Are you broadcasting your automation from a station near you? If you are already using wireless, you have already plunged into the basics. But even if you are not currently a wireless maven, you are at least well aware that the topic is very much in the air—pun intended.
Is the technology new? Short answer: no, this is radio. Radio is a technology that has been in development since the 1890s. Hundreds of thousands of electrical engineers, ordinary people, even composers and movie stars have contributed millions of refinements to radio since its infancy. For example, in August 1942, Hollywood beauty Hedwig Kiesler Markey (Hedy Lamarr) and avant-garde composer George Antheil published an early U.S. patent describing frequency-hopping, spread spectrum technology. And the same basic technology—manipulation and harvesting of electromagnetic waves—is behind our cell phones, microwave ovens, radio controlled toys, radar, television and, of course, AM, FM and digital broadcast radio. Bottom line, regardless of the noise and the proliferation of terminology, wireless automation is radio.
Further, while discussion of wireless automation seems to quickly soar into the complex worlds of controller and enterprise networking, the radio itself is just the delivery vehicle. The electromagnetic pulses broadcast by a transmitter and harvested by a receiver are conceptually the same as the high-and-low electron flows sent via cables and circuit board traces in land-based systems. Granted, the type of radio governs how many pulses can be reaped in a given millisecond—and how the electromagnetic waves behave in earth’s atmosphere—but when you come down to it, wireless automation is about sending ones and zeros.
Having said that, there are, in fact, complexities in the details. Wireless solutions differ depending on application. And here, as in every other aspect of automation, vendors seek ways to differentiate their offerings, so there are features to sort out. For the most part, however, the technologies involved in radio are well-established, and perhaps more importantly, the radio world has been standards-based almost from the start. Most of radio’s standards are around the two interrelated facets of its world: the clearest possible reception of a signal and best practices for the prevention of interference.
The term “wireless” captures 95 percent of its benefit: it provides communications without wires. Festoons, slip rings, sliding contacts, conduit, wire runs (and, of course digging through wood, plasterboard and concrete)—all these and more recede into the background when you use wireless technologies.
Unfortunately, when you begin thinking wireless in automation, the biggest challenges are, one, so much has been accomplished on so many facets, and, two, every detail of radio technology has accumulated details as this or that wrinkle has been ironed out. There are a number of interrelated concepts—for example, wavelength vs. data rates vs. interference (short form: the longer the wave, the less problem with walls and trees, but the less data per second—of course, with dozens of provisos and qualifications).
For those plunging into wireless for the first time, the most significant source of anxiety is likely to be the alphabet soup—or, better, alphanumeric soup—of radio nomenclature. Some of the descriptors indicate the frequency band used for transmission (for example, 900 MHz or 2.4 GHz—that’s megahertz and gigahertz, for the uninitiated); some pinpoint the transmission and reception technologies (for example, frequency-hopping spread spectrum). Some are standards-based (e.g., IEEE 802.11x, in reference to a common wireless standard from the Institute of Electrical and Electronics Engineeers). Some of the terminology derives from a related sensor or controls protocol (for example, Wireless Hart), some from the computer consumer world (Wi-Fi, short for Wireless Fidelity) or computer networking (wireless Ethernet). Finally, some terms have even joined the soup from application domains (e.g., wireless SCADA, for supervisory control and data acquisition).
Thus, almost every radio component will have a profusion of headings in its specification sheet: a standards moniker (e.g., IEEE 802.15.4), what we might call the street name (e.g., Wi-Fi), network reach (e.g., WLAN or WWAN, for wireless local area network or wide area network), automation moniker (e.g., DeviceNet), and so on. The Wireless Landscape diagram at right, provided by the Instrumentation, Systems and Automation Society (ISA) helps bring this confusion under control.
There are a couple of take-aways implicit in the diagram. First, there is a useful convergence of low-power usage, low cost, and low data rates embodied in the IEEE 802.15.4 standard. ZigBee and the soon-to-be-released WirelessHart equipment are found here. The low data rate is ideal for monitoring sensor setpoints and triggering actuators with requirements for momentary or relatively sporadic control. Many of the radios involved can run for years on a single set of drugstore batteries, and many feature built-in self-healing connectivity that monitors and routes signals around glitches between transmission and reception. Interest in wireless for these kinds of applications is growing rapidly, for reasons covered in “Wireless Links Railcars into Croda’s Sensor Network” (see p. 52)—the technology allows direct tracking of often-critical values, even for assets located far from a plant’s wiring.
Second, the dramatic adoption of IEEE 802.11n Wi-Fi devices by corporate information technology (IT) and retail consumers—devices that were developed for Internet TCP/IP (transmission control protocol/Internet protocol) protocols running on Ethernet—has paved the way for the development of wireless Industrial Ethernet devices employing this standard. These benefit from the mainstream nature of device design, with its chip-based, economic circuitry, with enhancements for ruggedness and reliability. Wi-Fi-related components are especially welcome where manufacturing and IT work closely together—any given IT infrastructure, if it is not positively standardized on Ethernet, at least contains gateways that provide an instant conduit to Ethernet.
Finally, although it is not obvious in the graphic, the continuum of standards and technologies has spawned the development of gateways that translate nearly every kind of device input and output into nearly any other kind. This is not to downplay the engineering involved: the effort that goes into a reliable, seamless real-time gateway is immense. But because industrial markets increasingly pressure vendors to make their offerings compatible out of the box, the era of disparate, proprietary, standards-ignorant equipment is at last winding down. As Kevin Romer, application engineer for the Industrial Automation Group of automation vendor Advantech Corp., in Cincinnati, says, “The trend today is to convert older technologies to Ethernet, rather than from one proprietary technology to another.” Advantech has long been active in personal computer (PC)- and Ethernet-based automation.
Other than the cool factor—radios are fun—the key benefit is savings in installation costs, time and labor, because going wireless deletes both the costs of cables and the costs of routing them. Beyond this, the purchase price of radio components is low compared to most automation products, because so much of the technology can be driven with high-quantity, low-cost chips. Further, in most instances, the time needed to bring a new wireless unit online is far less than that needed to install a wired device. And there is what we might call a geographic side. Wireless especially enables connectivity when there are challenges to running wires, such as to cranes and remote assets, or to equipment in which movement and/or vibration cause too much wear in umbilical wiring, slip rings or contacts.
Wireless can allow you to reach into new areas of the plant, places where wire could never go, enabling new flexibility in system configuration.
This is not to say that wireless will make your life free from anxiety. There are issues. In order of importance, these are reliability, security and throughput (including latency). For many, security and reliability are tied for first place; for most, the edge goes to signal reliability. There are times and situations under which any radio transmission can be interrupted or degraded (exactly when will differ, depending on broadcast technology and protocol). Skipping a beat is not an option in manufacturing, so you must adopt tactics to ensure 100 percent reliability, either through redundancy or such solutions as mesh or self-healing networks.
Potential headaches around latency and throughput are application-dependent, with some being computer/controls network dependent, not strictly radio network dependent. For example, standard Ethernet can fall short in manufacturing because vanilla Ethernet is non-deterministic. That is, Ethernet focuses on the (eventual) delivery of relatively large amounts of usable (if not perfect) throughput, at the cost of time lost to re-transmitting colliding or fragmented data.
This is clearly a problem if you must have millisecond control over a machine. On the other hand, it is not a problem if, once an hour, you are transmitting aggregated data up to an enterprise system, where a minor delay is not an issue. Various more deterministic, real-time flavors known collectively as industrial Ethernet, of course, seek to address this problem.
If you have decided that you want to use a radio to send your data somewhere, planning is paramount—hardly a new concept. The problem really needs to be taken apart and analyzed. At the heart of the dilemma is that almost any radio technology, on any broadcast wavelength, using any protocol, could be used for almost any automation task. That said, each technology, band and protocol has its own strengths and weaknesses, some highly relevant to applications and environments (for example, the ability of longer wavelengths to penetrate walls, foliage and the like). Many have their own history in relation to information technology standards (for example, the Ethernet-grounded Wi-Fi family) or to point-to-point sensor automation (for example, Zigbee or WirelessHart). Over time, the field of choices here, as in so many technical areas, will only grow.
Taking into consideration both the application-dependent strengths and weaknesses of various wireless offerings is clearly crucial. This planning is necessarily multi-disciplinary.
Obviously, a team approach is required, and Automation World will be exploring this and other considerations in a series of articles focusing on wireless this year. Conceptually, however, the exercise is not much different than any project that impacts the topology of a network or controls strategy—of course, with the injection of some radio expertise into the mix.
The key is to over-design the system—provide more security than you think is necessary and place radios and choose antennas to put radio frequency (RF) power where you need it. High gain and directional antennas are often the right choice.
Kevin Zamzow, business development manager at vendor ProSoft Technology Inc., in Bakersfield, Calif., suggests, “Work with rifles, not shotguns. You gain reliability by ensuring the strongest possible signals and using directional radio technology where you can. Radios are constantly increasing in speed, and equipment is increasingly able to use available bandwidth and signal strengths, so equipment trends are favorable.” Zamzow is an advocate (as are many others) of full RF audits, even when employing self-organizing networks: “You need to find the feasible distances at your plant for line-of-sight technologies. What’s feasible for the ultra-high-frequency radios that can penetrate walls and foliage? Where do you need repeaters? It’s important to pin down where there are any shortfalls, and find solutions for them.”
Interestingly, vendors interviewed for this article expressed a spectrum of opinions as to the current state of wireless automation. Some see wireless as just moving into the automation mainstream. Others, defining the domain as widely as possible (thus including radio frequency identification, or RFID, radio-based SCADA and other, older technologies), feel that wireless usage is already widespread. At least the technology is, for the most part, well-established.
The future of wireless in automation runs the gamut from new things in the low bandwidth range (for example, forthcoming equipment built to the WirelessHart specifications) to emerging broadband realms such as WiMax and ultra-wideband (UWB). WirelessHart builds on international standards, including the Hart protocol (IEC 61158 from the International Electrotechnical Commission), EDDL (IEC 61804-3), IEEE 802.15.4 radio, and frequency hopping, spread spectrum and mesh networking technologies. WiMax and UWB are still settling out, but hold promise for applications that require the highest speeds and data rates.
Cliff Whitehead, manager of strategic applications for Milwaukee-based automation vendor Rockwell Automation Inc., put it this way: “The best approach is to take an outside-in view—that is, don’t focus inside the labs on research and development, but on how people really want to use the technology. We haven’t begun to think of all the uses for wireless automation.”
For more information, search keyword “wireless” at www.automationworld.com.
Sponsored Recommendations
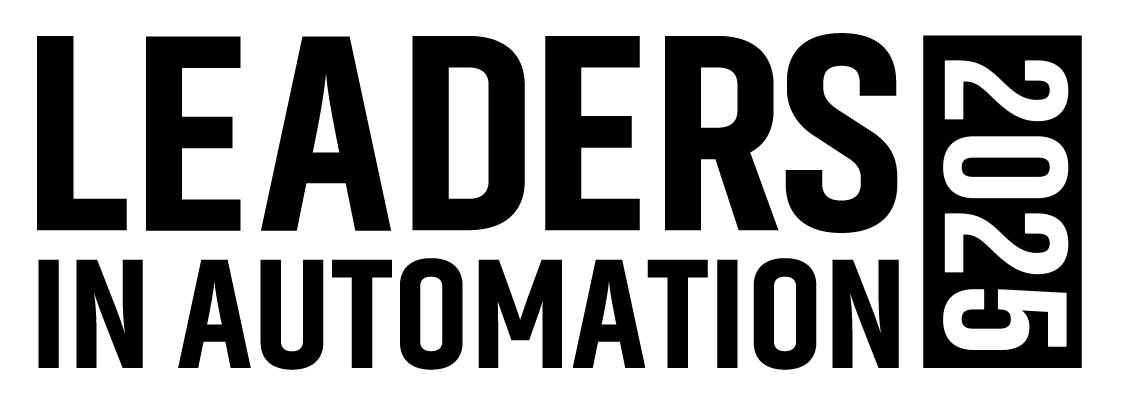
Leaders relevant to this article: