Market-driven demands for increased flexibility and faster changeover in packaging line operations have spurred innovation in automation, including that fundamental building block of automation—motion control. Design improvements coupled with increases in computer processing power and bandwidth for data acquisition have combined to make motion control systems smaller and smarter, yielding an array of operational benefits and rendering them more capable of tackling 21st century packaging challenges. Though consensus has begun to form on the design front, questions remain on how best to make use of the added intelligence that designers of motion control systems now have at their disposal.
First, design. The buzz here centers on the new generation of servo modules that combines the servo motor and drive into a single compact package. Attempts to combine these components began more than a decade ago, with varying degrees of success. Usually, these were repackaging of existing components, and their benefits were partially offset by problems with heat dissipation in the smaller form factors, which generally limited them to power levels of 1 kilowatt (kW) or less.
In the past year-and-a-half, however, servo-drive modules with modular components specifically designed for integration have hit the market. The number of components and overall size have both been reduced, and heat build-up lessened, making them suitable for a wider array of applications. Their manufacturers can point to some significant benefits from this new generation of integrated servo-drives.
“In terms of the cost of a packaging system, our integrated servo module approach saves 15 percent in component costs alone compared to our own conventional servos, and OEMs (original equipment manufacturers) have documented much higher savings in wiring and cabinet space,” says Tom Jensen, engineering manager for Elau Inc., Schaumburg, Ill.
The wiring reduction Jensen mentions is achieved, firstly, by the fact that integrated drive and motor combinations eliminate the wiring previously required between the drive and motor. System design accounts for further reductions. Jensen again: “We are using a single cable segment from cabinet to distribution module, then dropping down one cable to each of our servo modules. This cable includes the motion network and power. Feedback cables are eliminated because feedback from the motor encoder to the drive is within the module. We can also eliminate the need for a separate device bus on the machine.”
In Elau’s system, each distribution module can service up to four servo modules. The cables that are used end in single, snap-fit connectors, leaving no individual wires to be terminated on the drives—another feature designed to simplify and speed installation and maintenance.
“If a motor or servo drive need to be replaced,” explains Jensen, “instead of detaching all the wiring from the drive in the cabinet and dismounting it, then unbolting the motor, our system allows you to simply remove the four motor mounting bolts, flip the cable connector open, and replace by reversing those steps.” Motors and drives are thus replaced together so that the source of the failure can be analyzed back at the repair facility without impeding production.
Simplifying and speeding wiring, and thus installation and maintenance, has become something of a mantra among leading motion control vendors, and with good reason. As Rob Rawlyk, product manager for vendor Beckhoff Automation, Burnsville, Minn., notes, “Installation time is often a very significant factor and can have a considerable impact on the bottom line. As a general rule that everyone should agree with, fewer wires result in faster installation, easier maintenance and a better machine. Less required wiring time also leads to fewer chances for wiring errors.”
Bob Hirschinger, marketing manager, Logix motion, for automation supplier Rockwell Automation Inc., Milwaukee, notes another benefit arising from the simplified wiring of these newer motion control systems: “Reduced wiring requires less supporting hardware such as fuses, contactors, resistors and filters. Fewer components helps machine builders lower their total cost to design, develop and deliver.”
Cabinet concerns
Today’s integrated servo motor and drive configurations also address another concern occasioned by the proliferation of servos for motion control—excessive cabinet size. Removing the drives from the cabinets and placing them with the motors immediately and significantly shrinks cabinet space requirements. And smaller cabinets can yield some rather large benefits, as Elau’s Jensen points out. “Cabinet size is both an initial cost and a footprint issue. Plus, heat from drives may need to be dissipated, causing the cabinet to be air conditioned, which becomes an energy consumption issue.”
Jensen notes that the move to integrated servo modules also allows new modules to be added or upgrades field-retrofitted by plugging them in, without impacting the electrical cabinet. “The common practice of requiring an extra 30 percent open space inside the cabinet can now be eliminated.”
Reducing cabinet size, which at first glance can seem largely a housekeeping issue, can thus impact flexibility. As Rami Al-Ashqar, control product manager for automation supplier Bosch Rexroth Corp., Hoffman Estates, Ill., points out, “Let’s say you wanted to add a de-stacker. In the past, you might have needed to change your whole cabinet to add the additional servo axis. Now, with our new integrated drive and motor solution, all you have to do is just run another cable to the new module and you’re done. These drastically reduced, simplified cabinets also make it a lot easier for maintenance engineers to locate problems if they occur.”
Robots too
These advantages are being felt in the fast-growing robotic packaging segment as well. Dave Pap Rocki, chief technical officer for Adept Technology Inc., a Livermore, Calif.-based robotics supplier, notes that his company’s recently introduced Quattro packaging robot has the drives and servo system integrated into the base of the robot. “This greatly simplifies design of the control cabinet and cell. And with servo control at the drive, we can increase the update rate for robot trajectory and servo loops. This allows smoother and faster performance.”
Though the use of integrated servo modules will, by itself, reduce cabinet space requirements, machine designers have a role to play in maximizing these benefits. Mike Wagner, global segment business manager, packaging, for Rockwell Automation stresses that “there are also good design practices that need to be followed. OEMs must begin to break the machine control cabinet down into smaller modules. This has multiple benefits, most of which can be realized using any off-the-shelf technology today.”
And regardless of the type of motion control product employed, Nipun Mathur, product marketing manager of motion control at National Instruments Corp., Austin, Texas, another automation vendor, cautions OEMs and users to avoid “power wastage resulting from inefficient control techniques and incorrect sizing of motors.” He advises that “using faster control systems and spending time correctly sizing motors can help in reducing the lifetime cost of the machine."
{mosimage}
The intelligence factor
As noted, these new systems are not only small, but they’re smart, with processors capable of assuming an array of operational, communication and diagnostic functions embedded in them. The reasons for downloading more intelligence to the servo module seem compelling. Mathur notes that “the complexity of machines has dramatically increased over the last decade.” Thus, “embedding more intelligence into control systems spread across the machine/plant is being used as a way to overcome this increased complexity.”
John Mazurkiewicz, president of Baldor Electric Co., a Fort Smith, Ark.-based motors and drives manufacturer, observes, “By splitting up the coordination task from a centralized controller into small, fast, decentralized tasks in the drive, the controller performance improves, due to reduced network and CPU (central processing unit) load. Easy-to-use, high level programming languages available in localized drives reduce what could be an intimidating software project to a predictable task.”
Mazurkiewicz, who is also president of the Motion Control Association, Ann Arbor, Mich., adds, “When machines operate at high speeds, safety devices must react rapidly, and any extra safety levels increase design complexity. The best solution is placing the safety responsibility in the drive.” He concludes, “Distributing intelligence down to the drive realizes immeasurable cost savings because not only is build time is faster, but commissioning is simpler.”
And increased intelligence at the device level is not simply a production-line issue. “When we talk about distributed intelligence, we really need to focus on the ability for the automation solution to communicate its status and performance to the plant supervisory systems on a real-time basis,” insists Rockwell’s Wagner. This sort of communication is facilitated—even spurred—by the steady expansion of industrial Ethernet on the plant floor. ARC Advisory Group Inc., Dedham, Mass., predicts that the market for Ethernet-based devices and input/output (I/O) will grow by more than 27 percent a year, from an estimated 1 million nodes last year to 3 million in 2012.
“The end-user needs to be able to tie the enterprise resource planning (ERP) system directly to all machines,” continues Wagner, “thereby breaking down the barriers between the making, packaging and material handling processes in a plant. At the end of the day, you will have a plant that has the ability to make decisions about workflow and production, allowing for maximum efficiency.”
A compelling proposition, but one that is not without its skeptics. Increased intelligence is, of course, a good thing, but the devil is in the details, insists Elau’s Jensen. “We do not adhere to the notion of distributing as much intelligence as far down as possible.” Keep the drive as simple as possible, he insists, rather than load it with extra functions that can drive up its price tag and, by overburdening it, degrade its performance.
“The right things to distribute to the servo,” Jensen maintains, “are all servo loop closures, including position. Offloading tasks such as cam tables, however, wastes network bandwidth, takes motion tasks out of the IEC (International Electrotechnical Commission) 61131 standardized world and onto a DSP (digital signal processor), and prevents features such as cam changes on the fly. We advocate a centralized motion and logic control strategy with a distributed motor loop control and motor/drive auto-recognition strategy.”
Others in the industry agree with that general proposition, Beckhoff’s Rawlyk among them. “While our products and solutions can support distributed architectures,” he explains, “our preferred method is to remove much of the intelligence from the servo and drive level. Having just one higher level controller and drives with less integrated intelligence helps increase functionality and reduces required programming time for most applications.”
Rawlyk says that with recent advances in personal computer (PC)-based control technology, “there are very powerful, yet inexpensive centralized control options engineers should consider. When a high-powered PC-based controller is combined with a high-speed fieldbus, a large number of drives can be more flexibly coordinated in various ways.”
How many processing functions should servos and drives be asked to perform? That’s a question that industry pros will be wrestling with for some time, and one that may eventually be answered—or rendered obsolete—by advances in computer technology. But quite apart from the question of precisely where the intelligence should be located, it’s a sure bet that the rising demand for more flexible packaging solutions will fuel the market for more intelligent motion control technology, and vendors will strive to meet those market needs.
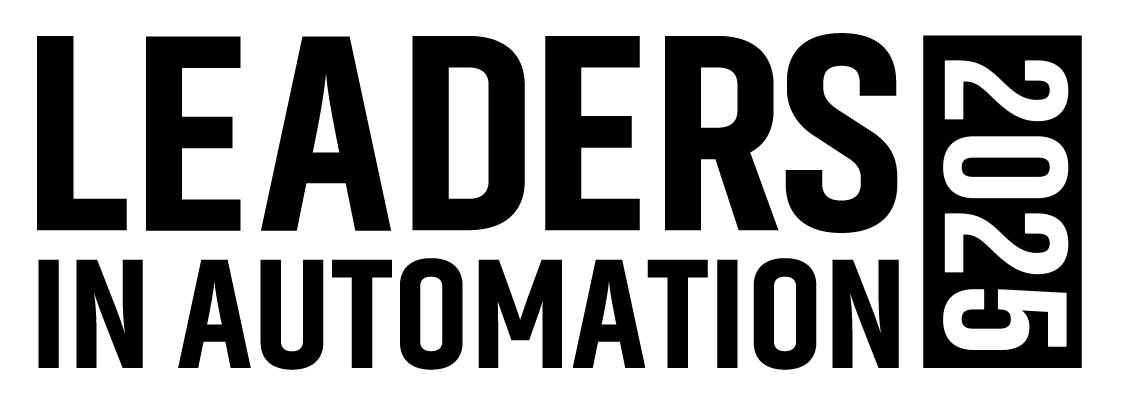
Leaders relevant to this article: