Trapped! Stranded! Held hostage! All are terms that have been used to
describe data that likely exists in many places in your plant or
factory today—data that, if made accessible on a continuous, real-time
or near-real-time basis, could potentially help you save money in a
variety of ways. Now, the emergence of new industrial wireless
networking technologies promises some cost-effective ways to free that
locked-up data.One case in point comes with last year’s release of the WirelessHart standard for use in process measurement and control applications. The first WirelessHart-compliant products are expected this fall. And while the focus of attention may be on new sensors and instruments with built-in WirelessHart capabilities, another major opportunity will involve retrofits of existing field devices using so-called WirelessHart adapters.These gizmos will attach to any installed Hart instrument to enable access to the diagnostic data that is available on a separate digital channel in every Hart device, in addition to the 4-20 milliamp (mA) analog Hart signal. Most legacy distributed control systems (DCS) are not equipped to understand this digital data, depriving their users of a source of valuable information for improving plant operation and maintenance. WirelessHart adapters will be designed to pick up this “stranded” data and transmit it wirelessly to the user.This data, if used correctly, could deliver potentially huge benefits to manufacturers, proponents say. “According to some experts, if an industrial plant used Hart data to change only 25 percent of its preventive maintenance to predictive maintenance, it could realize up to a staggering 60 percent reduction in maintenance expenses alone,” says a white paper published by Airsprite Technologies Inc., a Marlborough, Mass., wireless technology provider. For more on WirelessHart adapters see “A New Way to Get Hart Data,”.A different kind of “stranded” data is also present today in the hundreds of millions of analog dial gauges that pepper plants and factories throughout the industrialized world. These legacy gauges typically aren’t wired into any network, but give up their information only when a human physically walks up and reads them. Many manufacturers today expend significant labor hours in sending workers around with clipboards or hand-held devices to take regular readings of these gauges. Methods for automating these readings have been available, but until now, have been costly and invasive, often requiring a production shutdown for installation.But now, there’s a new player in the market that is touting a relatively low cost and noninvasive wireless technology for attacking this problem. Cypress Systems Corp., a San Jose, Calif., spinoff of integrated circuit (IC) supplier Cypress Semiconductor Corp., has come up with a device called a Wireless Gauge Reader that simply clips over the front face of an existing gauge.Equipped with a tiny, chip-based camera and associated electronics, the Wireless Gauge Reader is designed to read the analog gauge, convert it to a digital readout, and also transmit the reading wirelessly to a central server, using a proprietary, 2.4 gigahertz (GHz) mesh network. The battery-powered Wireless Gauge Readers can be installed in minutes without breaking pressure seals, performing leak checks, running wires or interrupting the underlying process, according to Cypress Systems—all at a cost of less than half that of alternative systems.“It’s like an electronic eyeball. Just like a human eye would read the needle and gauge, the Wireless Gauge Reader looks at the gauge, interprets it and converts the reading to a wireless transmission, so then you can integrate the data with your existing systems, whether that’s a DCS, or whether it’s a cell phone notification or just a Web browser,” says Harry Sim, Cypress Systems chief executive officer. The wireless range for the device is more than 300 meters, Sim says, and battery life is two to three years under typical sampling rates.Sim, former vice president of marketing at Phoenix-based automation vendor Honeywell Process Solutions, left that post in September 2006 to become the first CEO of Cypress Systems, and takes credit for the Wireless Gauge Reader concept. The first Wireless Gauge Reader was installed at a customer site in October 2006, Sim says. Cypress Systems has so far installed about 1,000 of the devices at about 20 customer sites.A follow-on product, a Wireless Transducer Reader, does not use the optical camera technology, but instead connects to standard 4-20 mA, 0-5 volt, or 0-10 volt outputs to read and wirelessly report data from other kinds of “stranded” devices. That product was introduced in the first quarter of 2007. During his time at Honeywell, Sim notes, “the focus was on things that were very much mission critical. They were real time. They were closed loop. They had to work every millisecond, or the plant would have a really big defect, or blow up, or something like that.” But at Cypress Systems, he says, the focus instead is on closing the technology gap for a variety of applications that are non-mission critical, in which there is often a “man in the loop” to gather data. For these applications, users could often potentially benefit by having “near-real-time data” delivered wirelessly, Sim says. The sampling rates on the Wireless Gauge Reader, for example, are often set anywhere from 15 minutes to a few hours, according to need. But until now, it’s typically been too costly or too much of a hassle to set up systems for automating the collection of this data, Sim explains.One early user of the Cypress Systems products is Micrel Inc., a semiconductor manufacturer that operates a 150-millimeter wafer fabrication plant at its San Jose, Calif., headquarters. With a capacity of 30,000 wafer starts per month, Micrel’s plant is more than 20 years old, containing a mix of old and new equipment, and operates without full benefit of current automation technology. Critical to the plant’s production are various combinations of process gases needed to produce the desired semiconductor chips.These process gases are supplied from about 300 different gas cylinders equipped with pressure gauges that the company has traditionally monitored manually twice per day. “That’s very expensive for me. I have a guy who I’m paying a pretty good salary to wander around with a clipboard and take readings and write them down,” says Ron Farry, equipment engineering manager for the Micrel plant’s maintenance organization.Farry has previously looked for ways to automate the process; the traditional approach would involve replacing the gauges with networked, transducer-based gas panels. But to do that, Farry says “we’d have to run wires all over the place, and the costs of that would kill us.” Besides, he adds, “I don’t want to break into the gas lines [to install transducers,], because then I’d be creating leak points and a whole other set of problems.” Indeed, with the transducer-based solution, the affected production line would have to be shut down, likely for days, to reconfigure the gas piping and retest for leaks.In all, counting the cost of equipment, installation and rework labor, and the associated production downtime, Farry figures the cost of a traditional wired transducer system to automate the gauge reading would run about $4,000 per gas cylinder gauge. Given that kind of a price tag, Micrel decided to make do with its manual gauge reading approach.So when Farry in 2007 heard about “a new confangled widget” that Cypress Systems was promoting for automated wireless gauge reading, he was skeptical, but willing to learn more. Cypress Systems brought a demonstration unit of its Wireless Gauge Reader to the Micrel plant. And Farry was quickly convinced. “Within 10 minutes of looking at it and messing around with it, I could see that it was something that could help us immensely,” he recalls.So Farry issued a challenge to Cypress Systems. “I told them, ‘I want you to give me five of these units, and I’m going pick the places to monitor. We’ll try them for 90 days and see how they perform, and in the event that they do everything that you advertise, we’ll move forward.’ ”For the test set, Farry picked gauges of different sizes and shapes, with different numbering scales, and some with partially fogged lenses. Cypress Systems installed the units, which transmitted their readings wirelessly to the vendor’s Blue Box receiver/server. The Blue Box was hooked up to the personal computer (PC) in Farry’s office, where he could monitor the results using a Web browser. The result: the Wireless Gauge Readers did indeed work as advertised, successfully reading the variety of gauge types, and Farry gave the go-ahead to move forward.By this spring, Cypress Systems had installed a total of about 150 Wireless Gauge Readers and Wireless Transducer Readers in the Micrel fab plant. Of the 150, about 100 of the devices are installed on gas cylinder gauges, says Farry, while Micrel’s facilities staff is using about 50 of the units to monitor water pressures, temperatures, air flows and other parameters.Compared to the estimated $4,000-per-point cost of a wired transducer-based system, the Wireless Gauge Readers were installed at a cost of about $1,250 per point, with no production disruptions, says Farry. Each unit required about 10 to 30 minutes to install. “As part of the [Cypress Systems] service, we order it, they install it, and it’s a ‘we-don’t-even-know-they’re-here’ kind of activity,” as Farry puts it.The benefits of the system have been several. “For one thing, I was immediately able to free up labor,” Farry notes. Over the fab’s two-shift operation, Micrel has been able to reduce the time devoted to making gauge reading rounds by one full-time equivalent technician—time that can be redeployed to other tasks.Additional savings have come because Micrel can now safely use more gas out of each cylinder before changing it out. In the past, in order to take no chance on running out of a critical process gas, a technician making rounds would sometimes replace a cylinder that was still a quarter or even a third full. Now, software provided with the Wireless Gauge Reader system sends alerts to a technician’s cell phone, pager or e-mail address when a cylinder’s gas level reaches a pre-set limit and the cylinder needs to be changed. “This way, we might be able to pick up anywhere from 15 percent to 20 percent more gas out of a cylinder,” Farry observes.A third benefit relates to the historical data tracking enabled by the Wireless Gauge Reader server, which can store up to three years of data under normal sampling rates. By examining the pressure history on the 100 cylinders equipped with the Wireless Gauge Readers, Farry says he was able to correlate the source of “some weird process issues” that the plant was having. The culprit turned out to be gas condensation and loss of gas pressure caused by cold weather conditions. The company now can take steps to avoid this issue by using thermal wraps on some cylinders in the future, he notes. But its something “we never would have seen” without access to the historical data provided by the Wireless Gauge Reader system, Farry observes.Altogether, Farry estimates that the combined operational savings from the 100 Wireless Gauge Readers installed on the gas cylinder gauges will amount to about $215,000 per year. At a cost of $1,250 per point, that’s a total installation cost of about $125,000, putting the return on investment (ROI) at only seven months.With that kind of payback so far, Farry says he plans to install additional Wireless Gauge Readers for use in a variety of cost saving initiatives at the fab. “If I’m able to spend the way that I want to,” he says, “we’ll probably have another 150 to 200 of them installed by the end of the second quarter next year.”At Cypress Systems, Sim notes that the Wireless Gauge Reader product integrates various proven solutions developed by its parent, ranging from the 2.4 GHz wireless radio technology used in wireless keyboards and mice to its PSoC programmable system-on-a-chip to interpret and process the signals.The company has several patents pending on various Wireless Gauge Reader technologies, Sim says. These include “the whole concept of optically reading gauges noninvasively,” and related concepts covering lighting methods, mounting techniques and algorithms for reading about 3,000 different variations of industrial gauges. Sim contends that the company rarely encounters an indoor gauge that the device cannot read. But he does concede that perhaps a third of outdoor-mounted gauges that have long been exposed to the elements do sometimes present problems, and may have to modified or replaced.Industry observers such as Wil Chin, a research director covering process measurement devices at ARC Advisory Group Inc., in Dedham, Mass., see a vast potential for the Wireless Gauge Reader and products like it. “Conservatively speaking, we believe that there are more than 56 million field devices installed in the process automation area,” says Chin. “But if you look at the number of gauges, it’s probably anywhere from five to ten times that figure. So you’re talking about a huge number.”Further, beyond just manual dial gauges, an even larger potential exists for products designed to extract and wirelessly transmit data from any of a wide range of existing industrial devices that aren’t electronically enabled or tied into networks today, many agree. “If somebody can just bolt something on, instead of literally replacing the entire device, that’s going to be a real attractive item for processors and manufacturers,” observes Cliff Whitehead, co-chair of the Factory Automation Study Group for the Instrumentation, Systems and Automation Society’s ISA100 wireless standards committee.Sim couldn’t agree more. Beyond the Wireless Gauge and Transducer Reader products, Cypress Systems is gearing up to roll out a string of additional products that are designed to rescue trapped data wirelessly from various other kinds of industrial and commercial legacy devices, he says.In late September, the company planned to introduce a Wireless Pneumatic Thermostat—aimed at the commercial building market—as well as a Wireless Steam Trap Monitor (WSTM) for the industrial arena. The WSTM will mount noninvasively on existing steam traps and will use temperature sensing and built-in intelligence to detect and wirelessly alert users of stream trap failures and leaks. An estimated 15 percent to 20 percent of all steam traps are malfunctioning at a given time, says Sim, and each leaking trap wastes $5,000 or more in energy costs per year.“We see a large number of points out there that are in this non-mission critical, near-real time, man-in-the-loop kind of space,” says Sim. “We think it’s in the hundreds of millions of devices. This is not a sexy space, but it’s huge,” he adds, and it is a market to date that has been “completely underserved.”
Companies in this Article
Companies in this Article
Sponsored Recommendations
Sponsored Recommendations
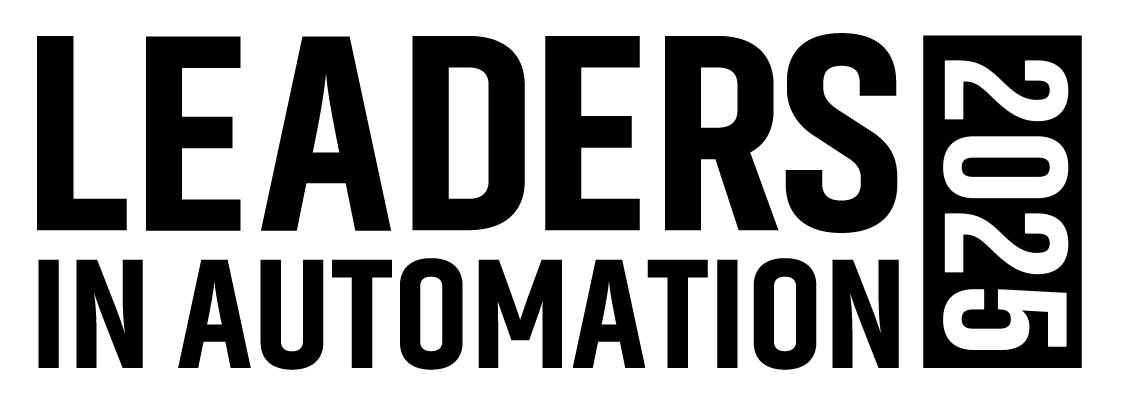
Leaders relevant to this article: