What happens when top-down automation data reaches a machine controller—does it go any further? And, what happens when bottom-up data generated by the machine controller tries to move upward, past the machine controller into the automation system?The automation world has become so complex that there are no simple answers. Taking a holistic view of manufacturing, every machine in a facility has the potential to become a tightly integrated entity in a smoothly running enterprise-wide system. And, taking a machine-by-machine view, every machine in a facility can just as easily work in isolation from any top-down system, quietly sequencing its switches and driving its motors as it pushes a workpiece or process along.Why talk at all?If we cannot solve the puzzlement around how machines, controllers and automation should relate to one another, we can at least look at some of the give-and-take—the opinions and the reasoning for adopting this or that strategy.The first question, of course, is why create an automation environment that reaches into a machine, or vice-versa, a machine that transmits out onto the automation network. After all, a top-drawer accountant sinking into the carpets in walnut acres is unlikely to want to know the X,Y,Z position of a tool, or the flow past a valve at any given millisecond. Even dropping several hierarchies, the plant manager would not have much interest in that information. But the closer you bring the camera to the machine—past operations and production management, down to process supervisor, maintenance crew and finally, to operator—the more important the individual bits and bytes might be.Certainly, operations on any level could do some good things with aggregated data. If a trending chart tells the group that parts are drifting because a tool position is repeatedly out of spec, or a flow anomaly has begun to throw a formula or a process off, they would want to give some attention to the machine. In addition, overall equipment effectiveness (OEE) depends on a broad range of machine data (again, aggregated, to be sure). Those who are tasked with finding all the ways to increase throughput or decrease waste find food for thought in overall machine behaviors.No wonder, then, that middleware and machine controllers have developed more and more avenues for reaching overall automation networks, and from them to enterprise-level systems.Whether these avenues are heavily traveled is a different matter. The isolated machine is still much in evidence. There are, of course, some holes in this approach. When a machine is not connected, no dashboard will reveal to higher-ups how well it is performing, or if it is even turned on. Quality statistics will at best be captured inside the machine controller (one assumes for selective harvest later), at worst by the operator or a quality control resource with a caliper and a notepad. Finally, material and product flow will be harder to track.The truth is, however, in a small to medium facility, sticking with manual data tracking methods is perhaps easier than the weeks or months of effort required to assemble a meaningful automated information flow.“We’re ready to integrate any of our controllers with a plant-wide network,” says Jeff Thomason, manager of turnkey operations for Hardinge Inc., Elmira, N.Y. “The controllers have the hooks, they have Ethernet connectivity, and there’s plenty of capability for data aggregation if someone wants to pick and choose what to send to an automation network. But we’ve almost never been asked to do it.”As a major supplier to discrete manufacturers, Hardinge makes a broad range of equipment: turning machines, vertical and horizontal machining centers, pallet changers, grinders and work holding components. Its customer base ranges from small machine shops to huge production facilities for major multinationals.Future use“We consider the capability as one for future use,” Thomason continues. “We see the need and we’re convinced we’ll see a lot of it in the future, but actually using it depends on the manufacturing philosophy of the company involved. Not many have gone through the exercise of defining what they want to quantify, or answering the question of exactly what parameters they want to see upstream.”According to Thomason, a major stopper has been security issues. “Intranets hold a great deal of promise,” Thomason says. “Having a browser-based dashboard sounds great. You could see a green blip for every online productive machine, or a yellow or red one for a problem, from anywhere. But people hesitate to poke holes in their firewalls. It can be tough to keep a secure connection when unique rules govern almost every element, and every machine installation is unique to a greater or lesser degree. And in our experience, IT usually has a simple approach—‘You don’t breach our system.’ We continue to include integration options beyond the machine in every quote, but only rarely does it happen.”The world of packaging equipment, which straddles both discrete and process manufacturing, echoes this to an extent. “We’ve adopted PackML (for Packaging Machine Language, a programming protocol from the Organization for Machine Automation and Control, or OMAC) in our controllers, but we haven’t been called on to use it yet,” says Paul Zurlinden, manager of technical systems, at packaging machine builder ProPack Systems Inc., Salinas, Calif. Instead, the company focuses on modularity and flexibility of Elau-based controllers within its own equipment. Intelligent servo modules from Elau, a unit of Paris-based Schneider Electric, allow ProPack to dovetail its equipment with other systems at the packaging operations of a number of fresh vegetable, snack food and beverage manufacturers.“Our emphasis is on ease of implementation and space-saving,” Zurlinden says. “There’s always a certain amount of flux and change in production, so we develop systems that can accommodate additions easily.” He agrees, however, that tight integration with plant-wide systems is in the offing: “Many facilities we service are moving into more and more automation, and a lot of people are watching and waiting.”Interestingly, others in packaging experience a relatively high level of adoption for communication beyond the machine. “Seven years ago, we began telling our customers that they could have e-mail alerts or pages, or daily or hourly updates,” says Joe Grove, vice president of engineering for Ossid LLC, Rocky Mount, N.C., a division of ProMach. “Now, a great many are tying into our equipment, for OEE numbers, and for ways to optimize lines in general.”Ossid packaging equipment primarily serves food and beverage producers, as well as meat and poultry processors. “We sell to both huge companies and little ones,” Grove says. “About 40 percent is Fortune 200. When I look back across our engineering presentations, in the past, it was the big companies that said, ‘Just give us the packaging functionality.’ The little companies were the ones who said, ‘What can I do to squeeze the most out of this machine?’ They were the first to want to optimize upstream and downstream.”“Now,” he says, “everyone is feeling a need to optimize. There are more smart factories, much more automation, and much more emphasis on getting defect-free product out the door quickly.”Historically, Ossid offered machines with proprietary controllers, but that has shifted to mainly Allen-Bradley and Siemens controllers, integrating them with industrial personal computers (IPCs) on the hardware side, and National Instruments’ LabView and Microsoft SQL on the software side. The transport layer is Ethernet.Flexibility is key as well for C P Packaging LLC, an Appleton, Wisc.-based specialist in form fill seal machines, primarily for food and pharmaceuticals industries.“From the start, we were looking for ways to design machines that stayed clean, and didn’t touch product or the product side of packaging materials,” says Ray Buchko Jr., C P Packaging vice president of operations. The company’s machine and controller strategies cover both equipment functionality and networking communications. “We wanted integrated motor and drive systems to minimize wiring and connections. You can’t have cables or wires hanging in the machine frame area,” Buchko says. “Chains were out—they are too dirty and too high maintenance—so servo motors were clearly the right thing.”C P has standardized on Bosch Rexroth drive and control components, primarily for engineering advantages (for example, availability of trouble-free servos in cold environments and in the face of high-pressure wash down), but also for communications. Bosch Rexroth controllers employ the SERCOS (for serial real-time communications system, the IEC 61491 standard promulgated by the International Electrotechnical Commission) controller-to-intelligent device interface that exploits Ethernet internally. An available Internet protocol (IP) channel allows direct communication up or down to broader networks, including device protocols, automation communications and enterprise nets.One-cable solution“We’ve incorporated almost every sort of protocol you want to mention,” Buchko says. “OPC (an open communications standard), Ethernet, Profibus, and many more. The biggest enabler in the machine is the use of a daisy chain cable strategy. Instead of a series of cables from each motor, a single cable carries communication data, power and feedback. It allows us to minimize components while maximizing communications.”Connecting machines with automation requires a split focus. The primary face of a machine’s controller is toward making things happen within the envelope of the machine itself—turning motors on and off, rotating a valve or ballscrew so many revolutions (or sending encoder signals to make that happen) and the like. Once the numerical control program is done, the emphasis is on hardware rather than on software. On the other hand, automation networking is far more software-centric. The result is that the two worlds, machine innards and automation schema, simply do not speak the same language.There are a number of bridge strategies that straddle the two worlds and allow them to communicate. One is middleware software; a second is middleware built into the controllers themselves.One middleware software example is Freedom eLog monitoring system from the Infimatic unit of MAG Industrial Automation Systems LLC, Sterling Heights, Mich. Freedom eLog is a Web-based software-based monitoring system that plays across a broad range of machine controllers. It has to. “We have to connect to some 30 brands of machine tools,” says Jim Braun, MAG Americas’ vice president for development and standardization. Over the last 30 years, MAG has assimilated many large machine tool manufacturers globally. MAG products include machining and turning centers, transfer lines, welders, assembly equipment and ancillary equipment.The system provides both basic and detailed information. Among the basic: whether a given machine is running or not. Among the more complex: historical production data or trending, which can transform thousands or millions of sensor and electrical data into quickly scanned visual summaries.Old and new
“We’ve installed it on both old and new equipment,” he says, “and we actually have two very different interfaces. For older equipment—fifteen years old or older—we provide a hardware module that installs in the electrical cabinet. For newer equipment with PC- or software-based controllers, we talk across an OPC interface.” In the older equipment, the installed module taps signals in the controller, translating electrical impulses into data that can be sent across a factory network to servers.In common with many dashboard applications, MAG’s system allows authorized users to drill down to detailed information on a given machine, as well as report on uptime, alerts history, operator availability and more. “The companies that are most successful with it are those that look at all the possible information, then determine what data and reports people need to see,” Braun says. “There are many elements ready to go right out of the box, but every installation is unique. But it’s useful in seeing manufacturing flow and tracking problems when parts go across five or six or more machines from different suppliers.”There is a definite correlation between lean techniques and adoption of MAG’s system: “Our highly successful customers have Six Sigma Black Belts involved—that is, they have people in place who are well trained on work flows, elimination of waste, and ways and means to fix problems that arise. These aren’t places that put reports on someone’s desk and then forget about them.”MAG’s next initiative will be based on MTConnect standards, now in active development. MTConnect is an open, eXtensible Markup Language (XML)-based communications protocol for middleware. It will allow the distribution of data from equipment to higher-level systems, and is being developed by the McLean, Va.-based Association for Manufacturing Technology (AMT) and technical experts from the University of California at Berkeley. In addition to MAG Industrial Automation Systems, technical advisory group members include the National Institute of Standards and Technology (NIST) along with Bosch Rexroth, GE Fanuc, machine tool maker Mazak, Sun Microsystems and 19 others, including end-users GE Aviation and General Dynamics. Technical observers include machine tool builder Okuma America as well as Siemens Energy & Automation Inc.“The initial release spec for MTConnect is just now being born,” Braun explains. “It’s primarily for machine monitoring, but will branch to robotics, tooling, material staging and the like. The emphasis is on user-friendly, flexible systems that can be readily adapted to pass any kind of information back and forth. It has a lot of advantages—it’s open, it’s easy to define new types of data, and it’s tightly focused on manufacturing needs.”The latest tackWe now come to the last strategy: build the middleware into the machine controller itself, a tack increasingly evident in a broad range of controller offerings. “Motion control technology is now blending into wider and wider capabilities,” says Dave Whittenton, marketing manager, motion control business unit, for Siemens, in Nuremberg, Germany. “Operational interfaces are richer and richer, whether machine-to-machine, machine-to-operator or machine-to-plant. Technology now allows systems to exchange information openly.”Whittenton feels it is important to take a holistic view of how a machine and its operator interface with production. “Ability to tie into network topologies is more and more critical,” he points out. “Time-critical motion control is just one part of the equation, and rack-mounted programmable logic controllers roll up everything into one box—human-machine interface, motion control, OEE data, production profiles, and so on.”“If adoption is slow,” he adds, “it’s because manufacturing evolves in micro-steps, not macro-steps. But the micro-steps are adding up, and the need now is to consider every machine as part of an overall system. Production is as much about transferring products into and out of work cells as it is about motion control in each cell. The wider the view, the more approaches are blended into the mainstream.”Sidebar Article - Home Runs—Bad, When it's not BaseballTo read the accompanying article to this story, go towww.automationworld.com/feature-5146
“We’ve installed it on both old and new equipment,” he says, “and we actually have two very different interfaces. For older equipment—fifteen years old or older—we provide a hardware module that installs in the electrical cabinet. For newer equipment with PC- or software-based controllers, we talk across an OPC interface.” In the older equipment, the installed module taps signals in the controller, translating electrical impulses into data that can be sent across a factory network to servers.In common with many dashboard applications, MAG’s system allows authorized users to drill down to detailed information on a given machine, as well as report on uptime, alerts history, operator availability and more. “The companies that are most successful with it are those that look at all the possible information, then determine what data and reports people need to see,” Braun says. “There are many elements ready to go right out of the box, but every installation is unique. But it’s useful in seeing manufacturing flow and tracking problems when parts go across five or six or more machines from different suppliers.”There is a definite correlation between lean techniques and adoption of MAG’s system: “Our highly successful customers have Six Sigma Black Belts involved—that is, they have people in place who are well trained on work flows, elimination of waste, and ways and means to fix problems that arise. These aren’t places that put reports on someone’s desk and then forget about them.”MAG’s next initiative will be based on MTConnect standards, now in active development. MTConnect is an open, eXtensible Markup Language (XML)-based communications protocol for middleware. It will allow the distribution of data from equipment to higher-level systems, and is being developed by the McLean, Va.-based Association for Manufacturing Technology (AMT) and technical experts from the University of California at Berkeley. In addition to MAG Industrial Automation Systems, technical advisory group members include the National Institute of Standards and Technology (NIST) along with Bosch Rexroth, GE Fanuc, machine tool maker Mazak, Sun Microsystems and 19 others, including end-users GE Aviation and General Dynamics. Technical observers include machine tool builder Okuma America as well as Siemens Energy & Automation Inc.“The initial release spec for MTConnect is just now being born,” Braun explains. “It’s primarily for machine monitoring, but will branch to robotics, tooling, material staging and the like. The emphasis is on user-friendly, flexible systems that can be readily adapted to pass any kind of information back and forth. It has a lot of advantages—it’s open, it’s easy to define new types of data, and it’s tightly focused on manufacturing needs.”The latest tackWe now come to the last strategy: build the middleware into the machine controller itself, a tack increasingly evident in a broad range of controller offerings. “Motion control technology is now blending into wider and wider capabilities,” says Dave Whittenton, marketing manager, motion control business unit, for Siemens, in Nuremberg, Germany. “Operational interfaces are richer and richer, whether machine-to-machine, machine-to-operator or machine-to-plant. Technology now allows systems to exchange information openly.”Whittenton feels it is important to take a holistic view of how a machine and its operator interface with production. “Ability to tie into network topologies is more and more critical,” he points out. “Time-critical motion control is just one part of the equation, and rack-mounted programmable logic controllers roll up everything into one box—human-machine interface, motion control, OEE data, production profiles, and so on.”“If adoption is slow,” he adds, “it’s because manufacturing evolves in micro-steps, not macro-steps. But the micro-steps are adding up, and the need now is to consider every machine as part of an overall system. Production is as much about transferring products into and out of work cells as it is about motion control in each cell. The wider the view, the more approaches are blended into the mainstream.”Sidebar Article - Home Runs—Bad, When it's not BaseballTo read the accompanying article to this story, go towww.automationworld.com/feature-5146
Companies in this Article
Companies in this Article
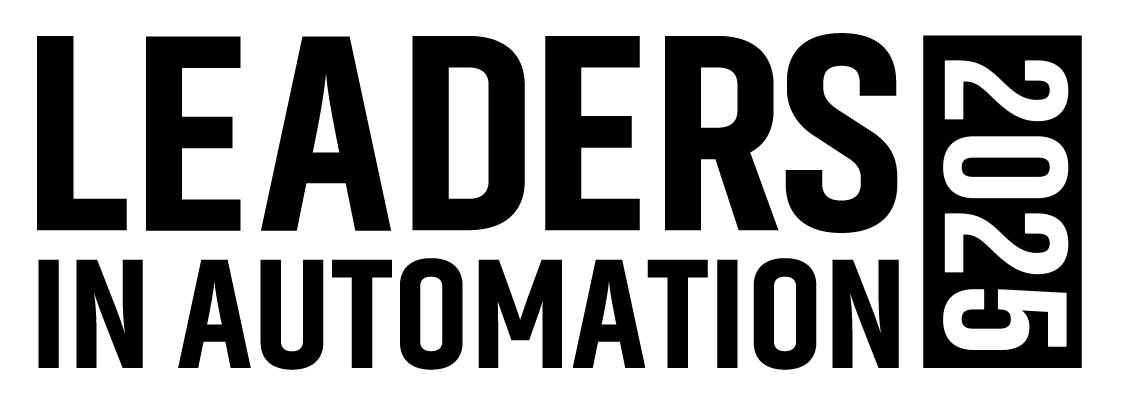
Leaders relevant to this article: