John Marioni, U.S western regional sales director for KUKA Robotics
Corp., landed his first solar industry customer in late 2006.
“That was an awakening for me,” says Marioni. “I thought, ‘Wow, this is a cool customer, and I wonder if there are others out there.’ ” Sure enough, says Marioni, when he looked around, he discovered solar manufacturers “popping up left and right” within his multi-state western territory, and all were prime candidates for the improved productivity, flexibility and cost reduction that robotic automation can bring. Today, says Marioni, who is based in Bothell, Wash., “solar is definitely where the majority of my [sales] numbers come from.”
No one is predicting that robot sales to the solar photovoltaic (PV) industry could ever match those to the automotive industry. The car makers and their suppliers still account for more than half of all robotics industry orders, even despite the current economic downturn. But during the past couple of years, accelerating growth in the solar space has definitely grabbed the attention of robot vendors.
Last summer, for example, Adept Technology Inc., a Livermore, Calif., supplier of light-duty, vision-guided robotics, rolled out an integrated product line named Adept Solaris that is aimed specifically at the market for high-speed solar cell wafer handling and inspection. “If you look two or three years out, I would expect that a quarter to a third of our business will be in solar,” says John Dulchinos, Adept president and chief executive officer.
Looking up
Others are equally upbeat. “For robotics, the solar industry is definitely exciting. It represents a growth curve that we haven’t seen for quite a while outside of industries like medical or pharmaceutical,” observes Rush LaSelle, general manager for the West office of Fanuc Robotics America, in Lake Forest, Calif.
Opportunities for flexible robotic automation abound throughout the solar PV production process, the vendors say, from the handling of polysilicon ingots and bricks at the front end, through high-speed solar cell wafer handling tasks, to the large solar panel and module assembly applications at the back end. For many solar start-ups that are looking to develop their production processes, the robot vendors can contribute valuable process knowledge gained in other industries. “We have good experience in certain segments in the flat-panel manufacturing areas, such as TVs, for instance, and other applications where we’ve handled flat-panel-type product,” points out Dan Shumaker, market research manager for Motoman Inc., a West Carrolton, Ohio-based robot vendor.
As robot makers gear up to compete for the solar business, they are eyeing potential for very rapid growth. To be sure, the current economic downturn and tight credit environment is putting a strain on the solar industry today, and some solar manufacturers have recently announced layoffs. Despite continuing growth in installation of solar panels, supply has lately been outstripping demand, say industry watchers, which is putting downward pressure on pricing. But the long-term outlook for solar manufacturing appears bright, most agree. World solar photovoltaic market installations reached a record high of more than 2.8 gigawatts in 2007, up by 62 percent over 2006, according to Solarbuzz LLC, a San Francisco-based solar energy research and consulting firm. And some industry watchers see that number soaring to 10 to 15 gigawatts by 2012.
The goal is “grid parity,” the point at which solar photovoltaic electricity produced without subsidies is equal to or cheaper than electricity produced by other means. That point is still several years away, say industry experts. Former President George W. Bush set 2015 as the date for grid parity in the United States, though other countries are targeting earlier dates. But the lack of grid parity today is not slowing the rush toward solar technology development and production.
“In the long term, it’s very clear that solar is something that will achieve grid parity with other energy sources, and once that happens, things will really take off,” says Kevin Steele, industry segment manager, semiconductor and solar, for automation vendor Bosch Rexroth Corp., in Pleasanton, Calif. “So at this point, you’re looking at an enormous number of investors going into this market, and a large number of players who are trying, as quickly as possible, to gain market share,” Steele says.
That is fueling a strong market for automation, as solar manufacturers strive to bring down costs and achieve economy of scale, and to prove that their particular flavor of solar technology is a better solution than that of the next supplier. “A lot of these solar companies already have a couple of years worth of orders, and they don’t even have their plants built yet, so it’s a race to get these plants built, get them automated and get them producing product,” observes KUKA's Marioni.
Thanks to generous government incentives, today’s largest solar market is Germany, followed by Spain, Japan and the United States, where California leads the way with various state incentive programs in place. All eyes now are on the administration of new U.S. President Barack Obama, which is expected to launch additional federal programs aimed at boosting alternative energy technologies, including solar.
“Based on the feedback I get, sooner or later, the United States will definitely be number one in megawatts or gigawatts produced from solar power. But the timing for when that happens depends very much on government programs,” opines Carsten Busch, industry global segment manager, solar, for ABB Robotics, in Friedburg, Germany. Busch sees global solar market growth slowing to perhaps 15 percent in 2009, down from 30 percent to 40 percent during the past couple of years. But like others, he sees a burgeoning market going forward.
Three to four years ago, says Busch, most manufacturers of solar cells or solar panels had plants with production capacities of 10 to 20 megawatts (MW) annually. But within the last couple of years, many have taken steps to ramp up from small, individual or pilot production operations toward mass production capacities of 50 MW up to 200 MW per year, he says. “The next step now is to build up factories producing gigawatts. And the higher your production size, the more automation you need,” Busch points out.
Production ramp
One company that is making the ramp is Evergreen Solar Inc., of Marlboro, Mass. The company was founded in 1994 based on a proprietary, low-cost approach to making silicon wafers known as String Ribbon technology, developed at the Massachusetts Institute of Technology. For years, the company has had a pilot operation and research and development (R&D) center in Marlboro. That facility is capable of producing about 15 MW per year, says Dan Welch, Evergreen director of process engineering. But about four years ago, with the arrival of a new chief executive officer, the company began a push toward the higher volumes needed to commercialize the technology.
The first move was formation of a three-way joint venture with Q-Cells AG, Thalheim, Germany, and Renewable Energy Corp ASA (REC), of Hovik, Norway. The joint venture—called EverQ—constructed a 30 MW per year capacity solar wafer, cell and manufacturing plant in Thalheim, which began production in 2006. A subsequent 60 MW EverQ plant came on line in Thalheim in 2007, and the joint venture is building a third, 80 MW German factory that will start production this year, Welch says.
Meanwhile, Evergreen Solar has also built an additional factory on its own in Devens, Mass. “That factory is designed to be 160 MW,” says Welch, with the first 80-MW phase now in ramp-up, and scheduled for full production by the end of the first quarter. The second, 80-MW phase will be fully operational by the end of the second quarter, he adds.
While many solar industry manufacturers perform only one of the three main components of solar PV production—wafer growth, solar cell fabrication or module assembly—Evergreen is an integrated producer that does all three. And the company relies on robotics in all three production areas.
In the proprietary String Ribbon wafer growth process, two high-temperature filaments are continuously pulled vertically through a silicon melt. In the process, the molten silicon spans and solidifies between the filaments to form a ribbon-like wafer about 80 millimeters (mm) wide and 190 microns thick, says Peter Kane, senior member of the Evergreen technical staff. As the ribbon is pulled into what is called a fly box, a robot grabs the leading edge, cuts off a 150-mm length and deposits the wafer into a carrier. This operation relies on a custom robot manipulator designed for the task, says Kane. But for the other production operations, Evergreen relies heavily on standard commercial industrial robots.
Be gentle
In the solar cell production area, wafers undergo a series of chemical processing steps requiring the wafers to be moved from conveyors into and out of multiple machines. It’s a task that couldn’t be done without high-speed robots, says Welch. “To do a 160-MW annual output in Devens, we’re running 2 million wafers a week, so if we tried to do that with manual or human labor, we could never get the volume and the consistency we need,” he points out.
“If we had people handling our wafers, our yields would be horrendous,” adds Kane. Because the razor-thin solar wafers are brittle and extremely fragile, they could not be handled by human operators without high rates of breakage, he explains. This problem can be avoided with robots designed to be gentle. One method used by vendors, including ABB, Adept and others, is the use of Bernoulli grippers. Based on the Bernoulli effect, these grippers rely on a high-velocity airstream to ensure that wafers are lifted gently without contact being made.
For its solar cell wafer handling area, Evergreen Solar relies on high-speed Delta-style parallel robots, primarily ABB Flexpickers supplied by ABB or Manz Automation, a Germany-based robotic integrator, says Kane. “Between EverQ and Devens, we’ve got almost exactly 100 parallel robots in production,” he notes. The four-axis, three-arm parallel robots are overhead mounted, and can handle more than 150 picks per minute. Integrated vision technology not only provides robot guidance for wafer picking, but also for quality inspection. “We look for cracked cells or edge defects, things like that,” Kane relates.
In its solar panel production areas, Evergreen relies on KUKA robots in at the Devens plant, and on robots from Reis Robotics, a German supplier based in Obernburg, in its EverQ operations. “They’re mostly large, six-axis robots for handling fairly large payloads. The panels typically weigh up to 30 or 35 pounds and the end-effectors can weigh quite a bit more than that,” says Kane. “We have about 28 six-axis robots in Devens.” A variety of robot models are used, some on gantries for axial movement, others stationary, for numerous glass handling and panel assembly applications.
In the panel production area in particular, Evergreen has found the flexibility of robots to be useful during the fine-tuning of its production processes. In one instance, for example, modification of a tape head on a robot that applies edge gaskets to the solar modules required a corresponding change in motion—a task that was made easy by simply reprogramming the robot, says Kane.
Help me
In fact, as noted by Fanuc’s LaSelle, the flexibility of robots is especially important in an emerging industry such as solar, in which many manufacturers are start-ups that are still perfecting their processes. “There are a multitude of people in the space that have a product, and from a physics and lab standpoint, it’s fantastic. But from a manufacturing standpoint, it’s in need of refinement,” LaSelle observes. This is where robot manufacturers and experienced robot integrators can help, he notes. The work that Fanuc has done with Energy Innovations, a solar industry start-up, is a good example, LaSelle says (see “Robots Make Modules Manufacturable,”).
Robot makers say that in many cases today, new robot installations are either going in to replace jobs that were previously done manually, or they are being designed into new, greenfield factory operations. Fixed automation is an alternative for some tasks, but many jobs can only be done by robots, vendors contend, due to a need for speed, flexibility and other factors.
As solar technology advances, for example, solar cells are being made increasingly thin—going from about 300 microns to 150 microns or thinner—making them impossible for humans to handle without significant breakage, says Adept’s Dulchinos. ABB’s Busch concurs. “There are companies that are testing our Flexpicker down to a thickness of 160 microns, and even thinner,” Busch says. The trend will necessitate the use of robots such as the Flexpicker and Adept’s Quattro s650, a four-arm parallel robot, these men say.
The payback from robots for solar industry users can come typically in a year, and definitely within two years, says Adept’s Dulchinos. “If you can drive twice the throughput out of the same amount of factory space, you cut your overhead expenses in half, because they’re going out on twice the volume. So the justification for robots is you drive much higher throughput out of a factory” he says. “You save labor, you lower scrap and you improve quality.”
Companies in this Article
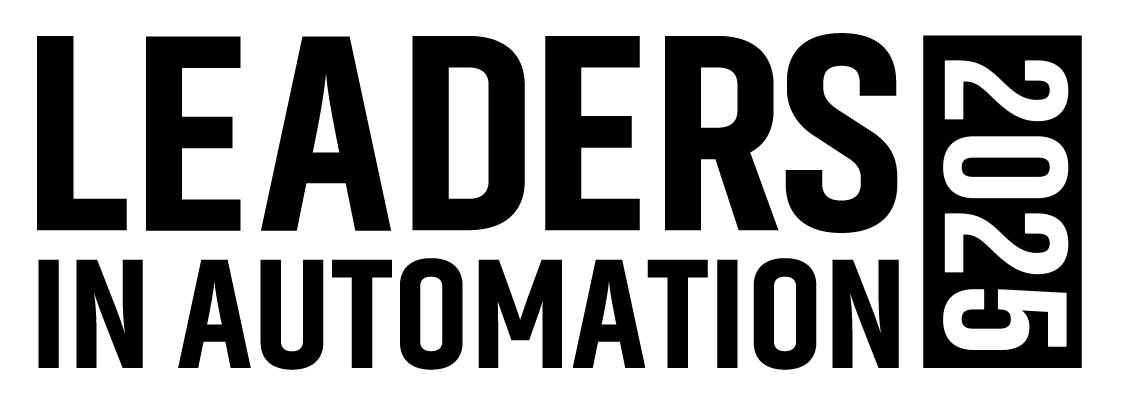
Leaders relevant to this article: