Sidebar: To read the accompanying sidebar to this article, go to www.automationworld.com/feature-4380
What is not lovable is a standard that is a-building, when controversy clouds the issues, arguments grumble on, and useless light and heat are thrown off. Welcome to the currently unlovable standards situation in wireless communications for industrial use.
Of course, wireless for industry is just a radio. And controls these days are just computers. In the world where radios and computers play together, there are plenty of existing standards for all sorts of needs—ZigBee, Bluetooth, WiFi, to use their street names—but for various reasons, they have problems in factories. Some consume more power than is feasible for battery-operated equipment. Some invite highly problematic interference. Some require unwanted middleware or kludges to connect to automation. Some are just not reliable enough to handle industry (you would not, for example, want to use your cell phone to monitor a pressure vessel full of volatile compounds).
Fortunately, people are tackling the problem of wireless for automation. One effort is the WirelessHart communications standard, a fledgling that is recently out of the nest and learning to fly. And there is the ISA100 effort, still hatching.
WirelessHart, part of the Hart 7 specification of the Hart Communication Foundation, can be thought of as a vertical standard, one developed for a single automation protocol for process industry. At the moment, it is happiest when applied to devices that provide intermittent and more or less one-way sensor reportage. In contrast, ISA100 (more specifically ISA100.11a) in development by the Instrumentation, Systems and Automation Society (ISA) is horizontal—or more nearly horizontal—because it is being designed to meld various specifications into what ISA100 documents call “a family of standards.” This family will eventually cover such protocols as Hart, Foundation Fieldbus, Modbus, Profibus, Common Industrial Protocol (CIP) and more. It will eventually cover all automation needs, including closed-loop control. Further, it will be (or can be) applicable to both process and discrete manufacturing.
The strongest positive for WirelessHart is that it is done, having been ratified in September of last year. Fully and officially compliant devices will be available this year from ABB, Emerson Process Management, Endress+Hauser, Siemens and perhaps others. A second positive for those with Hart-compliant automation installations is that if it lives up to the promise, WirelessHart equipment will easily join any existing Hart network, no problem, no learning curve, no lost time.
On the other hand, the greatest promise of ISA100 is its one-standard-fits-all approach. If it can deliver on its promises, the benefit to end-users is huge, simplifying equipment procurement, reducing spares inventories, and cutting network installation and configuration time. A second promising note is that ISA100 has long actively solicited input from end-users, with a number of end-user members on various committees. When done (and if it is done right), ISA100.11a should have stronger standards as a result of this participation.
At the same time, negatives are inherent in each. A protocol-specific wireless specification such as WirelessHart raises the specter of competing specifications for every individual automation protocol still in use, new or old. The biggest drawback of this is potential fragmentation of vendor offerings—and the laws of production dictate that the fewer devices produced for a given protocol, the higher the cost per device. On the other hand, the overarching drawback of ISA100 is its ambitious attempt to be comprehensive. There is a chance that is has bitten off more than it can chew. And, there will be a lot of jawing and a lot of friction before everyone is equally happy (or equally unhappy but grumbling only slightly).
There are significant benefits to a standardized technology. Jim Reizner, corporate engineering, at The Procter & Gamble Co., the big Cincinnati-based consumer products company, puts it this way: “Take the 4-to-20 milliAmp (mA) standard, which is so ubiquitous that many don’t even recognize it as a standard. The 4-20 standard defines a lot more than just electrical current levels—it defines a multitude of aspects required to make systems and instruments from various vendors interchangeable. Think about it—when a 4-20 mA pressure transmitter from one vendor fails, what happens when technicians go to the storeroom to get a replacement? They need only make sure the replacement device meets the application requirements—things like pressure range, metallurgy, process connection method and so on.
“The tech does not need to make sure the 4-20 mA from vendor A is compatible with the 4-20 from vendor B,” Reizner notes. “This kind of interchangeability is defined by the standard. It means we can use instruments from one company with control systems from another, and we can replace instruments from one vendor from those from another vendor. We can purchase instruments and equipment that are priced right.
“At Procter & Gamble, we tie our involvement in standards directly to the people who are the most important to us—the people who purchase and use our products. Without standards-based production equipment, the price of products to our consumers could possibly increase, and keeping our costs low would be more difficult.”
Not incidentally, Reizner is co-chair of the ISA100 End User Working Group, which provides direct input into the ISA100 development process—meaning that he has already been involved in wireless implementation at P&G. Has P&G forged ahead without standards?
Not really, he says: “Whenever we can, we produce on standards-based equipment. So, even when it was too early for WirelessHart, there were standards involved in our wireless installations. Everyone’s equipment follows some standard, and the vendors readily provide that information. Their radio may be IEEE 802.15.4 (a standard of the Institute of Electrical and Electronics Engineers), or they may be using IEEE 802.11b/g or others. The important thing is to understand what compliance to those standards means to your application, and more importantly, what compliance to such standards does not define for your application. This means that, at the moment, wireless standards compliance is much more complex than it will shortly. Right now, you have to get into the details of the wireless landscape if you want to be sure you’re applying the best solutions for your specific problems.”
Cliff Whitehead, manager, Strategic Marketing for vendor Rockwell Automation Inc., in Milwaukee, emphasizes the need for industry-specific standards for wireless. “The unique aspects of wireless mean that standards are important. In the wired world, it’s easy to trace the cable to the device. And, you can be confident of unequivocally determining that the devices at both ends of the wire are working properly, and are reliable and secure. They are tangible. Things are far less tangible with wireless.”
Plus, wireless communications raise new issues. “You’re sharing a medium—RF (radio frequency) energy in the atmosphere. This medium has many, many potential users—from microwave ovens to PDAs (personal digital assistants), cell phones, MAN (municipal area network) grids—there are a lot of radios inside a manufacturing environment. If you don’t establish boundaries and rules that everybody can play by, you have the potential for chaos.”
The benefits to end-users are clear, but there are benefits to suppliers as well. Bob Karschnia, director of technology for Austin, Texas-based automation supplier Emerson Process Management, points out, “A decade ago, conventional wisdom said that pursuing standards is a poor thing to do for a vendor—it’s better to do something proprietary, so you can lock out the competition. But we’ve come 180 degrees from that point of view. We’re convinced that standards-based equipment is to our advantage. Proprietary offerings may have a larger piece of the market, but that market is a much smaller pond than is possible. Standards-based offerings give you a lower market share percent, but the lake is far larger. Our estimate is that 80 per cent of process control today is shipped with Hart capability—and there are some 20 million to 25 million installed devices. We were happy to open up our technology, co-developed with Dust Networks, (a Hayward, Calif., wireless technology company) to the WirelessHart effort—it’s the best way to refine the details and the best way to get it deployed.”
The process world is increasingly implementing wireless—industrial standards or not. Wireless technologies have already made appreciable inroads in data transmission from sensors, and wireless is already doing a little control here and there. In other words, industrial users are turning on the radio because they have work to get done, and wireless helps them do that work. With two key standards either already on stage or in the wings, what strategies can end-users adopt that will allow eventual standardization for applications right now, which are by definition non-standard?
“We did a massive amount of field trials in cooperation with early adopters of our wireless equipment,” says Karschnia. “Two primary modes of implementation emerged—the FCC (Federal Communications Commission) point of view that says, ‘I control every aspect of this wireless space,’ or a more eclectic network view that ensures workability regardless of RF noise.”
Karschnia argues that attempting total control is fruitless. “In case after case, problems turned out to resist resolution. It wasn’t the predictable noise from emitters—Wifi, cell phones, things like that—it was dead spots or EMI (electromagnetic interference) pulses when air conditioners kicked on, or noise from any number of different kinds of equipment.”
Enter the self-determining network: “Instead of trying to control what you cannot control, design the network to work around problems as they come up. About the time that we came to this conclusion, we ran across Dust Networks and were impressed with their time-synchronized mesh network algorithms to work their way around network disruptions.”
There are, of course, other methodologies for defeating noise: dedicated transmission bands, highly tuned antennas, spread-spectrum/frequency-hopping, electromagnetic impulse suppression or filtering devices, and more.
“Our earliest applications of wireless were for what I call our niche applications,” says Procter & Gamble’s Reizner. “These were high-return applications, including areas or distances where wires just wouldn’t work, or were driven by specific technical needs. We did think about standards to the degree those standards were available—such as IEEE 802.11a.”
Many of the more sophisticated users followed this available-standards approach. Many more were less interested in any form of standards. They simply wanted to get work done, saw radios as the best solution, and installed their own units, standards or no standards. Their focus was on functionality, and these early installations might make for more or less isolated islands in the near future.
The key is to start with a defined application need. “People who start out with the goal of applying wireless technology rather than solving a business problem are going to work themselves into trouble,” Reizner says. “Those trying to apply wireless without any knowledge of the wireless landscape will likewise work themselves into trouble.”
Will the installed applications change, once standards are available? Reizner explains, “For applications that turn out to be non-standard, we would be highly unlikely to rip the equipment out and replace it with standard equipment—unless this was technically required to get the job done, such as interfacing with a newer system. Some of the vendors for wireless systems note that they will provide an upgrade path to the standard, once the standard is available, but they forget to note the costs of the upgrade, and you need to be aware of these. They can be significant.”
Emerson’s Karschnia underscores that “end-users ask us for something that works, but increasingly they also ask us to show them how a given installation will be standardized in the long run.”
The march of technology is in our favor, since so many basic infrastructures have been dynamic, to say the least. Telecommunications moved from copper to fiber and from fiber to cell technologies in not much more than 10 years—with plenty of copper and fiber still being installed. The result is a growing army of engineers designing chip-based modular hubs and interfaces that allow everything to talk with everything else. Much of this design effort is readily transferred to industrial needs, offering the economies of plug-ins, swap-out boards, and modular routers not just for wireless automation, but for control in general.
The real key, of course, would be to design an installation that will work to every standard that will eventually appear. To say the least, this poses a significant challenge. “There are many areas where we don’t know yet what we don’t know,” says Dave Kaufman, business development director for automation vendor Honeywell Process Solutions, and who is active in ISA100 development. “Wireless in production will change how we do things. It will add new capabilities, and we have no idea what people will discover, what new needs will arise. The standards effort is laying the groundwork for efficiency and effectiveness for next 20-30-40 years.”
Reizner advises, “Identify the problem you’re trying to solve. Wireless can be intrinsically attractive, but you don’t want to have a solution where you’re not too sure of the problem it addresses. Once the problem is clearly identified, having a good understanding of the plethora of potential solutions—and tradeoffs—is important, wireless or not.”
He suggests working with one vendor, when possible, “or with vendor groups, when they can show a track record of working together to provide successful wireless installations.”
Modularity provides another avenue for future-proofing, provided that the modules are priced such that swapping is economical.
Rockwell’s Whitehead underscores the need to add standards participation by a given vendor. “You future-proof by looking at who is participating in standards activity. Find out who provides a clear migration path from today’s device to a standards-based one. This doesn’t restrict you just to the big names, though these are all involved—many second-tier and niche producers are helping in the process.”
“The more heads,” he says, “the better the solution when you come to consensus. The fundamental strength of the standards process is that it’s smart people bringing their experiences, trying to find the best of a range of good solutions.”
Automation World has extensively covered industrial wireless topics. To see more, search terms ISA100, WirelessHart or wireless at www.automationworld.com.
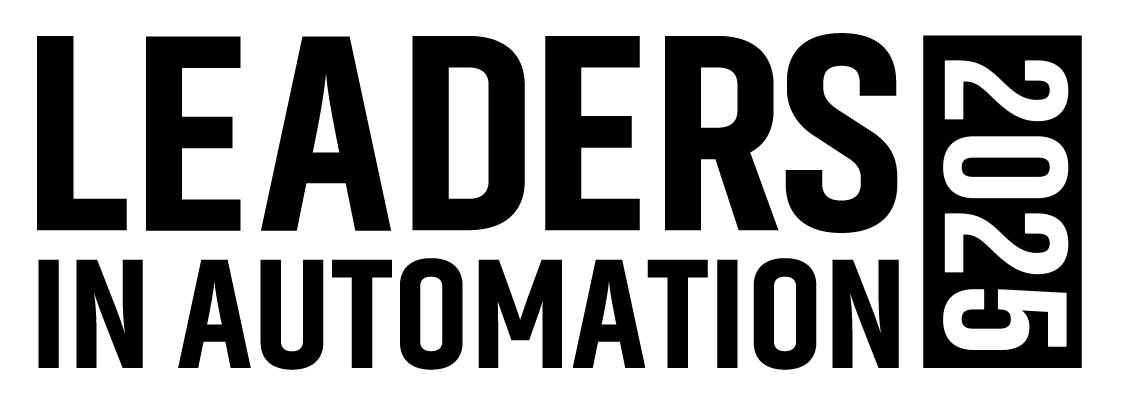
Leaders relevant to this article: