Sometimes people will say, “Asset management, that’s just a maintenance function,” as if that is a bad thing. Ensuring the production availability of all the equipment that has been procured and installed—often at the cost of millions of dollars—is an awesome task. And, it is the task of everyone—not only the maintenance department. Operations departments play an important role in finding problems before they escalate. Tying data into information technology systems can provide additional benefits. Everyone needs to play in this game.Bringing asset management up to global best-in-class status often requires a change in perspective and approach. The process needs a defined strategy to know where to go and how to get there. And how management and employees view metrics and personnel roles plays an important part, as well.Boston-based analyst firm Aberdeen Group Inc. researched companies in the process industry to glean some ideas about what sets best-in-class companies apart from run-of-the-mill outfits. The results are detailed in Aberdeen’s November 2008 report, “Operational Excellence in the Process Industries.”The research showed that best-in-class companies enable senior executives with real-time visibility into operational performance. According to Mehul Shah, Aberdeen research analyst, “The most successful companies in the process industries leverage automation and manufacturing software throughout the plant to optimize manufacturing operations, but they also integrate these systems to the business systems. This gives them the visibility needed to avoid adverse events within operations and improve overall efficiency.”The report recommends that companies establish cross-functional teams to standardize appropriate key performance indicators (KPIs) and provide role-based visibility, among other things.Beyond predicting
Achieving some of the recommendations put forward by Aberdeen requires changing perspective and incorporating new tools. George Buckbee, vice president of marketing and product development at ExperTune Inc., a process control software supplier in Hartland, Wis., says, “In the past, asset management tended to focus on expected service life, then on diagnosing failures, then on predicting and managing maintenance issues. In the current state of affairs, asset management tools like [Expertune’s] PlantTriage are also finding system bottlenecks and identifying ways to increase system capability,” says Buckbee.Success in asset management comes from having the right tools and the right practices in place, Buckbee points out. “Tools alone do not solve problems. And practices without tools are highly inefficient. Asset management tools, such as diagnostics, performance tracking and maintenance planning help in the automatic identification, prioritization, and resolution of asset performance issues.”Managers and engineers searching for the right tools and practices to improve asset management should look in a number of places for the appropriate technology. Moin Shaikh, fieldbus technologies marketing manager, at automation supplier Siemens Energy & Automation Inc., in Spring House, Pa., says, “Asset management means different things to different people. I’d start with ‘plant asset management’ or ‘collaborative process automation,’ in the terms of ARC Advisory Group. It includes field instrumentation, then plant floor and operations, then at the top is the enterprise level.”Plant asset management (PAM) is tied to the plant floor, says Shaikh—it’s the first system that comes into contact with equipment. It’s also quite different from enterprise resource planning (ERP) or computerized maintenance management systems (CMMS), he points out. “PAM is more focused on reducing unplanned downtime and improving maintenance functions,” Shaikh explains. “CMMS systems are also sometimes thought of as doing this, but they are more focused on managing the overall maintenance system. At the upper layer, systems talk to enterprise asset management to optimize plant throughput and look at KPIs related to production.”Shaikh takes the discussion a little deeper as he looks into the sources of information to feed the visibility and KPI applications required for good management practice. Stating that traditional asset management systems obtained information through the control systems, Shaikh adds, “We need a way to look not only at the process itself, but also at the health of the equipment. There are many intelligent devices, but there are also systems that are not so intelligent.”This is where fieldbus systems come to play, Shaikh says. “With fieldbus technologies, we have seen now that we not only open and close valves or monitor temperatures or control the speed of drives as through the control system, but we can also talk to the devices and gain a whole lot more information in a cost-effective way. We can look at doing more than controlling, but we can get this information from motors or valves or other field devices in a digital format.”Jeffrey Vasel, global marketing manager, 800xa asset management, integration, for automation vendor ABB Inc., in Wickliffe, Ohio, thinks managers should take a step back from the process in order to get another perspective. “Most people think smart instruments when they think asset optimization, but it goes well beyond that,” he states. “In fact, that may not be the best place to start. The best place to begin is with criticality analysis. Look at what has the most impact on environment, production and safety. Then start small, focus on a couple of projects, then expand, hopefully, to plant-wide strategy.”A well-executed asset optimization strategy can reduce unnecessary maintenance and downtime, track causes of failures, identify “repeat” offenders, provide root-cause data and fault diagnosis, and recommend actions. It also detects failure conditions in advance, eliminates manual actions, handoffs and paperwork, and reduces latent time between problem identification and resolution. The results of this approach are exemplified at ABB customer Vale Inco, a Toronto-based mining company. “It makes all the difference in the world. I’ve never seen such a big motivator of people,” says Sheldon Osmond, mechanical maintenance engineer at Vale Inco.Really remoteVale Inco Nickel Mining’s Voisey’s Bay location in Labrador, Canada is only accessible by plane or boat. In 2005, operations came onstream ahead of schedule. With the help of ABB Full Service, Vale Inco was able to achieve commercial nickel production significantly ahead of schedule and attain an all-time-high production level.ABB Full Service is a performance-based maintenance partnership that drives operational excellence. It assumes complete responsibility for maintenance and focuses on improving productivity in a performance-based manner. ABB shares risk by contractually committing to KPIs, such as increased overall equipment effectiveness (OEE) and reduced total maintenance costs, and by assuming full responsibility for maintenance. Iskueteu-ABB, the joint venture between Iskueteu, an aboriginal limited partnership, and ABB, was contracted to provide the maintenance services to Vale Inco (then Voisey’s Bay Nickel Mining Co.).The geography of Labrador is such that there can be a wait of many days to receive spare parts while the weather clears. So accurate information accessed by all the appropriate people is a must. In one instance, an experienced mechanical supervisor felt that tailing pumps should be rebuilt after 1,200 hours. It takes two workers 12 hours each to rebuild each pump. If they are not rebuilt in time, “nonwearable” areas begin to wear and the pump then must be replaced. While it’s being replaced, processes move to a redundant, back-up pump. So there is no spare while the rebuild is going on. The decision is critical.The supervisor’s experienced guess was that a specific pump had seven to 10 days left. But by employing ABB’s Asset Optimization (AO) solution, asset monitors were implemented and real-time and historical production data gathered, including vibration monitoring for “out-of-tolerance” readings, run time and thermal image data. According to AO, there were only 72 hours left, or three days. The process was moved to the redundant pump and the maintenance crew began to rebuild the worn pump. Thanks to visibility of actionable data, there was no guessing and no unplanned downtime. There was also no unnecessary replacement earlier than needed. AO enabled a cost-effective predictive maintenance strategy to replace a costly, guess-work-based, preventive maintenance plan.People perspectiveAnother change in perspective that brings a plant closer to best-in-class involves the role of people. Here, technology can be “the best friend to the blue-collar worker,” according to Charlie Mohrmann, vice president of sales for Wonderware Mobile Solutions, Houston. “Enforce process workforce procedures, change behavior,” he declares.Use of a mobile computing platform, such as Wonderware’s IntelaTrac, gives operators and, in fact, everyone in the plant, the opportunity to record things they notice as they walk through the plant. Because upwards of 40 percent to 60 percent of plant assets are not instrumented, this workforce role adds many “intelligent sensors” to the system. Sometimes, the instrumented system only catches big equipment problems, while most downtime is caused by more mundane issues such as insufficient oil levels. Mohrmann cites internal studies that indicate that companies who install these mobile solutions can typically see a 35 percent reduction in maintenance costs.ExperTune’s Buckbee also sees a need to put information into the hands of those who need it. “As companies have downsized, and competition has increased, skilled personnel are being stretched more and more each year. With such limited resources, it is more important than ever that every person stays focused on the most important tasks only, and is able to complete their work efficiently,” Buckbee says. With Expertune’s Control System Asset Management product in place, automated diagnostics and performance KPIs are automatically prioritized, he relates. Further, as asset management tools are integrated more directly, plant personnel can move quickly and efficiently into troubleshooting and issue resolution. Often, issues are identified, prioritized and reported directly to the user, with drill-down, analysis and issue resolution available directly from the user’s computer desktop, according to Buckbee.One example of leveraging people is the use of Expertune’s Active Model Capture Technology. Using this technology, dynamic process models are captured automatically, based on regular control changes by operators. Using Active Model Capture, some users have reported a five-fold increase in their ability to optimize controller tuning and process dynamic studies, Buckbee says.Change metrics perspective
Peter Martin, vice president at automation products and services provider Invensys Process Systems, Foxboro, Mass., sees a simplification of the meaning of asset management into just equipment maintenance. But, he says, “To business managers responsible for process manufacturing operations, asset management implies the effective deployment of all assets within their operational domain to meet business objectives.”Martin also sees that both operations teams and maintenance teams provide the most impact on the efficient operation of industrial plants and the resulting economic value generated, while engineering departments apply technology to support the effectiveness of operations, maintenance and other plant organizations. “The traditional primary measure of the maintenance organization is asset availability,” states Martin. “The traditional primary measure of operations is asset utilization.”The most effective way to manage assets from a business perspective is to manage both asset utilization and asset availability together in a holistic manner to drive business value, according to Martin. “This has not historically been the case,” he says. “In most manufacturing operations, operations management drives improved asset utilization and maintenance management drives improved availability, and the two have typically approached each independently.”For asset utilization improvements, engineering has applied technologies such as advanced control, multivariable control, recipe management and process optimization, Martin observes. For asset availability improvements, engineering has applied strategies such as preventive maintenance, predictive maintenance and reliability-centered maintenance. Most of the maintenance strategies are still at the individual equipment level and many are merely focused on instruments and valves, Martin continues.This approach, according to Martin, has severely limited the value generated from industrial asset sets. “These technologies and strategies have been applied independently of each other, and it has not been clear as to whether improved business value is the result.”Martin believes that asset performance management is the balancing of asset availability and asset utilization. And, because they are inverse functions, maximizing them independently will seldom result in maximum business value. “To make these decisions optimally requires an effective business measurement system that can provide business value insight into the desired operational balance between effective availability and effective utilization,” says Martin.Invensys has a patented approach to real-time business measurement that does exactly this—dynamic performance measures (DPMs). DPMs measure the business value of base assets, asset sets or groups of asset sets as a real-time vector that represents the true value that they generate. The real-time business performance data that results from the use of DPMs enables a much more effective approach to true asset management than do traditional methods, Martin says. Rather than merely managing the availability of some instrumentation, plant personnel can drive business performance from asset sets, up to and including the entire plant, he asserts.Changing asset optimization perspective from equipment level to strategic, changing people perspective from a focus on budget line items to a broader, connected and committed workforce point of view, and changing metrics perspective from sometimes conflicting differences between operations and maintenance to a holistic business approach… These are all steps that will push a company far along the path to best-in-class.For an example of how Shanghai Petrochemical improved its asset management strategy using Lifecycle Management methodology from Honeywell Process Solutions, visit www.automationworld.com/feature-5014
Achieving some of the recommendations put forward by Aberdeen requires changing perspective and incorporating new tools. George Buckbee, vice president of marketing and product development at ExperTune Inc., a process control software supplier in Hartland, Wis., says, “In the past, asset management tended to focus on expected service life, then on diagnosing failures, then on predicting and managing maintenance issues. In the current state of affairs, asset management tools like [Expertune’s] PlantTriage are also finding system bottlenecks and identifying ways to increase system capability,” says Buckbee.Success in asset management comes from having the right tools and the right practices in place, Buckbee points out. “Tools alone do not solve problems. And practices without tools are highly inefficient. Asset management tools, such as diagnostics, performance tracking and maintenance planning help in the automatic identification, prioritization, and resolution of asset performance issues.”Managers and engineers searching for the right tools and practices to improve asset management should look in a number of places for the appropriate technology. Moin Shaikh, fieldbus technologies marketing manager, at automation supplier Siemens Energy & Automation Inc., in Spring House, Pa., says, “Asset management means different things to different people. I’d start with ‘plant asset management’ or ‘collaborative process automation,’ in the terms of ARC Advisory Group. It includes field instrumentation, then plant floor and operations, then at the top is the enterprise level.”Plant asset management (PAM) is tied to the plant floor, says Shaikh—it’s the first system that comes into contact with equipment. It’s also quite different from enterprise resource planning (ERP) or computerized maintenance management systems (CMMS), he points out. “PAM is more focused on reducing unplanned downtime and improving maintenance functions,” Shaikh explains. “CMMS systems are also sometimes thought of as doing this, but they are more focused on managing the overall maintenance system. At the upper layer, systems talk to enterprise asset management to optimize plant throughput and look at KPIs related to production.”Shaikh takes the discussion a little deeper as he looks into the sources of information to feed the visibility and KPI applications required for good management practice. Stating that traditional asset management systems obtained information through the control systems, Shaikh adds, “We need a way to look not only at the process itself, but also at the health of the equipment. There are many intelligent devices, but there are also systems that are not so intelligent.”This is where fieldbus systems come to play, Shaikh says. “With fieldbus technologies, we have seen now that we not only open and close valves or monitor temperatures or control the speed of drives as through the control system, but we can also talk to the devices and gain a whole lot more information in a cost-effective way. We can look at doing more than controlling, but we can get this information from motors or valves or other field devices in a digital format.”Jeffrey Vasel, global marketing manager, 800xa asset management, integration, for automation vendor ABB Inc., in Wickliffe, Ohio, thinks managers should take a step back from the process in order to get another perspective. “Most people think smart instruments when they think asset optimization, but it goes well beyond that,” he states. “In fact, that may not be the best place to start. The best place to begin is with criticality analysis. Look at what has the most impact on environment, production and safety. Then start small, focus on a couple of projects, then expand, hopefully, to plant-wide strategy.”A well-executed asset optimization strategy can reduce unnecessary maintenance and downtime, track causes of failures, identify “repeat” offenders, provide root-cause data and fault diagnosis, and recommend actions. It also detects failure conditions in advance, eliminates manual actions, handoffs and paperwork, and reduces latent time between problem identification and resolution. The results of this approach are exemplified at ABB customer Vale Inco, a Toronto-based mining company. “It makes all the difference in the world. I’ve never seen such a big motivator of people,” says Sheldon Osmond, mechanical maintenance engineer at Vale Inco.Really remoteVale Inco Nickel Mining’s Voisey’s Bay location in Labrador, Canada is only accessible by plane or boat. In 2005, operations came onstream ahead of schedule. With the help of ABB Full Service, Vale Inco was able to achieve commercial nickel production significantly ahead of schedule and attain an all-time-high production level.ABB Full Service is a performance-based maintenance partnership that drives operational excellence. It assumes complete responsibility for maintenance and focuses on improving productivity in a performance-based manner. ABB shares risk by contractually committing to KPIs, such as increased overall equipment effectiveness (OEE) and reduced total maintenance costs, and by assuming full responsibility for maintenance. Iskueteu-ABB, the joint venture between Iskueteu, an aboriginal limited partnership, and ABB, was contracted to provide the maintenance services to Vale Inco (then Voisey’s Bay Nickel Mining Co.).The geography of Labrador is such that there can be a wait of many days to receive spare parts while the weather clears. So accurate information accessed by all the appropriate people is a must. In one instance, an experienced mechanical supervisor felt that tailing pumps should be rebuilt after 1,200 hours. It takes two workers 12 hours each to rebuild each pump. If they are not rebuilt in time, “nonwearable” areas begin to wear and the pump then must be replaced. While it’s being replaced, processes move to a redundant, back-up pump. So there is no spare while the rebuild is going on. The decision is critical.The supervisor’s experienced guess was that a specific pump had seven to 10 days left. But by employing ABB’s Asset Optimization (AO) solution, asset monitors were implemented and real-time and historical production data gathered, including vibration monitoring for “out-of-tolerance” readings, run time and thermal image data. According to AO, there were only 72 hours left, or three days. The process was moved to the redundant pump and the maintenance crew began to rebuild the worn pump. Thanks to visibility of actionable data, there was no guessing and no unplanned downtime. There was also no unnecessary replacement earlier than needed. AO enabled a cost-effective predictive maintenance strategy to replace a costly, guess-work-based, preventive maintenance plan.People perspectiveAnother change in perspective that brings a plant closer to best-in-class involves the role of people. Here, technology can be “the best friend to the blue-collar worker,” according to Charlie Mohrmann, vice president of sales for Wonderware Mobile Solutions, Houston. “Enforce process workforce procedures, change behavior,” he declares.Use of a mobile computing platform, such as Wonderware’s IntelaTrac, gives operators and, in fact, everyone in the plant, the opportunity to record things they notice as they walk through the plant. Because upwards of 40 percent to 60 percent of plant assets are not instrumented, this workforce role adds many “intelligent sensors” to the system. Sometimes, the instrumented system only catches big equipment problems, while most downtime is caused by more mundane issues such as insufficient oil levels. Mohrmann cites internal studies that indicate that companies who install these mobile solutions can typically see a 35 percent reduction in maintenance costs.ExperTune’s Buckbee also sees a need to put information into the hands of those who need it. “As companies have downsized, and competition has increased, skilled personnel are being stretched more and more each year. With such limited resources, it is more important than ever that every person stays focused on the most important tasks only, and is able to complete their work efficiently,” Buckbee says. With Expertune’s Control System Asset Management product in place, automated diagnostics and performance KPIs are automatically prioritized, he relates. Further, as asset management tools are integrated more directly, plant personnel can move quickly and efficiently into troubleshooting and issue resolution. Often, issues are identified, prioritized and reported directly to the user, with drill-down, analysis and issue resolution available directly from the user’s computer desktop, according to Buckbee.One example of leveraging people is the use of Expertune’s Active Model Capture Technology. Using this technology, dynamic process models are captured automatically, based on regular control changes by operators. Using Active Model Capture, some users have reported a five-fold increase in their ability to optimize controller tuning and process dynamic studies, Buckbee says.Change metrics perspective
Peter Martin, vice president at automation products and services provider Invensys Process Systems, Foxboro, Mass., sees a simplification of the meaning of asset management into just equipment maintenance. But, he says, “To business managers responsible for process manufacturing operations, asset management implies the effective deployment of all assets within their operational domain to meet business objectives.”Martin also sees that both operations teams and maintenance teams provide the most impact on the efficient operation of industrial plants and the resulting economic value generated, while engineering departments apply technology to support the effectiveness of operations, maintenance and other plant organizations. “The traditional primary measure of the maintenance organization is asset availability,” states Martin. “The traditional primary measure of operations is asset utilization.”The most effective way to manage assets from a business perspective is to manage both asset utilization and asset availability together in a holistic manner to drive business value, according to Martin. “This has not historically been the case,” he says. “In most manufacturing operations, operations management drives improved asset utilization and maintenance management drives improved availability, and the two have typically approached each independently.”For asset utilization improvements, engineering has applied technologies such as advanced control, multivariable control, recipe management and process optimization, Martin observes. For asset availability improvements, engineering has applied strategies such as preventive maintenance, predictive maintenance and reliability-centered maintenance. Most of the maintenance strategies are still at the individual equipment level and many are merely focused on instruments and valves, Martin continues.This approach, according to Martin, has severely limited the value generated from industrial asset sets. “These technologies and strategies have been applied independently of each other, and it has not been clear as to whether improved business value is the result.”Martin believes that asset performance management is the balancing of asset availability and asset utilization. And, because they are inverse functions, maximizing them independently will seldom result in maximum business value. “To make these decisions optimally requires an effective business measurement system that can provide business value insight into the desired operational balance between effective availability and effective utilization,” says Martin.Invensys has a patented approach to real-time business measurement that does exactly this—dynamic performance measures (DPMs). DPMs measure the business value of base assets, asset sets or groups of asset sets as a real-time vector that represents the true value that they generate. The real-time business performance data that results from the use of DPMs enables a much more effective approach to true asset management than do traditional methods, Martin says. Rather than merely managing the availability of some instrumentation, plant personnel can drive business performance from asset sets, up to and including the entire plant, he asserts.Changing asset optimization perspective from equipment level to strategic, changing people perspective from a focus on budget line items to a broader, connected and committed workforce point of view, and changing metrics perspective from sometimes conflicting differences between operations and maintenance to a holistic business approach… These are all steps that will push a company far along the path to best-in-class.For an example of how Shanghai Petrochemical improved its asset management strategy using Lifecycle Management methodology from Honeywell Process Solutions, visit www.automationworld.com/feature-5014
Sponsored Recommendations
Sponsored Recommendations
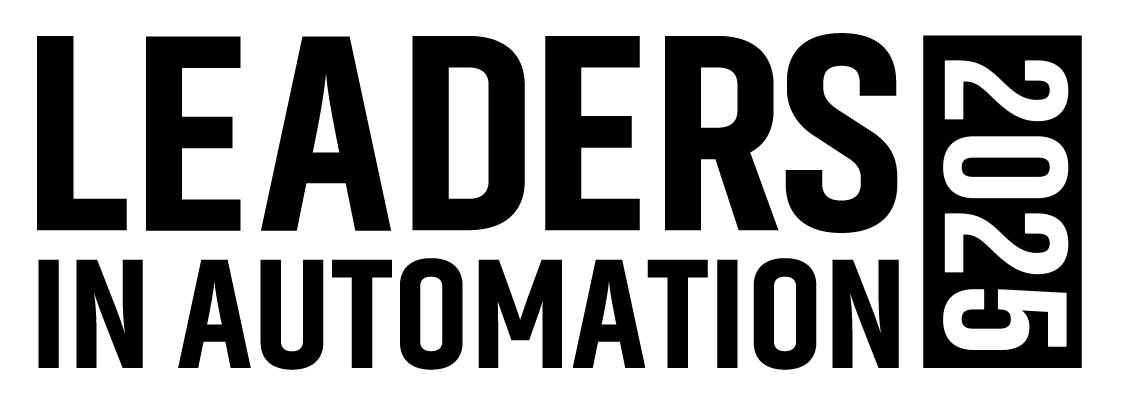
Leaders relevant to this article: