The pull of wireless technologies in manufacturing monitoring and control is strong. You can reach equipment whose motion or remoteness makes hard wiring impractical. You can integrate systems in which physical layouts, overstuffed cable trays or expensive trenching mean that wired alternatives add up to more expense than going to the airwaves. In general, you can add devices faster than is possible with wires, at least if your situation demands new wires.
That said, attaching names to specifics turns out to be hard—at the moment. Few want to put their names to applications. To be fair, the situation is influenced by the fact that wireless control and monitoring offers ways to do things that have not been done before, and some are concerned that speaking up might lose them competitive advantage. Plus, while a good many installations are relatively cut-and-dried, a significant number are literally moving into new territory, at least for the company who is being asked to talk about it. Until the bits and pieces of common experience coalesce into a more or less public body of knowledge, people have a right to be a tad uncertain about the glare of publicity.
But wireless is definitely at work, in three broad categories. The first is a long-established use of radio monitoring for point sensors or field instruments, found in a wide range of distributed systems, from electrical grids to remote sensor monitoring in a variety of manufacturing settings. While these are highly useful (and many have been in place for a long time), they tend to be one-way set-ups (from the sensor to the control system) and are generally not intricate.
The second category includes those installations in which a radio has become a virtual wire—that is, wireless transmission is taking the place of wired communications in a controller or computer network. These are a little more interesting from an automation engineering perspective.
Finally, there is general movement into new kinds of applications—or at least new kinds of benefits—stemming from new capabilities afforded by the technology. Like kids with new toys, engineers have found ways of expanding the envelope.
Still, even the basic, distributed radio-to-a-sensor set-up has interesting wrinkles, primarily because highly focused chips have become increasingly available. In addition, such infrastructure elements as self-organizing broadcast networks, or “mesh” networks, make for rapid deployment. As Robert Shear, director of market development for wireless chip vendor Dust Networks Inc., in Hayward, Calif., said of the latter, “WirelessHart and (the coming) ISA100 standards cover reliability and security issues, and self-organizing [radio transmission] networks adds the flexibility that plant people need. There are always going to be potential interruptions of wireless transmissions, and allowing every sensor the ability to seek and lock on to every possible route means that data can be delivered regardless of obstructions.”
A case in point of the strengths of self-organizing networks is provided by one Emerson Process Management customer, an offshore oil harvester. Emerson, an Austin, Texas-based process controls vendor, employs Dust Networks technologies in many of its wireless sensors. Off the coast of Norway, one of the hydrocarbon harvester’s oil rigs needed ways to monitor wellhead annular pressure, as well as heat exchanger pressure drop. Time pressures added to the challenges—when hard-wired, changes in monitoring required two days to implement. The wireless installation required two hours or less for changes, and the self-organizing network was immediately able to reach a wireless gateway placed above one side of the rig. Pre-installation concerns centered on the dense piping and labyrinthine metal structural elements of the platform: Would they interfere with radio frequency (RF) transmission?
In the actuality, there was no issue, since the sensors easily routed themselves to the access point. Instrument engineers went from a decidedly tentative attitude toward wireless to full confidence in the ability to put sensors in any needed location, and the rig’s wireless network continues to expand.
In the development of the kind of small, cost-effective wireless devices employed in the oil rig application, it hard to overestimate the long-range influence of custom chips. Dust Networks provides a single chip that is embedded in the Emerson devices. The chip combines complete, low-current RF circuitry that requires only an antenna connector, as well as self-organizing network capabilities that allow it to act not only as an end point, but also as a router.
In a similar approach, but with a slightly different focus, ConnectOne’s WirelessHart-compliant iChip line offers Ethernet wireless fidelity, or Wi-Fi, serial communications capabilities, and even a built-in Web server, suggesting that any existing device with serial communications can be made into something that can phone home to any browser. Amit Resh, who recently made the jump from research and development (R&D) to vice president, business development, for ConnectOne, in Phoenix, points out, “We feel that established Internet protocols make it easier when the last mile or meter is meant to be Wi-Fi-enabled.”
ConnectOne’s chip is already embedded in a variety of non-industrial products, including medical diagnostic equipment, and even monitoring equipment that keeps tabs on the humidity and temperature in the Sistine Chapel. A little more down-to-earth (and process-related) is an application at a food processing plant, monitoring hand-washing equipment to help the processor ensure that its personnel meets hazard analysis and critical control point (HACCP) standards. Another ConnectOne customer is about to release a truck fleet management product.
“You gain flexibility when you can transform a remote machine into a Web site that reports ten, twenty, thirty or more live parameters,” Resh says. And, although the concept is perhaps not an ideal way to spend a day off downtown, “it reaches anywhere. If you wanted, you could go into any Internet café and monitor and control to your heart’s content.”
Adds Dust’s Shear, “When basic networks are reliable and easily organized, you unlock the creativity and expertise of people in the plant. They begin asking, ‘Now that I can connect, what new chunks of information can I use?’ Technology is most valuable when the end-users have the value.”
Like the world of remote sensing, continuously rejuvenating itself with evolving standards and new embedded chips and technologies, our second category, where radios act as virtual wires, continues to expand. “It tends to be an area where closed-loop control is not critical,” points out Jeff Becker, global wireless director for process automation vendor Honeywell Process Solutions, in Phoenix. “Wireless is good where it’s hard to run wires, obviously, but it’s a technology that’s finding many other uses. We have a customer that’s using wireless to document and monitor OSHA (U.S. Occupational Safety and Health Administration) safety shower equipment—and if that may not sound like much, the result is that they have saved a million dollars in operational and compliance costs.”
The “wireless wire” type of application allows for rapid extension of process control networks. “Greenfield plant networking clearly can benefit from any workable networking approach, but expansion of existing facilities is a rich ground for wireless,” Becker says. He adduces a refinery customer that brought its tank farms directly into its automation network this way. “They already had fiber rings talking to the core,” he explains, “but the tank farm was on the edge of the facility, and they were nervous about trenching across undocumented ground. What tipped the scales initially for a wireless plan was the long lead time that was projected for trenching and pulling fiber.” Installation savings were in the hundreds of thousands of dollars—and a subsequent increase in control over scheduling and inventories followed on.
The refinery needed high availability and reliability for supervisory control from its advanced blending and movement applications. Long distances and hilly terrain around the facility site were potential problems for throughput. In the wireless network implementation, Honeywell suggested a wireless Fault Tolerant Ethernet (FTE) network. Honeywell’s FTE establishes two active paths that load-share between the two and can survive multiple faults.
To ensure high throughput of device and system messages (including alarms), system designers were able to reduce the number of wireless hops to avoid hills and a high density metal building. Honeywell connected two multi-node wireless networks via wired Ethernet, allowing two units to work together to eliminate throughput loss at hop or bridge points.
Savings and ease of implementation are simply one element of wireless—some of the most interesting applications of wireless are those in which end-users have been able to do new things or make a fundamental change in operations. Yes, wireless enables new connectivity to difficult-to-reach equipment, but in and of itself, more data is not necessarily a move forward. On the other hand, using new data to improve processes is definitely a plus.
It is not always the most sophisticated set-up that accomplishes this. An Emerson Process Management customer, a steel finishing mill, installed wireless to control cooling water spraydown. Previously, water flow was controlled by hand, based on visual judgment; now, wireless water flow meters allow scientific control over the cooling process. Once the process was instrumented, operations management discovered that optimum water flows were significantly different from what had been assumed. The result? Through better water control, the mill has reduced coil rejections dramatically.
In addition, the application is enabling the plant to model process control schemes for different steel gauge runs, which will allow precise calibration of cooling water for coil processing if and when needed.
In a second mill application, wireless pressure monitoring ensures that the bearing lubrication systems on run-out tables are working correctly, preventing bearing seizure than can damage steel moving across the tables.
A completely different application of wireless, but with the same kind of enablement through new capabilities, is a Honeywell customer that replaced clipboards and walkie-talkies with wireless mobile control stations. In the clipboard days, during times that operators were walking the plant, extra personnel had to be brought into the control room, both to watch the screens and to field the walkie-talkie traffic.
With wireless mobile stations, operators are now able to gain a control-room view directly, wherever they are in the plant. “They get full control views, including all the screens and alarms,” Becker says. “Our customer was able to redeploy the stand-by operators and smooth out operations for a combined savings of more than $200,000 per year.”
In a different application, an aerospace manufacturer was experiencing delays in bringing skidded equipment into control networks as they were moved from job to job. The company was able to bring the skids into the network using wireless. Where previously, valuable production time was lost while the skids were wired after placement; now, production is online virtually as soon as the skids are relocated.
So, the savings are there, and the technology is intriguing—what is the best way to put it in place?
The implementation of wireless, even the simplest of installations that feature self-organizing radio networking (devices, in other worlds, that are relatively plug-and-play), benefits from strategic thinking.
Preliminary considerations—heard from multiple suppliers—need to focus on two aspects of the plant’s overall wireless situation. The best-practice initial move is to perform a site survey to assess where signals may already exist. Scouring the area for existing signals has become a necessity, because there can be RF generation from computer-controlled equipment, from wireless installations at neighboring buildings and plants, and from undocumented and unauthorized implementations. “There can be many surprises from a spectrum analysis,” Honeywell’s Becker explains. “Unauthorized hot spots are becoming increasingly common, because anyone with a computer can go to a box store and pick up dirt-cheap wireless hubs or access points to set up their own private wireless net—without IT (information technology) involvement.”
The second preliminary activity is to take a best guess where wireless might be used next year and thereafter.
Determining future needs is complicated by the fact that wireless has a way of catching on; scalability can rapidly become a key issue. “Wireless has a way of expanding dramatically,” Becker says. “People do an initial installation to fix some burning need, see how it works, and then begin discovering how to use it here, there, and everywhere. It’s best to think about broad-based multifunctional systems from the start, even if right now, you think you just want to read one hard-to-reach sensor.”
Rapid expansion, in particular, can create a very real potential for transmission band and channel glut, because, as Becker says, “you can run out of spectrum fast in unplanned forays. It’s better to develop guidelines for spectrum allocation as early as possible.”
Another important consideration is availability, which can be distinct from reliability. The technology is mature enough to ensure—well, almost ensure—that the radios on
well-engineered devices will remain on the air. The question is, will they (and their broadcast network) always be available to transmit necessary data in a timely manner? “In process applications, real-time or near real-time availability is crucial,” Becker points out. “Yes, you can generally be assured that data will reach its destination, but if it arrives a half-hour late, there can be serious consequences.”
A related issue is to understand speed trade-offs. Fast, high bandwidth transmissions such as those needed for industrial Ethernet, control, or mobile worker applications have a set of network needs that differ from slower, battery-conserving transmission modes. Even a single device can have multiple speed requirements—relatively leisurely for ongoing running data, then real-time for alarms and alerts, or for updating on demand. “In an ideal world, you would design a network capable of multiple speeds,” Becker says. “That way, you have the flexibility to match applications directly to their power consumption and speed requirements.”
Standards-based devices promise easier integration of multi-sourced equipment, as well as easier implementation compared to proprietary wireless devices. Becker asserts that any system selected for industrial plant use should support Wi-Fi and wired Ethernet, and have a migration path to the ISA100 standard.
On the hardware side, chip-based embedded wireless frees the primary circuitry of a device to concentrate entirely on specific control strategies. “Chips allow device developers to focus on device functionality and free up device CPUs (central processing units) for the task at hand,” says ConnectOne’s Resh. “Chips can offload the transmission elements, including runtime radio requirements or Ethernet and Internet connectivity.”
Even if your current needs call only for relatively time-insensitive reading of sensors, plan for future open-loop control requirements. “It is far easier to use a control-ready system for monitoring than it is to be forced to upgrade a monitoring-only system in the future,” Becker points out.
Crucial for battery-operated equipment are ways to predict current drain and thus determine maintenance intervals. Downtime for a surprise battery swap is not the happiest of ways to allocate production time.
“Application interfaces are usually driven by their respective departments,” Becker says. “And many users want to bring information coming from their wireless devices into their existing legacy applications and protocols. Having the ability to network easily with legacy applications is ideal, and it allows the network to service the entire operation—not just single departments.”
Plants experience changing environments, and because wireless can be affected by transient line-of-sight problems, implementations need to consider such elements as traffic, and rain and snow. A sunny-day installation on a quiet day can become difficult when a parade of trucks is filing into the docks or an afternoon thunderstorm rolls in.
Network security is one thing—and is an element controlled by any standard worth its salt—but radio security is a final consideration. “If you’re located in a populated area, remember that any housing structure could have considerable consumer box-store wireless,” cautions Becker. “You’ll need more selectivity on antenna design in this setting, and you’ll want to beam your own RF inward as much as possible, using directional technologies.”
The last word? Not for a long time
Wireless industrial and control networking is a reality, but has the technology reached maturity? There is no single answer. Radio technology is mature, of that there is no doubt. Spectrum and mesh management is a mix of old and new. One by one, production personnel come to experience wireless first-hand, and most become, if not out-and-out evangelists, at least converts. If industrial wireless follows the path of IT and consumer wireless, then we are on the edge of an explosively expanding production approach. But—just to inject a little chill of reality—manufacturing is not an area in which little glitches or nagging headaches can be long tolerated. To the extent that wireless devices can avoid these, they will flourish. Stay tuned.
>> Listen to Gary Mintchell’s podcast conversations with Dust Networks’s CTO Kris Pister at www.automationworld/view-3875 and Honeywell’s Jeff Becker at www.automationworld.com/view-3697
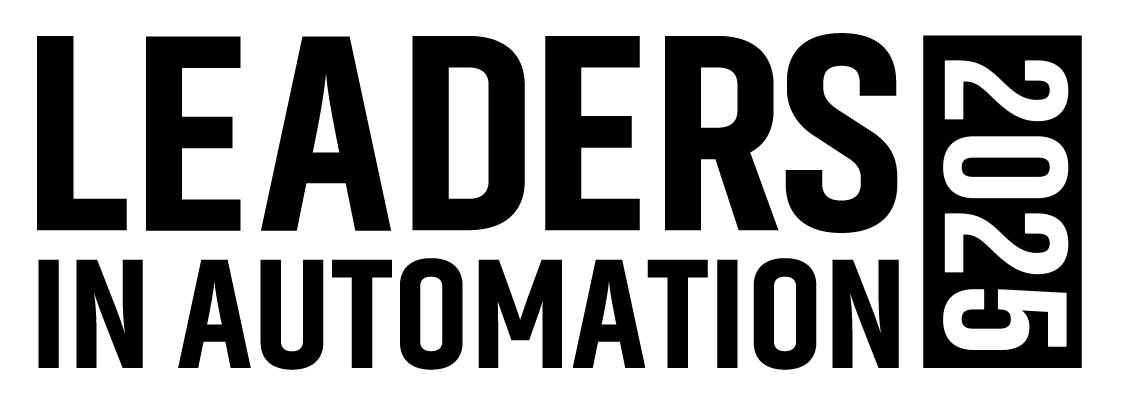
Leaders relevant to this article: