But Chris Van Sambeek took it on and met it. Van Sambeek is a control systems engineer at Appleton Papers Inc., a diversified paper manufacturer based in Appleton, Wis. He was involved with upgrading and re-instrumenting a large paper-coating machine when management asked if there was a way to tap into diagnostic information in the various field devices on the machine to improve reliability, and, as a bonus, to provide accurate information to support the company’s ISO 14001 certification process.
Though challenges remain for connecting assets to information, engineers automating asset management systems have boosted plant profitability—and even helped increase sales.
“The machine is controlled by a PLC (programmable logic controller) with connections to more than 100 Hart devices,” says Van Sambeek. “I pull out the Hart data through the backplane via a multiplexer before it enters the control system. I investigated a fieldbus, but we already had Hart hard-wired into the system. We weren’t pulling live data from the existing MicroMotion devices—merely using it just for configuration. With the project, we saw there was a great benefit from pulling information for the new system.”
Typical of most U.S.-based manufacturers, Appleton faces a lot of overseas competition. In this business, customers drive machine upgrades when they change the specifications of what they want. Engineers at Appleton have to design ways to meet the specs, as well as figuring out ways to drive down costs. Van Sambeek describes the installation, “It was pretty much a straightforward installation. We did lots of legwork verifying the network interface cards from Spectrum Controls and the software ahead of time. There was considerable cost savings with only one twisted pair cable to get the information rather than the usual multiple conductors. You do have to watch your shielding for electrical noise, but it’s no problem for someone knowledgeable with instrumentation and 4-20 milliAmp wiring. You do have to make sure that your application software is compatible with the personal computer’s operating system and up-to-date.”
Appleton uses the Asset Management Suite from Emerson Process Management, an Austin, Texas, process automation supplier, as an integral part of its ISO 14001 documentation program. ISO 14001 is an environmental management system standard promulgated by the International Organization for Standardization.
“We used to document all device calibrations by hand in big books,” Van Sambeek says. “What we needed was a way to combine all the information in such a way that a technician coming in at night who might not be familiar with the instrument can find all necessary information to perform his maintenance or troubleshooting duties. We use the data logger for event documentation, as well. The keystroke logging gives us a history of who did what and when. We also can dump the device configurations into mobile terminals to download to the instrument.”
The net result for Appleton was a $25,000 savings on wiring costs for the project. It also cut the number of man-hours required for instrument documentation in half. Calibration and configuration costs were cut by 50 percent to 75 percent. The alarm management feature reduced downtime by providing better information and filtering non-essential alarms.
Watch energy use
Observing a manufacturing operation with an eye toward reducing cost and inefficiencies can result in projects covering all manner of systems, machines and processes. One topic especially high on every manager’s list concerns energy. With rising oil prices driving higher electricity costs, this suddenly becomes an area in which “real money” can be saved.
John Hillencamp, a Knoxville, Tenn.-based sales representative for automation vendor Yokogawa Electric Corp., has an automotive manufacturing company customer that was looking at ways to do just that. “My customer wanted to get a handle on its energy costs and narrow down the costs per line per device to make sure it’s profitable.”
Hillencamp installed a Yokogawa MW100 data acquisition/data logger system with panel-mounted power and energy meter that integrates all of the measuring functions required for power management. The system included a Yokogawa PR300 power meter system that also features connection via Ethernet to a local area network that enables centralized monitoring of power usage and demand.
“The customers love a Web browser interface, and the MW100 comes with a built-in Web server,” notes Hillencamp. “I did the whole project in-house. The built-in Web server has pre-built screens that are very easy to integrate. We look at water, nitrogen, compressed air, temperature, humidity—anything that can affect soldering machines. Where information previously went only to the facilities department, now cell supervisors can call up the system and see if there is a problem. For example, they can look at adjusting air pressure or see other ways to cut operating costs and boost quality.”
The system has been only recently installed, so payback calculations are incomplete. But the low cost of installation and increased information available to operations staff has given management a reason for confidence.
Asset management has typically been the purview of maintenance departments. These are the people charged with assuring asset availability. As the last example showed, operations personnel also stand to gain from asset management implementations. Whereas operations are seen as the “money-making” part of manufacturing, maintenance is often seen as a cost center. This can lead to interdepartmental bickering. Forward-thinking managers are searching for ways to get both arms of manufacturing in the same game.
Scott Teerlinck, global business manager of plant services business at automation supplier Rockwell Automation Inc., in Milwaukee, says he’s seen a trend toward “strategic maintenance.” This strategy tries to turn maintenance from a cost center into a competitive advantage. “New products in this area are giving customers better response to disaster recovery and faster troubleshooting. They track user actions in order to help find the root cause of problems and to support regulatory compliance,” he reports. “The future lies in taking an enterprise view of maintenance and asset management. Some companies are starting to look at virtual storerooms across geographical boundaries. We’re working with a company that manages five storerooms as one. Companies are also trying to capture maintenance decisions in order to quantify them and determine their impact on the bottom line.”
Filling bottles
One user of Rockwell’s support services is Tony Yanora, operations manager for the Pepsi Bottling Group, in Columbia, Md. At his last post at the company’s Detroit plant, he faced the problem that people at all fast-growing manufacturing plants eventually face—continual addition of new equipment results in a multitude of types and brands of components.
In Yanora’s case, the problem showed itself in the complexity of stocking and replacing sensors and variable frequency drives. Not only was the problem one of maintaining a large stock of parts, with all the costs involved, but technicians also took extra time to find the correct sensor, read the instructions about how this particular one was installed and then complete the repair. Similarly, although all of the drives were the same brand—Allen-Bradley —there were too many in stock.
“We had something like 20 to 30 brands of sensors from different vendors,” Yanora relates. “We needed to standardize to make repairs more quickly and reduce downtime. So, we called in Rockwell Automation to do an installed base evaluation. As part of the agreement, Rockwell goes through all the panels and bottling lines to identify all the components—sensors, drives, motors, controllers. We evaluated their report, then signed a parts management agreement with them. They evaluated all the parts and, after we standardized on Rockwell sensors, worked up a cross-reference to move all the other vendors’ parts to the Rockwell equivalent. This move reduced our inventory in the maintenance storeroom. In the three years that we have been in this program, line efficiency has increased by 8 percent.”
Part of the Rockwell program included constructing a matrix of sensor types and training all maintenance personnel on it. This part of the program by itself improved maintenance efficiency. A Rockwell engineer still visits the plant one day per month to check things out and provide training and troubleshooting tips.
The program didn’t stop with sensors. Previously, Pepsi stocked 2 horsepower and 3 horsepower drives. Now, it has standardized on 5 horsepower. These drives will run the smaller motors, so inventory could be reduced while the line is still served. Yanora says that the storeroom in Detroit has become so efficient that it recently saved another plant in Burnsville, Minn., a long downtime waiting for a drive. That plant had a 30 horsepower drive go down, and the lead time to obtain a new one was two weeks. The plant was able to obtain one from Detroit overnight. “We became a quick turnaround warehouse for the other Pepsi Bottling plants,” says Yanora.
Utilities are another set of manufacturing companies that make use of asset information in order to provide better uptime for their operations clients. But the utility business model allows for even greater impact on the company’s financial performance, as this story from DTE Energy Co. shows.
Engineers at the Performance Center at DTE Energy, a Detroit utility, were looking for a way to provide comprehensive information not only for operators trying to maximize the productivity and reliability of plant assets, but also for the merchants who buy and sell energy so they can provide the most accurate bids possible.
John Kapron, DTE senior technological specialist, says, “We built a technology framework that includes asset management reliability information and uses technology from Matrikon to connect multiple data sources and relate them to our Hierarchical System Index (HSI) in order to calculate process cost and asset health.” Matrikon Inc. is a technology supplier located in Edmonton, Alberta, Canada.
“The HSI is a way to organize things in the plant,” explains Sumanth Makunur, DTE lead engineer. “For example, our company has six power plants. Each plant has units; each unit has primary systems; each primary system has secondary systems and equipment. We constructed a hierarchical model to explain these systems and map all of our data sources to the model. All the plants have the same descriptions of systems so that we are always measuring apples to apples.”
Connectivity tools
The system uses many connectivity tools. Matrikon’s product uses OPC, an open connectivity standard. Other connectivity components talk OLEDB (for Object Linking and Embedding, Database). The system has a metadatabase. “Users of the system are anyone in power generation. We have no restrictions on what anyone within the company can see,” says Makunur. “But various people all have specific responsibilities for different areas,” he adds. “System owners have responsibility for their own systems. They can navigate through the Hierarchy and find their information. Some engineers may have fleetwide system information needs. The Performance Center monitors all the plants and works with the merchants to tie us to the market to offer the most accurate bids.”
Kapron notes that the framework is in place with many components in operation now. DTE Energy has been working on this already for the past four to five years. A proof of concept worked, and now that people have confidence in the system, key systems are expected to be done by the end of 2008. “The key benefits,” says Kapron, “include the ability to monitor market performance that has helped the bidding process for selling electricity.”
Asset management technologies work not only for various types of manufacturing plants, but they add value for original equipment manufacturers and distributors too. Charlotte, N.C.-based J&H Machine Tools Inc. not only distributes computer numerical control (CNC) and metrology equipment from Mori Seiki, Zeiss, United Grinding Technologies and Star but also designs manufacturing cells for its customers and contracts for proactive maintenance and repair. Since October 1999, J&H has been live on IFS Applications, and this enterprise environment enables many of the value-added services that have allowed the company to grow in an increasingly competitive market. IFS AB is a Swedish supplier of enterprise application software with North American headquarters in Schaumburg, Ill.
According to J&H Information Systems Supervisor Robby Johnson, the ability to easily configure complex production lines for customers to achieve specific end-product results—and use that configuration to drive orders of the correct machine tools—drives efficiencies from the sales process into accounting and beyond.
Apart from a consultative selling approach bolstered by the rules-based configurator, J&H distinguishes itself through proactive service management, using IFS Applications to deliver enterprise asset management thinking to its customers. “The service management piece was a big reason we went with IFS,” Johnson says. Immediately after machinery is delivered to a customer, J&H personnel use IFS Applications to track activity associated with that machine, and leverage the information to improve service and uptime. “When a machine is ordered and it is delivered, that machine is entered into IFS for that customer as a functional object,” Johnson explains. “When the machine is installed, a work order is created and tied into that functional object. We have people who man a phone line and when they start a work order, that is entered in, and then, if necessary, a service tech is sent out and their time is tied into that work order.”
Data in the service management tool delivers value long after service is performed. “It gives us a way to track what is going on with that machine,” Johnson says. “Our phone techs can see closed work orders on a machine. They can also see what has gone on with similar machines—what has been done to solve that problem. Prior to this knowledge base, we did not have a way to see how much a customer had spent on a certain machine.”
Getting information into an asset management system is crucial to its success. Moin Shaikh, marketing manager for asset management at automation supplier Siemens Energy & Automation Inc., in Spring House, Pa., says, “Networking technologies are essential to an optimized asset management system. Therefore, when we talk about asset management, we take a holistic view of all production assets—any diagnostics that can help users be more effective and reduce downtime. We’re trying to expand information beyond equipment and trying to incorporate the process side of things.
Regardless of the manufacturing challenge, tools exist to help managers get the most from their assets.
For an informative Webcast on enhancing production performance, visit www.automationworld.com/view-3133.
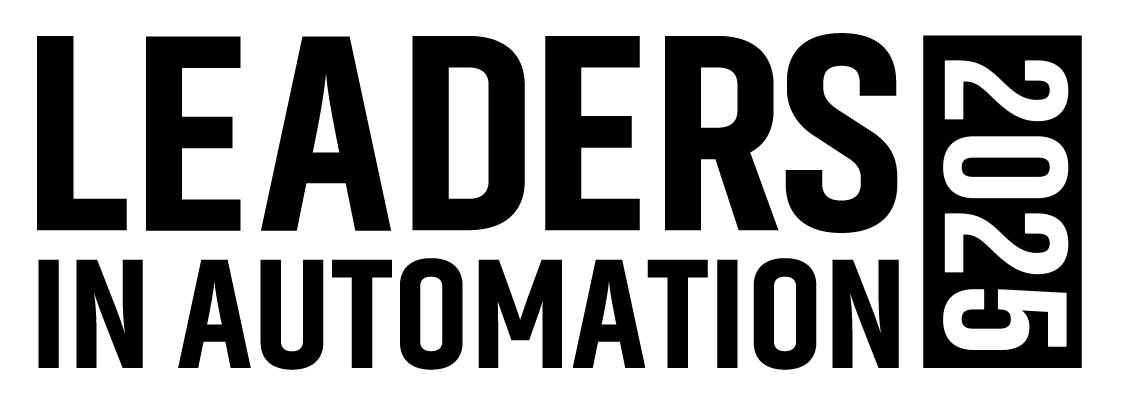
Leaders relevant to this article: