Few topics raise the hackle feathers of political emotions as much as talk of “global warming” or “green.” Some people are passionate about conservation. Others are suspicious of an anti-business, liberal conspiracy. Putting aside politics, what companies are discovering is that they can be sensitive to the environment, earn credibility with the public for being good citizens and improve the bottom line—all at the same time.
People who have been implementing energy savings projects have discovered that no stone should be left unturned while looking for likely candidates for projects. Machine and process operations are often a good place to start. But the heating, ventilation and air conditioning (HVAC) systems can be a gold mine of cost savings, too.
Puzzlingly slow
One thing that puzzles many observers, though, is that with all the technologies developed during the past 15 years and the resulting publicity, why has adoption of energy-saving technologies been so slow. John Malinowski, motors product manager at Baldor Electric Co., an electric motor manufacturer based in Fort Smith, Ark., says that a big part of the problem is the way people are rewarded for job performance. For example, he says, of the total cost of an electric motor over its life, only about 3 percent is the original purchase cost. Upwards of 97 percent of the cost is the amount of electricity it will draw. The purchasing agent is not graded on this major part of the cost, however, but rather on just the original purchase price. It would take an executive level decision to change the system and make energy cost reduction a part of everyone’s job description.
Dan Cheung is senior process control engineer at Domtar, a pulp mill located in Kamloops, British Columbia, Canada. In one process, the mill burns calcium carbonate to make calcium oxide in a lime kiln with a capacity of 400 tons per day. “We were using 8.5 gigajoules per ton of energy on the system,” says Cheung. An industry benchmark survey showed the usual rate to be 7.3 to 7.4 gigajoules. He decided that action must be taken.
“We hired an energy auditor who checked out the conditions of the instrumentation and process and came up with a report that said an energy savings project was doable. In fact, they conservatively estimated that we could get down to 7.4 or 7.5 gigajoules. That would mean almost a million dollars per year savings potential. The three- to four-month payback was very attractive, so we proceeded,” Cheung says.
Working with Norpac Controls, a distributor of Emerson Process Management control products in Vancouver, British Columbia, Cheung initiated a project to implement model predictive control from Emerson on the mill’s existing Emerson Delta V control system. In addition to the software, Cheung also used this time to check and calibrate all the instrumentation. The resulting improvements were huge. “It is very cold today,” Cheung says, “yet, we are still burning at a rate of 7.2 gigajoules per ton. In fact, once the process stabilized, we found we could increase production by about 10 percent while still cutting the energy usage rate. These are very, very, very impressive results. It makes me look like a hero.”
Measure to control
Joel Shapiro, group manager for measurement and control at vendor National Instruments (NI), in Austin, Texas, says, “One thing that comes up in meetings with customers is that once people understand what they have, it helps them understand where to start. I just read a quote in “The Economist” regarding energy and greenhouse gas emissions that went something like, ‘If you start to measure, people start to reduce.’ We enable the measurement.”
NI customer Nucor Steel uses National Instruments’ CompactRIO programmable automation controller and FieldPoint input/output modules, along with NI’s LabView software, to reduce expenses running a furnace that melts scrap steel at its Marion, Ohio, plant.
Electrical Engineer Dave Brandt says a detailed economic justification in this case wasn’t much of an issue, because the cost of the NI solution was low. The system implementation began with a scrap weighing system. This piece of automation fed into process information. Knowing the amount of scrap steel going into the furnace meant that the amount of lime and other materials added to the mix would be more accurate. Further, energy input to the furnace could be better controlled so that operators don’t overmelt the steel. All of this adds up to fewer “pourbacks” to get the steel chemistry to the point that it will meet specification. “We didn’t have baseline data on energy costs to see savings,” says Brandt, “but we have dramatically reduced pourbacks—down to just 10 last year out of 6,000 pours. This adds up to significant gains in productivity.”
Sometimes, the documentation and data acquisition required go beyond production data. Taking the idea to the next level is a South African company involved in mining, energy, chemicals and synthetic fuels. Sasol, originally the South African Coal, Oil & Gas Corp., in Sasolburg, South Africa, worked with consultants from Invensys Process Systems, a Foxboro, Mass., supplier of process control and performance management products, to define measurements and how to use the information in order to not only improve the energy usage of its boilers and reduce overall electric consumption, but also to prove to accounting that the savings were real.
Doing it better
Russ Barr, director of the Performance Measurement Group, a consulting arm of Invensys Process Systems, says, “Sasol embraced the whole idea of, ‘We can do it better.’ They are striving to achieve operational excellence from the operations side, integrating performance measurements from a business perspective with financial measures. Problem was, financial measurements were released on a monthly basis—far too late to be useful for real-time operations decisions. So we helped them develop algorithms to start to bring together the disciplines.
When we made improvements, both operations and finance could agree from the information in their dashboards that the improvements were valid. It is absolutely the key that everyone’s dashboards, including operators, includes financial measures.”
Sasol achieved a 6 percent savings on energy feedstocks and a 4 percent savings on electricity costs the first month after implementation. Subsequent monthly results showed progressively better savings. More consistent operation from a business perspective led to approximately a $230,000 savings in just the first month.
Many commercial boilers that provide heat to schools, plants, commercial buildings and other large facilities consume a lot of energy. Says Steve Connor, director of marketing for Cleaver Brooks, a Milwaukee-based manufacturer of such boilers, “Boiler fuel consumes an ever increasing share of the cost of operation. Now, with oil procurement issues, rising costs and customer concerns about the effluent from the exhaust stack, we used the obsolescence of our burner control system to search for a way to upgrade to the 21st Century to achieve the goals of improved efficiency and reduced emissions. We didn’t have sufficient in-house controls expertise, so we had to find a partner. After a search, Rockwell Automation came out as someone who could help us.”
Cleaver Brooks engineers felt that using a programmable automation controller, such as the Allen-Bradley CompactLogix from Milwaukee-based supplier Rockwell Automation Inc., would give its customers more flexibility than a custom microcontroller. Rockwell engineers helped CB develop the control system. “That’s how the Hawk ICS was born,” reports Connor, in reference to the new boiler control. And the controller platform is used not only for burner management, but also for positioning, fuel/air actuators for optimum combustion efficiency, and automated damper control, so that when the boiler is off line, ambient air is not pulled into the system. Allen-Bradley variable frequency drives are networked to the system to control the combustion fan so that the motor is not using full horsepower against a closed damper.
“It’s great to be green, but there must be a financial return for the customer,” concludes Connor. “Customers are aware of the problems in the Middle East with oil supply, and they are concerned with pollution and their carbon footprint. But higher efficiency is still the primary selling point.”
Saving 20 percent
How would you like to shave 20 percent from your energy cost per product manufactured and increase productivity at the same time? SEW-Eurodrive is a manufacturer of variable frequency drives and gear motors. This German company has its headquarters and principal U.S. manufacturing facility in Lyman, S.C. Managers at the plant are always looking for ways to reduce the costs of energy, materials and waste. Plant Manager Carl Hinze and Assistant Plant Manager and Head of Maintenance Chuck Chandler have assembled an impressive list of accomplishments in their program. Along the way, they have reduced the energy cost per part manufactured by 20 percent over three years.
Sometimes, justifying the upfront investment in these projects is hard to get buy-off from the finance department. “We’re a privately held company, so we don’t have to justify expenditures to the board. If it makes sense, we do it,” Hinze says. “We’ll study a problem and proposed solutions. Then we’ll try out a pilot project just to make sure it isn’t just ‘salesman talk.’ We just tried out new lamps in our lighting fixtures in the plant. If it works in the entire plant like it did in the pilot, we stand to save almost $33,000 a year.”
The plant recycles all possible manufacturing waste. This not only reduces landfill costs, but sometimes adds a little income. Items recycled in one way or another include wood pallets, cardboard, computer equipment and metal chips from the machining processes. Hinze and Chandler also turned a critical eye to manufacturing processes. In one operation, by changing from grinding to hard turning, they cut the cycle time in half, reducing electricity consumption and increasing productivity. Going from electric heat to natural gas reduced cost on the carburization process. When the price of natural gas went up, they purchased regeneration U-tubes to cycle waste heat back into the system to reduce consumption. Automating the cooling system with variable frequency drives allowed them to shut off pumps when there was no demand.
Chandler concludes, “We’re constantly looking for ways to reduce energy costs. Our owner is concerned with environmental protection and recycling, so it’s just a company mindset. Sometimes it’s hard to do a project, but we do it when it makes sense.”
The many reasons for increasing energy efficiency and thereby reducing consumption include numerous environmental and social goals, but reducing expenses still ranks as number one when businesses and other entities look at the situation. Another example of reducing electrical energy consumption lies outside the walls of a manufacturing plant—it’s the invisible workings of a municipal swimming pool. Municipalities are large energy users from water and wastewater treatment to facilities. The pumps that keep water for swimming fresh and clean are another source of energy use—and expense.
Swimming in costs
Tim Friend, plant supervisor of the South Windsor, Conn., community swimming pool complex was keenly aware of the operating expense of running a 10 horsepower, a 20 horsepower and two 30 horsepower pumps used in cleaning the million-plus gallons of water contained in the facility’s three pools. The water must be constantly pumped through a series of filters 24 hours per day, every day in season. The pumps previously operated at full horsepower constantly.
“We wanted to lower our high power bills,” says Friend. “We knew we were wasting energy via running the pumps at full power—especially after hours. Fewer impurities are in the water when nobody is swimming, so by slowing the flow at night, we knew we could still maintain adequate filtration in the pool and the same levels of water quality.”
So, Friend consulted with Brian Robinson, a sales engineer with FlowTech Inc., a South Windsor, distributor of ABB products who had assisted on previous projects in the water treatment plant. They evaluated the impact that implementation of ABB variable frequency drives would have on the problem.
After installation, the pump speeds were set back using the on-board time clocks that initivisitate pre-programmed, pre-set speeds in the VFDs. Pumps were programmed to run at 90 percent power during open-pool hours, and to ramp down to 60 percent for 12 hours each night after pool close. These settings were anticipated to yield an energy consumption reduction of more than 65,000 kilowatt-hours (kWh) per season—and save the pool more than $7,000 in operational cost annually.
To view the accompanying sidebar article to this story, "How to Get Management Approval", go to www.automationworld.com/view-4000.
Companies in this Article
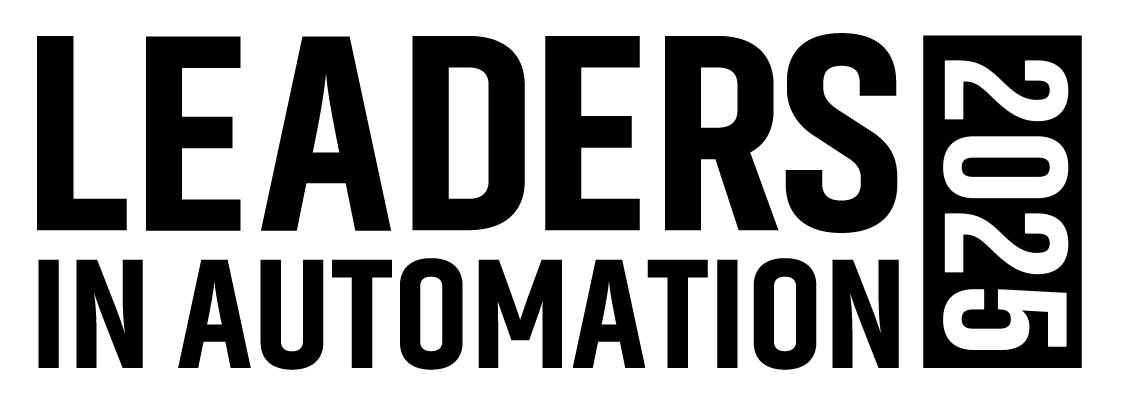
Leaders relevant to this article: