It was Christmas Eve 2008 and Bob Bechtold had one last project to wrap up before heading home. The president and founder of Ontario, N.Y.-based Harbec Plastics Inc. was working on his green energy consumption report for the U.S. Department of Energy, but something wasn’t adding up. Puzzled, he flipped it back to the finance department to check his figures, but he was assured there were no errors. Despite steadily growing the business each year for the past three years, his energy costs had gone down by 35 percent.“I was absolutely flabbergasted. Even though I’ve been preaching about it, I never realized how much impact it would have.”While Bechtold admits to harboring a certain tie-died-save-the-Earth-hippy streak, his alternative/Green energy investments at Harbec have all been driven by economics. The custom injection molding company’s relationship with alternative sources of energy dates back eight years. At that time, the company was completely reliant on the municipal grid for its power, and “brown-outs” were becoming a significant problem. Harbec supplies complicated, one-of-a-kind parts to a range of industries including medical, automotive and consumer goods, with very short lead times. A power disruption is the worst possible problem the operation can encounter. Any interruption means the sophisticated sequences being performed by computer numeric control (CNC) machines and computer-aided design (CAD) stations are lost, requiring six to eight hours to reprogram and restart. Resetting the other machines in the process requires at least another hour of production time, and then the company must account for raw materials wasted due to damaged or lost batches. In June 1999 alone, Harbec experienced three such outages.“Brown-outs are insidious,” says Bechtold. “Everything in the place is computerized, so with a brown-out, we’d not only lose batches, but we’d have to replace burned-out circuit boards, causing even more machine downtime. The utility really had nothing to say about it. They offered to put a power facility a little closer to Harbec, but it would cost us $100,000 and there was no guarantee it would make a difference.”Off the gridInstead, Bechtold started looking for ways to reduce or eliminate Harbec’s reliance on the electrical grid. The solution was the installation of an ultra-efficient Combined Heat and Power (CHP, also referred to as cogeneration) plant based on twenty-five 30-kilowatt (kW) natural gas-fueled Capstone microturbines. This was supplemented with a 250 kW German-manufactured Fuhrlaender wind turbine that meets up to 25 percent of the plant’s power needs. The hot exhaust from the micro turbines is directed to a heat exchanger, which is able to transfer the heat to water. The hot water is then used to heat the 9,000-square-foot plant through radiant in-floor heating systems, and through pre-existing forced-air systems. During the summer, the hot water is sent to an absorptive chiller, which uses heat to create cold water for air conditioning.Despite the fact that the microturbines were the most capital-intensive option available at the time, Bechtold believes that they are the most cost-effective in the long term. The simplified design of the microturbine, which only has one moving part, means the same staff responsible for maintaining the rest of the plant’s equipment require little training to manage the power generators.The overall investment ties back to something Bechtold calls “eco-economics.” “Every decision we make, we make with a view to the bottom line, and renewable energy gives me a lock on my energy costs for the next 25 years. CHP makes us much more efficient. Those things add up to a very nice economic advantage, which, in turn, makes good business sense.“I never lead with the ‘green’ message any more,” he says. “No one cares. But carbon costs money. So who cares about carbon? Just save money. Then the world wins.”But wind power and CHP/cogen isn’t right for everyone. For one thing, not everyone is sitting on a Class three wind site as does Harbec Plastics. And with a veritable windfall of government funding and regulatory demands—such as the Renewable Fuels Standard, which President Bush introduced and President Obama is expected to stiffen—driving research, the alternative energy environment has become incredibly open and innovative.Energy smorgasbordIn fact, there is a veritable smorgasbord of alternative, or “renewable,” energy sources that can be harnessed to help organizations become more energy independent and reduce their carbon footprints. Anaerobic digestion, geothermal power, wind power, small-scale hydropower, solar power, biomass power, tidal power, nuclear and wave power have all become legitimate options.“Those energy sources have always been there, people are just looking at them differently,” says Marcia Walker, program manager for sustainable production solutions with automation supplier Rockwell Automation Inc., Milwaukee. Indeed, the use of ethanol-based fuels was advocated by Alexander Graham Bell as early as 1917. Even then, Bell was concerned about the dwindling supply of coal and petroleum. “People are looking at everything with new eyes,” adds Walker. “It’s exciting because it’s really a driver for innovation. Most initiatives receive some kind of pushback or reticence, but that’s not the case with this.”Don Mack, the PAS bio-fuels initiative lead at vendor Siemens Energy and Automation Inc., Spring House, Pa., is in full agreement. “It continues to amaze me the number of different things I see and hear about. I recently read about the use of termite guts to make bio fuels.” Termites eat wood, which is cellulosic and therefore a potential feedstock for bio-fuels such as biodiesel.“There are so many ways to come at it,” adds Bill Schiel, industry solutions manager for energy at manufacturing software supplier Wonderware, in Lake Forest, Calif. “But some things are constant. Every plant needs a reliable source of energy.”Analysts say the adoption of sustainable manufacturing practices is no longer really a matter of choice. Enormous pressure to be more sustainable is coming from all quarters.“It’s economy-wide; a complete transformation,” says Stephen Stokes, vice president of business and climate change for AMR Research Inc., in Boston. Sustainability is rapidly becoming a critical element in any manufacturer’s business plan “especially when it is considered as a means for driving energy and emission efficiency.“Last year was the year of ‘green.’ This year is going to be about being ‘smart.’ Can we dictate a better, more intelligent delivery of energy?”In his 2008 report, “Crossing the Great Divide: Sustainability as Corporate Strategy,” Stokes writes, “There has been a deafening wake-up call over the past year ... on the importance of constructing robust and diverse energy and resource acquisition/utilization programs. These programs must recognize the dual risks of both cost of purchase as well as likely future costs associated with generations of harmful atmospheric, hydrologic, and other emissions, pollutants and wastes. The green economy is a lean economy, so it is necessary to redefine the key wastes of lean production and seek out innovative and alternative approaches to energy and commodity procurement and use.”Sustainable manufacturingARC Advisory Group Inc.’s Vice President of Collaborative Manufacturing Greg Gorbach, in Dedham, Mass., identified four key sustainability-related threats to the enterprise in his September 2008 report “Sustainable Manufacturing: Remaking Today’s Manufacturing Enterprise for Tomorrow’s Economy”—regulatory risk; energy and resources risk; the impact of social environmental awareness and the need to be a company that consumers and business partners want to remain involved with; and the risks associated with severe weather/environmental changes resulting from global warming.“The shift to a climate-driven economy poses risks to brands as well as corporate reputation,” writes Gorbach. “The right decisions must be made and followed. It is up to the executive team to articulate a corporate sustainability strategy that provides direction for the rest of the organization. Management must establish priorities, make the required tradeoffs, and implement effective management control systems. Such systems will incorporate real-time visibility, shared targets, and accountability.”“A lot of our customers see this kind of thing as risk mitigation,” says Walker. “It’s important to brand management. People won’t buy your products if they think you are failing [to be as sustainable as possible].”Rockwell has made a series of significant acquisitions recently (Incuity, Pavilion) to bolster its sustainable manufacturing offering, while Siemens has partnered with the National Corn-to-Ethanol Research Center at the Southern Illinois University Edwardsville, to support research aimed at speeding the growth of alternative fuel technology.Many other automation vendors, including Opto22 and Bosch Rexroth, have also partnered with academia to sponsor research into alternative forms of energy, sustainable manufacturing and the automation systems needed to support them. Still others, like Wonderware and GE Fanuc have long had offerings aimed at the energy industry as a vertical market, and everyone, regardless of their historical focus, is building energy and sustainability-oriented capabilities into their solutions.However, in many cases, these systems are still works in progress.Best-fit control“In our arena, we are reliant on the automation systems and they really don’t exist. We are using technology that was developed for a different purpose. We are stuck in a best-fit situation,” says Dr. Steve Fitzpatrick, president and chief executive officer of Waltham, Mass.-based Biometics, an engineering, architectural design, construction management, validation, CGMP consulting and project management services company that serves the biopharmaceutical and biomass conversion industries.“Most of our control systems were actually designed for use by the oil industry. They have excellent methods for measuring flows and masses. But now, we need that for solids and slurries. We have to find control systems that handle, or are tolerant of, the presence of those solids.”Fitzpatrick says that we are moving into a new phase in history, unknowingly paralleling Stokes’ view that Clean Tech is actually the sixth wave of industrial innovation. “There are three strikes against petro fuels: it’s running out, it causes global warming and it tends to be located behind enemy lines.”Change is inevitable, and for Fitzpatrick, change means dealing with biomass, which means solids. “We need to be able to monitor and control these new types of streams in an efficient and economic way. We deal with high temperatures, acids and erosion. Wood feeds often come in with a high degree of sand and grit and the technology isn’t there to deal with it. That’s a drawback.”At the end of the day, it comes back to Bechtold’s eco-economics.“Energy is cheap as chips right now,” says Stokes. “It’s a no brainer that we treat it with contempt. But that is going to change.”
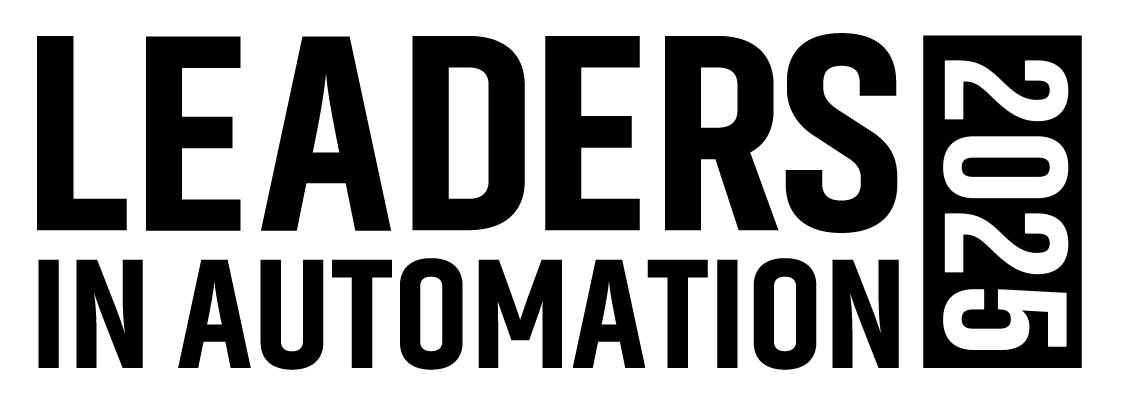
Leaders relevant to this article: