications market will grow by 7 percent annually for the next five years, from $6.5 billion in 2008 to $9.2 billion in 2012. Furthermore, AMR suggested that the global recession would actually drive supply chain technology adoption.
“We did some executive forums and found that most people we asked said they didn’t have a risk strategy,” say Andrew Kinder, director of product marketing for SCM at Alpharetta, Ga.-based Infor Global Solutions, an enterprise software supplier. “They assumed that SCR was about natural events like hurricanes. These things are graphic, but they don’t represent the biggest risk.”
“The acute conditions, like swine flu, terrorism and bad weather, are very hard to predict,” adds Trevor Miles, director, product marketing at Ottawa, Ontario, Canada-based supply chain management solutions provider Kinaxis Corp. “The odds of you predicting one of these issues and it coming to pass are very remote. On the other hand, the chronic, day-to-day risks like intellectual property protection, quality control and rising prices, are more predictable and more manageable. Customers, supply…that’s where you can make a lot of difference.”
Kinaxis, Infor and Datacraft all offer solutions that provide manufacturers with visibility into what is happening in their supply chains and the ability to collaborate more intimately with trading partners, something they universally agree is key to any mitigation strategy.
Risk management
According to Robert J. Schneider, managing principal, Risk Management, International Organization for Standardization (ISO), in Geneva, Switzerland, risk managers should work with senior management to embed risk management practices into all mission-critical points along the supply chain. The process should be a continuous engagement with the supply chain process for ongoing assessment and reassessment of the constantly changing supply chain environment.
Schneider identifies three key objectives of an effective supply chain risk management strategy:
• Identifying and prioritizing critical business elements
• Mapping the entire supply chain to show interdependencies
• Identifying potential failure points along the supply chain.
“The ultimate goal of an effective and comprehensive SCR management strategy,” says Schneider, “is to embed risk awareness into all the core elements of the organization, from the C-suite through supervisors and department heads across the various supply chain functions.”
Adds Kinder, “You need to formalize the process of identifying the risks and building them into your plan. Build risk assessment into your day-to-day operations. Build it into the day-to-day process and make it part of everyday life.”
Kinder suggests four best practices for managing supply chain risk:
• Make every employee a Risk Manager. Leading companies in every industry are implementing solutions that empower their executives, managers and staff to proactively manage risk and stay alert to opportunities.
• Monitor and communicate corporate performance in real time. Enterprises must be equipped to quickly detect, notify and assign exceptions.
• Provide a shared foundation that allows all stakeholders to collaborate to resolve risks.
• Proactively measure performance and mitigate risk through continuous business process optimization.
Subscribe to Automation World's RSS Feeds for Feature Articles
Sponsored Recommendations
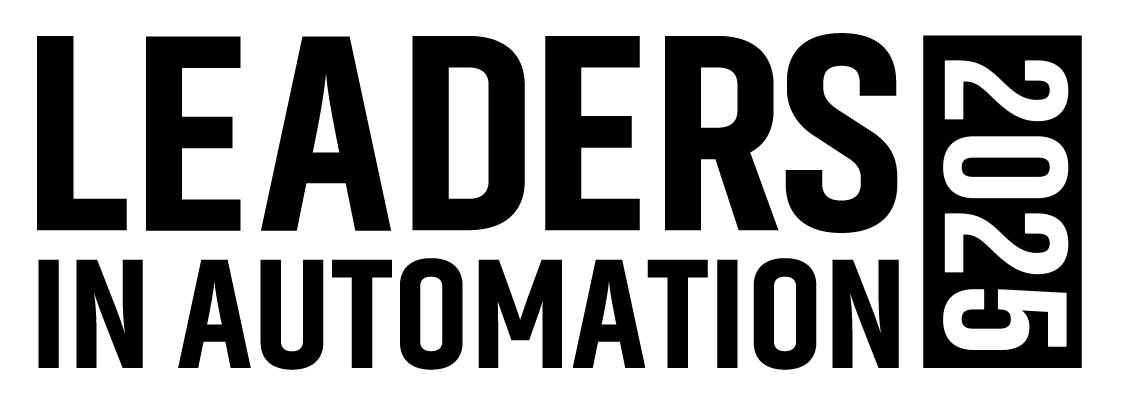
Leaders relevant to this article: