“One of the great innovation challenges today is energy efficiency,” states noted innovation author Andrew Hargadon.There is no doubt that “green” can be a divisive topic. There are some circles in which the dropping the name “Al Gore” is considered impolite. But when word spread that Automation World was working on a green engineering article, just about every supplier in the automation industry came forward with a “green” or “sustainable” story to tell.Five years ago, an energy efficiency story typically focused solely on electric motors—either encouraging engineers to switch to Premium efficient motors or to add variable frequency drives, or both. Now the story encompasses these and much more. In fact, process automation supplier Yokogawa Electric Corp., of Tokyo, sent a 48-page brochure that details how both inside the company and with its customers, the company pushes green initiatives from energy savings to reducing emissions.Ideas that promote green automation and sustainability exist everywhere, it seems. Technology provider companies have scientists and engineers looking into many technologies to discover products to help customers accomplish goals such as reducing waste, improving energy efficiency and the like. Fred Discenzo, manager of diagnostics and sensors, advanced technology, at automation supplier Rockwell Automation Inc., in Mayfield Heights, Ohio, studies what types of sensor technology exists or needs to be developed to advance the company’s sustainable initiative. “We have proposals out for a number of projects,” says Discenzo. His team is looking at sensors that would be a vital part of a process system for extracting oil from algae. Investigations into other anaerobic digestion systems, such as converting animal and food waste into fuel, are also in the works.“For example, there are 1,000 grocery stores in Ohio that generate over a ton of waste per day each,” Discenzo says. “If we could make a digester easy to use for grocery store workers to convert this material into fuel that could perhaps reduce or eliminate the energy purchases of the store, this would have a significant impact on the energy grid. Ohio and many other states now have directives on the amount of energy that must come from alternative sources.” The key technology to make systems such as this feasible lies in sensors that sense chemical and biologic conditions, and that is just what Rockwell is working on.Ask Brian MacCleery for ideas, and it’s hard to stop the flow. MacCleery, who is senior product manager, embedded and control, at automation supplier National Instruments Inc. (NI), in Austin, Texas, has been researching green projects and returns through general sources, as well as through the work of NI’s system integrator partners. “There is a huge return on investment (ROI) in retrofitting existing motor systems using field-oriented control (variable frequency drives) and energy efficient motors,” MacCleery says. “There’s a pretty cool report from the Lawrence Berkeley Labs on energy efficiency in wet corn milling. You can couple variable frequency drives to model predictive control based on ROI and net present value.”A team at sensor manufacturer Sick Inc., in Minneapolis, searched for a project to support its objectives to reduce its carbon foot-print under ISO 14004—an Environmental Management Standard promulgated by the International Organization for Standardization —and began thinking about all the styrofoam the company used to pack light-curtain components. Styrofoam offers good rigidity and protection, but it isn’t recyclable and is harmful to the environment. The company was using die cut pieces especially made for each product that generated much waste.Manufacturing Manager Dan Wink says that the main constraint in eliminating the styrofoam was the need to protect the product during shipping. The team evaluated a solution entirely of corrugated cardboard, but unfortunately, it didn’t offer enough protection to the parts, as they learned after a series of “drop tests.”Expandable foamThe team searched further for solutions and found one through a distributor—Jesco Industrial Supply, which partners with Sealed Air Corp. It presented the idea to use Instapack foam.Wink describes the process, “This is an expandable foam, like insulation. It comes in a liquid state. The equipment dispenses liquids into a bag and seals it automatically. You put the bag in a specially designed mold to form a shape that will protect the product. The resultant block when it hardens matches the product with nearly zero waste. What sold us is that the material is CFC/HCFC (chlorofluorocarbon/hydrochlorofluorocarbon) free, which supports the global RoHS (Restriction of Hazardous Substances) movement, and it can be recycled for various other purposes, such as by grinding for filling into such products as cushions for patio furniture. The material can also be burned in waste energy facilities with very little ash. Some municipalities burn waste for energy, and this material works very well for that purpose. It took about nine months to put the whole project together, and we saw a ROI of less than six months.”Electric motors are used in all types of manufacturing, from pumps and fans to conveyors. They remain a huge user of energy in manufacturing. The U.S. Energy Policy Act of 1992 (EPAct) included electric motors within its scope as it targeted national energy reductions. Kitt Butler, director of motors and drives at Advanced Energy, Raleigh, N.C., a nonprofit consulting, testing and research organization that focuses on industrial energy issues, points out that the U.S. Energy Independence and Security Act of 2007 (EISA) is slated to go into effect in December 2010. Butler provides input to the U.S. Department of Energy (DOE) organization charged with developing regulations to enforce the Act. This piece of legislation broadens the scope of coverage to smaller, two-digit frame size motors.Rich Mintz, national product manager of drives vendor SEW Eurodrive, in Lyman, S.C., points to an innovative approach developed for one application that generates nearly enough electricity to run the application—by using some characteristics of modern variable frequency drives.“We have an application where a stacking crane operating in a two-dimensional x-y axis picks and stores products in a high bank of shelves. The motors of both coordinates need to accelerate as the crane moves, from say, lower left to upper right of the unit. The crane, plus the product, can be very heavy—perhaps up to 20 to 30 tons. When the motor needs to decelerate, it generates a lot of energy that was just burned off in the braking resistor. We asked, what if we could coordinate the sequence of moves such that we could decelerate one move, capture the energy and use it to power the other move. With a programmable logic controller, we could calculate the travel times and optimize when to make certain moves. We were able to save 25 percent on energy without adding extra hardware.”Still on the topic of variable frequency drives, Rafi Wilkinson, product manager at Yaskawa Electric America Inc., Waukegan Ill., another automation supplier, describes the company’s new Matrix drive technology. The construction is direct AC-to-AC electricity without the usual intervening DC bus. The matrix name comes from the innovative array of insulated-gate bipolar transistors (IGBTs) that provide the controlled current pulsing to drive motors efficiently. “Power comes out of the drive with low harmonics and inherent full line regeneration. It also has a more sinusoidal current pattern that reduces standing wave phenomenon that has the possibility of burning out motors. With this construction, when we put power back out on the grid, it is cleaner power.”It’s a good idea to study the entire facility if you’re about to undertake a project to realize energy savings, says Corey Morton, product manager at supplier B&R Automation,in Roswell, Ga. “You should walk around at various times and get a sense for how they are operating. Do they leave lights on all the time? Are air compressors running all the time? You also should implement measuring technologies in order to understand where you are. We can help customers figure out how well they are using their equipment. One thing is to look at how many products they get out of a machine in a period of time. If they can increase from, say 50 to 100, that translates to energy efficiency.” To view a list of useful websites on Energy Efficiency,go towww.automationworld.com/feature-5243.Green by PDATo comply with federal clean air regulations, mercury emissions from coal-fired power plants must be continuously monitored. The proportional measurement technique requires sampling rates to be continually adjusted to remain in proportion to stack flow. In addition, all calibration, maintenance, and leak-checking modes must be automated. NI integrator Data Science Automation (DSA), of Pittsburgh, developed a system using a programmable automation controller (PAC) that operates remotely, controlling the sample collection for as long as a week. The only computer connection is an RS-485 serial network output line to a data logger. Therefore, all control and programming of the PAC, as well as all user feedback, is through a wireless connection on a personal digital assistant (PDA) running the NI LabView PDA Module.Richard Brueggman, president and founder of DSA, says, “We get into all sorts of projects. We’ve been part of the NI systems integrator alliance for 15 years. In this case, the customer wanted to automate the process for mercury emissions monitoring. We designed the product for them.”Timothy Nolan, consultant and lead engineer on code development for the project, says the project was more complex than it might appear on the surface. “We had to take a sample and match the rate of flow in the stack, then compensate for a number of environmental conditions. What we accomplished was to reduce manual labor, plus assuring the accuracy of the calculations.”“The remote location of the system and lack of network connection meant that the device would run ‘headless’ with no computer connection,” explains Nolan. “The deployed executable communicates with a rugged PDA through a shared variable library with the NI cFP-2120 as the shared variable server. The variables are network published and an 802.11 wireless Ethernet bridge connects the NI cFP-2120 Ethernet port to the wireless capability of the PDA. Both system commands and changes of program state are communicated through the PDA, which can also display and change system settings. Other than beginning the automated sampling mode described above, the PDA is used to operate several user-interactive modes.”Taking a macro view, Brueggman says, “I’m thrilled as an owner to have the opportunity to contribute these types of applications to our nation. I’m an environmentalist at heart and active in conservation. When we have the opportunity to take on projects that aren’t destructive but contribute to the health and well being of the planet, we wish we could do more.”Adds NI’s MacCleery, “Some politicians look at this issue as a net cost to the economy, not as additive. Renewables are an opportunity for growth.”Does it pay?Gathering information is seen as crucial by almost everyone. Using the information is often the problem. In order to use it, you must be able to see it. Bill Schiel, industry solutions manager for energy at manufacturing software supplier Wonderware, in Houston, notes that some of his firm’s customers are starting to use human-machine interface (HMI) software to accumulate and visualize energy management key performance indicators to see how they are meeting their goals. Energy management goals are now high on corporate lists, says Schiel, either because management believes that it looks good on the annual report or because they realize that it helps cut costs.Monitoring and information gathering can have broad application. Marty Etzel, vice president of sustainability solutions for SAP AG, in Newtown Square, Pa., sees several areas in which products of this sort can help customers’ sustainability efforts. “A big topic this year is registration, evaluation and application of chemicals,” Etzel observes. “Companies are going to have to start reporting chemicals. The future could be detailing the carbon footprint of a product.”Etzel describes this arena as “a bit like the Wild West right now.” But once things get standardized, it is an application area that will become increasingly visible, he believes. “There is a growing interest in sustainable performance reporting. More companies are preparing sustainability reports issued annually. Outgas and emissions monitoring management is going to become increasingly important,” Etzel predicts. “Information technology also has the potential to have a huge impact on corporate energy management programs.”Advanced software technologies such as advanced process control, model predictive control and simulation can pay huge dividends if implemented and used correctly. A well-instrumented plant coupled with up-to-date software can provide a wealth of information and decision-making help for managers.Doug Johnson, director of global energy management for automation supplier Emerson Process Management, in Austin, Texas, says, “If you have on-site electric power generation, say, boilers, the question is how to improve efficiency of generation and the mix of managing energy you generate, buy and send back to grid.”And that’s just one question of many for managers and engineers evaluating energy savings investments, Johnson adds. “There are a lot of energy savings investment options. Some of the options gain with automation. You can improve the visibility of critical measurements to know what you didn’t know before, like the heating value of complex fuel mixes,” he points out.Measuring the right parameters eliminates guesswork, Johnson says. This takes wise instrumentation. Reducing variability with advanced smart optimization allows manufacturers to increase output while reducing energy and carbon emissions. Implementing advanced process models and simulation helps find out what works best and keeps operators sharp.Making real-time decisions in complex and changing situations, such as which boilers and turbines to run, or how much electricity should be produced, or which fuels should be burned, requires advanced optimization systems, says Johnson. “It’s like a modern jet fighter pilot who needs computers to help fly, because everything is so complex and things happen so quickly. Then, technologies such as wireless allow you to measure things you never could measure before to provide more information for your models.” “You used to do green engineering in order to be a good corporate citizen. Now, managers are measuring the return on investment for green projects,” points out Joe McMullen, product manager, process engineering, for Invensys Process Systems, another automation vendor based in Foxborough, Mass.And the projects can pay off, McMullen notes. “We have an optimization product where you can put in the cost of energy as a variable and then optimize the process. It connects to the process historian and brings the data into the model and reconciles the data. You can run different scenarios. Green engineering is here to stay. That’s why I push so hard within the organization. Not that we didn’t before, but we didn’t think about it in that way—how it helps clients. Now you need to be green to be competitive.”Related Sidebar - Clean Burning CoalTo read the related sidebar accompanying this article, go to www.automationworld.com/feature-5242.To view a video interview on alternative energy with Gary Mintchell, Editor in Chief of Automation World and Al Novak, Director of Alternative Fuels at Emerson Process Management, please visit http://snipr.com/bmlt8
Companies in this Article
Companies in this Article
Sponsored Recommendations
Sponsored Recommendations
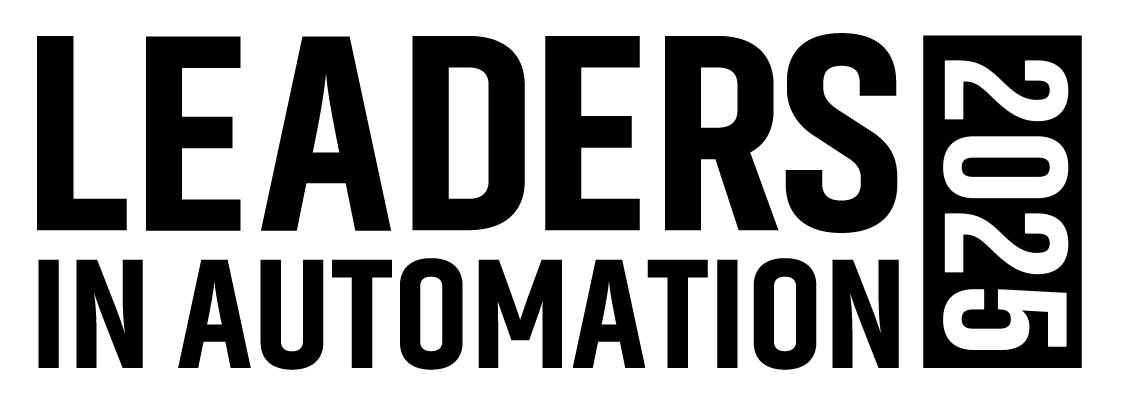
Leaders relevant to this article: