Distributed Control Systems Vendors Respond to PAC Questions
Jan. 21, 2008
We received four responses, from executives at ABB, Emerson Process Management, Honeywell Process Solutions and Yokogawa Electric Corp. Below is a portion of the text of an e-mail message sent by Automation World Managing Editor Wes Iversen to each of the companies, followed by the responses we received:"I am looking for some input for a feature story I am putting together for the February issue of Automation World on programmable automation controllers, or PACs.The PAC term, as originally defined by ARC Advisory Group in 2002, described a new kind of controller that would eventually replace PLCs. ARC defined various characteristics for PACs, including multi-domain functionality—the ability to handle logic, motion and process control, among other functions—all on a single control platform. As part of my research for this story, I have comments from several of the major PLC vendors stating that PACs are not only displacing PLCs in a growing number of applications, but that PACs are also competing with, and displacing DCSs in some applications, most notably 'hybrid' applications. In a growing number of cases, they say, the major DCS and PLC vendors now find themselves bidding on the same jobs, and PAC solutions are winning contracts that would previously have gone to DCSs. Examples of such “hybrid” applications might include a food processing plant, which in the past might have used a DCS at one end of the plant for the process control, and a PLC at the other end to handle the packaging line; this plant today might instead be using PAC technology to do the entire, integrated control job. The same kind of thing is happening in oil & gas, pharma and other traditional DCS strongholds, according to some PLC/PAC vendors. I am wondering if you could respond to a few questions on this topic:1) As a major process controls vendor, are you more often competing against traditional PLC vendors touting PAC solutions for hybrid applications involving both discrete and process control needs?2) How does your product line stack up against the PAC technology offered by the traditional PLC vendors?3) Have you enhanced your product line or added new controller products to more effectively go after the “hybrid” marketplace for integrated control? If so, please describe.4) How would you characterize your product line’s ability to handle logic or discrete control, together with process control, on a single platform? What about motion control? Other control domains?5) Where do you see the controls market headed in the future vis-à-vis these kinds of multi-domain controls applications?"Following are the responses received:Response from Jonathan Bretzius, P.E., East Regional Channel Manager, ABB Inc.1) As a major process controls vendor, are you more often competing against traditional PLC vendors touting PAC solutions for hybrid applications involving both discrete and process control needs?Bretzius: Certainly, many customers today are employing smaller, more agile, and more distributed systems than in decades past, which opens the door to PLC vendors with hybrid capabilities. Vendors that have traditionally sold PLC's have definitely been making a push into Process Automation with Hybrid Systems, just as classic large DCS vendors have pushed into the PLC and Factory/Discrete Automation areas by repacking the controller portion of the DCS System. At the control level, the differentiators or gaps on both sides have closed, Heavy Process Automation users still seem to have a preference for strong Advanced Process Control features (and related support expertise) which are still easier to implement in a DCS Controller. PLC’s and DCS’s were competing and hybrid controllers were in use before ARC’s "PAC" term was coined. Many DCS’s and PLC’s have a number of advanced and "PAC-like" capabilities without necessarily calling themselves PAC’s. Not everyone has been motivated to adopt the new PAC term amidst advances in technology. The term that we are using today is just controller or a hybrid controller. The term "Hybrid" sufficed as a new term for the PLC/DCS convergence, until Motion was newly included as a 3rd domain to consider by ARC. Motion has typically applied more to the PLC domain. The main differentiator between Classic PLC Vendors and the Classic DCS Vendors appears to be the tight integration of information across the overall Hybrid Control System. For example, an engineer should be able to search for a variable across not only the control logic, but also the Graphics, Historian, Batch, Asset optimization and Fieldbus, Field Device configuration. Today, integrated information is most efficiently delivered by the DCS vendors, especially with a system that is built from the ground up for integration - like ABB’s Extended Automation System 800xA, or Freelance compact DCS system. 2) How does your product line stack up against the PAC technology offered by the traditional PLC vendors? Bretzius: ABB segments the market for Automation four ways: Factory Automation PLC's, Process Automation PLC's, Compact Hybrid DCS Systems and Full Featured DCS Systems. Our philosophy aligns well against the traditional PLC vendors employing PAC technology. For more process intensive customer needs, we employ our Compact 800, Freelance, and System 800xA solutions and support. For more discrete intensive needs, we employ AC500 solutions and support. Even better, these four various ABB systems can all be combined for the best of all worlds when necessary (along with ABB drives, instrumentation, analytics, motors, etc.) All of our systems support IEC 61131-3 Logic tools, but each market segment still requires some functionality that requires specific features that would not be appropriate for every segment. ABB's AC500 is our Factory Automation PLC that offers scan times in the microsecond level which is ideal for high-speed applications such as a Printing press or precise high-speed cut-to -length applications, and motion control, which is a presumed domain of PACs. The AC500 specializes in integrated high-speed "discrete" master/slave bus capabilities (Modbus, Modbus RTU, Profibus DP, DeviceNet, CANOpen, ASibus...,) along with DDE/OPC, Ethernet and ARCnet. An integrated HMI tightly links information and control logic.ABB's Compact 800 is our Process PLC that offers entry level pricing for stand alone, advanced process control, redundancy and complete process simulation for most hybrid applications. This solution provides a cost effective but scalable foundation which can grow into a complete Plantwide Control System with complete integration of system wide information.ABB's Freelance System is our compact DCS System where tight integration between Control, Graphics, Historian, Alarm & Events, Fieldbus Engineering, Field Device Management is required out of the box, without the need for server database overhead.ABB's System 800xA is our flagship DCS System that provides complete enterprise integration with Hybrid DCS functionality as above, along with tight integration of Batch, Safety, Real Time Production Intelligence and Enterprise wide integration of third party database applications such as Maximo, SAP or Intergraph SmartPlant Instrumentation, to name a few. System 800xA takes object based programming to the enterprise level with our patented Aspect Object Technology.ABB’s Freelance, and 800xA systems also specialize in the "process" bus capabilities (Foundation Fieldbus H1/HSE, Profibus PA/DP, HART, Modbus, Modbus RTU, Modbus TCP/IP...) typically used in process applications. If a PAC is to presume domain coverage for both DCS and PLC applications (not to mention motion) it should offer both discrete and process bus capabilities that are both broad in offering and easy to employ. This is a tall order that ABB does uniquely well with our product marketing mix. 3) Have you enhanced your product line or added new controller products to more effectively go after the “hybrid” marketplace for integrated control? If so, please describe. Bretzius: Compact 800, Freelance and System 800xA can all be configured as Hybrid Systems to perform PAC functionality quite well. The Control Builder tool set integrates ladder logic & instruction list discrete programming languages seamlessly with the sequential programming languages of Function Block diagrams, Structured text and Sequential Function Charts. ALL ABB Controllers support true multitasking to ensure that the right process scan time (down to 10 ms) is achieved for each critical discrete control loop, while allowing for extensive process control capacity by extending out the scan times for slower process control loops, In recent years we have also developed a line of industrial field panels, 'Panel 800', to support the needs of distributed PLC/PAC's across the factory floor where a full Engineering/Operator workstation would not be well suited. In addition, the open rack configuration and remote I/O support allows complete scalability from below 100 I/O to over 1000,000 I/O points in a common platform. Specific to the AC500 PLC, an HMI integrated into the programming software provides a more tightly coupled operator interface than traditional PLC's, creating a hybrid environment. As with ABB’s Compact 800, Freelance, and 800xA systems, the AC500 multitasking advantage is important for program execution efficiency and simplification. Fast loop execution is ensured via especially high-speed CPUs (microsecond scans) executing high-speed I/O across high-speed buses. Standard AC500 I/O can be configured for high-speed execution as needed. For distributing the control, and for the sake of modularity, security and/or execution speed, large programs in one controller are easily and inexpensively segregated into smaller, very capable controllers, which can be tightly integrated across myriad bus options, employing powerful local and global variables schemes. For a distributed (de-centralized) architecture, the AC500 is tremendously effective in terms of lean cost and in ease of implementation....with especially few hardware interfaces required, very flexible software, and much less software effort required.\ABB certifies as "Industrial IT-enabled" the many ABB and third party discrete and process devices that can be employed together into an enterprise solution. This includes our controllers/devices from the discrete world (PLC’s, switches, sensors, motors, starters) and our controllers/devices from the process world (DCS, Hybrids, analyzers, transmitters, valves.) Indeed, we can mix-and-match ABB DCS controllers with ABB PLC I/O into a unified system (among many other ongoing developments.) 4) How would you characterize your product line’s ability to handle logic or discrete control, together with process control, on a single platform? What about motion control? Other control domains? Bretzius: Each of ABB's Automation Solutions fully supports IEC 61131-3 logic development, tools to create function block and code libraries, and DDE/OPC. In addition, they each tout multi-program, multi-tasking capability, support high speed counters, sequence of events, and capable engineering development and testing/simulation tools. Each controller will support a wide range of industrial Fieldbus architectures from both the process and discrete manufacturing markets. Motion control is a growing specialty of the AC500, which nicely employs PLC-Open motion control function blocks and the ABB ACS/M1 High-Performance Drive to meet the demands of today's motion and positioning control applications. Due to ABB's market-leading position in Variable Frequency Drives, Instrumentation, Analytical, Power and motor control, ABB is able to offer turnkey automation solutions with very sophisticated machine, switchgear and motor control that is tightly integrated with the overall control system regardless of the ABB controller. 5) Where do you see the controls market headed in the future vis-à-vis these kinds of multi-domain controls applications? Bretzius: ABB has aligned our Automation portfolio with the four different brands to meet the specific needs of each market segment as we have defined above. Rather than presuming one type of controller can do it all (attractive to vendors,) there is a likelihood the market will continue to demand a solution that precisely meets the needs of the individual customer. ABB has a unique and long history among all vendors as the long-term supplier of both DCS's and PLC's, along with all the related discrete/process field devices. We believe that the market demands are unique and warrant a multi-controller strategy, and that this trend will continue to require specific features in each industry that will make it very difficult to follow a “one size fits all” strategy. Like Tiger Woods or any golfer knows, you need the right tool for the landscape and distance that your environment requires. Response from Duncan Schleiss, Vice President, Marketing. Emerson Process ManagementSome thoughts regarding the notion of a PAC (programmable automation controllers). Let's consider a PAC nothing more than a CPU that has some functional capability. There will be a need for small PACs for lesser CPU intensive applications and the need for large ones in the same sense that not every computational algorithm can be solved with a PC nor is a Cray computer needed for some of the trivial applications. Likewise some will be built for-purpose that can do for example SIS (safety integrated systems), motion, advanced control, or embedded batch. Some will need to be indoors and some outdoors and will have different environmental conditions. The landscape one sees is a wide variety of PACs for a wide variety of applications. In some cases similar or the same hardware may be used and in other cases economics shall not permit that. Nonetheless, a family of CPU requirements emerges in the same sense that the IT computing world offers a wide variety of hardware solutions for various applications.On the software front, a wide variety of software applications are needed to address the application space – from motion computing, MES, PID, synchronized drives, etc. Some overlap in the functionality may emerge, but for the most part, fit for-purpose application software shall prevail. One is left with a wide variety of physical CPUs and a wide variety of application software with some vendors covering niches and others attempting to cover the entire space or parts thereof. At Emerson, we’ve consciously decided to focus on key industries that do not have the motion control needs of the packaging or automotive industries. Given this focus, we see little in the way of additional customer value by integrating this functionality in to controllers specifically designed for process control. There are extremely rare occasions where there is a need to cover packaging applications for customers as an extension to the basic process control system. In these cases, the package unit typically comes with a PLC installed. In this case integration to the PLC is more important than anything else and this is an area we have focused on. A tightly integrated solution on Ethernet/IP, ProfiNET, HSE, etc is of more value to our customers than a native solution by Emerson and we have focused on making this integration easy. This approach has really resonated with our customers. Given this backdrop, we do not see the case for a PAC specifically or the notion of the need of multi-domain functionality in the markets served by Emerson. We’d rather spend that extra effort on delivering additional value to customers in our traditional space. With this backdrop, we have gone ahead and answered your questions below. 1) As a major process controls vendor, are you more often competing against traditional PLC vendors touting PAC solutions for hybrid applications involving both discrete and process control needs? Schleiss: No. We focus on very specific markets and find ourselves against traditional competitors. We seldom see the PLC providers in this space. 2) How does your product line stack up against the PAC technology offered by the traditional PLC vendors? Schleiss: We don’t compete with PLCs in the markets we serve. 3) Have you enhanced your product line or added new controller products to more effectively go after the “hybrid” marketplace for integrated control? If so, please describe. Schleiss: Our product line has been, since its introduction enhanced, extended, and improved in the served markets. We are continuing to enhance these offerings. In the hybrid markets, we focus on letting the customer pick the supplier of choice based on certain features (typically price given that these applications are largely addressed by commodity PLCs) and ensure that we have the world’s best integration to these options. 4) How would you characterize your product line’s ability to handle logic or discrete control? Motion control? Other control domains? Schleiss: Our automation systems address logic functionality either through programming or by use of prebuilt logic blocks. We have the capability to handle discrete control very well. We can address all the needs the of our focus customers noting that motion control market is not a focus of ours. 5) Where do you see the controls market headed in the future vis-à-vis these kinds of multi-domain controls applications? Schleiss: The markets remain the same and don’t benefit from these multi-domain controllers. The question is somewhat analogous to asking whether a cross between an orange and an apple with satisfy the consumers’ palette. We believe it is a fairly good bet to believe this would not work – the markets are dissimilar and consumers seek different solutions.Responses from Jamie Bohan, Segment Marketing Manager for Developing Markets, Honeywell Process Solutions 1) As a major process controls vendor, are you more often competing against traditional PLC vendors touting PAC solutions for hybrid applications involving both discrete and process control needs?Bohan: Assuming that by discrete you mean packaging, the answer is no. We do see PLC vendors competing for hybrid opportunities but we aren't seeing them offering a PAC type solution.2) How does your product line stack up against the PAC technology offered by the traditional PLC vendors? Bohan: The PAC concept as defined by ARC is based on interoperability—tools that incorporate multiple disciplines such as logic control, process control, motion control and drive control in a single, open platform with common tagging and a single database. This type of system has long been a requirement in the DCS world. In fact, the term "hybrid" was pioneered by DCS vendors who were able to offer both sequential and process control in one platform many years ago. We're seeing the PLC vendors make good strides in terms of being able to handle process control requirements for small processes. However, there are some very real differences between a PLC and a DCS when it comes to process control (as opposed to motion/discrete control—where PLCs grew up) that cannot be overcome on a PLC based platform. It is in this area where we see the biggest gap in today's PAC offerings. 3) Have you enhanced your product line or added new controller products to more effectively go after the “hybrid” marketplace for integrated control? If so, please describe. Bohan: Honeywell has been in the hybrid market for over 20 years with some of the biggest names in batch manufacturing. As described below, our platform provides the desired integration today. 4) How would you characterize your product line’s ability to handle logic or discrete control? Motion control? Other control domains? Bohan: The goal of our platform is to provide an "operational cockpit" from which the operator has a view into all necessary plant information. The source of the data is irrelevant to the operator, rather the ability to efficiently and effectively monitor and run the plant is paramount. Data from any source can be brought into the platform and integrated using a global database. This provides the ability to access information, manage alarms, view graphics, etc from any source in a consistent fashion. From a control perspective, we recommend and offer purpose built control processors for process and motion control - as these two domains are very different. 5) Where do you see the controls market headed in the future vis-à-vis these kinds of multi-domain controls applications? Bohan: Honeywell's experience in these markets has been and continues to be that customers have specific requirements for automation in both process and motion control and they are not willing to compromise in either area for the sake of a single controller. Thus, it is essential to maintain the control and operational characteristics of each domain, while providing an integrated platform. We don't see this going away. This paradigm is very similar to the integration of IT with plant control. These two domains have different drivers and different operational philosophies. Although the two have converged some over the past few years, there is still a need to maintain the integrity of the plant.Response from Bruce Jensen, Manager, Systems Marketing and Sales Support, Yokogawa Corp. of America 1) As a major process controls vendor, are you more often competing against traditional PLC vendors touting PAC solutions for hybrid applications involving both discrete and process control needs? Jensen: There are some times that we compete in the small systems application arena or in specific industries as you noted. However it is less so in the refining, petrochemical arenas where the project tends to be large. Often PLC/PAC augment an overall solutions as an I/O subsystems, where Yokogawa's DCS is the primary HMI to the process operator. The decision factors usually involve the level of redundancy, single source vs multiple source, initial price, who is doing the applications, speed required for analog and/or digital response, and what industry experience is put to use. In small system applications, they may not be factors. And as you noted in Pharma and Food, they may want a united system and architecture in the processing as well as packaging areas. In larger applications, influence factors are level of engineering required, single source of responsibility, total cost of ownership over a 10+ year time period, level of redundancy, and performance. 2) How does your product line stack up against the PAC technology offered by the traditional PLC vendors? Jensen: The factors are generally have to do with initial prices and then total cost of ownership and less from technology. With small form factors in the DCS for controller and I/O and with Field networks, price per point for DCS systems have fallen making them competitive with PAC/PLC architectures. PAC/PLC have grown their architectures to handle larger I/O, integration of Field networks and a fuller library of control algorithms. We call that scalable now. The advantage DCS systems have over PAC is the scalability to very large I/O counts. Controllers, networks and firmware are designed for high communication and processing loads making them more reliable with a higher performance (specifically at the HMI level where data must be communicated and displayed from the controller to the HMI, and at the loop performance level), where PAC handle faster processing at the discrete level. But in essence a system architecture involves 1) HMI, 2) controller 3) I/O, and 4) networks that tie I/O to controllers, controllers to other controllers and HMI, and in to information infrastructures. A main difference then lies in how those components are put together and what are the configuration and engineering tools and level of sophistication. Generally, a PLC/PAC requires configuration/engineering of both a controller database and an HMI database. In a DCS, this is a global database with diagnostic displays automatically created by the system. But to me the term DCS, Hybrid, PAC, PLC, doesn't mean that much - it's what functionality does the user want and what hardware and software tools does it take to get there. What is happening is that functionality that systems are performing with I/O, controllers, and HMI are converging, albeit still with some architectural differences, and ways the software works. 3) Have you enhanced your product line or added new controller products to more effectively go after the “hybrid” marketplace for integrated control? If so, please describe. Jensen: Yokogawa introduced its more compact controller and I/O for its CENTUM CS 3000 DCS system in 2001 and has added different varieties of I/O ever since. Most of these modules were analog and digital cards with different isolation characteristics and different densities. Also, a set of communication I/O modules to talk the variety of Fieldnetworks, Foundation Fieldbus, Profibus, and now even Ethernet/IP. One such recent I/O, to be released in Feb is a specific turbine control I/O module - servo module (LVDT or 1 to 5 V DC standardized signal for position feedback signal and 24V DC ON/OFF signals for quick close and outputs up to +- 50mA signal for servo control ). And through that period enhanced HMI and integration capability through NT, Windows 2000, XP, 2003 Server, and now Vista. In 2005, Yokogawa introduced a GB network and other augmentations include OPC client capability for subsystems and to migrate other vendor systems. In addition, a compact controller that could handle 14 additional I/O nodes for higher capacity was introduced. 4) How would you characterize your product line’s ability to handle logic or discrete control, together with process control, on a single platform? What about motion control? Other control domains? Jensen: Yokogawa supplies a full range of products for varying markets and features needed for various industries: CENTUM CS 3000 - Distributed Control System; ProSafe-RS - Safety Instrumented System - using 1131-3 configuration tool set; Stardom - SCADA RTU, 1 small scale controller brick and one flexible I/O controller that can be described like a PAC; FA-M3 - a PLC for factory automation - more popular in Japan than in the U.S., which includes motion control I/O; DAQstation and MW100 - recorders and data acquisition stations.Thus, Yokogawa has a line of process automation systems encompassing the full gamut of applications and user wants within different divisions of the company. So the features of each system has strengths in different process industries and in different applications. So internally, we have some of the same issues as to tailor the correct product within our own portfolio to the application and industry. But speaking to where your questions are directed, I am assuming the DCS, so the ability to handle logic, discrete control and process control on a single platform is inherent in most DCS designs, where most DCS/hybrid suppliers have expanded the architectures to handle the multi Field networks and designed to handle integration to both subsystem and supervisory systems. PACs are also going this direction 5) Where do you see the controls market headed in the future vis-à-vis these kinds of multi-domain controls applications? Jensen: DCS, Hybrid, PAC, PLC and even SCADA creates more of an emotional response in the industry where users tend to equate the terms with architectures and software that they are aware of from legacy systems that they've worked which had those names. Really, this is about how architectures are put together and the how software tools sets are made to create the applications more intuitive and with lesser efforts. Also, future network architecture and Ethernet protocols will have better security built-in instead of add-on to make configuration of architectures easier both for internal and external access.To see the main story this sidebar was taken from - "PACs Gain Momentum" - please visit www.automationworld.com/view-3895.
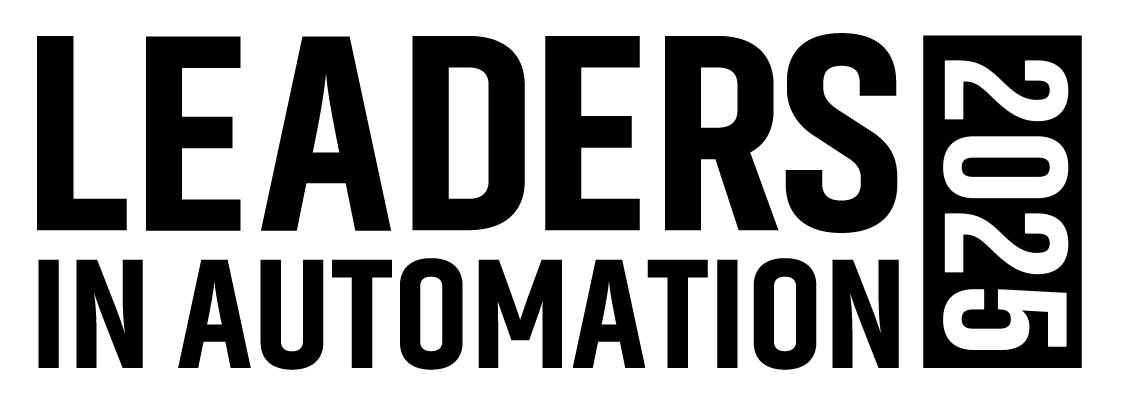
Leaders relevant to this article: