Track-and-trace applications have grown principally through the impetus of government regulations. Companies in industries ranging from pharmaceutical to food production must keep track of products, including the genealogies of lots of production and distribution. These companies needed the ability to react quickly to recall products when a problem is reported. A thorough track-and-trace system assures maximum recall of affected products, while also limiting the recall to just those products, greatly reducing the cost of a recall.A track-and-trace system includes a data input system, software that includes a historian and analysis tools, and visualization and reporting. Data input ranges from manual to such automatic tools as bar code and radio frequency identification (RFID). While none of these systems is new, manufacturing professionals have discovered an important by-product of collecting all this data—information about the detailed working of the manufacturing process.This application is so general that it fits many different industries. The already mentioned pharmaceutical and food-and-beverage industries must have some sort of application in order to comply with regulations of various governmental agencies. Companies that are part of the supply chains of companies in these industries may also need to implement the applications in case of a quality problem with their customers. Beyond that, companies in entirely different industries have found value in applications that could be considered track and trace simply because of the real-time information and data mining opportunities afforded by the systems.Marc Leroux, manager of collaborative production management at automation supplier ABB, in Norwalk, Conn., says, “The regulatory reason for companies getting into track and trace is still there, but more and more industries are getting involved. Rarely does one industry stand on its own. Chemical companies feeding into regulated industries, for example, or paper companies providing food wrappers may also need to maintain traceable records. When people discuss track and trace, the first thing they think of is the 21 CFR Part 11 regulation of the U.S. Food and Drug Administration (FDA). This is probably the most stringent set of requirements, but there are others such as the TREAD Act (for Transportation Recall Enhancement, Accountability, and Documentation) and the European Food Act. You have to be able to track from any point backward and forward.”It's in there
Product developers at ABB figured that this application was so ingrained in all parts of manufacturing that they built track-and-trace functionality into the company’s flagship 800xA control platform. But the basic question is probably not whether to do track and trace, but rather what are you going to do with it.“One big advantage of this application, of course, springs from the regulatory issue,” says Leroux. “This is a critical business risk. If you can’t find your product or don’t know where your components came from, you could have to shut down your business.” Leroux notes that companies now are starting to take advantage of the 800xA track-and-trace capability to provide better and more efficient customer service. Customers are not as loyal to a brand as in the past, so companies are looking to maximize investment returns and find cheaper materials,he says. Because people are not paying more for a brand but paying for customer service, applications that improve this function provide a competitive advantage. Leroux provides an example of a company in the paper industry that began using its track-and-trace application to evaluate customer complaints. “Previously, complaints took up to a week to resolve going through four or five departments with many manual records,” he says. “Now they can move the complaint automatically through the computer system with one person. The result was a reduction in the system from multiple people tied up for a week to one person tied up for a couple of hours.”The paper company application could be somewhat complex. The process is that chemicals and pulp enter the system. They go through a machine that outputs a huge roll of paper. This roll is then cut down to 60 rolls. Each roll then feeds a “sheeter” that cuts the paper into familiar sheets. Sheets are assembled into reams; the reams fill a box; and the boxes are placed on pallets for shipment.The problem entailed tracking a customer complaint from one box or even one ream of paper back to the roll. As someone went through the system, he or she would look for other customers who received products from that roll who might have similar problems. A quick call would uncover that either this was an isolated instance or that there was a bigger problem. If it were a bigger problem, engineers could use the same data to help find the root cause and fix the problem. Customers were impressed that the company didn’t wait for a complaint and then delay and answer, but that the company had a solution sometimes even before the customer knew it had a problem.Switching from the pulp-and-paper industry to food production, Mike Hader, director of information technologies at Odom’s Tennessee Pride Sausage Inc., in Madison, Tenn., acknowledges that his track-and-trace application began in response to U.S. Department of Agriculture and, to some degree, FDA regulations. Tennessee Pride uses a software application that is now owned by Infor Global Solutions, a supplier of enterprise software based in Alpharetta, Ga.Says Hader, “We implemented lot tracking at the end of 1999. Lot management is absolutely crucial to Tennessee Pride. This is partly due to government regulations, but also because it’s part of our warehouse inventory rotation. Everything we produce has a short life span. It’s crucial that we ship the oldest lot first. This is made even more complex by dating the products. Different customers have different dating requirements that must be tracked. So, we can’t just manage by SKUs (stock keeping units), but we must also track lot number.”If there would be a problem that drew questions from the FDA, Tennessee Pride would have to trace forward and backward from the problem. Anything that touches the food, including packaging, must be identified. “Admirably,” says Hader, “Infor’s ERP (enterprise resource planning) does a good job of this. The inventory dashboard we use can drill into a product, and managers can see how many are in each of different age buckets and then drill in further to see how many are in the warehouse.”Fresh sausage
Benefits of a track-and-trace application at Tennessee Pride begin with compliance to government regulations. From a finance point of view, though, it allows the company to manage inventory to get sufficient inventory turns. Getting suppliers to use bar codes allows the system to expand into the supply chain. Since it uses third-party warehousing, the application enables significant automation of the entire inventory-to-shipment system.The consumer packaged goods (CPG) industry faces its own challenges, but one that it doesn’t face is stringent government regulation. Charlie Rastle, CPG industry manger for Rockwell Automation Inc., the Milwaukee automation supplier, says that industry adoption of track and trace is more in relation to product recall possibilities. “Originally, companies found that existing paper-based systems met the few needs that they had. But these companies are now looking for ways to improve overall business. So they track inventory in plants to achieve better control of the supply chain. “According to Rastle, the classic situation is when an order comes in through the ERP system. Assurance that there are sufficient materials to make the product comes through a track-and-trace application. It offers an automated way to coordinate inventory and production orders to enable a company to achieve close to “just-in-time” management.A second useful benefit comes from linking manufacturing to sustainability. “If I can track better, I can identify where my waste streams are,“ says Rastle. “I can also see how big these are and then go about finding and correcting them.” He notes that Rockwell is also starting to see track-and-trace applications used for activity-based costing. “If you trace right, you can do it. In the CPG industry, you have so many products, you need to know how much each costs. In each step, you have waste. As you have more visibility, you can know more about your process and go out and make improvements. We’ve also seen linking Lean Manufacturing to Six Sigma,” Rastle adds. “Lean teaches to go out and analyze processes. Companies then use Six Sigma methodology to fix.”Sometimes, track-and-trace applications are seen by management as investments comparable to insurance policies. Maybe it’s something you know you need, but you don’t see the value until you have a claim—something you don’t really want. Similarly with track and trace, if that application was procured just for assurance of prompt response to a necessary recall and you never have a recall, then what was the value?Claus Abildgren, marketing manager, production management, for software supplier Wonderware, a division of Invensys located in Lake Forest, Calif., sees companies having a hard time justifying an upfront return on investment for a track-and-trace application. “Think about energy savings,” he notes. “You may not know which production runs consume the most energy until you install the application. Then you see your usage and can take steps to reduce. I like to use the analogy of a race car team. In the first year, they just got started and did a minimal investment. The result was a losing season. Then, they put in a data logger. By seeing exactly where and how to improve the car, they won nine of the next 13 races. The owner also owns a dairy. He used the same thinking there, became more knowledgeable about the process, and was able to make improvements.”Track-and-trace applications are beginning to resurface not with a full manufacturing execution system (MES), but as a non-intrusive data capture application, according to Abildgren. Not just a historian, but as a way to extract context out of process data. Track-and-trace data may even be monitored by finance departments, as well as the expected operations and engineering professionals.Grain to glass
Turning to yet another industry that discovered value in a software track-and-trace application, Wonderware customer New Belgium Brewery, of Ft. Collins, Colo., installed a later version of its software and integrated it with process automation from Opto 22, of Temecula, Calif. Chief Electrical and Automation Engineer Igor Valuyev says that making things easier and better for required tracking was the initial justification for the system.“Operators have a lot of data stored,” says Valuyev. “Previously, this was kept in three-ring binders.” It took teams of people to try to manually traverse the system, Valuyev relates. Data recovery was slow, and manual entry of data could lead to problems. Then, there were the homemade databases scattered throughout the plant. The track-and-trace system changed all that. “One of the measures of success of the system so far is the ability to go from grain to bottle and find necessary information within 30 minutes,” says Valuyev. “We wanted to reduce the amount of work required for operations, optimize our processes, consolidate data and make the whole system more user friendly as well as compliant.”New Belgium is still discovering all the benefits of the system, but the biggest so far is that data is more organized, says Valuyev. “We created a repository with a Web interface into the system so we have immediate visibility into the process and can tell when performance is good, or if it is going the wrong way. We also use Six Sigma and have integrated information from the track-and-trace application to it to a certain extent. We’re continuously improving exposure to bottlenecks in manufacturing or finding potential opportunities for improvement,” he adds.The application includes software objects built within Wonderware’s Application Server, a Web-based portal with Microsoft Visual Basic and Sharepoint, and Wonderware’s SQL server. “After we put it in, we learned a lot about our process,” concludes Valuyev. “We’ve been able to track from grain to glass—further than about anyone can go. It was a learning process and took quite a bit of time to get it right. If we have a problem, the system makes our job easier, since we can discover where the problem was introduced into the process and react faster. We see future uses of the system in analyzing our bottling capacity and planning for future expansion.”Chemical manufacturers are faced with a growing alphabet soup of regulations. Meeting this mishmash of mandates is difficult enough for chemical industry manufacturers with a handful of products that remain the same year after year. But for Eugene, Ore.-based Willamette Valley Co., which has numerous product lines with exact formulations that might change daily or hourly, a highly engineered information technology (IT) solution was necessary to ensure compliance. The engineered wood products company manufactures a broad spectrum of products used in plywood and construction-related industries. Offerings range from patch and putty, and paint, primers, sealers and repellents to specialized two-part elastomer coatings and spike-filling compounds used in railroad ties.Safety data sheets
Before Willamette Valley implemented IFS Applications from the Sweden-based ERP supplier Industrial and Financial Systems AB, (IFS) in 2002, the company was at a disadvantage in creating the materials safety data sheets (MSDS) required to ship their products across county or state lines—or to export to other countries. “The legacy system that we had was not ideal,” Willamette Valley Chief Information Officer Gerald Nakamura says. “It was more a separate, disparate system that required you to log in to generate the transport documents, so there was a lot of duplication of effort. We were really running two systems instead of one integrated package.”Nakamura says the natural solution was to integrate Willamette Valley’s instance of IFS Applications with a regulatory compliance package from Montreal, Quebec, Canada-based Atrion International Inc. “IFS was smart enough to recognize the best strategy and recommend integration,” notes Nakamura. “In a nutshell, it was a very well thought-out strategy by both IFS and Atrion. It was one of my better integrations with IFS. Right when we hooked it up, it worked out of the box.”The database-level integration eliminates re-work that had previously been necessary, and the system has been easily uplifted to accommodate newer versions of Oracle databases and a 2006 upgrade of IFS Applications, according to Nakamura. “During our recent upgrade of IFS Applications, we had to test the integration with Atrion, and it worked as expected,” Nakamura say. “What is important is that we have documents ready about our products for our customers and our shippers. These documents are automatically ready to go on every shipment even as we change our formulations on the hour or on the minute.”Make it right
Track-and-trace applications are typically historical in nature—providing improved ways of sorting through past production and finding relationships. There is another possible use, according to Rich Bruening, global product general manager, discrete solutions, for automation vendor GE Fanuc Intelligent Platforms, in Charlottesville, Va.“We’re trying to focus not just on genealogy, but on making sure you build it right the first time,” says Bruening. “We want to help customers ensure that the process is executed correctly. If we do, then they should be able to contain warranty expenses.” Automotive manufacturers are spending a lot of money to get early warning information from the field about potential quality problems that may be increasing due to the outsourcing of more and more work, Bruening observes. “We think we should help with a system that provides that ability right at the point of manufacture or assembly.”With automotive companies now seeing major exposure to quality problems from Tier One suppliers, there is a movement to spin off some of that exposure to them. Bruening notes, “In order to get their arms around the problem, auto makers have put wording into contracts to the effect, ‘if you supply bad components, I’ll charge you for the warranty.’ So the suppliers need a ‘birth certificate’ to deliver with each shipment. GE Fanuc’s Tracker product can both help the companies error-proof manufacture and deliver genealogy documentation.”Help exists for tracking through the supply chain in even more industries than automotive. Stewart McCutcheon, chief executive officer of Acsis Inc., a supplier of manufacturing and supply chain software based in Marlton, N.J., says, “Drivers for track-and-trace applications include the need for a safe, secure and efficient supply chain. Ensuring public health and safety is behind most applications. But companies are also introducing real-time sensing to achieve efficiency through error proofing. Then, as companies move toward pull manufacturing with an extended supply chain, they are looking for ways to account for quality, even when they don’t own all the manufacturing steps.”Track-and-trace applications have grown far beyond their original “insurance policy” role into an important business tool for success.
Product developers at ABB figured that this application was so ingrained in all parts of manufacturing that they built track-and-trace functionality into the company’s flagship 800xA control platform. But the basic question is probably not whether to do track and trace, but rather what are you going to do with it.“One big advantage of this application, of course, springs from the regulatory issue,” says Leroux. “This is a critical business risk. If you can’t find your product or don’t know where your components came from, you could have to shut down your business.” Leroux notes that companies now are starting to take advantage of the 800xA track-and-trace capability to provide better and more efficient customer service. Customers are not as loyal to a brand as in the past, so companies are looking to maximize investment returns and find cheaper materials,he says. Because people are not paying more for a brand but paying for customer service, applications that improve this function provide a competitive advantage. Leroux provides an example of a company in the paper industry that began using its track-and-trace application to evaluate customer complaints. “Previously, complaints took up to a week to resolve going through four or five departments with many manual records,” he says. “Now they can move the complaint automatically through the computer system with one person. The result was a reduction in the system from multiple people tied up for a week to one person tied up for a couple of hours.”The paper company application could be somewhat complex. The process is that chemicals and pulp enter the system. They go through a machine that outputs a huge roll of paper. This roll is then cut down to 60 rolls. Each roll then feeds a “sheeter” that cuts the paper into familiar sheets. Sheets are assembled into reams; the reams fill a box; and the boxes are placed on pallets for shipment.The problem entailed tracking a customer complaint from one box or even one ream of paper back to the roll. As someone went through the system, he or she would look for other customers who received products from that roll who might have similar problems. A quick call would uncover that either this was an isolated instance or that there was a bigger problem. If it were a bigger problem, engineers could use the same data to help find the root cause and fix the problem. Customers were impressed that the company didn’t wait for a complaint and then delay and answer, but that the company had a solution sometimes even before the customer knew it had a problem.Switching from the pulp-and-paper industry to food production, Mike Hader, director of information technologies at Odom’s Tennessee Pride Sausage Inc., in Madison, Tenn., acknowledges that his track-and-trace application began in response to U.S. Department of Agriculture and, to some degree, FDA regulations. Tennessee Pride uses a software application that is now owned by Infor Global Solutions, a supplier of enterprise software based in Alpharetta, Ga.Says Hader, “We implemented lot tracking at the end of 1999. Lot management is absolutely crucial to Tennessee Pride. This is partly due to government regulations, but also because it’s part of our warehouse inventory rotation. Everything we produce has a short life span. It’s crucial that we ship the oldest lot first. This is made even more complex by dating the products. Different customers have different dating requirements that must be tracked. So, we can’t just manage by SKUs (stock keeping units), but we must also track lot number.”If there would be a problem that drew questions from the FDA, Tennessee Pride would have to trace forward and backward from the problem. Anything that touches the food, including packaging, must be identified. “Admirably,” says Hader, “Infor’s ERP (enterprise resource planning) does a good job of this. The inventory dashboard we use can drill into a product, and managers can see how many are in each of different age buckets and then drill in further to see how many are in the warehouse.”Fresh sausage
Benefits of a track-and-trace application at Tennessee Pride begin with compliance to government regulations. From a finance point of view, though, it allows the company to manage inventory to get sufficient inventory turns. Getting suppliers to use bar codes allows the system to expand into the supply chain. Since it uses third-party warehousing, the application enables significant automation of the entire inventory-to-shipment system.The consumer packaged goods (CPG) industry faces its own challenges, but one that it doesn’t face is stringent government regulation. Charlie Rastle, CPG industry manger for Rockwell Automation Inc., the Milwaukee automation supplier, says that industry adoption of track and trace is more in relation to product recall possibilities. “Originally, companies found that existing paper-based systems met the few needs that they had. But these companies are now looking for ways to improve overall business. So they track inventory in plants to achieve better control of the supply chain. “According to Rastle, the classic situation is when an order comes in through the ERP system. Assurance that there are sufficient materials to make the product comes through a track-and-trace application. It offers an automated way to coordinate inventory and production orders to enable a company to achieve close to “just-in-time” management.A second useful benefit comes from linking manufacturing to sustainability. “If I can track better, I can identify where my waste streams are,“ says Rastle. “I can also see how big these are and then go about finding and correcting them.” He notes that Rockwell is also starting to see track-and-trace applications used for activity-based costing. “If you trace right, you can do it. In the CPG industry, you have so many products, you need to know how much each costs. In each step, you have waste. As you have more visibility, you can know more about your process and go out and make improvements. We’ve also seen linking Lean Manufacturing to Six Sigma,” Rastle adds. “Lean teaches to go out and analyze processes. Companies then use Six Sigma methodology to fix.”Sometimes, track-and-trace applications are seen by management as investments comparable to insurance policies. Maybe it’s something you know you need, but you don’t see the value until you have a claim—something you don’t really want. Similarly with track and trace, if that application was procured just for assurance of prompt response to a necessary recall and you never have a recall, then what was the value?Claus Abildgren, marketing manager, production management, for software supplier Wonderware, a division of Invensys located in Lake Forest, Calif., sees companies having a hard time justifying an upfront return on investment for a track-and-trace application. “Think about energy savings,” he notes. “You may not know which production runs consume the most energy until you install the application. Then you see your usage and can take steps to reduce. I like to use the analogy of a race car team. In the first year, they just got started and did a minimal investment. The result was a losing season. Then, they put in a data logger. By seeing exactly where and how to improve the car, they won nine of the next 13 races. The owner also owns a dairy. He used the same thinking there, became more knowledgeable about the process, and was able to make improvements.”Track-and-trace applications are beginning to resurface not with a full manufacturing execution system (MES), but as a non-intrusive data capture application, according to Abildgren. Not just a historian, but as a way to extract context out of process data. Track-and-trace data may even be monitored by finance departments, as well as the expected operations and engineering professionals.Grain to glass
Turning to yet another industry that discovered value in a software track-and-trace application, Wonderware customer New Belgium Brewery, of Ft. Collins, Colo., installed a later version of its software and integrated it with process automation from Opto 22, of Temecula, Calif. Chief Electrical and Automation Engineer Igor Valuyev says that making things easier and better for required tracking was the initial justification for the system.“Operators have a lot of data stored,” says Valuyev. “Previously, this was kept in three-ring binders.” It took teams of people to try to manually traverse the system, Valuyev relates. Data recovery was slow, and manual entry of data could lead to problems. Then, there were the homemade databases scattered throughout the plant. The track-and-trace system changed all that. “One of the measures of success of the system so far is the ability to go from grain to bottle and find necessary information within 30 minutes,” says Valuyev. “We wanted to reduce the amount of work required for operations, optimize our processes, consolidate data and make the whole system more user friendly as well as compliant.”New Belgium is still discovering all the benefits of the system, but the biggest so far is that data is more organized, says Valuyev. “We created a repository with a Web interface into the system so we have immediate visibility into the process and can tell when performance is good, or if it is going the wrong way. We also use Six Sigma and have integrated information from the track-and-trace application to it to a certain extent. We’re continuously improving exposure to bottlenecks in manufacturing or finding potential opportunities for improvement,” he adds.The application includes software objects built within Wonderware’s Application Server, a Web-based portal with Microsoft Visual Basic and Sharepoint, and Wonderware’s SQL server. “After we put it in, we learned a lot about our process,” concludes Valuyev. “We’ve been able to track from grain to glass—further than about anyone can go. It was a learning process and took quite a bit of time to get it right. If we have a problem, the system makes our job easier, since we can discover where the problem was introduced into the process and react faster. We see future uses of the system in analyzing our bottling capacity and planning for future expansion.”Chemical manufacturers are faced with a growing alphabet soup of regulations. Meeting this mishmash of mandates is difficult enough for chemical industry manufacturers with a handful of products that remain the same year after year. But for Eugene, Ore.-based Willamette Valley Co., which has numerous product lines with exact formulations that might change daily or hourly, a highly engineered information technology (IT) solution was necessary to ensure compliance. The engineered wood products company manufactures a broad spectrum of products used in plywood and construction-related industries. Offerings range from patch and putty, and paint, primers, sealers and repellents to specialized two-part elastomer coatings and spike-filling compounds used in railroad ties.Safety data sheets
Before Willamette Valley implemented IFS Applications from the Sweden-based ERP supplier Industrial and Financial Systems AB, (IFS) in 2002, the company was at a disadvantage in creating the materials safety data sheets (MSDS) required to ship their products across county or state lines—or to export to other countries. “The legacy system that we had was not ideal,” Willamette Valley Chief Information Officer Gerald Nakamura says. “It was more a separate, disparate system that required you to log in to generate the transport documents, so there was a lot of duplication of effort. We were really running two systems instead of one integrated package.”Nakamura says the natural solution was to integrate Willamette Valley’s instance of IFS Applications with a regulatory compliance package from Montreal, Quebec, Canada-based Atrion International Inc. “IFS was smart enough to recognize the best strategy and recommend integration,” notes Nakamura. “In a nutshell, it was a very well thought-out strategy by both IFS and Atrion. It was one of my better integrations with IFS. Right when we hooked it up, it worked out of the box.”The database-level integration eliminates re-work that had previously been necessary, and the system has been easily uplifted to accommodate newer versions of Oracle databases and a 2006 upgrade of IFS Applications, according to Nakamura. “During our recent upgrade of IFS Applications, we had to test the integration with Atrion, and it worked as expected,” Nakamura say. “What is important is that we have documents ready about our products for our customers and our shippers. These documents are automatically ready to go on every shipment even as we change our formulations on the hour or on the minute.”Make it right
Track-and-trace applications are typically historical in nature—providing improved ways of sorting through past production and finding relationships. There is another possible use, according to Rich Bruening, global product general manager, discrete solutions, for automation vendor GE Fanuc Intelligent Platforms, in Charlottesville, Va.“We’re trying to focus not just on genealogy, but on making sure you build it right the first time,” says Bruening. “We want to help customers ensure that the process is executed correctly. If we do, then they should be able to contain warranty expenses.” Automotive manufacturers are spending a lot of money to get early warning information from the field about potential quality problems that may be increasing due to the outsourcing of more and more work, Bruening observes. “We think we should help with a system that provides that ability right at the point of manufacture or assembly.”With automotive companies now seeing major exposure to quality problems from Tier One suppliers, there is a movement to spin off some of that exposure to them. Bruening notes, “In order to get their arms around the problem, auto makers have put wording into contracts to the effect, ‘if you supply bad components, I’ll charge you for the warranty.’ So the suppliers need a ‘birth certificate’ to deliver with each shipment. GE Fanuc’s Tracker product can both help the companies error-proof manufacture and deliver genealogy documentation.”Help exists for tracking through the supply chain in even more industries than automotive. Stewart McCutcheon, chief executive officer of Acsis Inc., a supplier of manufacturing and supply chain software based in Marlton, N.J., says, “Drivers for track-and-trace applications include the need for a safe, secure and efficient supply chain. Ensuring public health and safety is behind most applications. But companies are also introducing real-time sensing to achieve efficiency through error proofing. Then, as companies move toward pull manufacturing with an extended supply chain, they are looking for ways to account for quality, even when they don’t own all the manufacturing steps.”Track-and-trace applications have grown far beyond their original “insurance policy” role into an important business tool for success.
Companies in this Article
Companies in this Article
Sponsored Recommendations
Sponsored Recommendations
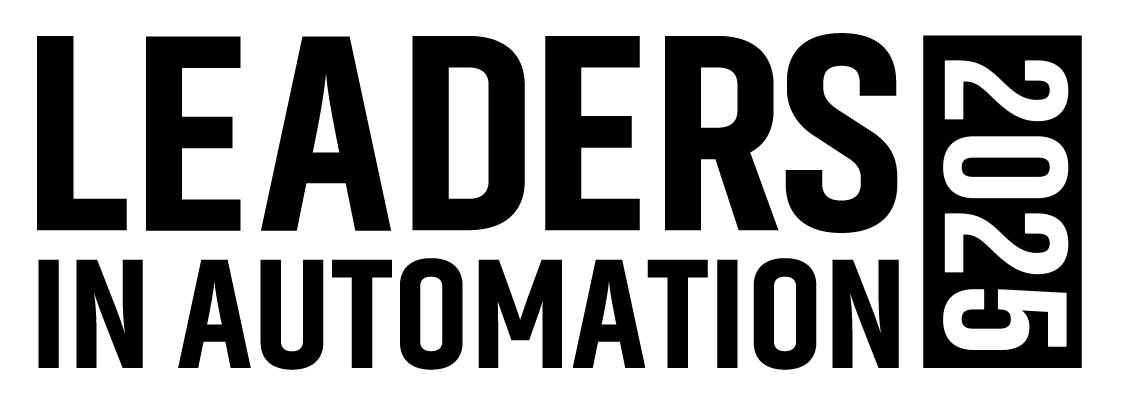
Leaders relevant to this article: