The time: the not-too-distant future.
The place: a General Motors
Corp. body shop, which is using intelligent robotics and flexible
manufacturing systems to turn out the latest GM vehicles.
Suddenly, the system sends an alarm to its human overseers: Based on real-time parameters that the body shop diagnostic system is monitoring, the system predicts that Robot 123 will fail in 10 minutes!
A GM engineer at a remote site springs into action. Using a 3D computer simulation that displays a complete and totally accurate “virtual” reproduction of what’s happening on the real-world body shop floor, the engineer reallocates the work being done by Robot 123 to another robot on the floor. Using the 3D virtual environment, he validates the change by simulating the new workflow.
Once he is confident that the second robot can handle the reassigned tasks, and that the change won’t cause problems elsewhere on the floor, the engineer clicks a button, causing operations in the real-world body shop to pause, while the new robot routine and associated program changes are downloaded to robot controllers, programmable logic controllers (PLCs) and other equipment on the plant floor. When the downloads are complete, the body shop resumes operations using the new routines, and a maintenance technician is sent to tend to the problem with the now-idled Robot 123.
All of this is accomplished in fewer than 10 minutes, avoiding the body shop downtime that would otherwise have been caused by Robot 123’s failure.
Vision chasing
That scenario—painted by Bob Tilove, laboratory group manager for virtual manufacturing research and development at the GM Technical Center, in Warren, Mich.—is not yet possible today. But it’s a vision that Tilove and his colleagues are working hard to make reality. And it is one potential manifestation of the so-called “digital factory,” or “digital manufacturing” technology that is attracting a growing amount of attention and excitement these days.
Digital manufacturing means different things to different people. But one major component of the technology is the class of 3D modeling and simulation tools that are used broadly in automotive and aerospace industries today to develop and validate control systems, robot work cells and production processes. It’s a small but growing category within the class of software products known collectively as product lifecycle management, or PLM.
“We are now able to completely and accurately simulate manufacturing processes in 3D. Once you get the simulation in place, you integrate the product design itself, you plunk it right down in the middle of this, and then you can actually validate that these manufacturing processes, the control systems, the robotic systems, the work cells and everything else actually work the way that you designed them,” explains Dick Slansky, senior analyst, at ARC Advisory Group Inc., Dedham, Mass. “And that’s this whole notion of virtual commissioning that is really resonating with manufacturers right now.”
There are two leading suppliers of these factory simulation and modeling tools. One is the French-based PLM supplier Dassault Systèmes, with its Delmia product line. The other is the former UGS Corp., with its Tecnomatix line of tools. UGS was acquired in a $3.5 billion deal last May by German-based Siemens AG, and is now known as Siemens PLM Software—a division of Siemens’ Automation and Drives Group, the world’s largest factory automation supplier.
The Siemens deal is driving a new level of anticipation in the digital manufacturing space. “When someone like Siemens comes in and says, ‘Hey, I’m going to make this part of my automation group, and we’re going to make sure that this technology is integrated,’ that makes a huge statement about the importance of this technology,” observes Ed Miller, president of CIMdata Inc., an Ann Arbor, Mich.-based research firm that follows the PLM market. “With Siemens, we’re talking about an organization that’s got the ear of the manufacturing floor already, and when they start talking about it, the world hears.”
In agreement is Alain Iung, vice president, Tecnomatix marketing, at Siemens PLM Software. “Today, many customers still don’t recognize the value of digital manufacturing,” notes Iung. “So this acquisition by Siemens actually changes the market space. People are starting to talk about digital manufacturing now, and we’re seeing a lot of excitement.”
Adding fuel to the fire was a joint announcement last December by Dassault and Rockwell Automation Inc., the Milwaukee-based automation heavyweight. The two companies said they have formed a partnership aimed at forging links between Dassault’s Delmia tools and Rockwell’s plant floor controls software. Dassault has signed earlier, similar partnerships with other factory controls vendors, including Omron and Schneider. But according to Patrick Michel, Dassault’s vice president for Delmia Solutions, Rockwell and Delmia software share a similar data structure that will “allow a higher level of collaboration with Rockwell” than with other controls vendors, at least initially. The first fruits of the Rockwell/Dassault link-up are anticipated by this summer.
Both the Siemens UGS acquisition and the Rockwell/Dassault partnership are expected to help accelerate a move toward tighter integration of the virtual world of product design and manufacturing planning with the physical world of plant floor automation and controls. The result, say proponents, will be major benefits for manufacturers, including lower engineering costs, reduced time to market and quality improvements.
Watch it double
Despite the relatively small size of the market for digital manufacturing products today, industry watchers believe that the increased attention to the technology will drive rapid growth. ARC puts the worldwide market for digital manufacturing software and services at about $479 million in 2006. “I think you might see that double in the next five years,” says Slansky.
Digital manufacturing revenues will definitely grow faster than more mature portions of the PLM market space, such as collaborative design tools, Slansky predicts. That category—which includes computer-aided design, manufacturing and engineering (CAD/CAM/CAE)—accounted for sales of about $4.4 billion in 2006, ARC figures show.
CIMdata is likewise projecting accelerating growth for digital manufacturing tools, with sales rising from about $436 million in 2006 to more than $1 billion in 2011. Among keys to that growth will be improved market education that will come with stepped-up promotion of the technology by the likes of Siemens and Rockwell, says Miller. “I suspect that if you went into the world of industry today and threw the term ‘digital manufacturing’ out to 100 people, a good five or six of them would be able to talk about it,” he observes. “It’s not something that the world knows about.”
To achieve widespread adoption, digital manufacturing will also have to become simpler to use, Miller adds. While he believes that the technology offers big potential for manufacturers of all sizes, it has gained the most traction to date among large automotive and aerospace companies for use in highly complex manufacturing environments. Miller notes that Dassault’s introduction last fall of Delmia PLM Express, a digital manufacturing suite aimed at small and mid-sized manufacturers, is a step in the right direction.
Organizational issues could also be a constraint. “I think the cultural barriers within longstanding manufacturing organizations have probably been the biggest impediment to adoption of digital manufacturing to date,” observes Jeff Hojlo, research analyst for PLM at AMR Research Inc., in Boston. “The silos of design and manufacturing still exist, and people who have been around manufacturing organizations for years just don’t see the need to connect the as-designed with the as-built.”
The learning curve required for manufacturing engineers to learn 3D simulation technology could also slow down adoption, many believe, not to mention the cost of the technology. While some level of CAD capability can be had today for less than $8,000 per seat, pricing for full-blown Delmia or Tecnomatix capability can go well into five figures per seat, vendors confirm. Pricing for Delmia Automation “can go all the way up to $100,000 per seat, if you take everything,” says Dassault’s Michel. But the lower level Delmia PLM Express package—which includes capabilities for workcell layout, robotics programming, ergonomic studies, assembly planning and virtual commissioning—is priced at around $15,000 to $20,000 per seat, he adds.
Startling savings
Whatever the price, there are indications from the field that the payoff from using digital manufacturing tools could be well worth the investment. Some large manufacturers report startling savings from use of the technology. In one application of “virtual commissioning,” for example, a BMW plant in Spartanburg, S.C.—by using Tecnomatix simulation tools—was able to reduce the time needed to commission control software for an automated chassis assembly operation; primary commissioning work was completed in a single day, compared to as many as eight days in previous comparable projects.
Likewise at the GM Tech Center, Stephan Biller, group manager for plant floor systems and controls, reports that the automaker has reaped big savings through a process that Biller calls “emulation for virtual validation of control logic.” The GM research team worked with the automaker’s manufacturing organization, Biller says, to develop the process using tools from both Delmia and Tecnomatix. Once a control system is designed, the GM process enables the virtual debugging of control logic in the lab prior to its actual deployment in a plant.
During a fall 2006 production launch at a GM plant in Lansing, Mich., the emulation process reduced the time needed for control logic debugging to around four to five hours, says Biller, compared to the three weeks typical in the past. As a result of that success, GM now plans to use the process on all future North American plant start-ups, as well as for others around the globe, Biller adds.
Similar improvements flow from modeling and simulation of mechanical systems, bothfor existing operations and for new plant or production line start-ups.
One automotive client of Waltonen Engineering Inc., a Warren, Mich.-based engineering services firm, for example, was able to eliminate a third shift at a production operation, while also improving quality, after Waltonen deployed a suite of Tecnomatix simulation and plant floor optimization tools to model the facility. The digital tools enabled the company to find and eliminate bottlenecks, resolve scheduling and buffering issues, and improve material flow to its assembly line, says Waltonen President Lloyd Brown. Further, the use of associated Tecnomatix quality and dimensional analysis tools enabled the company to trace and eliminate the sources of excess scrap in one portion of the plant, he adds.
The tools are equally valuable in shortening time-to-production for new lines and facilities, Brown notes. By following a strict process planning, design and engineering methodology that relies heavily on 3D modeling and simulation studies, Waltonen can verify key portions of a production line design along the way, while easily accommodating customer change orders during the process, he says. “We have a virtual build of the design before the first piece of steel is cut.”
The process is not only more efficient than previous manual methods, but significantly reduces errors and problems when the line is actually built. The result is “a nice quiet start-up,” as Waltonen Sales & Marketing Vice President Bryan Novach puts it. Indeed, Brown indicates, the process virtually eliminates design errors in the as-built line when compared to previous manual approaches. This significantly reduces debug time, and means the line can be up and running much more quickly than in the past. An additional bonus is the creation of an extensive digital library of eXtensible Markup Language (XML)-based features and objects that can be reused for subsequent production process designs, Novach points out.
But while savings at some companies have been notable to date, both the vendors and the big practitioners of digital manufacturing want more. And they are working on ways to forge tighter links between the virtual and physical worlds.
Dassault, through its partnership with Rockwell, provides one example. By developing links between Dassault’s Delmia Automation PLM software and Rockwell’s RSLogix 5000 control programming software, the two companies plan to provide a capability that Dassault’s Michel calls “virtual control design.” That process will go a step beyond today’s virtual commissioning capability, Michel says.
In virtual commissioning, a PLC or programmable automation controller (PAC) can be linked to a virtual mechanical environment through an open communications OPC connection. This enables debugging and validation that the two components will work together before a physical production system is built, Michel explains. “But that doesn’t change the way you write the controls,” he notes. “You have to wait until the controls are written and the virtual environment is defined. Only then can you plug the two together to check the end result.”
But in the partnership with Rockwell, “we are accelerating the development of the virtual environment and the controls by exchanging information beforehand, and not waiting until the end when something is ready to test,” Michel says. This is made possible by similar object-oriented data models used in both companies’ software, enabling bi-directional data exchange and synchronization of objects between the mechanical and control sides, he continues.
The capability will enable more collaborative design between mechanical and automation design engineers, says Rick Morse, software business manager for automation and simulation at Rockwell. “You can virtually commission and test what you’ve got anywhere along the way, because we have matching names and matching structures synchronized between the mechanical and the control sides,” Morse explains.
An initial utility product will be available this summer to provide the bi-directional linking between the two companies’ current software products, Morse says. Rockwell and Dassault will subsequently build the capability into future generations of their core products, he adds.
While Dassault and Rockwell have been publicly talking up the advantages of their partnership, Siemens PLM Software has provided fewer details about its integration plans.
In general, says Ziyon Amram, Siemens PLM vice president, manufacturing solutions, the company will invest in three areas involving integration of its PLM software with Siemens products—covering factory controls, manufacturing execution system (MES)/PLM integration, and links with other Siemens automation software. More specifically on the digital manufacturing side, the company announced an initiative called Project Archimedes last summer that is focusing on five specific areas: adaptive manufacturing, virtual commissioning, harmonizing lifecycles, hi-fi machining and mechatronics.
The company is partnering with manufacturing customers in each of these areas, and is also continuing on its Tecnomatix digital manufacturing road map that was in place prior to the Siemens acquisition, says Amram. And while a “formal road map” for tighter integration with Siemens technologies is not yet in place, it’s fair to say that the initiatives will not produce “big bang” results, but will lead to “intermediate deliveries” over a multi-year timeframe, he notes. Interested parties should watch Siemens PLM announcements at the Hanover Fair April 21-25, in Hanover, Germany, where additional information will be revealed, Amram adds.
Amram points out that Tecnomatix has had a relationship with Siemens since the late 1990s, even prior to its 2005 acquisition by UGS, so it is not as though the two companies are starting integration efforts from scratch. Like Dassault, Siemens PLM Software has a growing number of customers who are already using virtual commissioning, he says. And Siemens PLM intends further integration to provide digital manufacturing capabilities that go beyond the pre-production uses of virtual commissioning. “At the end of the day, our goal is to enable an environment that would proceed into production as well,” Amram says. The vision involves “true integration” between the virtual and physical worlds, with a single source of data to provide “visibility throughout the manufacturing cycle.”
To view the accompanying sidebar to this article, go to www.automationworld.com/view-4107
To download or listen to a podcast interview with ARC's Dick Slansky about digital manufacturing, visit www.automationworld.com/view-4037
Companies in this Article
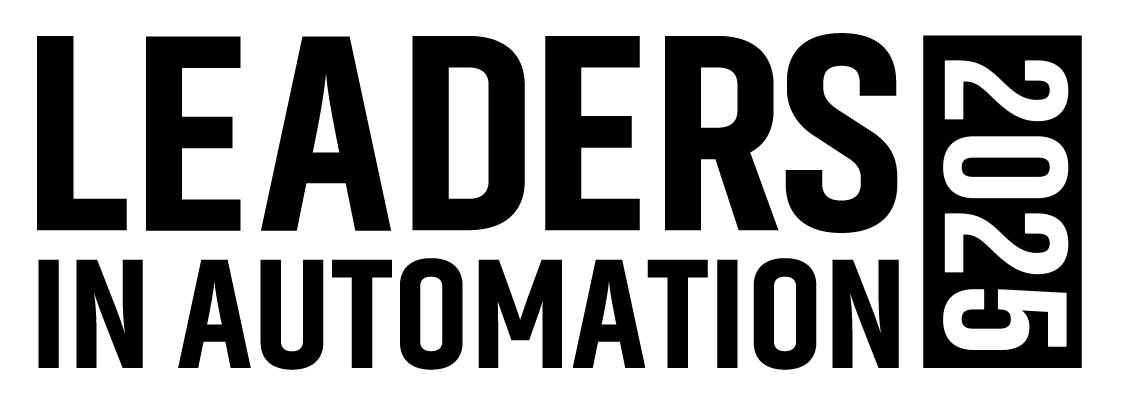
Leaders relevant to this article: