Reducing material consumption requires close attention to every detail, precisely monitoring every sensor and actuator with a speedy network. Manufacturers can see significant benefits by using faster networks.
“The pressure curve was very wavy with the old system,” says Chris Choi, chief technology officer for plastics machine vendor Husky Injection Molding Systems Ltd., of Bolton, Ontario, Canada. “With faster sampling time, pressure tracking becomes much closer to ideal. That lets us control the melting point more precisely, which results in much thinner walls.”
The mainstay in shortening those sampling times is a faster device-level network. Husky is one of a growing number of companies that’s using Ethernet as its only network. Though some vendors argue that existing fieldbuses are better suited for input/output (I/O) device level communications, engineers such as Choi feel that the benefits of Ethernet far outweigh the downsides. “Profibus and proprietary connections are slower,” he says. “With Ethernet, we don’t have any latency, so the whole system goes faster.”
That speed is the key to letting its customers save money and reduce waste with thinner walls, he explains. In a volume production run of 55 million parts per year, trimming just two grams from a 22-gram package can save $180,000. To make that happen, Husky employs one of the real-time Ethernet technologies, EtherCat, throughout the system. However, Choi muses that customers couldn’t care less what architecture the equipment uses so long as they can save materials, which also helps them win sales in this environmentally conscious era.
The equipment designers who help companies such as Husky do need to think about every aspect of their designs. Networks are a key element in the full systems architecture, touching on both performance and cost. Though Ethernet’s speed improvements may seem minor, they can make a big difference.
“EtherCat’s bandwidth is very important. If you’re sensing and actuating, and you get back or send signals using a faster network, you can gain 2 percent to 5 percent without changing anything else,” says Graham Harris, president of Beckhoff Automation LLC, of Burnsville, Minn. Gaining a few microseconds on activities that occur thousands of times each day adds up to significant improvements over time, he adds.
Cabling made easy
One of the reasons that industrial users are extending Ethernet down to the lower levels of their systems is to simplify cabling. Using a single medium at all levels can reduce complexity and give installers more freedom. At the same time, many consumers find this approach also saves them money.
Many Ethernet proponents say that DeviceNet, Profibus, or proprietary wiring schemes that have seen widespread use have far more rules and requirements than the Ethernet cabling that’s continuously being installed in homes and offices. Simplicity and home installations are tightly linked. “Ethernet wipes away a lot of the cabling issues that exist with legacy techniques,” Harris says. “You can string Cat5 (Category 5) cable around with a lot fewer rules of engagement.”
Those Ethernet cables are extremely simple to connect, and they’re much easier to troubleshoot than many existing schemes. That’s important, because wiring can be a time-consuming aspect of an installation. “When you have to hard-wire connections, you’ve got a lot of wires. Every connection increases time and the need for checking out the wiring,” says Mike Hannah, NetLinx Product Business Manager for supplier Rockwell Automation Inc., in Mayfield Heights, Ohio.
That simplicity was important for Husky. Lower costs were a nice side benefit. “We use the same cabling everywhere,” Choi says. “The costs can be significantly lower than with anything else.”
Though cables and connectors used in industrial applications are typically ruggedized, they still leverage the standard’s huge volumes. Ethernet cables for industrial usage can be a quarter of the prices of other cables, Harris says. Ethernet connectors can also be substantially less costly.
DeviceNet and Profibus cable/connectors and CC-Link cabling are all quite expensive, says Ted Thayer, automation systems product manager for vendor Bosch Rexroth Corp., of Hoffman Estates, Ill. “Other accessories that may be used with these networks, such as Profibus switches and CC-Link wireless transmitters, are also very expensive.”
Expenses are trimmed because Ethernet cables can be used anywhere, eliminating the need to stock separate sets of cables and connectors for fieldbuses. Although industrial cables are noticeably different from the versions sold in retail outlets, consumer-grade cables can always be used in a pinch if an Ethernet cable breaks and there is not a similarly sized cable sitting in the technician’s toolbox.
“If a cable breaks, you can run down to the store and get up and running until you get a ruggedized replacement cable,” says Karie Daudt, senior product manager with Turck Inc., a Plymouth, Minn.-based automation components vendor. She notes that these consumer-grade cables should be replaced with ruggedized versions as soon as possible.
But not all applications require costly industrial-grade cables. Plants that don’t have high levels of electronic noise or extreme temperatures can often get by with high-end consumer products. “You can use high-quality Ethernet cables,” says Stephan Stricker, product manager at supplier B&R Industrial Automation Corp., Roswell, Ga.
Though Ethernet can sometimes lower costs and complexity, even its proponents agree that the network can also be more costly than simple fieldbuses. When simple parts such as sensors are being tied to the overall network, a handful of alternatives may prove more cost-effective.
“At the sensor and actuator level, Ethernet can be a bit more costly, and many parts are not yet available for Ethernet,” Rockwell’s Hannah says. Many equipment makers are addressing this by providing bridge devices that link to fieldbuses on one side and Ethernet on the other.
“Bridge modules let you leverage fieldbuses for those parts. With bridges, you still have connectivity with Ethernet so you can get data with alarms and diagnostics,” Hannah adds.
Bridges can eliminate some of the cost drivers that arise when Ethernet is used for I/O-level devices. Managed switches can be trimmed, providing major savings. And though many device-level cables are more expensive than Ethernet wiring, some are less costly, providing more financial incentives for alternatives.
Bridge building
Using bridges also lets plant managers leverage each technology’s assets. Ethernet’s strength is moving relatively large data packets, but it’s not very efficient when sensor-level data must be processed. Field buses such as DeviceNet and Profibus remain viable solutions, particularly in plants where they’re already in use.
Other device-level buses such as Actator Sensor Interface (AS-Interface) are geared toward field installation involving sensors and actuators, offering speed and noise immunity. But they’re not good at moving large blocks of data. Users can also wire safety devices of any kind on AS-Interface.
“Ethernet for I/O level applications only makes sense when the Ethernet system is a requirement for higher level functions and the system has very few inputs and/or outputs,” says Helge Hornis, intelligent systems group manager for vendor Pepperl+Fuchs Inc., of Twinsburg, Ohio.
He says AS-Interface should be evaluated when a machine has about 40 sensors and 10 to 20 outputs. When requirements like these make AS-Interface or an alternative viable, the bridge concept works quite well.
“Combining Ethernet with a secondary low-level wiring solution, specifically AS-Interface, is particularly strong, since it fuses the strength of the two solutions in a way that their respective weaknesses are fully addressed,” Hornis says.
AS-Interface and fieldbuses aren’t the only architectures that are slowing Ethernet’s reach down to device level connectivity. IO-Link is an emerging alternative. The standard created under the auspices of Profibus International is being supported by a number of vendors. For example, Siemens is making IO-Link a focal point in some major trade show booths. Balluff recently expanded its IO-Link Expansion module line, which attaches directly to the Profibus or Profinet network.
The interface is designed for the individual linking of field devices such as sensors and actuators. Though its broad target is the generally same as AS-Interface, promoters note that they address different segments. “AS-Interface is mostly a one-bit bus. IO-Link is for devices with a bit more intelligence built in, like color sensors,” says Carl Henning, deputy director of the Profibus Trade Organization, in Scottsdale, Ariz.
Most engineers say that there’s no easy way to decide which architecture to choose. System requirements, along with the cost and availability of equipment, will tell plant managers which bus should be used for their I/O devices. “It’s expensive to migrate to Ethernet,” says Turck’s Daudt. “You really have to weigh the pros and cons; it’s not a simple task.”
Many approaches
Proponents of the single-network approach note that many benefits are gained when Ethernet extends to I/O devices. As with any technology, there are tradeoffs. Many suppliers say that any cost premiums associated with Ethernet are outweighed by benefits.“Even if the couplers are more expensive, it’s not a big difference. The flexibility you get far outweighs the extra cost,” Stricker says. Most observers agree that Ethernet networks are easier to expand as needs change. Sometimes, additional sub-networks will have to be added, but that expansion is fairly straightforward.
Whether networks are being expanded or being repaired when inevitable problems arise, one of the big benefits of Ethernet is that the tools and skill sets of the people who use them are far higher than with alternatives.“There are a lot of debugging tools for Ethernet,” Stricker says. “You can use them and a consumer PC (personal computer) to debug your network, you don’t need special tools.”
Though some large plants may link a number of Ethernet systems together, Ethernet can also reduce the number of networks within a facility. The network has enough bandwidth to handle safety and motion—functions that have typically used dedicated communications schemes. That provides a big benefit. “If you put motion products or safety networks on Ethernet, you really simplify your architecture, eliminating dedicated motion and safety networks completely,” Harris says.
Vendors are coming up with new ways to reduce complexity, which often means lowering costs. In networking, varied topologies can be structured to meet the wide-ranging requirements of the industrial world. Those configurations continue to evolve.
ODVA Inc., formerly known as the Open DeviceNet Vendor Association, completed documentation for a topology called the device level ring (DLR) last year. This linear scheme lets multi-port Ethernet devices work in ring topologies. That simplifies layouts and lowers costs, while also improving uptime by detecting breaks and reconfiguring communications around them. “With a DLR, customers don’t have to buy a number of switches to go to the device level. They can create a linear daisy chain,” Hannah says. “That’s not new, but using a device level ring lets you have a ring master that can recognize breaks in the cable and route communications the other way to minimize downtime.”
Conventional networking architectures used for years are used in different ways depending on user requirements. In some applications, suppliers recommend using a star architecture with a central hub surrounded by devices operating under its control. That can save a lot of wiring. “With Ethernet, you can make one machine a hub and have a few devices around it connected directly to the hub,” Stricker says. “That’s much easier than networks that force people to go back and forth with cables.”
That may be the most effective approach in some environments. But in others, the star topology is less desirable. Multi-port devices let companies build long strings of devices. “People are installing switches with two ports so they can use linear topologies instead of a star,” Henning says. “Stars don’t work as well in the factory as in the office. If you use a central switch, you need an individual wire running to each device.”
Regardless of the architecture used on the plant floor, Ethernet boasts far better remote access than alternatives such as fieldbuses. When the network is used throughout the facility, an operator sitting at home or in a plant halfway around the world can communicate directly with the actuators on a specific piece of equipment.
“When you’ve got Ethernet at the I/O level, you have better access to diagnostics information and alarming. That also means you can take corrective action from a remote site when those alarms are sent,” says Marty Jansons, a networking consultant at vendor Siemens Energy & Automation Inc., of Alpharetta, Ga.
Subscribe to Automation World's RSS Feeds for Feature Articles
Companies in this Article
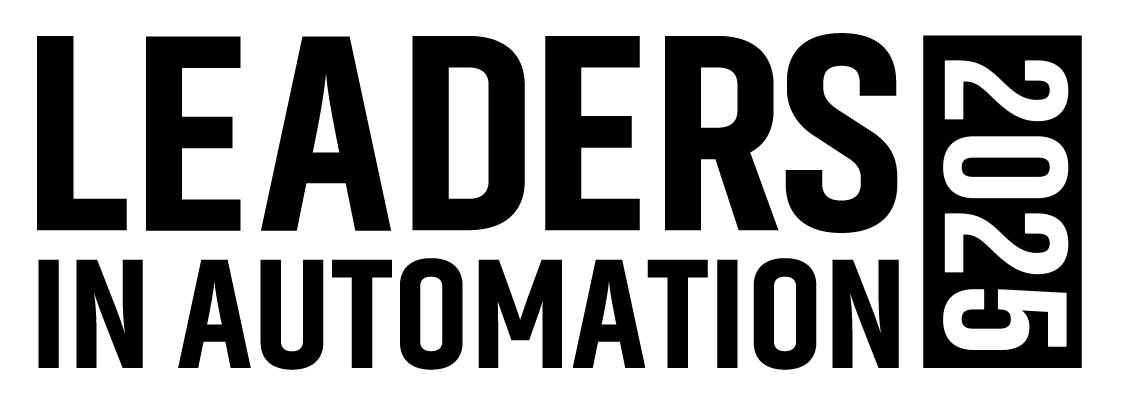
Leaders relevant to this article: