It’s some time in the first decade of the 20th century. Speaking conceptually and totally speculatively, somewhere, at some factory, the first wireless set-up was being concocted by an enthusiast for that brand-new technology—radio. An operator located in production boonies with a transmitter the size of a refrigerator and a Morse code key feeds an operator listening to a receiver in the factory manager’s office.
A century later, everything (outside of modulation of electromagnetic waves) has changed. The radio now would fit in a pack of gum. The antenna is half a hand-span long or less, not two stories high. Data rates are bytes per millisecond, not 20 seconds per word.
Though it seems to go unrecorded, some time in modern memory, wireless technology was employed in a point (or, more accurately, point-to-point) solution for a sensor. Before long, point-to-point radios covered both simple sensors (1/0, on/off) as well as more complex sensors and instruments, the latter transmitting ranges or multiple data layers.
Today, there is a continuum of approaches to wireless installation. It is rapidly becoming the medium of choice over wired installations, particularly where remoteness, equipment motion or mobility—or the economics of running wires—make a radio a good solution.
On one end of this continuum, there is a 10-minute installation of a simple sensor, broadcasting its data, its own way and across a radio band all its own. On the other, there is a huge network of sensors and instruments neatly dovetailed into a complex network that has been hammered out over weeks of design.
Given this broad continuum, there is no one right way to set up and harvest useful data from radio waves transmitted from sensors or instruments. As in all of manufacturing, it all depends. This article explore some of these dependencies at three points on the continuum: (1) the simple one-radio, one-sensor installation; (2) a middle-level set-up in a distributed control scenario; and (3) a sophisticated setting where enterprise planning and enterprise information technology (IT)) is the backdrop.
Table I presents some of the key parameters for each of these three positions on our continuum.
In a simple set-up, a sensor is connected to a controller or programmable logic controller (PLC) with a radio transmitter instead of physical wiring. Anything the wires would have done is now handled by the radio.
A tad more complex is a set-up that involves multiple radio/sensors that incorporate mesh networking, but this, too, can be set up quickly. Here, each radio is capable of routing signals automatically. Because a mesh network is dedicated to delivering the message to the end point, it can handle interruptions, yet still deliver the sensor reading. It is self-healing in that it can route signals around glitched or down nodes along the network.
“There’s too much fear around wireless,” says Phil White, chief technical officer of IOSelect Inc., an instrumentation manufacturer based in San Diego. “You can try something simple, quickly and relatively inexpensively. [Up to a point,] you can use one form of wireless next to another form and they will both work happily for years. If they don’t work, you don’t need to feel locked in. You can always change things.”
White’s approach is, like his company’s offerings, eclectic. Among many net and connectivity devices, IOSelect markets equipment designed to carry signals back from remote mesh networks via Ethernet radio to central control areas, “sometimes 10 to 20 miles down the road,” White explains. “Digital, analog, serial, all are in our bailiwick,” he says, and the equipment is designed to interface directly with a broad range of computers, PLCs and distributed control systems (DCS). “Very few of our customers are installing entire infrastructures. They’re trying to gather data that’s miles away, or they’re trying to put several radios in a big metal room full of lots of mechanical equipment.”
At this relatively uncomplicated end of the wireless sensor spectrum, problems and solutions are again, relatively crisp and clear-cut. “In many situations, you can do a fast, ad hoc site survey with portable radio equipment,” White says. “If things get more complex, find someone with experience and equipment for more thorough surveys.”
Paul Brooks, business development manager, networks portfolio, for Rockwell Automation Inc., an automation supplier in Milwaukee, points out a basic consideration. “Whether your system is simple or complex, equipment decisions depend on data rates,” Brooks says. “A photocell is a simple sensor, but if it’s monitoring an airport baggage handling system, its single-digit transmissions might be continuous at millisecond rates. On the other hand, if it’s telling you the level in material storage, once an hour might be fine. The right radio for a silo is not likely to be the right radio for a baggage system—for example, the battery in a battery-powered unit would last at most, a few hours, at millisecond rates, but five or ten years when sending once an hour. The technology at the airport might have to transmit reliably through walls, while the silo unit might be a simpler line-of-sight solution.”
For specific applications of wireless instrumentation, check out Automation World’s coverage of six users of WirelessHart devices presented at an Emerson Process Management press conference last September at www.automationworld.com/news-4686.
“Once you move beyond a few radios,” White cautions, “simple and direct may not be an option. If you have one machine that cries out for a wireless sensor because it moves around too much for wires, or is remote, or would require expensive concrete cutting, you can connect it to a PLC wirelessly in minutes. But the situation is far different if you have a larger system with hundreds of sensors, or sites that are miles away. For these, you need much more thought and planning.”
Agreeing is Stephen Lambright, co-founder and vice president of marketing and customer services at wireless systems manufacturer Apprion Inc., of Moffett Field, Calif. “A single point solution is simple,” he says, “but if the fourth, fifth, sixth set of sensors are on differing technologies, somewhere down the road, managing them all is going to be a train wreck.”
The first area for consideration of medium-sized wireless applications is the radio technology itself. The size of the application will dictate a need for a standard approach. “Standards” are defined in this article to mean either conforming to published or emerging standards, such as WirelessHart, the Institute of Electrical and Electronics Engineers’ IEEE 802.15 and IEEE 802.11x (wireless Ethernet) or standardized in the sense that all devices are open enough to connect easily with all others in the system.
“An open infrastructure is definitely needed,” says Apprion’s Lambright. “You want something that can be integrated easily, deployed once, and continuously brought up to date. You don’t want to have to study a given radio’s frequency spectrum. You want plug-and-play.”
Ease of future technological change is important as well. Frank Williams, president and chief executive officer for Elpro Technologies, a wireless supplier based in Stafford, Queensland, Australia, with North American headquarters in San Diego, says, “No customers want to deploy wireless only to find that if they scale up, they have to lose their original investment.”
To prevent or minimize losses due to technological progress, wireless at the radio design level is increasingly modular and upgradable. “You don’t want to be left behind when technology changes, and it will,” Williams points out. “You can specify equipment that can be upgraded across the network, with no changes in security and no changes in configuration, but with new levels of evolved standards or new feature sets.”
There is a potential additional facet to the mid-level application—increased breadth and depth of the system. Additional layers of functionality are possible with multiple-sensor systems, and additional functionality opens new potential for deployment beyond point-monitoring needs, into support for quality, operations and beyond.
“One wireless sensor or instrument broadcasting to one PLC is all about data connectivity,” Lambright explains. “But, five, or a dozen, or a hundred or more can easily be carriers not only of data, but of a broad range of security, safety and human communications information.” Bringing this range under control requires a team approach, involving not just manufacturing engineering, but safety to tap into critical alerts, quality to harvest metrics and manufacturing management to monitor procedures throughout the plant.
For a Web exclusive on how wireless monitoring helps Total Petrochemical gauge boiler wall thickness, see www.automationworld.com/webonly-5013.
Lambright adds, “Your company can take advantage of the fact that wireless can be a solution for more than you might consider as an automation specialist. The right planning will bring people together from other departments, breaking down siloed thinking and developing common goals.”
Everyone interviewed for this story agreed that both radio technology and sensor/instrumentation are becoming richer in function. “You don’t have to look very far into the future,” says Williams. “It’s like the burgeoning of distributed control capabilities when fieldbus caught on—we’re seeing more and more smarts being driven out into the far ends of distributed wireless systems. Why should a device send back every data point, when there is growing capability at the instrument to do data logging, perform if/then decisions or otherwise exploit a smart sensor? In this scenario, the sensor-plus-radio is less a signal conditioner and more a smart device.”
“The more information, the more potential value to the users of the network,” Brooks says. “When you have what amounts to an aggregation of sensor inputs at the I/O (input/output) module itself, you can move enough information [to feed a variety of functional needs]. The broader the departmental participation, the better the business case for wireless.” Of course, the more functionality you extract from ever-smarter sensors and instruments, the more you move toward a high-end wireless application.
At the far end of the application spectrum, the perspective is no longer strictly automation-focused. The view broadens to include enterprise-wide viewpoints. It is a world that is rapidly moving to a scenario in which every sensor or instrument dovetails into high-level, networked system architectures.
It is an approach favored by big producers, who can appreciate the benefits of highly integrated control strategies in general: comprehensive monitoring of equipment efficiency, close tracking of processes, top-to-bottom management of production resources. It is a world in which everything talks with everything else, with preference given to easily installed devices that interconnect quickly.
Big systems have many components, and the management of quantities of distributed components benefits from consistent deployment of preferred equipment from preferred vendors in consistent ways. It helps if the equipment conforms to open standards.
Meanwhile, the open standards themselves are in flux, with observers patiently (or impatiently) following the in-process development of ISA100, which encompasses an aggregation of standards including Ethernet and WirelessHart—and many others opting for less ambitious, but published standards. The latter include WirelessHart, IEEE 802.11x WiFi, ZigBee, a smattering of other radio standards, and even a range of cell phone technologies.
Jeff Becker, director of global wireless for Phoenix-based automation supplier Honeywell Process Solutions, delineates some of these standards, “Ethernet is gaining dominance in processing and manufacturing, so expect wireless Ethernet to follow. Process instrumentation favors WirelessHart and ISA100. For global operations, you find satellite and WiMax and others exploiting Internet Protocol. If you architect for unified communications at the center of all this, you are in a position to gain a number of benefits, from quick response to machine downtime, to tight inventory management, to responsive supply line and distribution management.”
Becker is a champion of the proposed IEEE 802.11n wireless networking standard, which ups the data rate by a magnitude—from 54 megabits per second over today’s WiFi to 600 Mb/s on 802.11n. Ancillary technologies are included in the draft standard, including multiple input, multiple output (MIMO) transmission technology, using multiple antennas to resolve higher rates of data than possible with a single antenna, and highly specialized multiplexing—simultaneous transmission of multiple data chains.
Over and above the technology, when planning integrated systems, Becker says, “You want, above all, to think of more than just the immediate application. Stay alive to where wireless can be used, where it might be used. This allows you to evaluate options with growth in mind. The more you search out flexibility and upgradeability, the happier you will be in two years.”
Security and reliability are key as well. “It’s not possible to talk enough about security,” says Rockwell’s Brooks. “You can lock a switch or a control cabinet. You need to be able to lock radio transmissions as well, and that’s not just against bad people outside, but well-meaning personnel inside as well.”
Finally, continuously evaluate your resources, whether internal, consultant or supplier. A common theme is experience. Becker: “Now that wireless is hot, everyone is jumping in. Make sure your supplier has experience.” Elpro’s Williams expresses the same sentiment: “Wireless is on the way up, and a rising tide floats all boats. Make sure you know who you are connecting with, and make sure they have wireless deployment experience.”
People are the final consideration—and this applies whether the application is one radio to one sensor or thousands of wireless devices in a comprehensive, interoperable network. As Paul Brooks says, “We spend a lot of time talking about wireless technology, but at the end of the day, it has to be installed and maintained by people. The reality is that people in plants want to be production experts, not wireless network experts. The easier it is at the human level to integrate your systems, the better.”
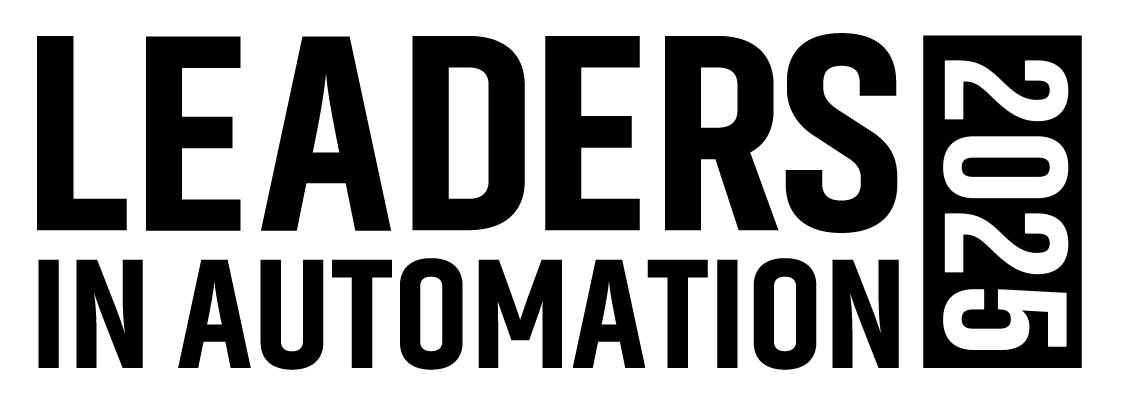
Leaders relevant to this article: